Advanced shops aim to be on the top of their game
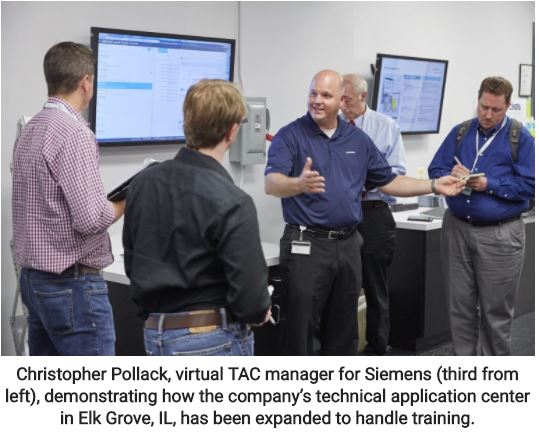
AdvancedManufacturing.org, a manufacturing news site, recently published an article describing how shop managers can learn to benefit from digitalization. “Advanced Shops aim to be on the top fo their game,” describes how shop managers can visit the newly-expanded Siemens Technical Application Center to get training in all things digital—from basic machining to advanced five-axis training and maintenance. Read an excerpt from the AdvancedManufacturing.org article here.
Shops looking for ways to improve productivity in traditional subtractive machining processes need look no further than ways to reduce setup time, improve spindle uptime, and implement CNC programming efficiencies. Shop managers overwhelmed by claims about the future of digitalization and Industry 4.0 can find ways to translate that exciting promise into their day-to-day operations—today.
One way would be to visit the newly expanded Siemens Technical Application Center (TAC) in Elk Grove Village, IL, for training in all things digital—from basic machining to advanced five-axis training and maintenance. Shops can visit Siemens’ TAC physically or via the Internet for training and learn how their shops can benefit from creating a virtual twin of all the steps taken to create a product using Siemens digital capability.
Here’s how companies large and small can benefit from the experience and models of these and other game-changing shop solutions.
Siemens Positions its TAC for Advanced Manufacturing
Siemens recently expanded its TAC to satisfy the demand for training to keep pace with digitalization and rapid changes in technology. According to Christopher Pollack, virtual TAC manager, “We created a mock mini job shop in the expanded TAC to demonstrate how Siemens’ digital capabilities take the process of manufacturing a part from inception all the way through to physical production. What we are doing is taking a big concept like digitalization and making it palatable and accessible at the shop-floor level.” In the mini job shop, Siemens designs a product using NX-CAM, engineers it and turns it into engineering drawings and files that are then handed-off via manufacturing SinuTrain software.
The virtual twin allows shops to do all the things that they had been doing out on the shop floor and do them on the PC without downtime and interrupting production, said Pollack. “They can validate the process through simulation and then transfer programs to their machine tools using MindSphere, the Siemen’s cloud for industry.” MindSphere is a tool for virtual management of CNC machines, tooling use, and data transmission, that provides the ability to validate programs and monitor machine uptime and other key indicators, Pollack explained.
The obvious benefits are that rather than causing downtime on the machine tool, shops can evaluate and leverage processes in a virtual environment, something that they would normally do out at the machine tool. “Tying up machine tools on the shop floor is typical of job shops and low production run companies where they’re not doing heavy CAD/CAM-based production, but doing more conversational programming that requires typing on the machine. What we are demonstrating is the typical transition process from a prime or Tier One [supplier] that has designed a product and transitioned it out to the job shop,” said Pollack.
The Siemens TAC now occupies more than 3150 ft (293 m2 of dedicated space. The machine lab features three milling machines (one of which is five-axis), one turning center, a KUKA robotic cell, an NX-CAM training station, and two upgraded classrooms for hands-on training using Sinutrain software and Sinumerik CNC simulators. TAC training includes four different classes; one for service and maintenance and three levels of operator training. Level 1 focuses on basic milling and turning. Level 2 introduces G-code, and Level 3 is the most advanced, focusing on five-axis machining.
“We are creating a parallel training track for online training with webinars, streaming video, and online instructor-led training for its basic classes,” said Pollack. “We know that people will travel a lot farther for advanced five-axis training than they would for basic classes which can be effectively handled through online training.”
You can read the full article, “Advanced Shops Aim to be on the Top of their Game,” on the AdvancedManufacturing.org website. Let us know what you think in the Comment section below.