What’s new in NX for manufacturing (December 2412)
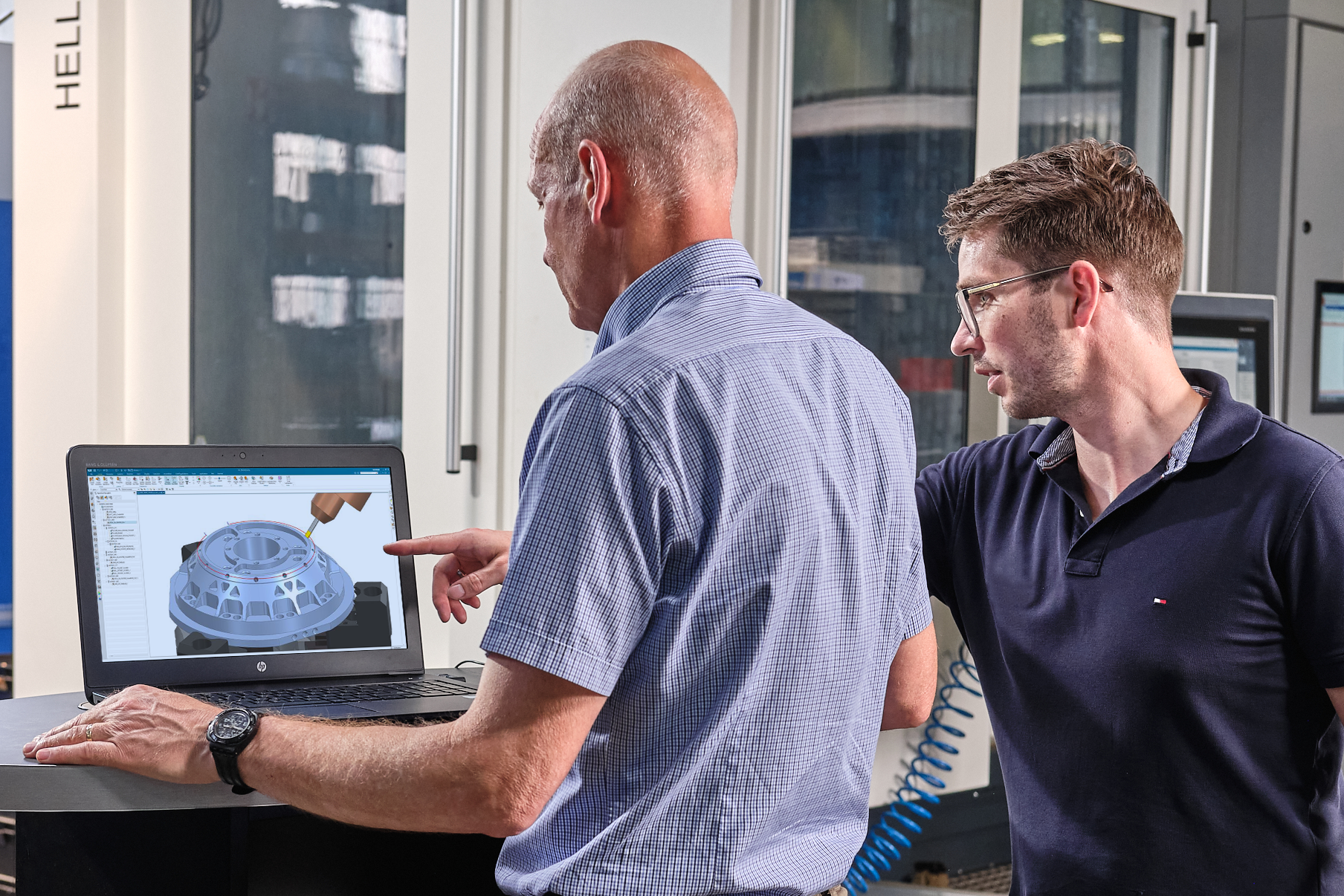
The latest version of NX for manufacturing is packed with the latest features and updates designed to transform the way you manufacture parts.
Each new release of NX for Manufacturing introduces new features and enhancements that boost productivity, improve usability, and streamline your workflows. These updates consistently bring advanced tools that reduce manual programming, saving you valuable time and costs.
Let’s explore some of the highlights from this release.
NX X Manufacturing: Transforming part manufacturing with cloud technology
NX X Manufacturing, the cloud version of NX Manufacturing, was recently launched, delivering flexibility, security, and scalability to CAD/CAM software. This powerful SaaS solution combines the advanced capabilities of NX with cloud technologies. Designed to enhance efficiency and productivity, Siemens’ NX X Manufacturing streamlines deployment and configuration while offering value-based licensing that scales to meet the needs of manufacturers of any size.
Read the blog to learn more about the capabilities of NX X Manufacturing.
NX X Manufacturing is available in three product tiers—Standard, Advanced, and Premium and add-ons through value-based licensing. These tiers are designed to meet varying part manufacturing requirements.
- NX X Manufacturing Standard: Ideal for prismatic parts, offering 2.5-axis milling, hole-making, turning, and on-machine probing for automated programming.
- NX X Manufacturing Advanced: Includes advanced 3- and 2.5-axis milling, turning, and on-machine probing, perfect for freeform parts like molds and dies with integrated CAD/CAM tools.
- NX X Manufacturing Premium: For complex manufacturing needs, it adds advanced 3- and 5-axis milling, rotary machining, turning, and over 20 customizable add-ons for specialized capabilities.
- Value based licensing: Boost your capabilities with over 20 customizable add-ons and enhance your software experience with specialized features for automation, machining, and simulation, tailored to specific project needs.
What’s new in NX CAM
The latest version of NX CAM includes automation enhancements and machine-powered programming, enabling faster programming, greater efficiency, and improved part quality.
Make Machining Suggestions
Create a complete machining process for a feature with just a click on a component’s face. The latest Make Machining Suggestion feature in NX CAM simplifies toolpath creation, automatically suggesting pre-defined machining processes with an optimized sequence of operations. For example, by selecting the floor face of a pocket you can automatically program the entire pocket using multiple operations and tools.
Additionally, capture your preferences and offer suggestions for future use, helping you program faster, while enabling higher standardization.
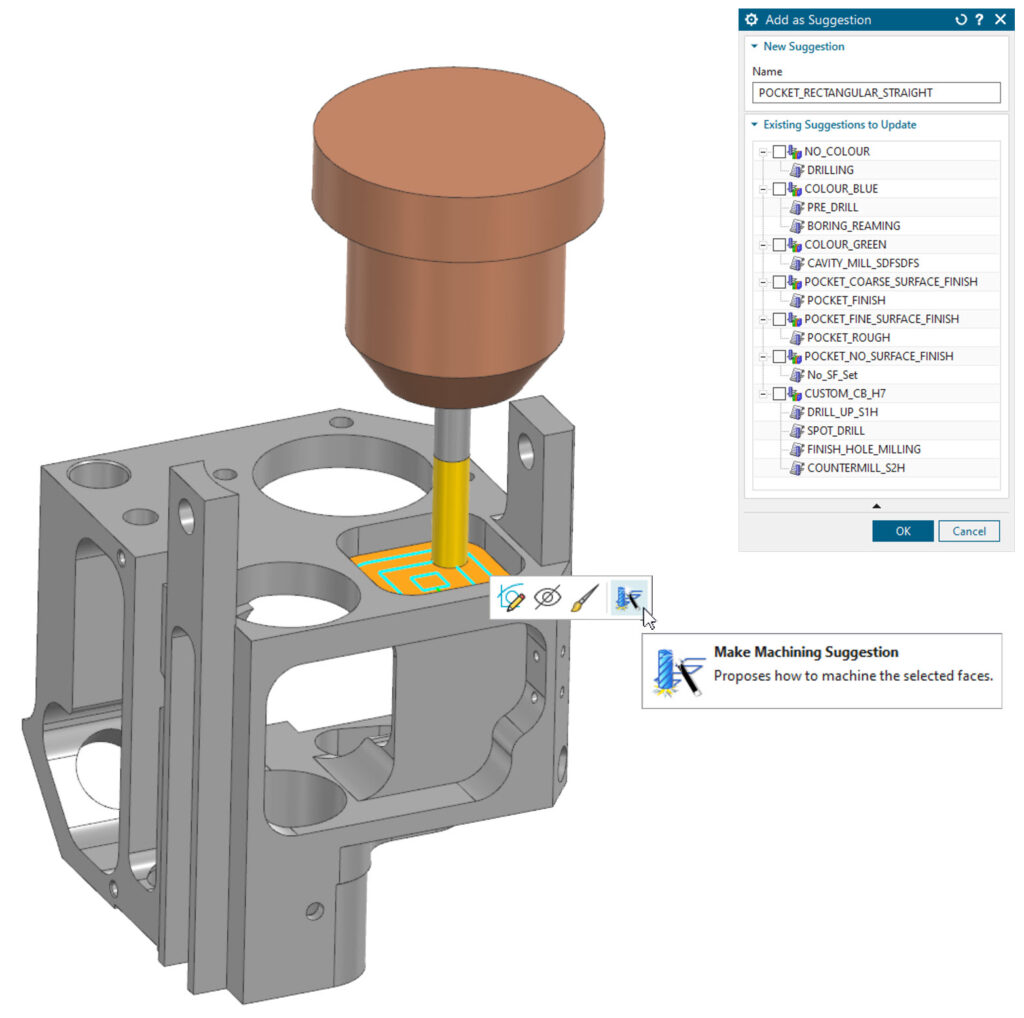
Automatic Hole Machining
Holemaking now includes enhanced automation capabilities. The newly introduced Automatic Holemaking feature allows you to fully utilize the power of Feature-Based Machining (FBM) when programming holes. You can select one or multiple faces with holes and NX automatically detects all holes of various sizes and complexities, groups them, and creates optimized toolpaths to effectively machine them.
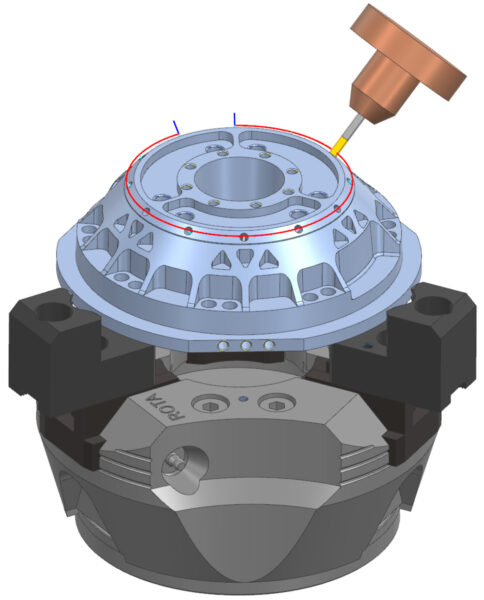
Machine Powered Programming
Machine Powered Programming (MPP) integrates machine tool capabilities directly into the programming process. Programmers can use the exact settings and parameters of the selected machine, simplifying the creation of efficient and error-free toolpaths, even for the most challenging multi-axis CNC operations.
With the new Real Machine Job Commissioning feature in NX CAM, you can efficiently commission tools, devices, parts, and fixtures using an intuitive graphical interface.
The Machine Setup Configurator Navigator transforms commissioning tasks by introducing a dedicated view for part and tool setup.
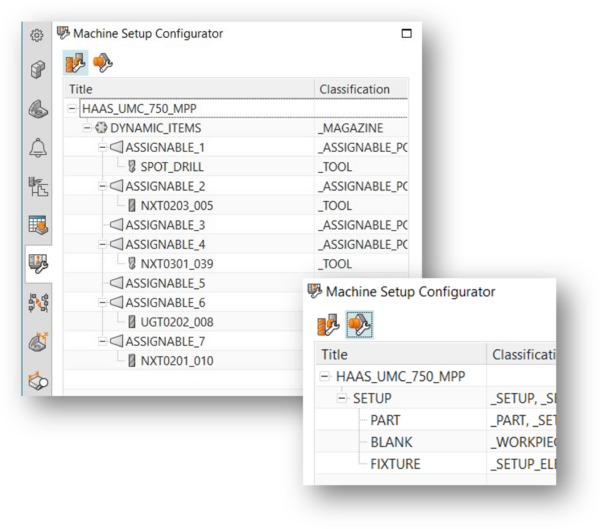
Machines with specified kinematics in the Machine Tool Builder can now be defined with turrets or magazines featuring static pockets. This enhancement ensures that tools are accurately positioned during CAM programming, improving setup efficiency.
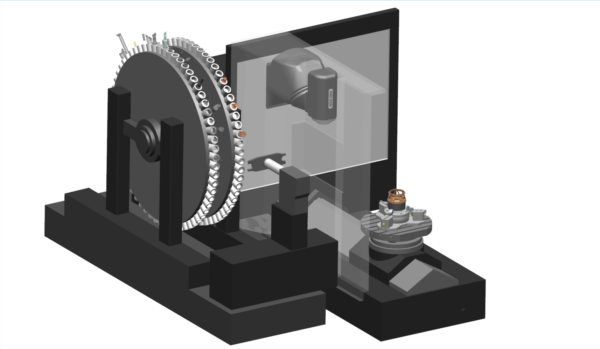
With turret support, you can now program lathe machines while fully leveraging all MPP advantages, including the tool-in-machine display functionality, making programming more streamlined and precise than ever.
The latest “Display Tool in Machine” feature in NX MPP allows you to verify turning and mill-turn operations with ease. By previewing machine motions during programming, you can optimize toolpaths and prevent collisions. This enhancement supports both single-channel lathes and complex mill-turn machines with B-axis or turn-mill configurations (e.g., DMB FD or Heller CT/CP), with updated axis and kinematics chain definitions in the Machine Tool Builder. With an instant preview for advanced turning technologies like Y-axis turning and dynamic tool orientation, this feature not only streamlines programming and improves accuracy but also enhances overall workflow efficiency by enabling faster verification and optimization of toolpaths while reducing the risk of collisions.
The latest chip breaking option for turning toolpaths provides an efficient solution for managing long, stringy chips during machining. You can now control the tool’s engagement with the workpiece to break chips into smaller, manageable lengths. This improvement enhances chip evacuation, minimizes entanglement, and promotes cleaner machining environments. It also reduces downtime, improves surface finishes, and extends tool life.
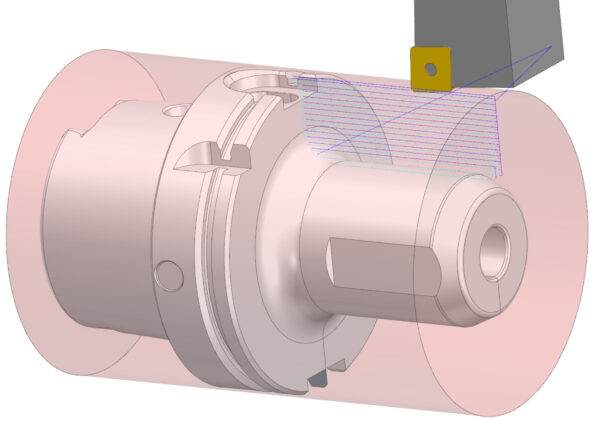
What’s new in On-Machine Probing
Cycles for tool setters and contactless tool setters
NX CAM On-Machine Probing now supports measuring cycles for both tactile and non-contact tool setters, enabling fast and automatic tool setting, monitoring, and breakage detection. This includes automatic tool offset calculation and correction, as well as tool breakage detection between machining cycles to prevent damage. Additionally, third-party integrations for spindle probes, tool setters, and non-contact tool setters are supported.
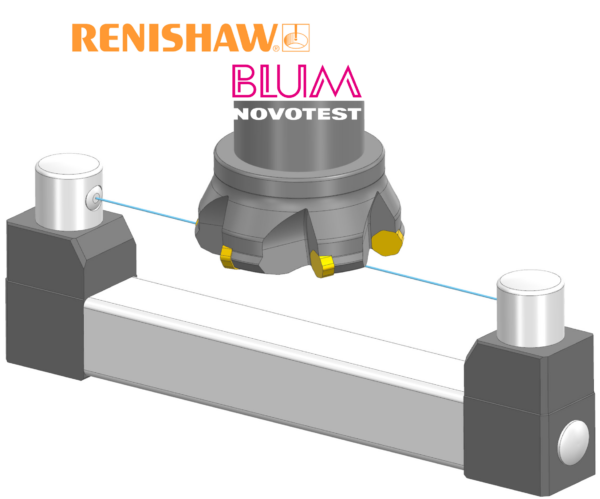
Normal to Face – Sinumerik MEAS
An intelligent avoidance method has been developed for individual single-point measurements using the MEAS command. This enhancement reduces unnecessary air motions by only performing retraction movements to the clearance plane when a potential collision with the part is detected, ensuring improved efficiency and accuracy with built-in collision checks.
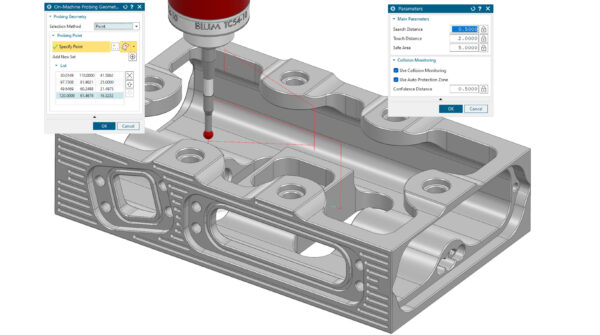
Renishaw I+ Cycles
Experience seamless part setting and inspection with the integrated macro software package that supports a wide range of cycles, from basic part setup to complex vector and angular measurements. The Renishaw I+ cycles now provide support for output to Siemens, Fanuc, Haas, Okuma, Mazak, Mitsubishi, and Brother controllers.
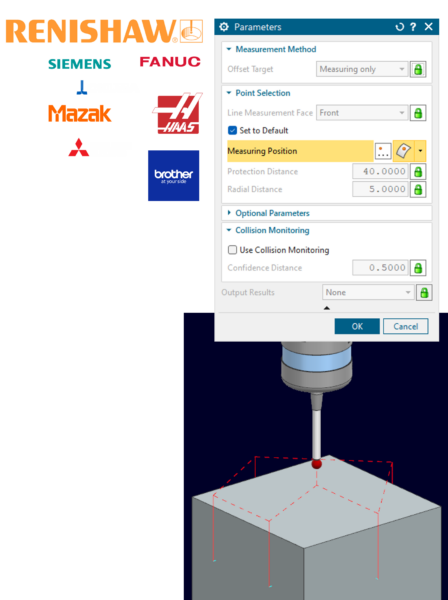
What’s new in Additive Manufacturing
The latest updates to multi-axis additive manufacturing introduce significant enhancements that improve user control, efficiency, and print quality, ensuring higher-quality builds and accelerating production.
Printer Library
The Printer Library for Multi-Axis Additive Manufacturing allows engineers to create and manage printer families with custom process parameters. It includes Build Styles for Operation Parameters, Build Rules for Custom Process Parameters, and a Material Library to define settings like step-over and slice distance. By assigning specific parameters to output types, such as finish passes or infill strategies, you can enhance control, improve print quality, and streamline additive manufacturing workflows.

Docking Passes
The new “Mark Docking Passes” feature in NX Additive Manufacturing introduces custom parameters for docking geometry, allowing you to optimize prints where two parts meet. Manage the heat sink effect by applying different process parameters at the docking pass, ensuring higher-quality builds at the contact points. By defining the docking area around selected bodies or faces, you can now reduce energy usage and improve print consistency, particularly in areas where parts touch.
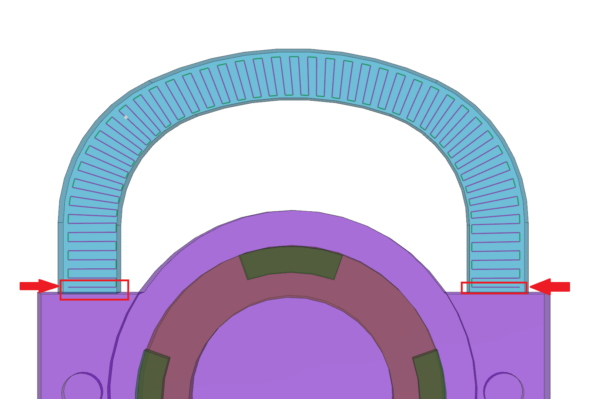
Toolpath Report Enhancement
Adjust the feed rate for cooling time, to achieve greater control over the cooling process layer by layer. This feature is useful for polymer printers and ensures continuous printing without cooling breaks, preventing part deformation. By adjusting the feed rate based on cooling time, you can increase the time per layer without interrupting extrusion, ensuring efficient and precise printing.
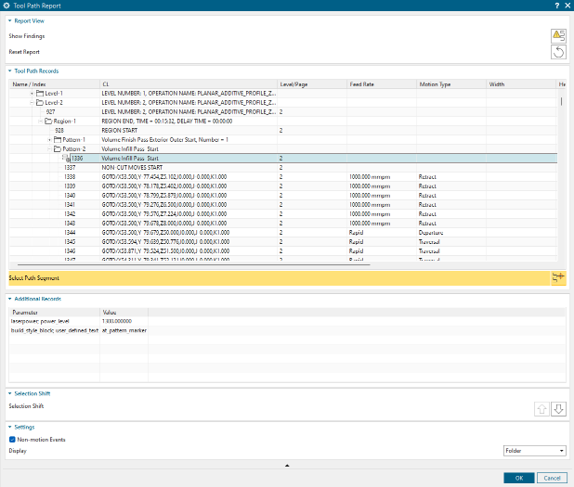
User experience has been improved, enhancing overall navigation and usability, with an updated toolpath report that simplifies the process of validating cutterpaths. You can now easily view layers, multiple regions, individual patterns, and additional records. With the Layer folder, you can quickly access specific layers, while region subfolders display different areas of the part.
The auto tool axis has been improved to deliver smoother motions around corners, particularly in overhang areas. Replacing the previous function, the new auto tool axis algorithm creates smoother output in corners, especially in overhang regions. There is no need for a UI setting to enable this feature, as it automatically replaces the previous functionality.
Thin-walled tubes can now be sliced with user-defined wedge angles, ensuring precision and customization for complex geometries. By splitting tubes into wedges with constant bead heights, this enhancement supports printers unable to vary bead heights and addresses the challenges in printing bends. Previously exclusive to Tube Additive Buildup, this method is now available in Tube Thinwall, delivering consistent quality for intricate designs.
Manifold Checker
The new Manifold Checker feature helps minimize build failures by detecting potential non-watertight bodies and other geometric issues early in the process. You can validate meshes to ensure they are fully watertight and free of intersecting faces, missing surfaces, or gaps—common issues that can lead to build failures. This feature verifies the integrity of 3D models, ensuring they are print-ready before the build process begins.
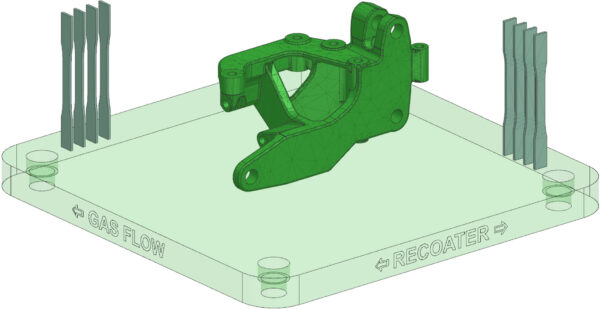
No-build Zones
With the new No Build Zones feature, you can define areas in the build tray where parts cannot be printed, such as regions with sensors or fixturing. These zones are automatically considered during 2D/3D nesting to ensure parts are placed in reliable areas, avoiding interference with machine components. This improves print quality, simplifies post-processing, and enhances build reliability.
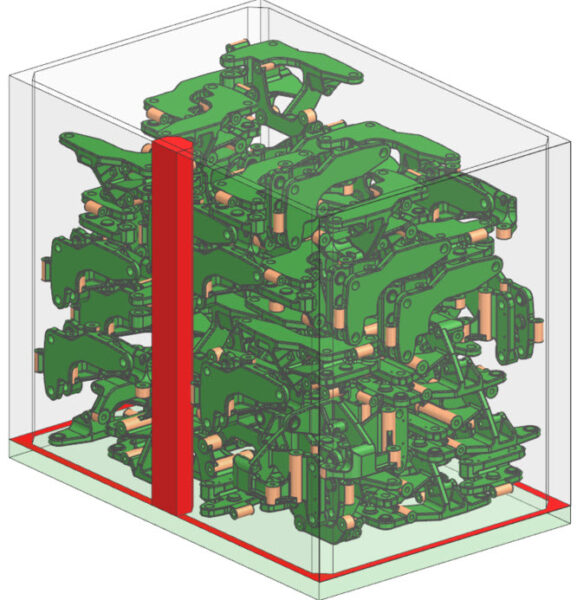
Improved Print Mark Performance
Print Mark Performance is improved, boosting efficiency for parts with print marks across multiple operations, including part addition, patterning, and move/copy actions. With the flexibility to defer print mark creation until output generation, users can reduce overhead, streamline workflows, and improve performance in complex builds, leading to faster operations.
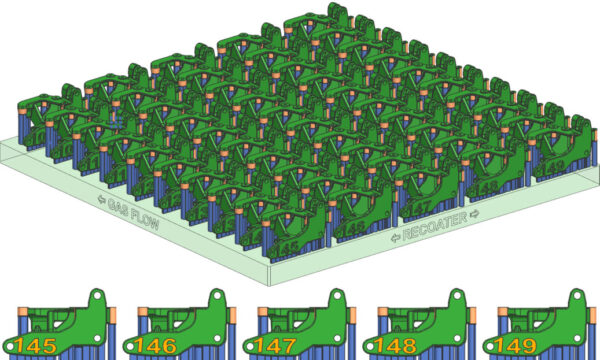
What’s new in Part Manufacturing Data Management
New updates to Part Manufacturing Data Management deliver enhanced capabilities to improve how you manage and access critical manufacturing data. With the integration of Teamcenter, Active Workspace, and the Manufacturing Resource Library, these new features help streamline workflows, improve collaboration, and ensure better control over manufacturing processes.
New commands have been added to the Manufacturing Resource Library ribbon in NX, offering you greater flexibility and direct access to essential functions within the NX environment.
Update Graphics in NX
You can now access resource management functions directly in NX. The Manufacturing Resource Library in NX has been enhanced with the addition of the “Update Graphics” command. This feature allows you to refresh 3D graphics for tool components created in Teamcenter, synchronizing classification attribute values and updating the 3D model. It offers greater flexibility, enabling you to adjust and update tool graphics directly in NX, even without an installed graphics builder on the Teamcenter server.
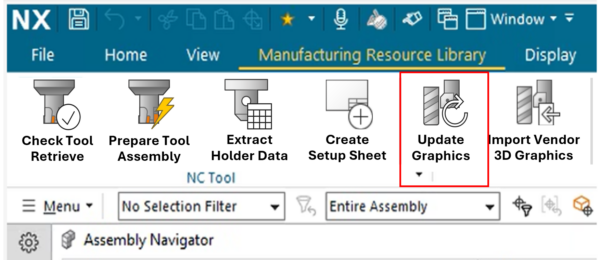
Import Vendor 3D Graphics in NX
The latest features in part manufacturing data management helps you reduce setup time, improve accuracy, and accelerate design workflows. With the “Import Vendor 3D Graphics” command, importing 3D models from tool suppliers is now easier without the need for Teamcenter Graphics Builder. The command automatically converts STEP files to NX part files, including attribute values, enabling you to quickly integrate 3D models. This improves efficiency, reduces manual effort, and ensures up-to-date tool data, accelerating design and manufacturing workflows.
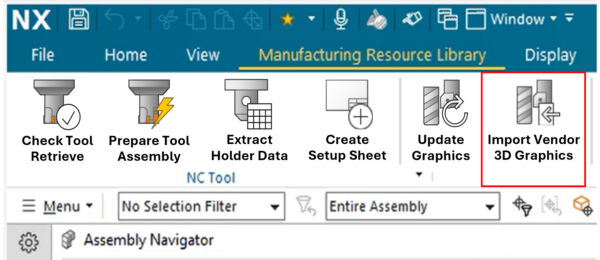
Advanced Guided Component Search
Component identification is now simplified with the latest enhancements to Guided Component Search. You can define multiple connection codes for a single connector and set alternate values, improving the search for matching components. This added flexibility enables the implementation of custom connection rules, significantly reducing the time required to identify the right components for assembly.
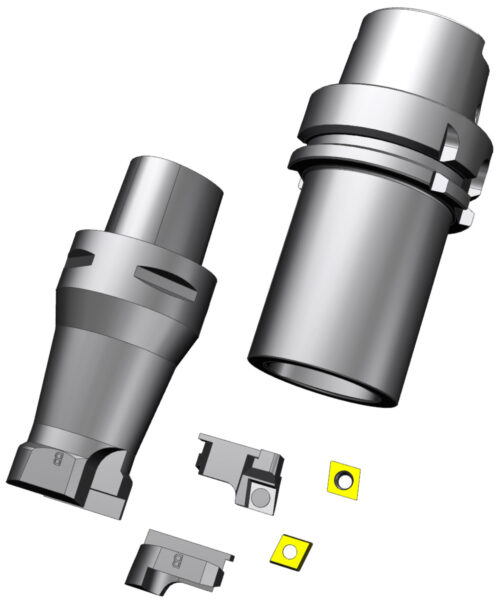
Gearing Tool Assembly Classes
Four new Gearing Assembly classes for managing gear cutting tools, including Hob Milling (solid and indexable) and Gear Tooth Forming Tools (solid and indexable), have been introduced. Based on DIN standards and customer feedback, these classes enable easy classification and retrieval of gearing tool assemblies, with mapping to NX CAM and access to class drawings, mapping tables, and familiar MRL functions for efficient tool assembly.
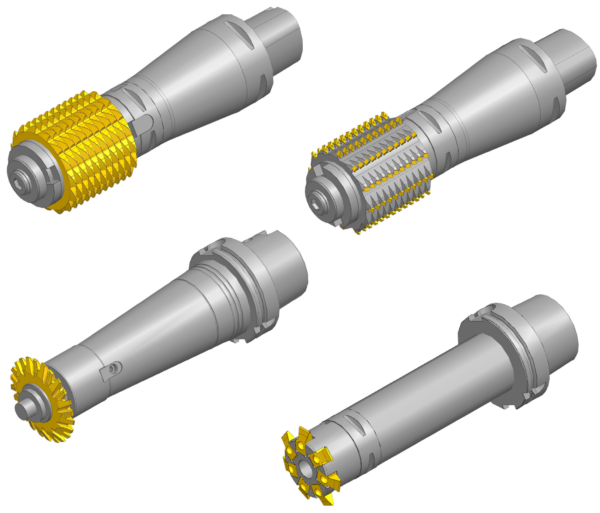
Shop Floor Connect
The latest version of Shop Floor Connect (SFC) brings enhanced flexibility, integration, and automation capabilities, offering improved support for change management, security, and system availability. Key updates include:
- Support for Change Management: You can now create change requests directly in SFC, which are stored in Teamcenter and linked to related CAM operations. This feature is crucial for industries like medical and aerospace, ensuring traceability and streamlined change management processes.
- Consolidation of SFC Admin Pages: SFC’s administration pages have been unified into a single interface for better transparency and user experience. Machine connections, configuration, failover settings, and license management are now managed from one location, simplifying setup and ongoing management.
- Automation of Machine Functions: An event handler is added to automate user functions/scripts before and after machine downloads and uploads, boosting efficiency and reducing manual intervention.
- Improved MES Integration: A call to MES before executing Teamcenter searches enhances the integration of SFC with manufacturing execution systems, enabling seamless workflows.
- Email Notifications for Failover: Operators will now receive automatic email notifications when switching back from failover to online mode, ensuring continuous communication and support for 24/7 production environments.
SFC Search Configuration by Organization: Search configurations can now be tailored based on organizational needs, providing enhanced security and flexibility.
What’s new in NX Assembly Line Planner
The latest version of NX Assembly Line Planner brings whole new capabilities to optimize production line design, simulate complex assembly sequences, and accelerate time-to-market through intelligent, integrated planning tools.
Fabrication Weld Planning
Fabrication weld planning is enhanced with parametric operations, allowing users to define specific parameters like weld length for accurate time calculations. These operations can be stored in the Operations Library and reused across process plans, ensuring precise time estimation and seamless integration with downstream applications.
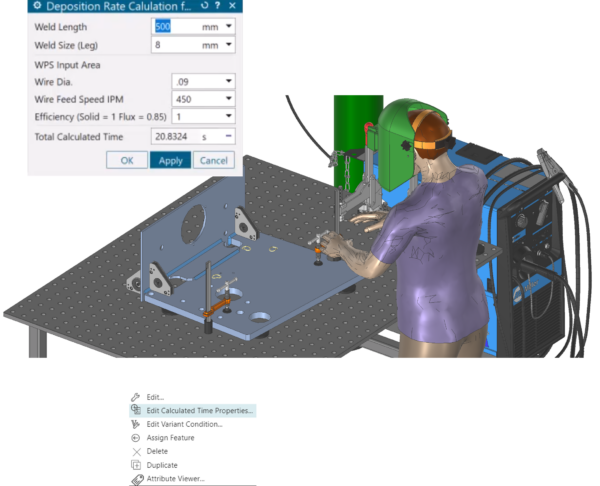
Resource Gantt and utilization
With the new Resource Gantt view, planning engineers can optimize resource utilization by visualizing the flow between operations across different stations. By focusing on critical resources, such as robots and conveyors, users can ensure resources are not overburdened, improving efficiency and maintaining alignment with Takt time.
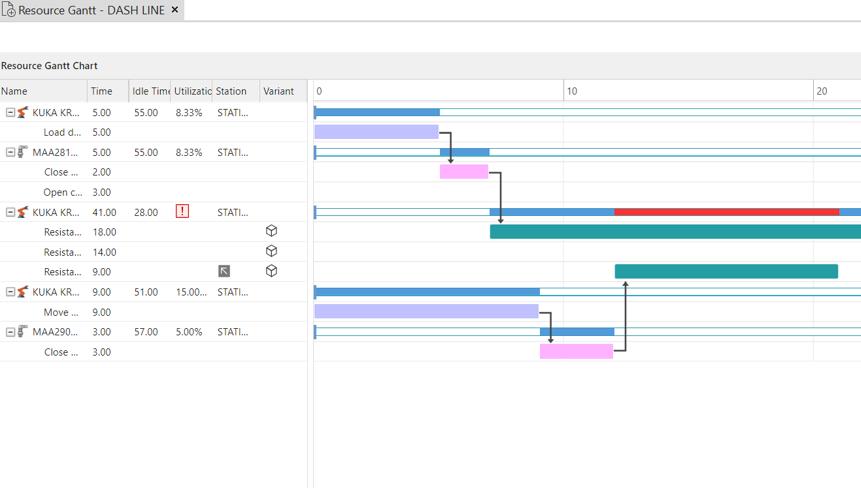
What’s new in NX Line Designer
Performance Enhancements (Minimal Load)
NX Line Designer’s load performance has been improved, delivering 10% faster load speeds compared to previous NX versions. Alongside this enhancement, save and close operations in Minimal Load mode have also seen substantial improvements, with saving now 77% faster and closing 12% faster in both native and managed environments. The Minimal Load – Lightweight Display ensures optimal performance while seamlessly loading additional data during user interactions.
Support for Lightweight JTs
The latest enhancements in NX Line Designer enable you to work efficiently with legacy lightweight JT data, allowing users to easily select snap points on face edges. This simplifies tasks such as moving objects, performing measurements, and adding datum points or coordinate systems. These improvements are especially valuable, as they streamline the definition of connectors, base frames, and tool frames. The Kinematics Editor now offers better control point selection on curves, edges, and faces, further enhancing the user experience.
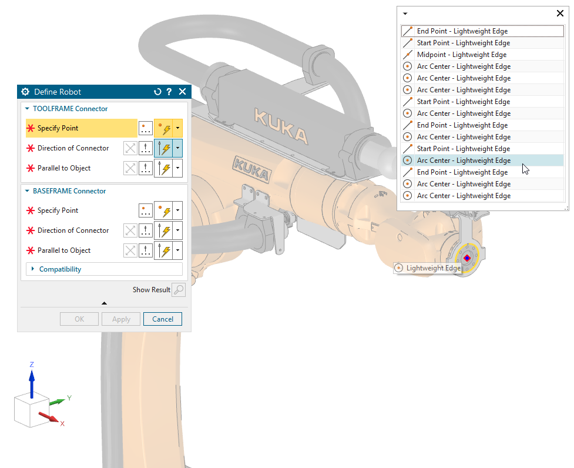
Equipment Kinematics
Equipment Kinematics has seen significant improvements, allowing you to define and manage kinematic interactions between components with greater precision. The new feature enables engineers to define bond constraints that attach components to a moving rigid group, ensuring cohesive motion within assemblies, while also grouping similar components to represent logical behaviours.
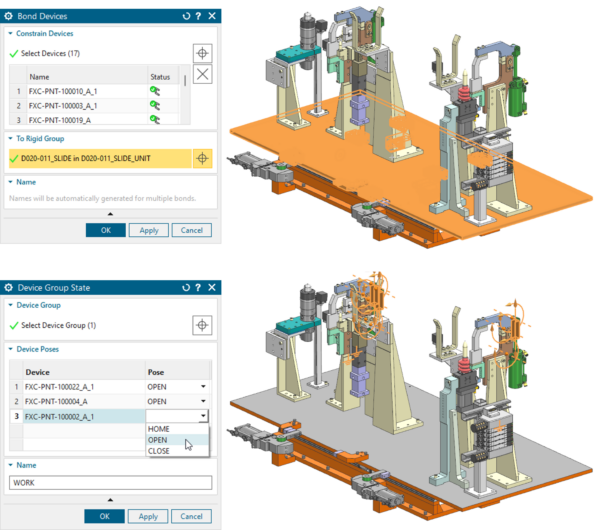
Refresh Teamcenter Information
A dedicated command, “Refresh Teamcenter Information,” is now available in the Plant Navigator to update Teamcenter columns such as Checked Out By, Modifiable, and Read-only. With just a right-click, users can refresh the columns to identify any discrepancies between the revision and version of a loaded part in NX and those in Teamcenter.
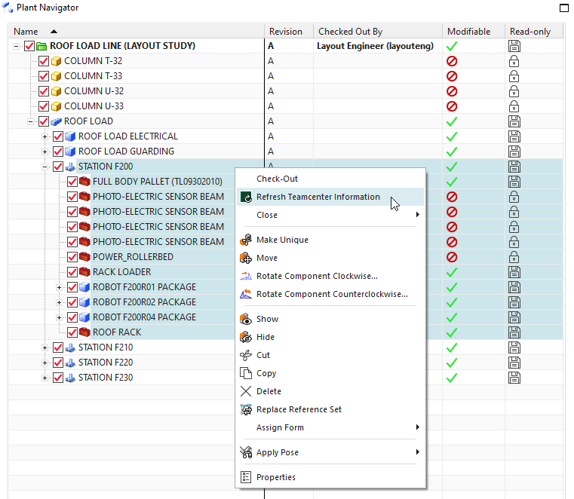
Learn more
Explore NX’s advanced capabilities for NC programming by signing up for the NX X Manufacturing trial. No installation is required meaning you can run NX in your browser, in just a few minutes.
Eager to learn more about the NX for manufacturing features? Check out the step-by-step tutorial videos on our online community.