What’s New in NX 11.0.1 for Design Engineering
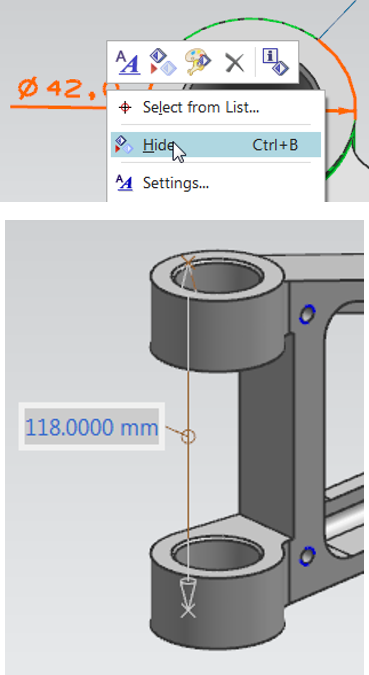
NX 11.0.1 simplifies and shortens the design process. We will start off by discussing the new functionality in NX 11.0.1 for modeling, then we will move into annotation, discuss process and industry-specific applications, and wrap up by talking about the changes in the architecture of NX itself.
Modeling
Topology Optimization is an exciting new functionality in NX 11.0.1. This technology has been around for many years, but the commercial implementations have been limited to CAE analysts. For this reason, topology optimization has primarily been used at the end of the design cycle to optimize a previous design. By enabling CAD users and designers to access Topology Optimization, it can be applied early in the design cycle. This saves time and design cycles and makes for a more robust final product. Siemens is partnering with Frustum, Inc. for the core technology, which is integrated into NX.
The user is not required to be a CAE expert; they need only understand basic loads and constraints. There is no need for meshing either. The design is optimized based on its functional requirements. To define these, the user can designate keep in or keep out volumes such as the box you see in this image. Cylindrical and counter-bore holes can be designated with things like socket clearance. Manufacturing constraints, finite element loads and constraints, and stiffness and mass objectives can all be assigned before optimization, along with material. The result is a highly smoothed, organic shape, though there will be sharp edges if they are required.
The optimized design can be used downstream for additive manufacturing. In addition, the design can be modified using Convergent Modeling.
Wireframe and surfacing are important tools for geometry creation, and NX 11.0.1 delivers enhancements that give you more options and better information to help you diagnose geometry issues.
You now have the option to trim curves to face boundaries, increasing their versatility. In addition, you can trim multiple curves in one operation, select which region you want to keep or remove, and preview the results. This especially helps when trimming multiple curves at once.
A new option in the Offset Curve command allows you to use a pass-through point, or a point where a curve intersects the surface, as the basis for an offset curve created from the edge of the surface. This enables you to make a smarter model that better reflects the design intent.
A warning is generated when a self-intersecting surface is created, either during creation or editing of the feature. Displayed in the part navigator, this warning allows you to quickly find and diagnose problem geometry so that you can fix it before it causes further issues.
This capability adds more options for the designer to incorporate nuances of their technique in surface and curve creation which enables more flexibility and less restriction in their workflow.
Blending has been and continues to be a key part of model design. In NX 11.0.1, edge blending has new capabilities to support unique use cases, like putting a large blend over a smaller one in an area with steps and cases where you have a tapered cylinder close to a tapered wall. In variable radius blends, through-points are now associative, the display is improved, and you can drag a variable radius point anywhere along the edge chain, not just the segment where it was created. These changes mean that you can quickly create blends that will robustly adapt to changes in the design and suit your manufacturing requirements.
The major enhancement in Face Blends for NX 11.0.1 is the option to select Feature Intersection Edges under selection intent. This enables you to use a face blend on a feature where a shared or common edge is the result of a Boolean operation. This means that the blend will update more quickly and adapt better to model changes. This functionality is applicable to many instances where we need the capability to blend our surfaces to one another, with options for aesthetic and function blending for ease of downstream operations like casting or machining.
Draft allows cast and molded parts to be released from a mold and is a critical step in designing parts that are easy to manufacture. In NX 11.0.1, new Draft Body capabilities let you create complex drafts to parting surfaces without resorting to manual methods or workarounds. What used to take 25 steps now takes one, a massive savings in time. Creating overlapping draft is faster and easier, as well. Tool tips provide improved user guidance, reducing the learning curve, and it’s easier to diagnose failures, as well.
The Combine command in NX 11.0.1 is a revolutionary new way of trimming surfaces. It allows you to combine multiple sheet bodies into a single solid body in a single operation. You have the option to select which regions to keep and remove. This functionality, which used to take multiple operations to do, not only adapts more robustly to changes and updates, it’s at least 5 times faster than the old method. It reduces the number of steps required to create a solid body and adds value for all users creating complex shape designs utilizing multiple sheets.
Annotation
Model-based definition, also known as product manufacturing information or PMI, is a great enabler for downstream manufacturing operations. The designer can document key dimensions and tolerance information directly on the 3D model, thereby reducing or eliminating the need for drawings that would communicate the same information. Not only can we reduce the amount of data necessary to be created by the designer, but we can also streamline NX CMM programming workflows and enable offline inspection paths to be created with little or no effort.
PMI and NX Drafting are both used to provide manufacturing and other information about models for downstream use. As such, they have a lot of similar functionality, though the end result they produce is different.
There are a number of changes in NX 11.0.1 that make PMI and Drafting easier to use and more efficient. For instance, the title on settings dialogs will now reflect the parent dialog that it is launched from, making it easier to keep track of what command you are in. The name of the work and target model view will be made bold in the part navigator to make them easier to find and improve consistency with other modules. The ability to select an object in the graphics area then navigate to its related items (such as section and detail views) saves time. Retained PMI Display makes it easier to determine the status of a PMI display instance using embedded alert icons. Enhanced Copy and Paste for PMI with a Paste Special command allows you to paste PMI display instances copied in a model view or graphics window as PMI display instances or PMI Objects, giving you more versatility.
There have been a number of enhancements to drawing views in NX Drafting. You can better maintain data integrity by ensuring a drawing view’s content cannot change with lock view option that prevents any changes to the view content, including view updates. Annotation and location of a view remain enabled.Orient view improves productivity by easily specifying the rotation angle for views during view creation or edit without the need to manually calculate the angle. View clipping improves productivity by eliminating the need to manually remove and restore centerlines and center marks. You can save time by setting the crosshatch parameters for a component across multiple section views at the same time. You can now display only the part of the boundary curve of a detail view where it intersects with the model geometry. This saves space on the drawing and allows more room for other content.
We are constantly working to maintain support for worldwide drafting standards. NX 11.0.1 offers support for the display of annotation on a single annotation plane that does not rotate with the model and locking size and position. It’s easier to interpret GD&T in NX 11.0.1 because you can automatically highlight associated datum feature symbols and datum targets that are referenced by a selected feature control frame. You can also set the NX internal sheet number to zero if needed. Finally, there is additional support for defining view label naming conventions such as excluding allowed letters to begin and end a view label.
Process and Industry Specific Applications
NX contains a large number of applications that are designed for specific processes and industries. Several of these have been enhanced in NX 11.0.1.
NX Tooling design in 11.0.1 has a number of enhancements that give you relevant information more quickly, automate repetitive tasks, and give you more control than ever.
You can now access Teamcenter Perfect Costing (TCPC) from NX and vice versa. In addition, NX has new capabilities tied to TCPC like the ability to recognize capabilities for both mold and stamping components, then manipulate these features to optimize the tooling usage. You can also send necessary information to TCPC and read necessary information like pull vector, which is used for feature recognition.
NX 11.0.1 makes it easier to design and validate dies in a single software environment with capabilities that support complex CAM motion simulation in NX Die validation. “Area calculation” can now output a sheet body that can be used for downstream applications such as modeling. This also makes it easier to it easier to visualize the area of the body. OmniFree Transformer gives the ability to control the magnitude of the curvature during deformation for improved performance and quality of morphing. Numerous enhancements to wall thickness functions support workflows for complex Powertrain components.
Mold design enhancements drive the automation of downstream processes. These enhancements include part family support for cooling fittings, a button to output an EDM format file by predefined template and a button to output eMan data.
Routing in NX 11.0.1 is designed to be more powerful, foolproof, and easier to use than ever before.
An improved Enhance Spline Path user interface is a faster, easier method to control spline shape.You can use dynamic handles to define and manipulate spline extension direction directly. New Setting Overstock user interface options allow pre-configuration of specific usages for overstocks, which reduces overstock errors. Enjoy wider usage of cableway functionality, ensure proper fill conditions, and make more efficient use of standard parts by using cableway properties on parts like clamps, grommets, and ducts. Points on splines can be easily offset from routing ports and multiple routing assemblies can use the same clamp, making it easier to create more realistic designs with better control. HVAC support is improved with things like Stock Transitions, Miters, and Insulation.
Joining and welding are critical manufacturing operations. NX has powerful tools to model and define these operations.
New in NX 11.0.1, the ability to mirror a bead feature and solid body at once can save tremendous time, up to 50% reduction in initial design time. It includes support for identifying the ‘connected parts’ that will be associated to these mirrored features, allows the mirrored features to be associative or not, and includes the ability to change this relationship. This will also save time on updates since only one side will need to be updated.
You can now edit multiple ‘single’ weld features at once. This improves editing performance by eliminating the need to reselect face data and improves accuracy by adding back the original recipe parameters. Finally, you can now create joint mark features as single weld features, making them more consistent with each other for faster learning and reduced training requirements.
NX contains a number of applications and functions that are specifically designed for individual industries. NX 11.0.1 includes enhancements to several industry-specific applications.
In automotive, NX has been updated to conform to the standard Euro NCAP pedestrian protection standard. In addition, the use of base data is more consistent and clearer, showing the source of each value, the ability to read key parameters from base data, and more. Making better use of base data improves efficiency by reducing the time spent inputting data.
In shipbuilding, it is now easier to create multiple stiffeners, all you need to do is select the start boundaries and the end boundaries. It’s easier to navigate the complex design of a ship with a new navigator for Basic Design groups, such as decks, plates, stiffeners, etc.
Architecture
Our last topic is NX itself, the architecture that NX is built on and which all of its functions use.The look and feel of NX is enhanced in 11.0.1 to provide easier understanding and better usability. Graphics improvements include the persistent display of the zoom/scale factor in the graphics window, the ability to orient your view normal to a non-planar face, and the option of a white background. Tooltips can now be displayed when hovering over the non-label area of a selection block, including the icon. Points are now scalable and easier to see. 3D box select lets you control the selection depth and volume size, and it shows what it is and is not selected in the display. Isolate in New window is a new function that lets you take your active displayed part or subassembly and show it in a new window, allowing you to remain in the assembly context while providing improved visual clarity for the specific part you are working on. You can now use selection intent in point offset, point along a string, vector constructor, and CSYS normal to body at point. This makes these commands easier to use and supports important customer workflows.
We are constantly working to improve the performance of NX. In 11.0.1, we have improved the performance of commonly used features and operations like Make Current Feature and Feature Update. This improves the speed of model editing and design changes.
We have implemented a number of changes that reduce file size. The product interfaces architecture has been optimized. Extract feature algorithms have been enhanced to improve feature update performance. Extract feature architecture is enhanced to better manage face and edge tracking, minimizing extract size. Together, these changes improve feature update performance and reduce part file size, which improves file operation performance.
The part navigator is a critical tool that users are constantly interacting with. NX 11.0.1 improves the performance of selecting and deselecting entities from the part navigator. In addition, there are now customer defaults to control the state of highlight like Original and Preview. This improves performance by reducing the amount of excess visuals in the graphics window. Feature groups no longer collapse when features are selected in the graphics window or when changing the work part, making it easier to select what you need.
Process automation allows users to customize NX and automate common tasks.In NX 11.0.1, expression groups are now in the part navigator, so they are easier to find and change. In addition, a number of small enhancements designed to keep expressions up to date, control the visibility of annotations and expressions, and new dialog and user interface options all combine to create a more intuitive and productive working environment.
NX Open is a powerful tool for creating custom applications within NX. In NX 11.0.1, you have more control over dialog boxes with the ability to control width, including maximums and minimums. This makes it easier to create the applications you need, the way you want to.
NX 11.0.1 delivers significant improvements in almost every major area of product design. These improvements will help you get your products to market faster, with fewer errors and issues.