Siemens Xcelerator | Advanced Machine Engineering | Part Three
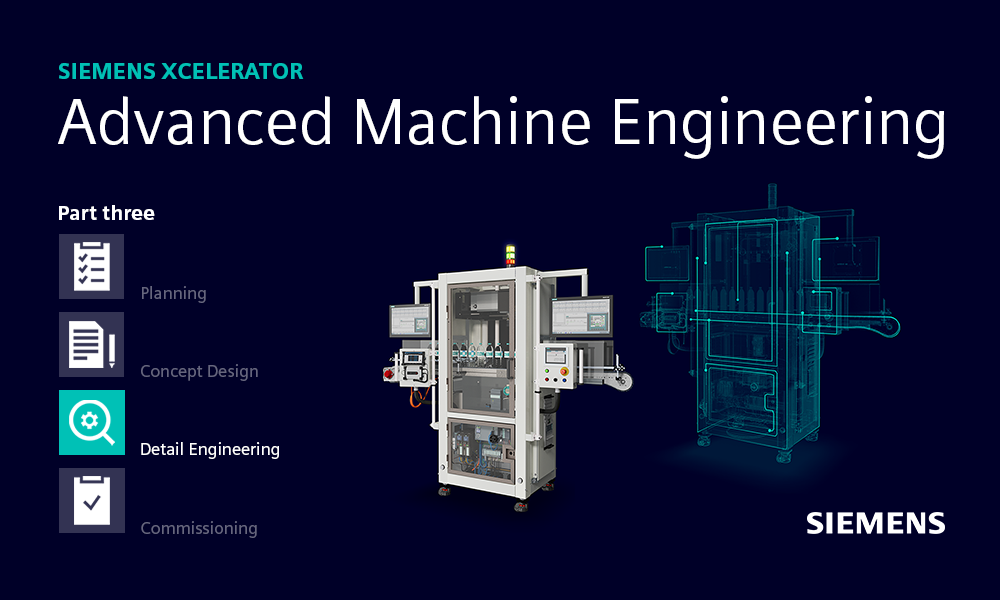
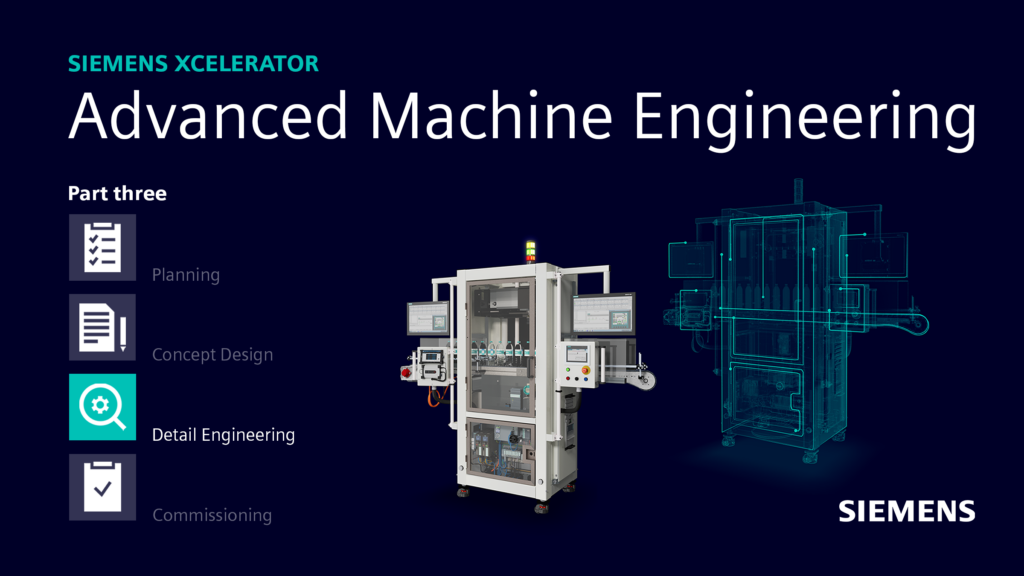
Our third installment of our Advanced Machine Engineering series is here, and we’ll be discussing the detail engineering stage in this process. We see this stage as the context in how we present to the market, and the step where we start bringing together all the final details from the whole process. This stage is important, as this is when we look at any final tweaks, final automation and the structural integrity of the design. These checks are essential before then going through the physical and virtual testing. This is the chance for the whole system to have the realization for what it’s going to need for the physical machine. You now have a concept of what hardware you’re going to use, how you’re going to apply it; and start pulling together the application, based on what you did in the design.
Then vs now
Let’s start by taking a look back at how this stage used to be, compared to the present. Back then we theoretically completed this stage by waiting for the machine to be ready. You start with what would be the first part of the machine, which would be safeties and diagnostics, and then you’d start slowly ramping up manual mode or auto mode to work through the machine. In today’s world, with the opportunity to work together with the mechanical people earlier on, like we’ve said previously, we want to break down the old paradigm of mechanical builds. In this new way, the objective is to take out any room for delays, especially from the automation design, and do simultaneous engineering.
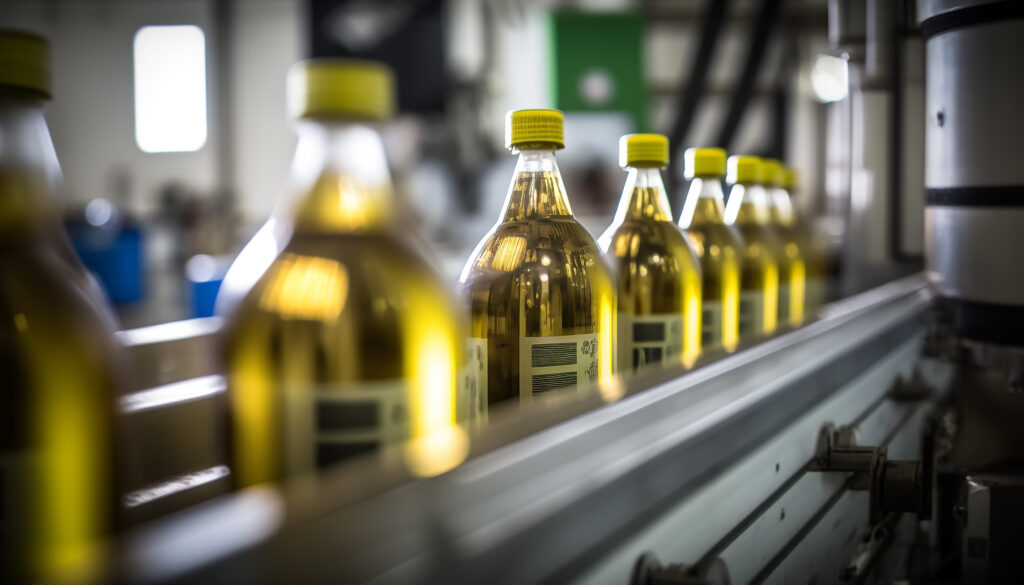
Challenges in the detail engineering phase
Every phase, of course, comes with its own challenges. In this phase of the process, it’s all about the communication and getting the design done. The emphasis really needs to be on how important the cross collaboration is between each layer of the design process. Like we said in part one of this series, to not collaborate early on, will cause bigger issues down the line. Working together, and with an integrated solution, like Siemens offers, is hugely beneficial to the overall process. A huge part of this challenge is changing the mindset of people. If electrical people and designers have worked in the more ‘traditional’ way for years, then bursting that bubble that they know, to make them collaborate sooner can be challenging.
One of the big changes today, versus maybe ten years ago, is that we have the ability for everybody to use the same model. This way, we can offer end to end support, especially at the detailed design stage. We receive very good feedback from our customers that embrace the master model, that all the engineers, from different organizations, can all use at the same time. This can very easily make sure every person is at the same stage, with the same data and avoids misunderstanding.
Saving time and money
The big one. The benefit that all companies want and need to hear from implementing any new strategy. By communicating all information up front, and getting everybody involved up front, you’ll get the machine done sooner, with less cost and improved quality. Alongside this, and something we’ll look at more in the next part, as you can do it all virtually, you will save your customer time and disruption when you’re installing the machine in their locations.
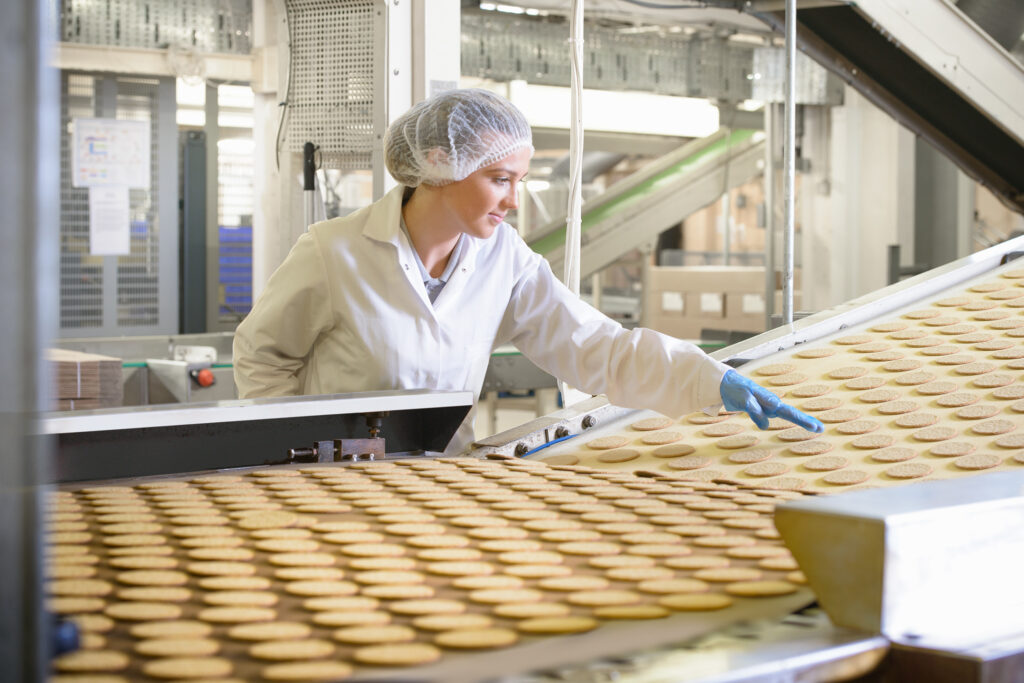
The introduction of this happening virtually saves on shutting down factories, or their flow of working. This way of working also improves the quality. If you can virtually test on the computer, it doesn’t cost you physical disruptions. You’re not risking breaking parts, or anything physical. Saving on not running through prototype parts and building parts, is a massive saving in material and time.
In short, collaboration increases communication, and saves time and money.
Importance of the Siemens reuse strategy
The biggest thing from a detailed engineering part about reuse, is reuse really is another area where you can save a ton of time and improve quality by reusing designs over and over again. This is especially important from a mechanical design perspective. Look at NX; we have the ability with our Shape Search to see if we’re looking for a new part. Did we already create a part exactly like this or similar? Can we use this as a starting place for the design? Utilizing that can really help you reduce your inventory and reduce time to market by using parts you already have in stock. In addition by reusing proving designs your company is reusing their intellectual property.
Total Integration Automation
Siemens Automation brings forward the most complete system centric approach. With the Total Integration Automation, (TIA) portal we can help you standardize with Siemens. This allows you to scale up from a small base of functionality to more advanced controllers, and same with the HDMI, and we’re able to do this in a system based approach. So that you have the entire automation system in one project file or build the entire automation from reusable objects that are known to perform the expected automation.
Mechanical geometry can be reused, but also the dynamic physics defined. When you drag a component from NX Mechatronics Concept Designer (MCD) library to the graphics you can get all the physics predefined. Then you can start the simulation directly, without any movement or defining the physics for the subsystem. This, again, saves time, especially for beginners or new users. Reuse strategies help a lot, and for different customers or users they can implement the reuse library by themselves. Siemens provides very good templates and documents to support this, especially for new users of NX and TIA portal.
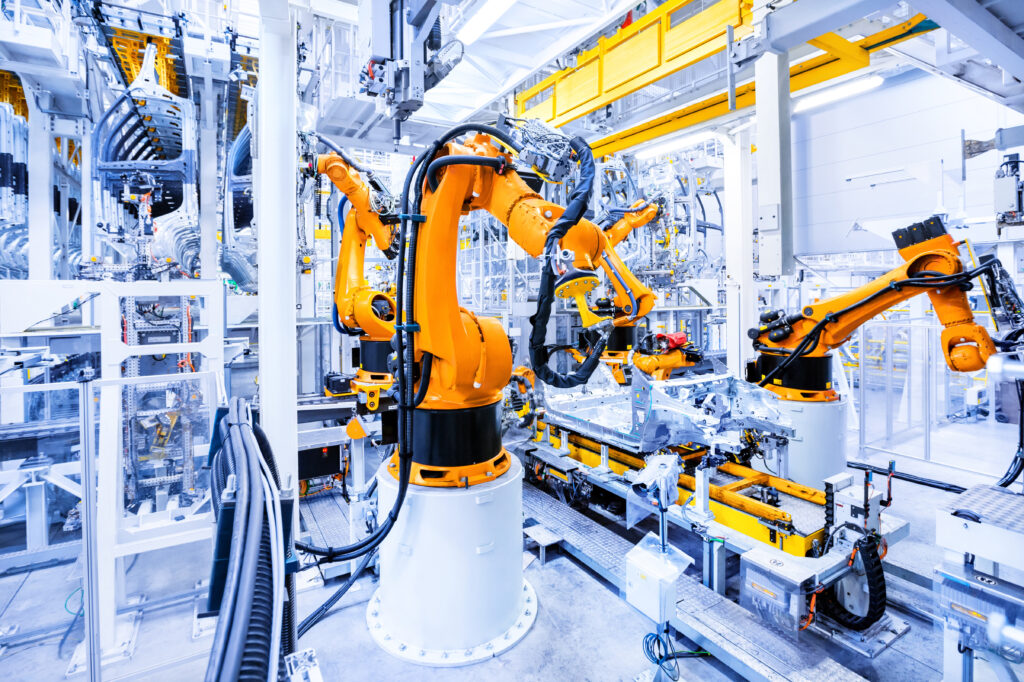
Conclusion
That draws this section to a close. To sum up the detail engineering instalment, the main takeaway is that you have to evolve your process, and you have to get all your people on board to do that. Sometimes that’s the hardest thing, but Siemens Advanced Machine Engineering is here to support you, and your organizational change management. Stay tuned for the last part in this series!