Siemens Xcelerator | Advanced Machine Engineering
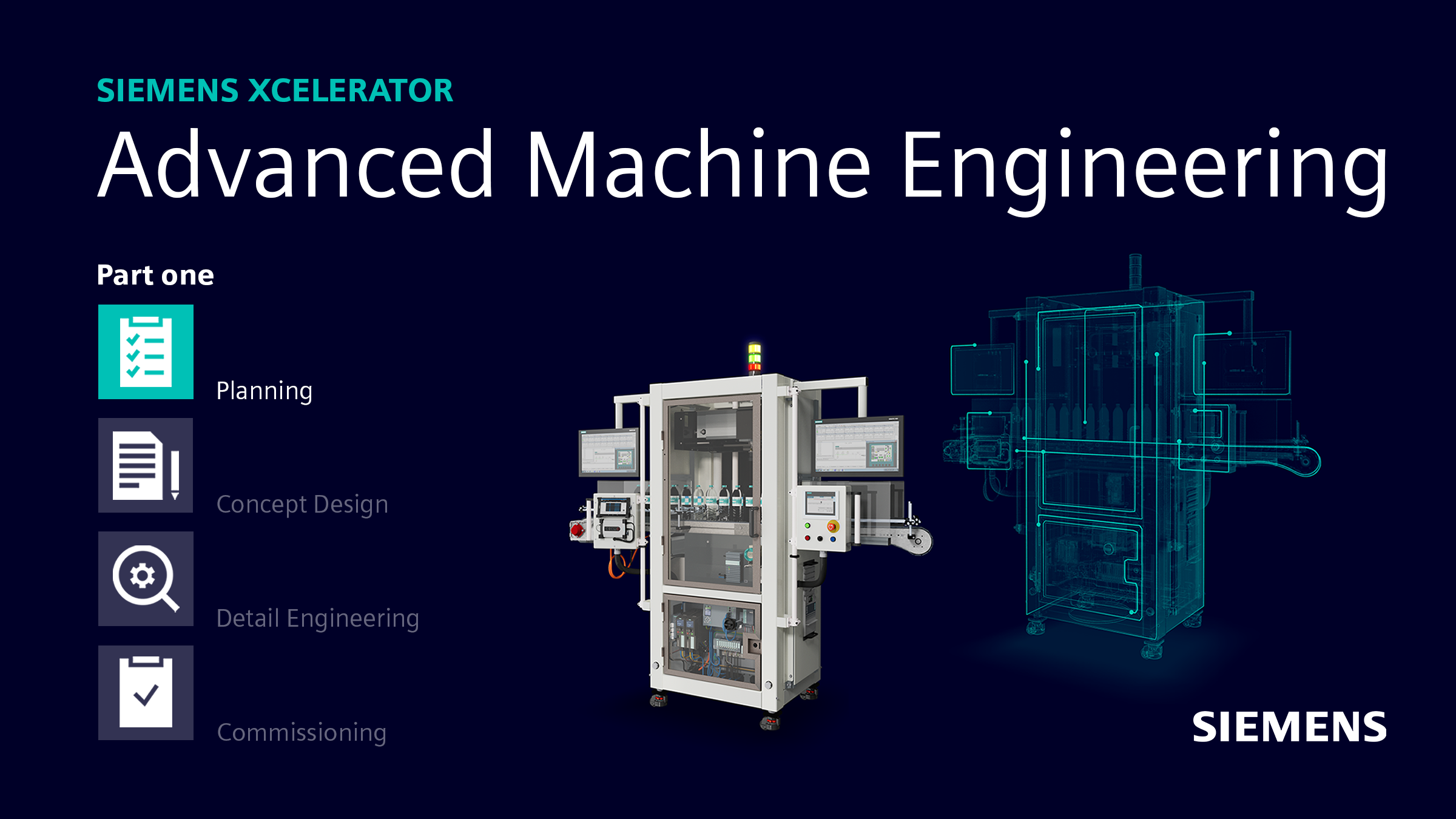
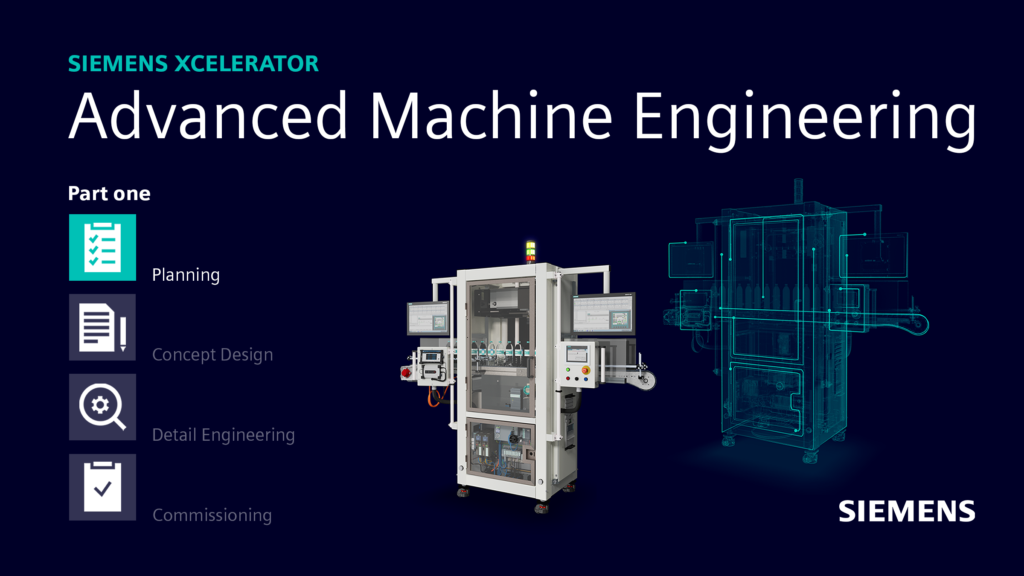
Part one of our new blog series is here! We’re discussing the Siemens Xcelerator Advanced Machine Engineering solution, and how this can support you with the lifecycle of their product. Traditionally, all parts of the machinery design process were kept very separate. The automation expert was separate from the mechanical expert, and the mechanical expert wasn’t collaborating with the electricals expert, and so on. This way of working meant that if any changes were made early on, in say the electrical part, it wouldn’t filter down to the other layers of the cycle. This lack of collaboration had a huge knock-on effect on costs, time and overall support of the machine engineering lifecycle. Today, Siemens brings a new design tool that can vet all the connecting work from each layer, to make the running of the design as smooth as possible. We can determine early on if the design requirements can meet the goal of the product and the production. Let’s look at the planning stage of this in more detail!
The multidisciplinary approach
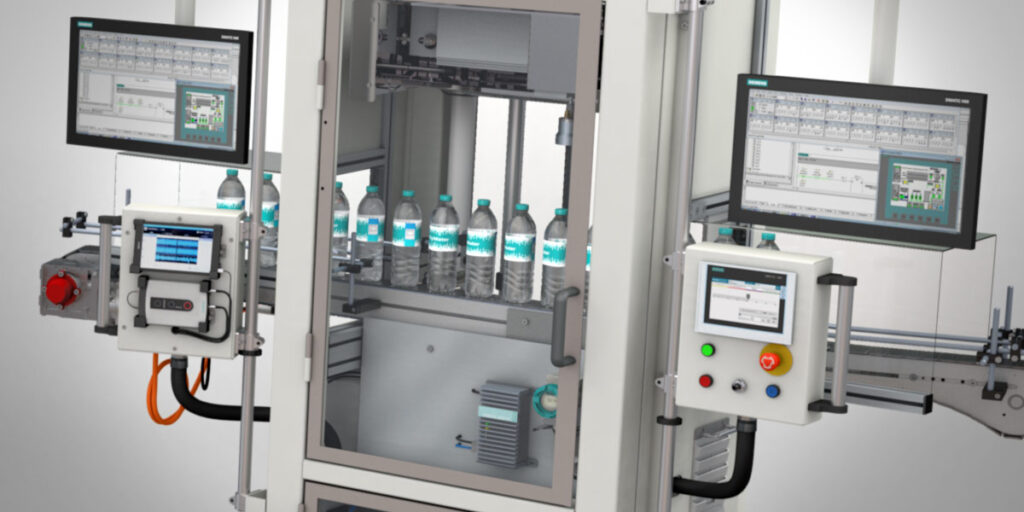
It seems appropriate to start our planning instalment with the actual, how? Different types of engineers, all throughout the process need to align, and this can sometimes be challenging. In the past, this has been a very sequential operation.
However, today, we are promoting and offering a multidisciplinary approach. This means that our customers, and the mechanical, electrical, automation and software engineers can work in parallel, instead of a series. Having this early collaboration between different specialisms allows the space to verify potential issues earlier. Do you have the right flexibility? What level of mechanical sophistication should you apply? Are there different variations of a product on the same line? Creating the environment to have these discussions early on means we can make critical decisions, when the cost to make those changes is low. We understand that one of the highest priorities for any company is to reduce costs, and with advanced machine engineering and early planning, this can happen.
Importance of Aligning Product Design and Performance
As we’ve mentioned in the introduction, the aligning of product design and the performance is key. The objective of what Siemens is doing today is ensuring all parts of the process should be aligned at the earliest point. Collaborating from day one to achieve the end goal is essential to having an effective lifecycle. In the early stages, it’s very important to look at your standards. For instance, paying attention to what you reuse and repurpose. In short, looking at the standards you can develop on each side, i.e. the mechanical, the electrical, and the automation side, to strive toward rapid engineering of the new machine.
If you have a completely different production line, manufacturing line and performance expectation based on the product that’s going be at the end of the line, then that determines the level of complexity in the production line. Whereas the ability to have these collaborating early on, even with the inevitable changes to variants as the product develops, simplifies the overall process and makes each stage, for each expert, much more efficient.
Challenges in the Planning Stage
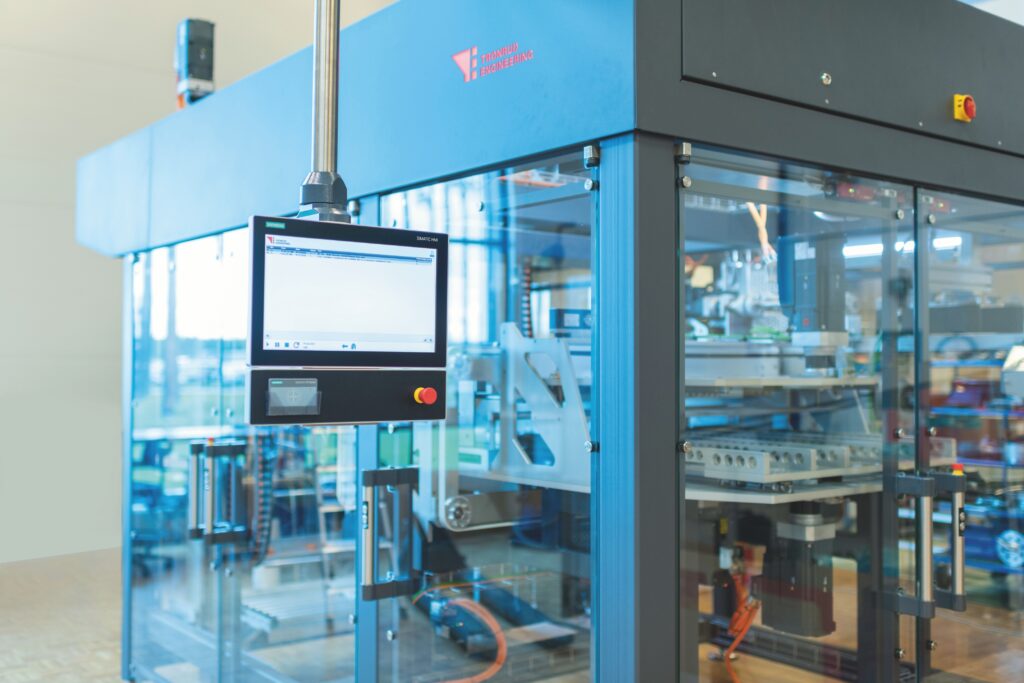
One of the biggest challenges at this stage is determining the ‘what ifs’. Like we’ve said earlier, in the past this is all vetted physically. But with our software tools that exist today, we offer the opportunity in that planning stage to prevent any major issues. Let’s say the machine builder has already started building the physical machine, and then the automation engineer notices a huge error and needs this amending – this is very difficult, and time consuming. But with these checks now possible in a virtual world, you can avoid this costly error.
This rolls into the next point, building prototypes. If you’re bringing a new machine to market and you have part of the machine that you want to test, creating a physical prototype is difficult. How do you then decide which prototype you build and test? In machine building you have many different variations, but for a company to put money, labor and time into building all the possible variants is redundant. We understand no company can, or be expected to fork out the cost of this. Only with advanced design and simulation tools, that we offer, can you achieve a prototype that’s so close to what you require, and meets the demands of the machine and the customer.
Handling Large Numbers of Requirements
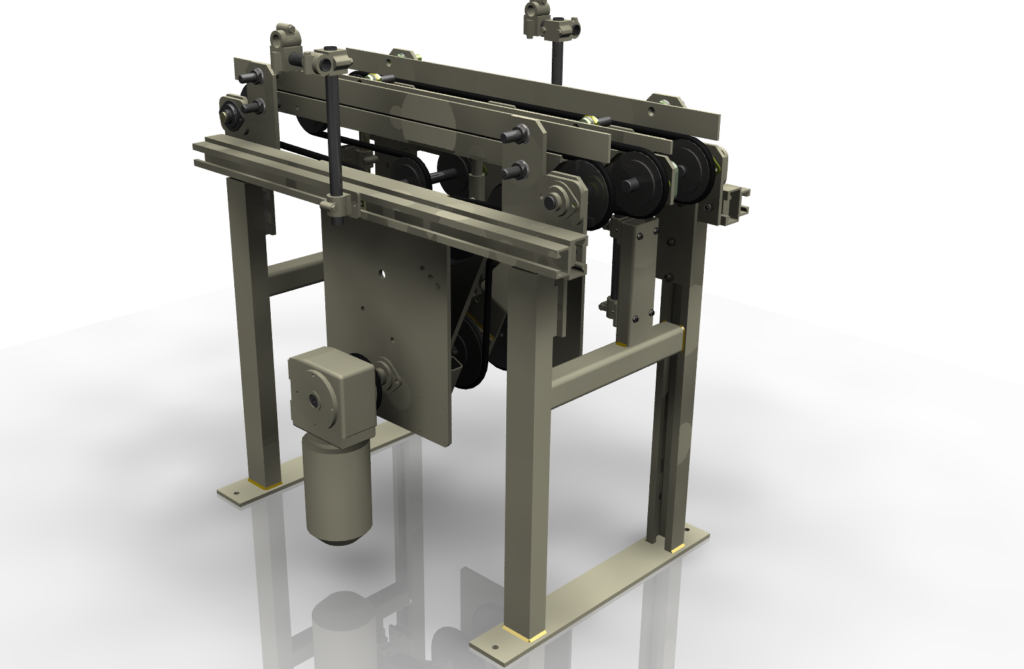
An important and very valid concern that we hear from customers is doubt around handling large numbers of requirements. We understand this completely, as customer requirements change frequently, and this can cost companies a lot of money. This is especially prevalent without clearly defined or mapped requirements. One of the strongest elements we offer within our solution is to be able to tie requirements directly. We can clearly document what requirements are expected and can link this; with this being the key component here. A solution being able to link all those requirements across the process, from mechanical, electrical and software, is absolutely critical.
We offer a leading toolset, where if the requirement were to change between the original equipment manufacturer (OEM) and the machine builder, we provide security. We have a system navigator that can integrate the requirements from the Teamcenter side, and integrate them into the NX side, while tracking them for machine design. Users are also able to create requirements and list the details that are necessary. For instance, let’s say a user wants to control the speed from one to another behavior. The user can create this in the navigator and list it. Once the development is done, they are able to use the navigator to track all the requirements and show the OEM that all the functionalities can fulfill the requirements.
Tracking Maturity of Product Development
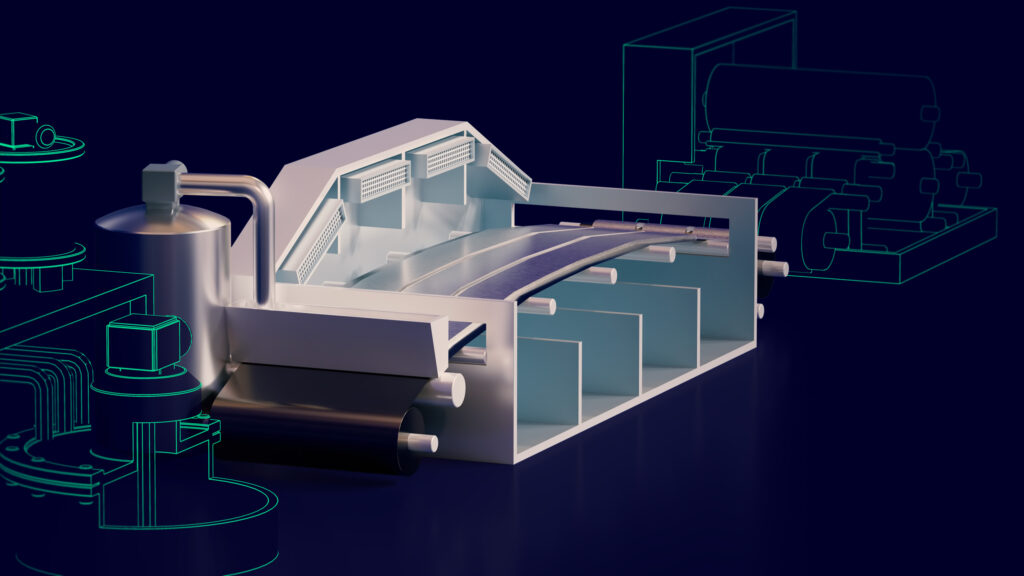
Whether you’re a designer or not, looking at a product and imagining all the data that is associated with that, is a lot! Imagine a soda can for example. Everything around the size, the material, the way it works, involves a lot of data. And tracking the changes in this can be a difficult task. However, with Siemens Xcelerator, our tools can manage every part of that data around the machine. From the CAD drawings to the electrical drawings and automation programing, every little thing associated with it, that brings the product to life.
Managing Change across Product Evolution
Any change made across any layer of the design affects each other. Whether a change is associated with the mechanical layer, or the electrical layer, these changes have a knock-on effect for each component of the design. This is a key aspect that we help with. Traditionally when changes like these are just left to email, or verbal communication, it can get messy and chaotic very quickly. And let’s say you are wanting to change the scale of your production, and you’re going from five machines, to building ten a year, this isn’t going to all be handled in a spreadsheet through emails. Each of these machines will requirements changes and modifications, like we’ve discussed, and that’s a lot of data for a phone call or email to handle.
“This is where NX steps in. You go from ten to a hundred machines, you need the design tools that can keep up with that to make those changes and iterations very fast. So, you need one of the most powerful modeling tools available to do that.”
Scott Felber, NX Marketing Manager
You need a secure system in place that can manage all the data associated with each machine and all the changes connected to that. These systems are part of our Siemens Xcelerator, and are capable of handling just that. Our solutions, NX, TIA Portal and Factory Automation hardware integrate and work together to handle the changes that we understand inevitably come with any product through the lifecycle.