“Gripping” the future: How Generative Design in NX is transforming engineering
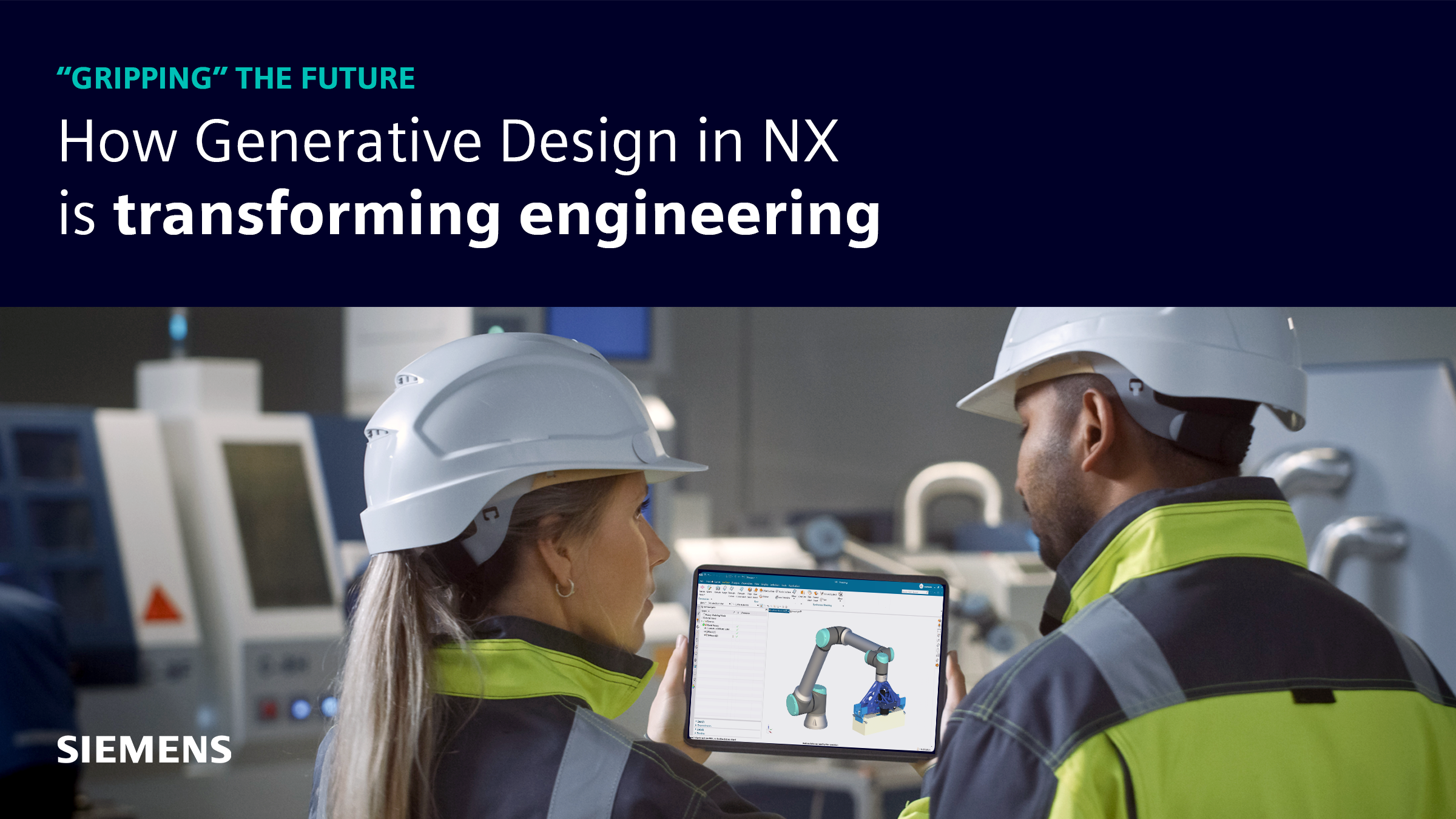
At the 2023 Hannover Messe, Siemens CEO Roland Busch warmly welcomed German chancellor Olaf Scholz to our booth for a discussion on the company’s core values. Emphasizing Siemens’ enduring commitment to innovation for a brighter future, the spotlight was on a remarkable piece of technology: a generatively designed, additively manufactured robot battery gripper, displayed at the bottom left of the picture. This cutting-edge component exemplifies Siemens’ dedication to pioneering solutions that have a positive impact on our world.
Small reductions – big savings
Why is a seemingly basic component like a robot gripper worthy of presentation to the Chancellor of Germany? It’s a matter of numbers. A better gripper design can save up to 3 tons of CO2 emissions per robot per year. The industrial robotics sector is experiencing rapid growth, with an average yearly increase of 11%. As of 2021, over 500,000 new robots are being deployed annually, contributing to about 3.5 million robots worldwide by 2022. To grasp the scale, consider this: the average robot arm weighs about 1 ton, while its accompanying gripper weighs around 21kg. This gripper, responsible for lifting batteries with an average weight of 12kg, may seem insignificant on its own. However, when the robot arm is operating continuously for a year, it produces about 5.6 tons of CO2 emissions. The implications become staggering when scaled to the entire population of existing robots. What if we could significantly reduce the mass of just the robot gripper, which constitutes a mere 2% of the entire robot?
Imagine for a moment that you could design a robot gripper that is not only as functional as the original but also substantially less complex. This gripper would consist of just 5 carbon-reduced PA 12 (Nylon 12) parts, an 84% reduction from the 30 aluminum or steel parts typically used. Not only that, but it would be 90% lighter. And guess what: instead of a lengthy lead time of over a month, this advanced gripper can be produced in just 2 days. It may sound like a fantasy, but I assure you, it’s not. With Generative Engineering in NX™ software, this possibility is within reach today.
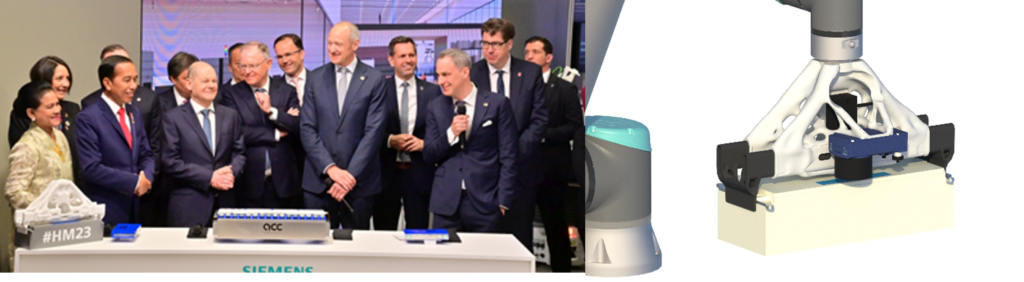
Out with the old – design, build and test
Let’s take a step back to the very roots of the design process. Throughout most of human history, and even until recently, the validation of a design was only possible after manufacturing, often through direct testing in real-world conditions. The triptych of manufacturability, esthetics and functionality has always been paramount for a successful design and all three aspects were required to be satisfied.
Naturally, ensuring a component’s manufacturability was the initial concern to ensure feasibility. However, this often led to the unfortunate realization post-construction that the design lacked functionality, necessitating design modifications before construction could start once again. Only to realize, even after addressing functionality concerns, the design is not fulfilling aesthetic requirements, and the cycle would repeat. What a waste of resources and time!
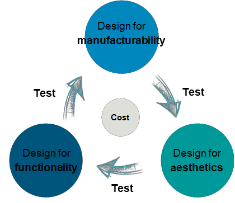
In with the new – simulation-driven design
In response to these challenges, new simulation-driven design techniques have emerged to help designers and engineers innovate and meet functional requirements more effectively. One of the most prominent advancements is topology optimization, a technique that, based on input boundary conditions and a given design space, returns the optimal material distribution. However powerful, those new solutions are often complex and require deep understanding of optimization theory. As a result, they were mostly targeting stress engineers and were not suitable for early-phase design by designers. Furthermore, these tools could only be used to provide design guidance as the resultant format was incompatible with the design process, and signification manual effort was required to reconstruct the results in CAD formats.
The traditional Designer and the emerging Maker user personas have much to gain from a CAD-system integrated designer-focused solution. Such a tool should be intuitive and easy to use, particularly in the early design stages, enabling users take the right decisions without requiring deep understanding in structural optimization and analysis. NX Topology Optimizer fills this gap as an NX-native generative engineering solution, seamlessly integrated in the NX platform.
NX Topology Optimizer
One of the key advantages of NX Topology Optimizer is upstream and downstream associativity. This means two things: any changes made to input requirements will not disrupt existing results — they will simply update accordingly. Likewise, modifications to the topology optimization results will not interfere with existing downstream operations—they will also update with a click. Furthermore, the solution is GPU-accelerated, delivering unparalleled speed compared to traditional CAE-based topology optimization solutions.
The resultant format produced by NX Topology Optimizer is a smooth body, easily editable within the NX environment, making it compatible for use in any downstream operations within the NX ecosystem. By utilizing Generative Design in NX, the challenges and limitations associated with the traditional design process are effectively eliminated, paving the way for enhanced efficiency and innovation.
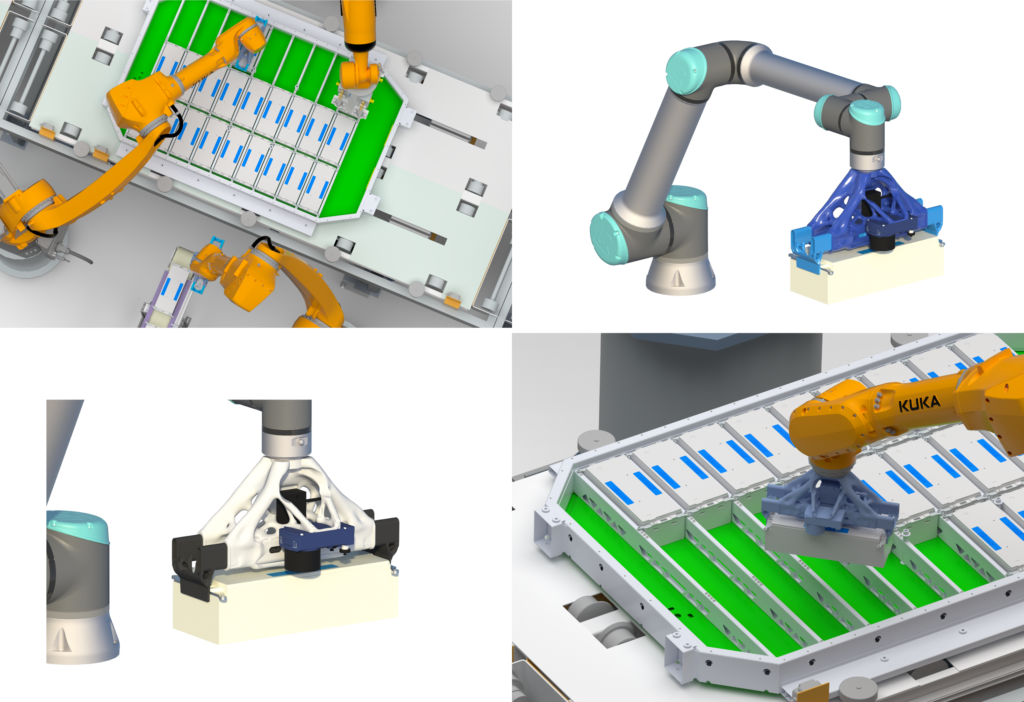
Generative Design to streamline development
So, what’s in it for you? Dennis Nier, business development specialist in Additive Manufacturing at Siemens Digital Industry Software, offers a precise answer to the question of why designers and engineering managers should invest in a Generative Design solution. “For designers, Generative Design simply generates entire lightweight components within a safety factor, eliminating the need to design and calculate every detail in the early phase.”
Generative Design streamlines the design iteration process, allowing for rapid exploration of design alternatives and empowering creativity. Dennis Nier explains further, “For engineering managers, investing in Generative Design translates to tangible benefits such as reduced product development cycles, lower material usage, decreased manufacturing costs, and meeting company directives such as net zero target.”
What about the complexity of the final part? Should it be a worry for designers? Dennis is clear, “I wouldn’t even talk about complexity here. The components will look different with generative design. The geometries will be more organic and will no longer contain the typical right angles and blocks.” NX Topology Optimizer is a manufacturing aware solution-by including the so-called shape constraints in the optimization, the solution returns manufacturable designs with the intended method, be it subtractive or additive manufacturing.
“Everything is also associative.”, he continues. “When design changes are made, the change automatically extends through the Generative Design geometries. This way I have much faster design iterations.” Regarding the resultant format advantages Dennis says, “Thanks to NX Convergent Bodies, the organic structures can also be further processed directly and sent to the 3D printer without having to remodel everything manually as with other solutions.” So, what initially seems complex makes our lives much easier and more effective.
Another common worry for designers is the learning curve of a Generative Design solution. “When we look at all the benefits, it is clearly time well spent to learn the generative design functionality in Siemens NX. You just have to learn its methodology, which usually works well after half a day”, Dennis said. “NX Topology Optimizer is easy to learn because the solution is fully integrated into NX and can therefore also be used in the familiar user interface”, he continued. “It behaves like well-known features such as Sketch or Edge Blend and is an element in the NX Part Navigator. Please just try it out, as it’s also fun to watch the organic geometries grow.”
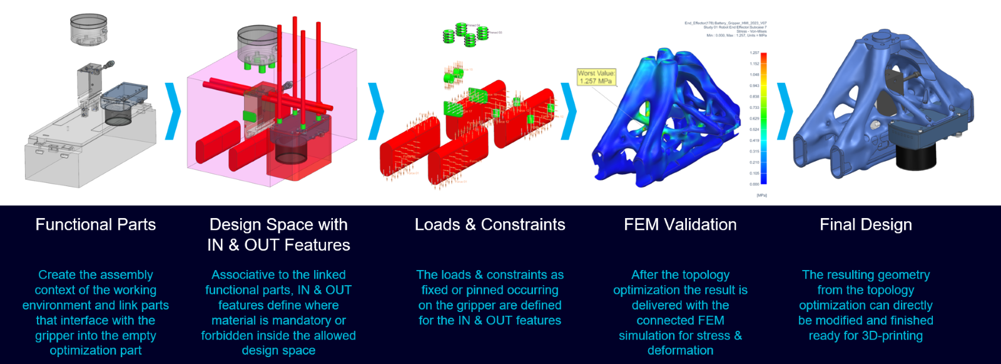
Finally, I ask him what he thinks about the full integration in NX. “It is an absolute advantage.”, he claims. “The process steps before and after Generative Design offer optimal and efficient use. From determining the right load cases in NX Motion for optimization to the final simple design validation with the NX Performance Predictor. Finding the optimal position for your setup with NX Design Space Explorer, prepare your geometries for manufacturing with NX CAM or NX Additive Manufacturing build preparation.”
Summary
In conclusion, NX Topology Optimizer, one of many puzzle pieces that make up the entire end-to-end Siemens Xcelerator portfolio, shifts the focus from traditional design constraints to performance-driven outcomes. As Dennis Nier aptly put it “Generative Design with NX Topology Optimizer simplifies complexity, making our work-lives easier and more effective.”
Comments
Leave a Reply
You must be logged in to post a comment.
eHallPass is a digital hall pass system designed for schools to streamline and track student movement.
ehall pass login