Consolidating 3D Printing Tool Chains to Mitigate Risk in Medical Device Applications
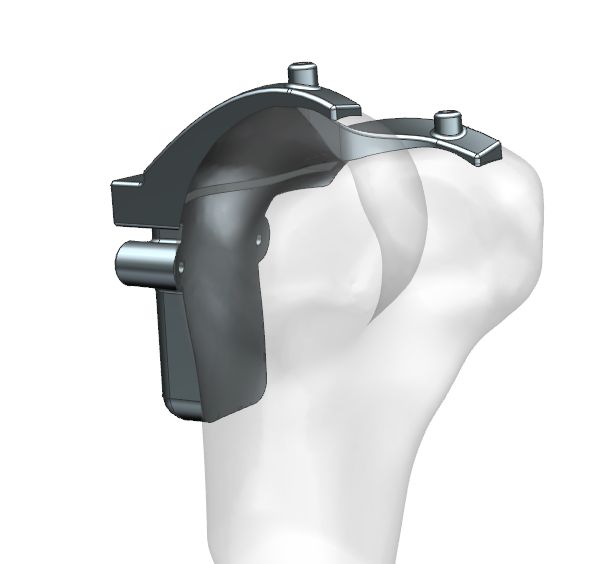
Use of 3D Printing technology to create medical devices has been widely publicized over the past several years. Most of these stories illustrate the unique ability for 3D Printing (aka Additive Manufacturing / AM) technology to produce highly complex organic shapes.
Examples of 3D Printed devices with complex organic shapes include individualized “3D twins” of patient anatomy for surgical planning or teaching, as well as individualized prosthetics, implants, and surgical instruments. With a growing number of materials, as well as improved cost efficiency and accuracy of printers, the diversity of AM-powered innovations that enable organically shaped and individualized devices has the potential to continue to grow rapidly. Expanded growth predictions also come from a second scenario, where AM can be a preferred production method for standard-shaped, non-custom parts. When production lot sizes are small, efficiencies with AM can be realized by eliminating tooling, fabrication operations, and assembly processes.
However, despite past success with AM, and very promising growth opportunities, there are significant risks with the current AM practices for workflows in device design and manufacturing. These risks must be recognized and addressed by device makers to fully realize the potential of AM, and avoid failure modes inherent in current practices.
Today, the biggest risks are caused by software “tool chains” in which different, specialized software applications are used sequentially to yield finished devices. A fundamental problem with serial tool chains is rework. What happens when you get off the “happy path”, and issues are discovered in the fourth, fifth, or tenth tool in the chain, and resolution requires a change in the first or second tool in the chain? That typically means serially reworking the entire workflow from the point of change.
This kind of rework should be viewed as expected, normal, necessary, commonplace, and even desirable since it theoretically leads to an improved final result. However, as AM attempts to enter an “industrial” stage of maturity, there are several risks associated a serial tool chain, especially if rework is manual and requires experts to re-do knowledge-intensive rework.
One risk is assuming that small, minor downstream changes can resolve issues, as a way to avoid a full repeat of the workflow.This often occurs when the upstream rework and tools are outside the experience and expertise where the downstream issue is identified. A classic example of this is a seemingly benign change made in manufacturing that doesn’t fully contemplate the impact on design function or design failure modes.
Another risk area is related to scalability of the serial tool chains. In development and startup production phases, experts craft detailed steps in each tool. But to scale up, less knowledgeable resources are trained to perform individual steps, without an in-depth understanding the entire workflow, and insensitivity to effects of small variations in work that may result in big problems. This is the Six Sigma challenge – to produce overall high quality consistent results requires very small variation and tight controls in each step. Furthermore, when scaling up, there is increased risk of errors in the tedious administrative file keeping of inputs and outputs across all the tools in the chain.
In the healthcare industry, where medical devices produced by AM tool chains may be Class III devices, i.e., where the health and safety of patients can be impacted, these risks must be mitigated. Fortunately, there is a well-understood and proven mitigation strategy available. The strategy is re-use of mature traditional manufacturing practices and technology, originally developed to support “subtractive” NC (numerically controlled) machining manufacturing methods and technologies. This approach has been in widespread use for decades, and in Siemens NX current product offering, is now re-purposed for AM:
- consolidate the tool chain onto a common platform, to concentrate and common-ize the technical expertise necessary for the workflow
- link the outputs and inputs in successive workflow steps so that if there is an upstream change, the downstream impact can be immediately, and automatically determined
- when possible, automate the updates of downstream workflow outputs, triggered by new inputs
Specifically, Siemens NX has comprehensive, integrated applications for AM design, topology optimization, print preparation, print simulation & execution, and post-print manufacturing processes.
Visit our website for more technical details about this exciting and transformative technology.
And, please contact me if you have questions about how Siemens can help you “industrialize” your use of 3D printing technology for your Medical Devices.Additive manufacturing