The bigger picture of implementing a global labeling system (GLS) for medical devices
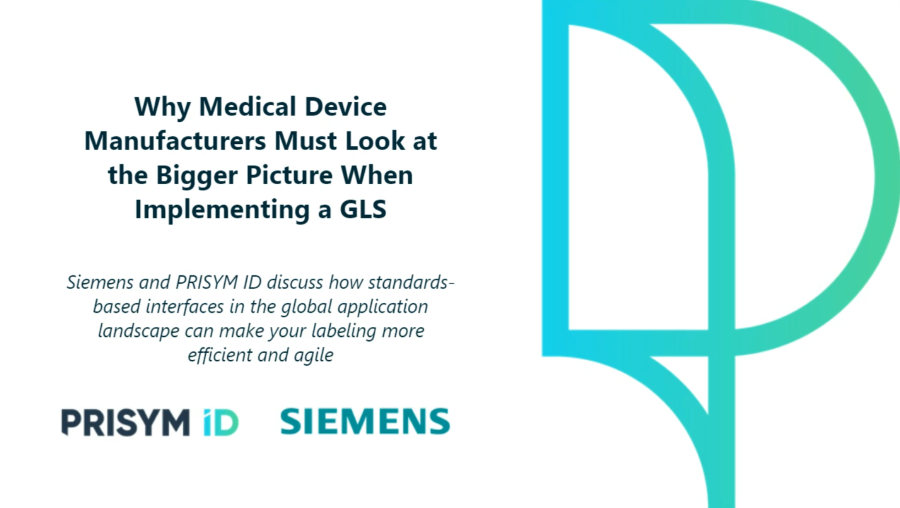
With the increasing complexity and risk in the medical device industry, the need for end-to-end labeling is critical. The ability to integrate labeling should be a core process for medical device manufacturers. The demands that organizations are battling can pose both a great challenge and a great opportunity for labeling.
Why a global labeling system is critical
Medical device products are marketed in as many regions as is commercially viable for the business. This can lead to operational complexity with scenarios where many divisions supply different product lines in the same geographic markets. Often, manufacturing in multiple production sites – both within the region or internationally – need to localize the products to meet country-specific market requirements. This can result in many product variations and stock-keeping units (SKUs). The resulting international supply chain then becomes vulnerable, affecting the manufacturer, supply of medical devices, patient safety and the reputation of the company.
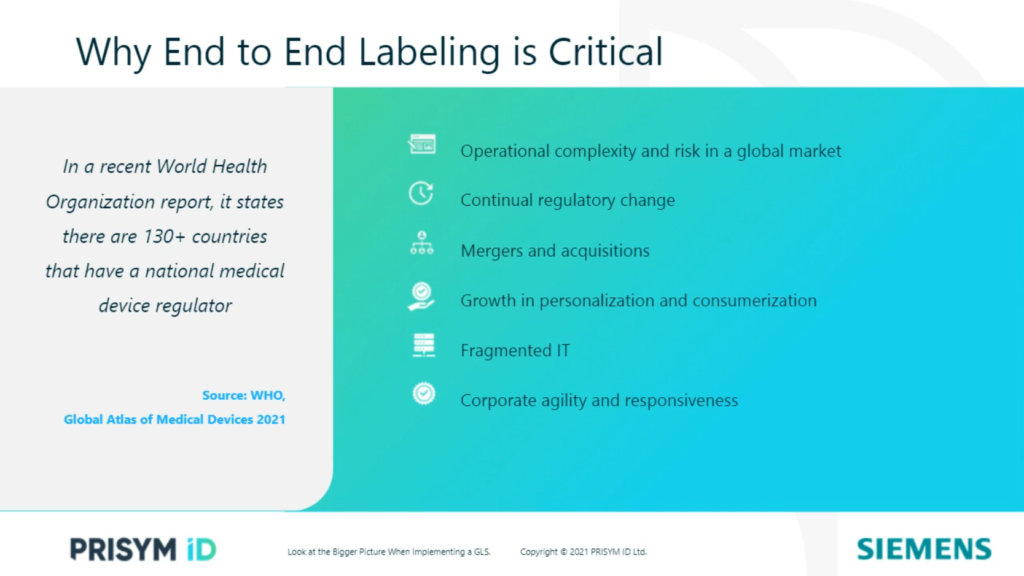
If labeling systems are not properly integrated into product lifecycle management, change control and manufacturing systems, the creation of scalable end-to-end labeling becomes complicated. When it comes to integrating a GLS, there must be an increased adoption of an agile mindset within an organization. This is a necessary catalyst for an organization to become more responsive, collaborative and customer-focused. However, achieving this necessitates systems and processes that can meet that expectation for agility. It is how medical device manufacturers respond to these challenges that will ultimately determine if they succeed.
The labeling data journey
When discussing end-to-end labeling, we must examine the labeling data journey. The labeling data journey starts with user needs and carries all the way through to label production and the device history record. True transformation of labeling processes needs to consider and support all the steps along the journey.
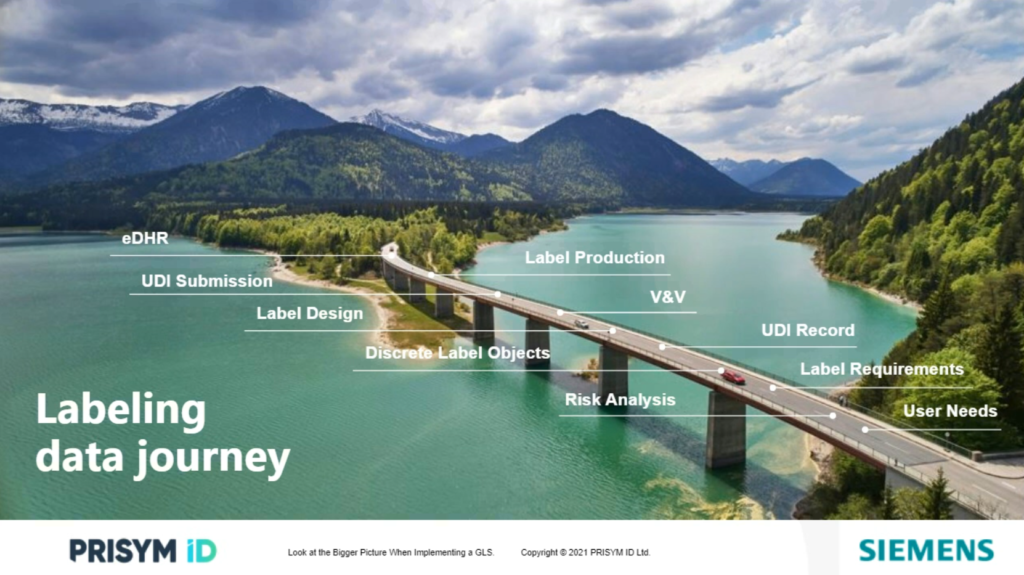
User needs must align with one or many risks, which leads to one or many label requirements. As the discrete labeling content is being defined, it needs to be applied to many design outputs, including packaging, instructions for use and product and packaging labels. Unique device identifiers (UDI) are also important to this process with label content and records submission required to a growing number of regulators around the world.
After defining the labeling, the labels must then be designed and tested through verification and validation (V&V) in order to use them in pre-market submissions and then production. UDI records themselves must be communicated regulators, and production must follow an enforced specification that they are in. Lastly, the production records must capture label content and inspection results in the electronic device history record.
Siemens offers the foundational infrastructure to connect all of these elements along the labeling journey. With vast experience in design and production through digital transformation, end-to-end labeling is possible.
The bigger picture of implementing a GLS
The complete digital integration of labeling data eliminates many of the compliance issues that lead to MCRs and field actions. Learn how to implement a global labeling system today.
The following webinar will discuss:
- Best Practices – Gain knowledge of best practices and advice on integrated labeling system architecture and configuration.
- Compliance – Understand why PLM, MOM and GLS solutions are linked and need to be closely aligned to ensure regulatory labeling compliance.
- Control – Get insight into controlling process flows for synchronizing creation, approval and change of product and label data.
- Integration – Realize why integrating labeling as a core discipline is key to your manufacturing process.