Simcenter Battery Design Studio
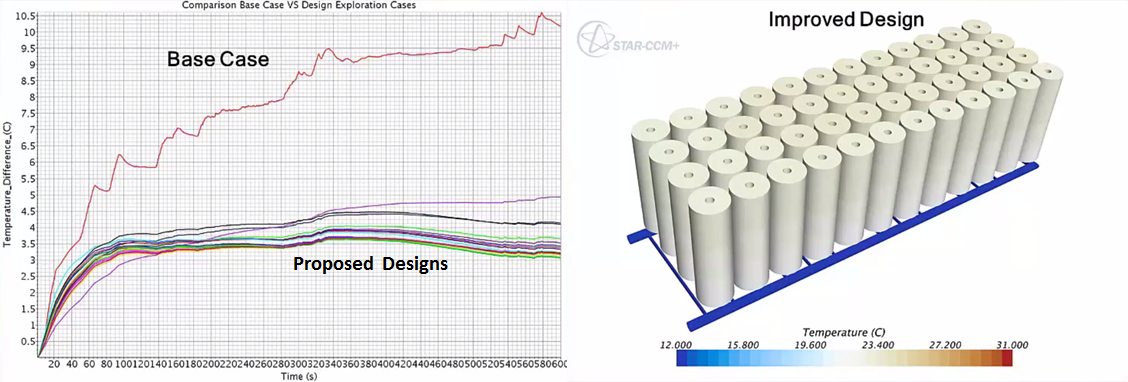
イーロン・マスク氏は2017年11月、決算発表後のアナリスト向け電話会議で「主な生産制約は、間違いなくバッテリー・モジュールの組立にあります」と述べました。「システム統合を委託先に任せたのですが、残念ながら完全に失敗しました。そして、それがどれほどの失敗だったか、ごく最近になってやっと気づきました」とマスク氏は付け加えました。
この重大な失敗について共有してくださったマスク氏に感謝しています。過去5年間における自動車市場の電動化に関して次のような気づきがありました。
- 車載デバイスの開発では、バッテリーセルの設計と性能が重要になっています。電力、エネルギー密度、安全性、経年劣化、コストなど、個々のセルで行った設計判断が、ダイナミックな市場における会社の地位に影響を及ぼす可能性があります。
- エンジニアリングの課題を解決することは問題ではありません (エンジニアはむしろ問題解決を得意としています)。問題は、来たるべき課題に気づかないことです。ただし、性能の高いモデリング料金を使用することは、意思決定を促進するために必須です。
- セル設計を習得したとしても、システム統合と 生産も同じくらい重視する必要があります。
つまり、バッテリーセルの設計チームは、広範なCAEシミュレーションを使用して、エンジニアリングの選択の影響を初期段階から考慮する必要があります。
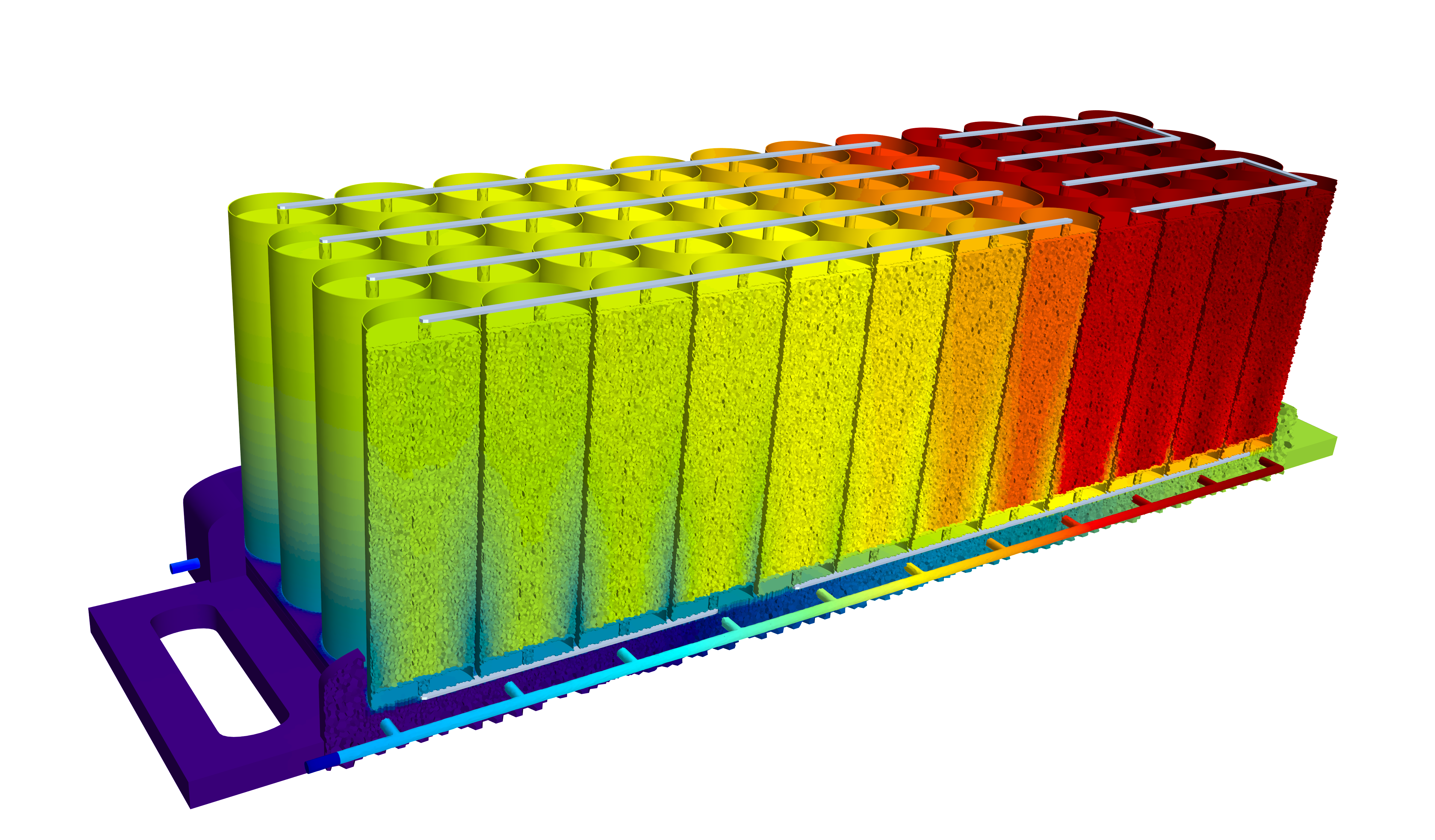
Simcenter Battery Design Studioは、リチウムイオン・セルの設計をシミュレーションすることで、セル形状の詳細な仕様やセルの性能をデジタルに検証し、エンジニアをサポートします。バッテリーセルの豊富なコンポーネントや、材料のデータベースが用意され、モデル開発を支援します。
メリットと特徴の概要:
- 物理セルの詳細: パラメーター化可能なテンプレートを備えたシームレスなGUI
- 統合的に結合されたセルの設計とモデル: 設計変更がセル性能に与える影響をシミュレーション
- マルチフィジックス・ソフトウェアの連携: TBMファイルを介してSimcenter STAR-CCM+にモデルをエクスポート
- 設計探索: バッテリーセルの設計と性能を自動的に最適化
- システムレベルでのシミュレーション: セルモデル特性をSimcenter Amesimにエクスポート
物理セルの詳細
Simcenter Battery Design Studioの最初のステップは、セル・コンポーネントの形状と特性を指定することです。チームの責任に応じて、それらはセルのサプライヤーによって提供されるか、コンポーネントのリバース・エンジニアリングを介して取得されるかのいずれかで実行できます。
Simcenter Battery Design Studioは、リチウムイオン電池のコンポーネント仕様を標準化します。ユーザーは、円柱状または角柱状のパウチからセル形状を選択し、電極、タブ、集電板の設計などの個々のコンポーネントを選択できます。各コンポーネントは、電極のセンタータブ設計などの特性でより細かく定義したり、集電板の材料と厚さを制御したりと、セルを完全に構築するための動作を複数実行することができます。
混合物の配合が通常知られている場合、正確な値は最初は推測であることがよくあります。しかし、文献や実験的な特性評価から入手可能な活物質の平衡電圧曲線から、ユーザーは低電流の放電曲線と良好に適合する混合物の調整が可能であるため、非常に正確な容量との相関を得ることができます。計算された「ビルドレポート」は、例えばセルの最終エネルギー密度や重量を確認することで、入力内容の検証にも非常に役立ちます。
また、ユーザーはジェリーロール部分のグラフィック出力を自動的に生成して、電極巻線が予想通りであることを確認できます。
セル性能のシミュレーション
Simcenter Battery Design Studioは、さまざまなレベルの性能モデルを提供しています。物理学ベースのマクロ均質モデルでは、セルのデューティ・サイクル中の電圧損失メカニズムなど、セルの電気化学反応に関する知見を得たり、電極全体の濃度分布や発熱分布を把握したりすることができます。等価RCR回路モデルでは、経験に基づくアプローチによって、セルの挙動を非常に計算効率が高い方法でモデリングします。
また、シミュレーションでは、電位の分布、電極全体のタブ付近に集中する電流密度など、セル内で起きていることを知ることもできます。
10A放電時のセルの電流密度分布
私のことやシーメンスのエンジニアリング・サービスチームとしての私の経歴をご存じの方、またはSimcenter SPEEDソフトウェアに関する前回の私の投稿を読んでくださった方は、次の質問をご存じでしょう。このようなモデルベース・システム・エンジニアリングのアプローチにおいて、実際に期待される成果とは何でしょうか?答えは、設計の選択が開発サイクルを通じてシステム性能に与える影響を理解し、初期段階から考慮に入れることです。お使いのツールによるサポートで、最適化された実行可能な選択をとれるようにすべきです。
一例として、シリコングラファイト複合セルに関するこのオンデマンド・ウェビナーでは、サフト社がSimcenter Battery Design Studioを使用して高エネルギー密度のアノードを有するセルを設計する方法を紹介しています。
システムだけでなく、並列/直列セルモジュールとバッテリー・パックの周辺要素との間の相互作用も考慮する必要があります。
マルチフィジックス・ソフトウェアとのシームレスな連携
シームレスな連携をするために、Simcenter Battery Design Studioを使用して、パックの3D電熱シミュレーション専用のセル電圧挙動を表すRCR経験モデルを作成することを基本的にお勧めしています。物理学ベースのモデルを使用することもできますが、RCR経験モデルは、結果の精度を一定に保ちながら計算コストを改善し、バッテリー・モジュール・レベルで作業する、専門家でないユーザーにより適しています。そのため、HPPC試験 (セルのSOC、温度、電流に依存する抵抗の特性評価のためにパルス充電および放電を実施) において、合成データまたは測定値からのデータを入力データとして使用し、Simcenter Battery Design Studioは、Simcenter STAR-CCM+内のバッテリーパックの3D挙動モデルに使用するRCR 3D経験モデル・パラメーターを非常に計算効率の高い方法で自動的に生成します。
上記の2つのSimcenter Portfolioソフトウェア間の連携は、Simcenter Battery Design Studioの出力ファイルであるテキスト・バッテリー・モデル (TBM) ファイルを介して行われます。TBMファイルは、Simcenter STAR-CCM+のBattery Simulation Moduleアドオンによって使用され、目的のバッテリー・モジュールの3Dモデルを構築します。Simcenter STAR-CCM+の形状、セル性能モデル、熱ソルバーを組み合わせることで、バッテリー・モジュールのエンジニアは、過渡シナリオでバッテリー・パック全体の電熱シミュレーションを実行できます。
ユーザーは、バスバー、電気絶縁パッド、冷却チャネル、バッテリー筐体などの他のコンポーネントをバッテリー・パックの一部に追加し (STAR-CCM+ 3D-CADまたはサードパーティのCADソフトウェアを使用)、自動メッシュ作成を実行したり、材料/冷却剤の性質を指定したりできます。
最後のステップは、デューティ・サイクル、または応用領域のあらゆる種類の過渡励磁電流プロファイル関数全体における過渡シミュレーションを実行することです。以下は、US06サイクル、環境温度25°C、一定の冷却ポンプ速度におけるバッテリー・モジュールの温度分布の一例です。
アルミニウム製の液体冷却プレートの上に18650セルが配置された4P12Sモジュールの例では (ここには表示されていません)、モジュール全体で大きな温度勾配を示す結果が得られました。これは、冷却システムが調和のとれた温度分布を維持できないためです。
この目的は、統合設計を検証し、開発サイクルの早い段階で、潜在的な欠陥、望ましくない制御挙動、または安全性の問題を検出することです。バッテリー・モジュールのマルチフィジックス「デジタルツイン」を使用することで、プロセス内で問題の発見が手遅れな可能性のあるハードウェアの段階で無駄な時間を削減します。
設計空間の探索と最適化の自動化
これらのシミュレーション結果から、エンジニアは、セルレベルで設計空間の探索に関する研究を開始できます。これにより、例えば、固定パックの設計を考慮しながら電池化学を研究したり、バッテリー・モジュール・レベルで形状と特性を研究したりすることで、バッテリー容量を最大化することができます。これらの設計空間の探索に関する研究は、Simcenter STAR-CCM+の一部としてDesign Managerを使用したり、Simcenter Portfolioの一部としてHEEDSソフトウェアを使用したりすることで実行できます。これを私は「デジタルツイン・マジック」と呼んでいます。シミュレーション・エンジニアは、システムの制約を尊重しながら、複数の属性性能のバランスを取るために、何百種類もの設計を半自動で効率的に、安全に探索できます。
温度がバッテリー・モジュール全体によく分布していないため、上記のバッテリー・パックの熱性能が向上することはすぐにわかります。これは確実に非効率的な冷却剤流の分布が原因で、これにより、過熱したセルの電気性能に確実に影響を与え、セルの耐用期間や安全性を損なう恐れもあります。
ここでは、設計探索の入力や、チャネル直径、チャネル数、冷却剤流量の方針などの変数を設定する研究例を以下に示します。設計探索目標として、ジェリーロールのセル温度差を2°C未満とし、圧力損失の低減を設定しました。以下の研究結果は、モジュール全体の温度の均一性が向上していることを示しています。
US06ドライビング・サイクルにおける基本ケースと改良設計との温度均一性の比較結果
ユーザー事例: Samsung R&D Institute
具体的な例として、Samsung R&D InstituteがSimcenter Battery Design StudioとSimcenter STAR-CCM+を組み合わせて使用し、設計上の決定がバッテリー・パックの性能のトレードオフに与える影響を調査した研究があります。
他のリチウムイオン電池メーカーと同様に、Samsung R&D Instituteは、より高いエネルギー密度と耐久性を備えた電池の製造を支援するツールを常に探しています。そのためにサムスンは、バッテリー・パックの3D電熱連成モデルにより、熱管理システムの最適化に力を注ぎました。
経験モデル・パラメーターのSimcenter Amesimへのエクスポート
Simcenter Battery Design Studio RCRの経験モデルでは、Simcenter Amesimソフトウェア内で使用するシステムレベルのバッテリー・モデルを設定するために必要なパラメーターを抽出する機能が利用可能になり、バッテリー・パックを「より大きな」システム (電動ホイール付き車両、航空機、発電所、さらには住宅用スマートグリッド) の統合コンポーネントと見なすことができます。
Simcenter Amesimでは、この動画に示すように、ユーザーはバッテリーのプレサイジング・ツールにアクセスして、(Simcenter Battery Design Studioなどから) セルの特性と技術要件のバッテリー・パック機能を自動的に構成できます。
生成されたバッテリー・パックは、電動パワートレイン、熱管理システム、電気ボードネットなどの他のマルチフィジックス・コンポーネントとそれらの制御を含む最終システムで使用できます。その目的は、セル/バッテリーの性能をシステムレベルで予測し、バッテリーとその周囲との間の将来の相互作用を初期段階から考慮することです。セル/バッテリーのサプライヤーとOEMとの間の共同作業を改善するための非常に便利なシミュレーション・プロセスにより、製品間の相互作用を簡単にモデル化、シミュレート、検証できます。