Streamline the additive manufacturing process with a single end-to-end workflow
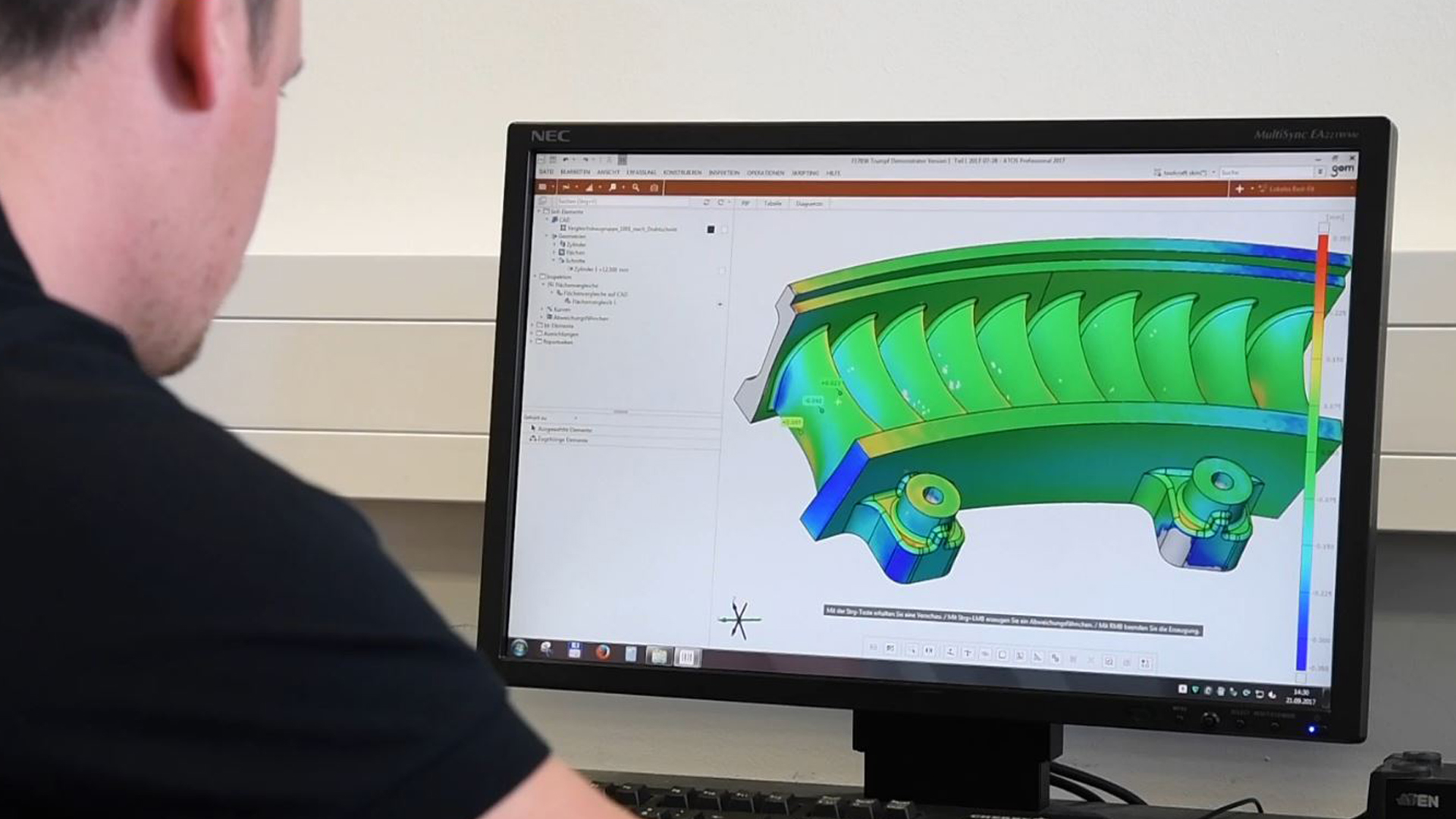
Additive manufacturing (AM) continues to grow and mature.
As the landscape becomes increasingly competitive, companies need to prioritize efficiency and precision, and that’s where additive manufacturing software can play a significant role in streamlining additive manufacturing processes from design to production.
A recent webinar took a close look at Siemens NX AM software, an end-to-end solution built specifically for additive manufacturing.
Watch the webinar trailer:
This webinar explores integrated workflows, simulation for printer deformation compensation, a comparison of scanned parts with nominal geometry and more.
Integrating additive manufacturing processes with Siemens NX AM
From design to production, the additive manufacturing process includes multiple stages, and each of those steps can different software tools.
Accurately transferring data between different tools is not only inefficient, but it can also lead to inaccuracies.
An integrated approach provides seamless data flow, reduces the risk of errors and enhances overall efficiency.
Early in the webinar, Mike Vasi of Siemens Digital Industries Software lists five advantages of using NX AM.
The associative processes used in NX AM ensure any changes made at any stage of the design process automatically propagate throughout the entire workflow.
This feature guarantees data consistency and minimizes manual updates, making it easier to manage complex projects.
NX AM also includes robust simulation tools that allow for thorough analysis and optimization of designs before printing, thereby enhancing the reliability of the final output.
Simulation for printer deformation compensation with Siemens NX AM
One of the most critical aspects of additive manufacturing is accurately predicting and compensating for printer deformations.
Siemens NX employs an inherent strain value method to simulate and compensate for these deformations.
In this webinar clip, Tom van Eekelen from Siemens Digital Industries Software explains how calibrating and simulating inherent strain values works.
The simulation predicts any deformations that will occur during the printing process.
These predictions are then used to create compensated STL files to ensure the printed parts closely match the nominal geometry.
This method significantly reduces the need for multiple dry runs, saving time and resources.
NX additive manufacturing processes from start to finish
The NX Additive Manufacturing Workflow offers a comprehensive approach to build preparation and execution.
Starting with part orientation optimization, the workflow guides users through generating support structures, running slice error distribution, and preparing the build plate.
The workflow also includes pre-build validation steps, checking for non-manifold bodies, deviation gauges, and collisions.
The integrated build processor server centralizes output generation, allowing multiple users within an enterprise to manage their print jobs more efficiently.
In this webinar clip, Kevin Epple from toolcraft AG talks through the entire process of creating a brake manifold for the Airbus A320, printed with titanium.
This setup streamlines the entire process, from design through printing, and provides real-time updates on the printing progress and any potential errors.
Comparative analysis of 3D printed configurations with Siemens NX AM
Machine parts, regardless of how they’re manufactured, undergo a series of quality assurance checks, including GOM scanning.
NX AM can compare the same designs using different supports and evaluate the accuracy of the models to determine which one is the best option according to the data.
The webinar highlighted three different configurations of the same part.
Tom van Eekelen walked attendees through the comparative analysis process in this webinar clip.
Testing and quality analysis within NX AM enables users to design and produce the best possible part through data-driven decision-making.
Conclusion
Like everything in manufacturing, additive manufacturing continues to evolve, and software solutions are helping companies improve the way they design and produce important machine parts and components.
With integrated solutions, robust simulations and efficient workflows, Siemens NX AM demonstrates the potential for significant improvements in additive manufacturing.
By embracing advanced solutions, the additive manufacturing industry can achieve new heights in precision and efficiency, ultimately transforming innovative ideas into sustainable products of the future.
Watch the full webinar to see these technologies in action and begin setting new standards in additive manufacturing.