Lightweighting robot grippers with additive manufacturing results in enhanced efficiency and sustainability
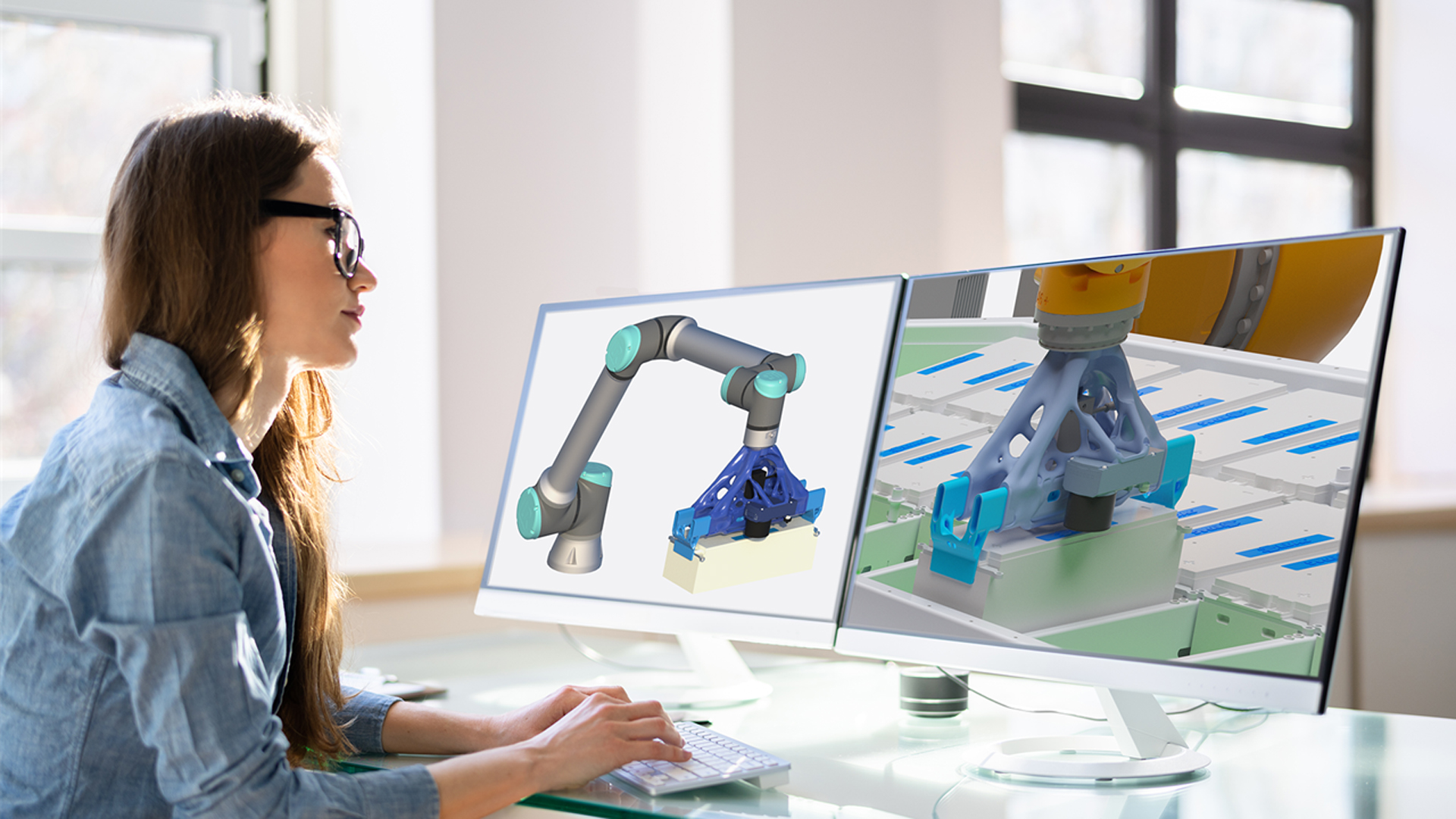
Between rising energy costs and an increasingly competitive landscape, today’s manufacturers are beginning to shift their focus to more sustainable and efficient practices, particularly in the realm of automation and robotics.
Lightweighting, or the process of removing weight from a component, is a recurring topic of discussion. Manufacturing facilities operating heavy robot arms and grippers that move material and products from one location to another are increasingly implementing the practice.
Switching from traditional, heavy robot grippers to innovative, lightweight robot grippers enhances operational efficiency and plays a crucial role in reducing the carbon footprint associated with robotic operations.
These newer, lightweight robot grippers are designed and manufactured in a fraction of the time compared to their traditional counterparts. Additive manufacturing (AM) makes it possible.
A recent webinar explored this topic in depth, including the design and manufacturing processes of lightweight grippers; their impact on cost, energy and CO2 emissions; as well as real-world applications that demonstrate the benefits of this transition.
Watch the webinar trailer:
Throughout the discussion, the integration of advanced software solutions for design and manufacturing is emphasized, showcasing how these tools facilitate the rapid prototyping and testing needed to advance in this field.
Exploring the shift to lightweighting AM robot grippers
Traditional, heavy grippers require the use of large robots, which have a substantial impact on the bottom line.
One of these large machines can weigh thousands of pounds while the objects they’re designed to move weigh only a fraction of that, presenting a significant mismatch in weight proportionality.
Furthermore, large, heavy robots contribute substantially to carbon emissions, estimated at 5.6 tons of carbon dioxide annually per robot.
As more and more large, heavy robots enter production, their associated monetary and environmental costs will only rise.
With over 3.5 million robots operational globally and around 500,000 new installations each year, the potential for energy and emission savings through lightweight grippers is immense.
In this webinar clip, the webinar presenter, Mr. Dennis Nier, outlines the current challenge and possibilities with an achievable solution.
With the development and growth of additive manufacturing, lightweighting has become easier.
It offers a solution that’s cost-effective in every way, from design and manufacturing to operation and service.
The benefits of lightweighting robot grippers
The shift from heavy to lightweight grippers is a transformative development.
Comparing traditional heavy grippers with their modern lightweight counterparts reveals significant differences in performance.
Traditionally, grippers are crafted from solid aluminum or an aluminum alloy. Conversely, lightweight grippers are additively manufactured with polymers.
These polymer grippers weigh significantly less – 64 percent less in one instance – and require less material to manufacture, all without compromising functionality.
They facilitate easier handling and maneuverability of robotic arms, and they extend the operational lifespan of machines by reducing mechanical stress.
Moreover, the adoption of lightweight grippers leads to a considerable reduction in energy consumption and carbon dioxide emissions.
In one production facility, replacing a single gripper resulted in using 54 percent less energy and an 82 percent reduction in CO2 emissions.
In this webinar clip, Mr. Nier shows a couple of real-world examples of engineers designing and building a much lighter robot gripper that costs less to manufacture and operate.
Replacing traditional grippers with optimized polymer models in industrial settings results in much lower costs, greater operational efficiency and a smaller carbon footprint to run a single robot.
The broad adoption of lightweight grippers and their cumulative sustainability impact could revolutionize manufacturing for the better, promising a greener and more cost-effective future in robotics.
Understanding the design process for lightweighting grippers
Designing lightweight grippers begins with using advanced CAD (computer aided design) tools and software.
This process must consider material and structural optimization, manufacturability and assembly.
By combining these facets, businesses can reduce the gripper’s weight significantly from traditional designs.
Siemens NX offers a wide range of additive design capabilities, and in this webinar clip, Mr. Nier shows the audience how to construct a comprehensive assembly and incorporate all the necessary inputs.
These powerful digital tools offer extensive help throughout the design process.
They include features like topology optimization, where material requirements and the design space are meticulously outlined.
Furthermore, the optimization process is intricately linked to constraints and load cases, simulating real-world applications to ensure a design’s feasibility and robustness. Features like topology optimization help designers produce the best possible grippers.
Digital tools can streamline the production process and enhance the gripper’s functional performance while adhering to sustainability goals.
Optimizing additive manufacturing in lightweight robot gripper production
New technologies are transforming the production environment.
With the right additive manufacturing tools, businesses gain enhanced workflows where engineers can integrate every step of the design and print preparation process into finalized manufacturing and assembly.
This seamless integration without the need for an import/export process ensures greater efficiency and accuracy.
Mr. Nier highlights how NX offers a single integrated additive manufacturing solution in this webinar clip.
The workflow begins with order management and continues with incremental stages of the design phase, where digital tools enable the creation of optimized structures tailored for additive manufacturing.
The transition to the production phase applies CAM (computer-aided manufacturing) techniques, which are essential to the seamless conversion of digital designs into physical objects.
Various additive manufacturing technologies facilitate the production of lightweight, robust robot gripper components.
These components are crafted using materials that exceed functional requirements, while also minimizing material waste.
Conclusion
Lightweight, additively manufactured robot grippers can significantly transform the industrial automation landscape.
The transition to lightweight grippers enhances operational efficiency, lowers energy costs and reduces the carbon footprint associated with robotic operations.
This evolution in manufacturing is made possible with advanced software solutions that facilitate seamless design and manufacturing processes.
Armed with these digital capabilities, businesses can rapidly prototype and test their designs before final manufacturing and assembly.
A greener, more cost-effective approach to industrial robots is just the beginning.
These innovative technologies pave the way for more sustainable and efficient manufacturing and automation practices in the future.
Watch the full webinar and discover how forward-thinking manufacturers are getting ahead.