How IT/OT convergence enables smart manufacturing: Podcast
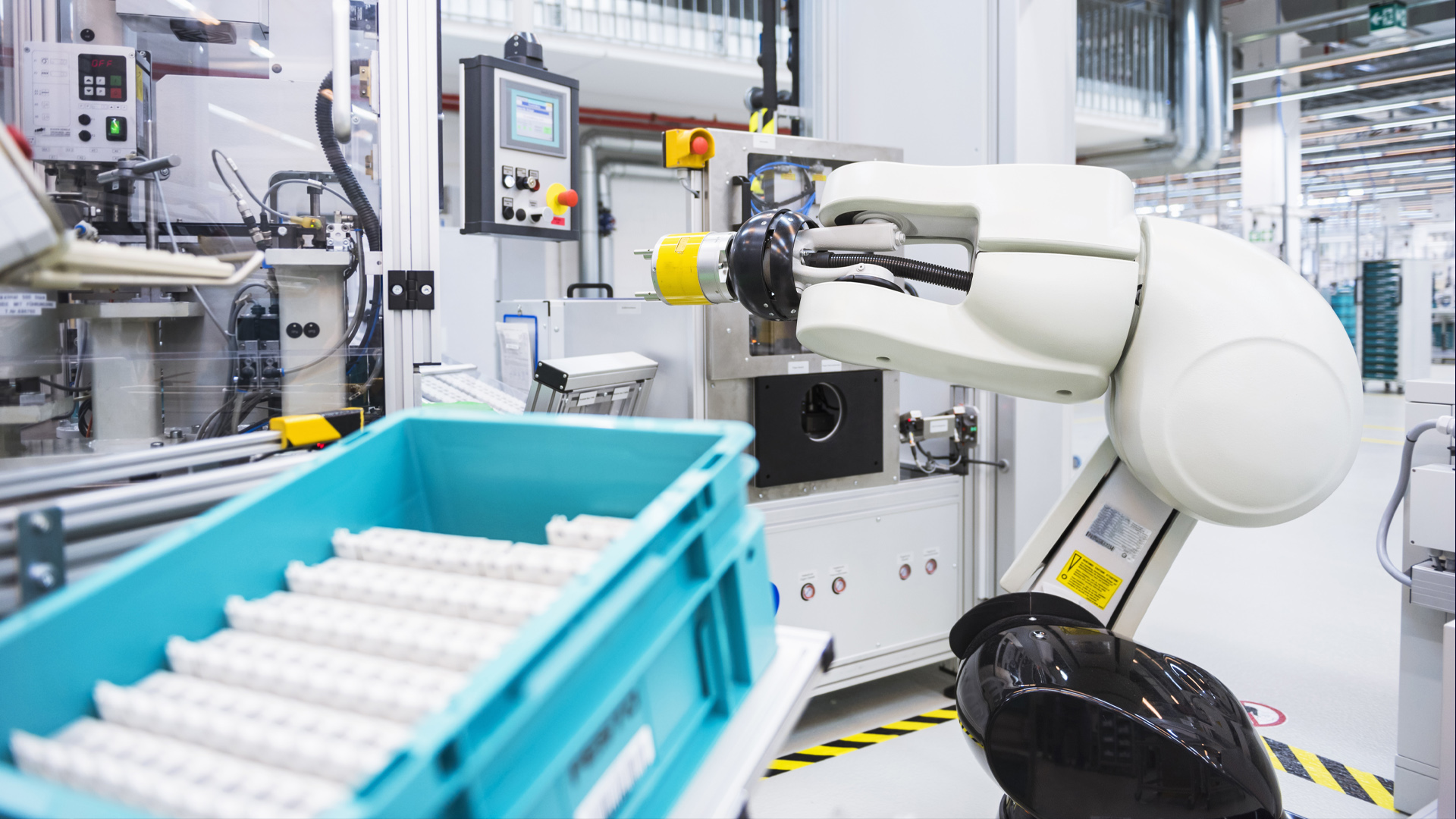
Information technology (IT) and operational technology (OT) have traditionally remained separate in the world of manufacturing. That’s beginning to change as new, smarter machines blur the lines between IT and OT to create new possibilities.
Manufacturers have a chance to gain the ability to leverage machine data like never before.
In a recent podcast hosted by Siemens Digital Industries Software, industry experts explored new opportunities for efficiency, productivity and sustainability through improved shop floor integration.
Podcast host Blake Snodgrass asked Rahul Garg, VP of Industrial Machinery about IT/OT convergence and what it means for the future of industrial machine manufacturing.
Listen to the podcast:
I’m joined by my wonderful colleague and expert from Siemens, Raul Garg. He’s the Vice President of the Industrial Machinery and Mid-market Program at Siemens Digital Industries Software. He’s responsible for global business development. Rahul’s 25-year career includes delivering software-based solutions for product engineering and manufacturing innovation globally. He has held leadership positions in research and development program management, sales, and P&L management, focusing on industrial machinery and heavy equipment since 2007. So, welcome, Rahul. Before we jump into this topic of convergence, let’s briefly discuss what’s going on in the marketplace with manufacturers. And what are some of the challenges they are facing right now today?
Rahul Garg: Thanks, Blake. First, I am very excited to be here and join you in this very interesting conversation. The manufacturing industry and many of the suppliers, i.e., the industrial machinery equipment providers, are going through some very interesting and perhaps some challenging times. While they’ve had many challenges from the past around global competition, low-cost providers, and customization, there are some new interests, very important factors that are impacting the whole industry. Two that are common across pretty much every industry, as we speak: one is supply chain and then the second one is labor shortage. Both of those are having a big issue for many of our manufacturers as we speak here.
Blake: So, how are manufacturers addressing some of these challenges that you just mentioned?
Rahul: When you look at some of these big issues that they are confronted with, improving operational efficiencies becomes very critical when you think about how to address things around supply chain and even around labor shortage, being able to find alternative suppliers and figuring out how to get your products and your manufacturing set up in the right way, finding and bringing your operators up to speed in the most efficient manner becomes very critical. So, all of these attributes drive it to eventually becoming more efficient with your operations and being able to drive the maximum utilization of your factories becomes even more critical. One of the important elements in trying to drive that operational efficiency is data. And data becomes an important element in your efforts to drive higher throughput, and higher operational efficiencies to your factories. And when you look at most factories today, they have a mix of older and newer equipment – newer smart machines that share data with a network and older machines that are data islands. And you need to allow a network of X sensors to provide all that data and bring all of that information together. So, those are some key things that manufacturers are doing to address these challenges as they see, at least, on the manufacturing front.
Blake: That’s great. And that helps us segue into our topic today on convergence of information technology and operational technology. Let’s start first by defining these terms and giving the relationship between the two.
Rahul: Operation technology is something that’s been around for quite some time. It’s the capability that runs your factory. It’s all the software that goes into the operation of the physical equipment, the controls and the technology that’s driving the machines, the controls, and the PLCs. It’s helping you move the factory. It’s the software that instructs the machine on what to do and is making sure that the hardware does the things that are needed. IT, on the other hand, is the technology, the organization computer technology that’s used to store, retrieve, process, analyze, and even action on electronic information inside your operations. So, typically, the IT part of information technology is used by management to make decisions, and operation technology is used by the factories to drive actions. So, on a high level, that’s what you can think of these two capabilities. And basically, what’s happening together is IT and OT together are now interacting more and more to achieve greater operational efficiencies and they are on a collision course. There is a boundary between what was traditionally there in the way information was managed with IT in server rooms and office buildings and OT being managed in the factory floor; and that is blurring. The data and the information is flowing more seamlessly as we speak. And the need to make that happen is becoming even greater.
Blake: Yeah, it really sounds like the two are really coming together. Let’s give some application to this. Do you have any examples of where this convergence is occurring or how it’s occurring?
Rahul: In the factory environment, the operational technology capabilities monitor the factory floor operations. Currently, we have capabilities like edge sensors that can stream data regarding an entire range of measurements and can give you a good sense of how the actual equipment is performing. This information, or data, can be captured as your factory floor is running, and can be fed into your IP systems. These IP systems are being set up to digitally optimize your business decisions and can be looking at this information from the edge sensors on smart machines. They create a much better view of how the equipment is running so that you can make real-time decisions. And these decisions can help optimize and further maximize your throughput through their factories. They can also help you make decisions, for example, like knowing that a certain part of a machine is failing, or it may be running out of stock or it may be having some issues which may impede the running of your factory. So, having that real-time knowledge, or real-time information can help you make better decisions on perhaps rescheduling the shop floor, bringing in new support capabilities, or service technicians before the equipment fails. So, all of this makes it very effective to maximize and utilize your factory operations.
Blake: It sounds like some real proactive digitalization is coming into play. So, tell me how convergence enables a digital twin of the operations?
Rahul: That’s a good question, Blake. More and more data equate to a better digital twin. The digital twin is a virtual replica of the physical objects of an entire machine or of the entire manufacturing system or the entire shop floor in a digital environment. So, think about it: while you’re running your factory, you have your digital twin of the entire factory with each individual machine in a replica format. The IT and OT convergence helps you get real-time data and real-time information into your digital factory. So, that operational data ensures much higher fidelity of the virtual digital twin and much higher visibility of the real-world operations. So, you’re getting the ability to see how the digital twin is performing while your real twin is doing its work.
So, it really makes it a compelling case to have an easy mechanism to understand what’s going to happen in the future in your operations without actually having to go and see it. And with this, obviously, the big advantage that manufacturers can get is they can confidently use the digital twin for optimizing the operations, predicting maintenance, enabling much better commissioning, better changeover, and faster production line changes. So, those become key capabilities for operations to conduct their business in a more efficient manner. And one of the key things that convergence is enabling is the ability to have even the factory operations staff take advantage of this new data in a more efficient manner. And one of the vital enablers for that is this whole notion of low-code or no-code applications. So, no-code or low-code applications become an essential ingredient in this whole concept of IT and OT convergence, where the operation technology people can quickly write new applications as well to help them with their operations, and to help them with that decision-making as well.
Blake: Those are some excellent points of how the digital twin is helping operations and convergence. So, if you could maybe get a little bit more granular and give us the benefits of this convergence.
Rahul: When you think about IT and OT convergence and the digital twin, specifically, the IT and OT convergence provides access to actionable data. This data empowers you to make much better decisions in an integrated manner to collaborate on the planning, the scheduling, and any additional research, and more importantly, on the performance of the equipment. That’s where one of the biggest value comes into play. And then this obviously provides extreme flexibility and visibility into your operations. This basically helps you to drive the ability to respond quickly to customer requirements, being very proactive and understanding your customer’s need, and responding to those customer needs. So, this results in improved efficiency to ensure zero downtime, zero waste, and zero operational issues – the triple zero as we call it. So, it helps maximize throughputs, lowering your cost to compete globally. And one of the other side benefits is it improves overall sustainability, minimizing resource usage, electricity, and water waste. So, those are some key benefits that are enabled through this IT and OT convergence.
Blake: Those are some excellent points. Would you do say that the current Siemens Industrial Edge Initiative is supporting this convergence?
Rahul: The Siemens Industrial Edge Initiative is actually an essential ingredient in this convergence. The whole Industrial Edge Initiative has three important ingredients. Number one is edge sensors that Siemens provides, making them easily available to a broad group of users. Number two is supporting an open ecosystem. Siemens recognizes that there are many companies that have a brownfield environment, and you need to be able to work in a manner where you can work with different providers of hardware and technology. So, we are a big proponent of open systems, which allows you to integrate and network with other manufacturers and bring in information from those other manufacturing environments as well. Thirdly, it’s a very critical ingredient to improve security and policy management. As you’re working in a highly distributed operational environment, you cannot underestimate the need for strong security, including the policies. So, Siemens is on top of that whole issue with critical technology that’s enabled through our edge systems, and our open ecosystem support. Additionally, it ensures that we provide necessary policy support that customers might need. So, this becomes a very important ingredient in enabling the challenge of IT and OT convergence.
Blake: Those are all excellent points. We’ve had an insightful discussion today, Rahul, regarding the IT/OT convergence and the impact it can have within the industrial machinery environment. And I thank you for joining me. And thanks to our listeners for tuning in. Please stay tuned for our next episode where we will explore Closed-Loop Manufacturing. Have a great day!
Understanding IT/OT convergence
At the center of IT/OT convergence lies the integration of two distinct domains – informational technology (IT) and operational technology (OT).
IT is the computer technology used to store, process and analyze the electronic information for a manufacturer. OT runs the factory, including the software, controls and PLCs that make machines work. Information technology is used by the business side to make decisions while operational technology is used to drive actions on the manufacturing floor.
Smart machines, edge devices and IoT capabilities are bringing these two realms closer than ever, making it easier for IT tools to see and analyze OT data from the shop floor.
IT and OT together are now interacting more and more to achieve greater operational efficiencies and they are on a collision course.
Rahul Garg, VP Industrial Machinery, Siemens Digital Industries Software
The integration of IT and OT brings tangible benefits to manufacturing operations. In the podcast, Rahul Garg mentions how edge sensors collect real-time data from machines on the factory floor. That data is then fed into IT systems for analysis. An analysis like this could be used to predict equipment failures, optimize production schedules, plan downtime, and more.
Learn more: Boost productivity and sustainability with shop floor integration | Ebook
Integrating shop floor data with IT systems also facilitates the creation of digital twins – virtual replicas of physical assets or manufacturing systems. By incorporating real-time operational data, digital twins offer unparalleled visibility into factory operations.
As more and more data flows between IT and OT, manufacturers can make more real-time data-driven decisions. Better informed decisions lead to better efficiencies, higher productivity and faster production line changes.
The IT and OT convergence provides access to actionable data. This data empowers you to make much better decisions in an integrated manner to collaborate on the planning, the scheduling, and any additional research, and more importantly, on the performance of the equipment.
Rahul Garg, VP Industrial Machinery, Siemens Digital Industries Software
The benefits of integrating IT and OT data extend beyond operational efficiency and digital twin performance. Actionable data empowers manufacturers to make better decisions collaboratively. With increased flexibility and visibility, companies can respond more quickly to customer demands, reduce waste and improve overall sustainability.
Smart manufacturing is more effective with IT/OT integration
As industrial machine manufacturing continues to evolve, IT/OT integration emerges as a transformative force driving efficiency, agility and sustainability. By harnessing the power of data, manufacturers can optimize operations, enhance decision-making and stay competitive in an increasingly dynamic landscape. The future of manufacturing looks brighter than ever.
Listen to more smart manufacturing podcasts
Episode 1: Unlock the potential of smart manufacturing for industrial machines
Episode 3: Unveiling the Power of Closed-Loop Manufacturing
Episode 4: Closed-loop quality in smart manufacturing
Learn more about IT/OT integration by downloading this informative ebook.