Improve heavy equipment serviceability with integrated service BOM management
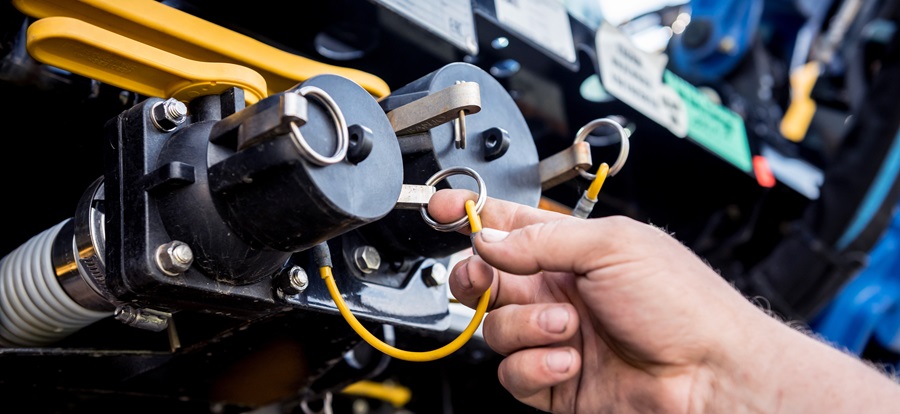
Ensuring that the right parts to support your heavy equipment production are available in the right place at the right time and in the correct quantities is key to implementing a service strategy. From an operational perspective, there is often a focus on optimizing inventories and logistics, yet ensuring that the correct parts are stocked sometimes gets lost in the mix. This typically comes from both ends of the product lifecycle, where at times there is a large delay in implementing changes and upgrades from engineering, and at the other end, a gap in managing accurate configuration details for the fielded assets. Both scenarios can raise inventory hold costs and scrap rates, among other inefficiencies. These challenges can be resolved with a managed view of the service material requirements that can bridge the ongoing design requirements to the specific asset configuration requirements. This managed view is what we refer to as the Service Bill-of-Materials (SBOM).
For many heavy equipment manufacturers, an integrated Service BOM that is connected through an enterprise digital thread, from design to manufacturing to service, likely does not exist. Sometimes it is simply captured as a disconnected parts catalog or as a separate BOM in the ERP system. There is likely no direct linkage to ongoing change processes or the physical assets, resulting in significant discrepancies over time. If this is the case, then it is also likely that the service impacts are not clearly visible and not fully considered when changes and updates are proposed. As the lifetime of complex assets generally continues to increase, this gap in visibility and traceability will only produce a greater challenge over time.
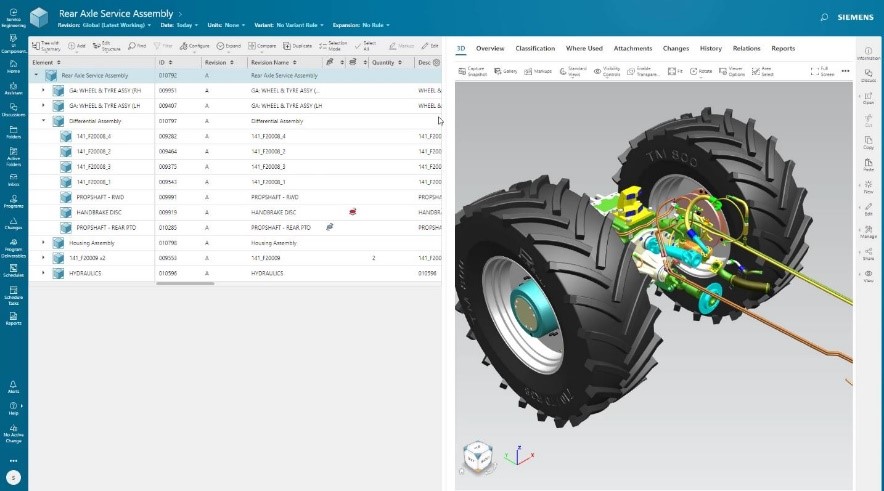
Integrated SBOM for heavy equipment service engineers
Take for instance the scenario of a service engineer who is responsible for updating service instructions as part of a change process. As a service engineer, you need to understand which parts work with the current configuration for a serialized asset. If you don’t have this information, your new service instructions may not be valid. Consider another scenario – as a service manager responsible for service optimization and asset efficiencies, you would want to have the ability to analyze the upgrade potential of serialized assets. Integrated SBOM would provide you with the knowledge of potential upgrades upfront and also enable the traceability of assets after the upgrades.
Now take the scenario of a service technician at a customer site. Without knowledge of the correct spare parts to use with the asset, or the right tools or skill set, how can they be efficient in delivering quality service?
Benefits of an integrated service bill of materials
An integrated service BOM that is directly linked to the engineering definition provides an accurate understanding of what parts are required to be tracked and maintained. Beyond linking to the engineering definition, the Service BOM can be used to:
- Define additional characteristics critical to service
- Expand the definition of purchased assemblies to include required serviceable items
- Define service kits to collect and manage spare parts that will be sold as service offerings
- Create and manage service assemblies to enable more efficient asset serviceability
- Identify service-specific items that may be required to perform service tasks
- Manage specialized tooling that may be sold as a service offering
- Manage compatible upgrades within the defined configurations
- Derive integrated parts catalogs in various formats including interactive 3D
This video shows a heavy equipment-related product demonstration of Teamcenter Service Lifecycle Management featuring service engineering and service BOM (SBOM) capabilities:
What value does an integrated service BOM bring to manufacturers?
As heavy equipment manufacturers strive to improve service operations, this critical aspect of the service lifecycle cannot be undervalued. Integrated service BOM management establishes the required foundational service data and enables the downstream efficiencies and quality improvements required to develop an optimal services strategy. It also provides a bridge for engineering to understand service impacts, opportunities, and asset performance in the field. Introducing an integrated service BOM as part of a broader service lifecycle management strategy can provide significant value, including:
- Early collaboration of service stakeholders for the identification of material or logistics issues before it is too late
- Reduced inventory costs through clear visibility of the most recent part requirements, minimizing inventory holds and reducing scrap rates of unneeded parts
- Improved efficiency of parts catalogs through automated creation and reuse of available data from the service BOM
- Improved traceability and clarity of service impacts across the enterprise
With robust integrated SBOM management, your service teams are equipped with the right information to get service right the first time.
Learn more about how our heavy equipment service lifecycle management solutions can boost overall heavy equipment service efficiency while reducing service costs.
Interested in trying a free software trial? Now you can explore Teamcenter Service Lifecycle Management with a free 30-day trial.