Feeding 10 billion people requires agriculture innovation
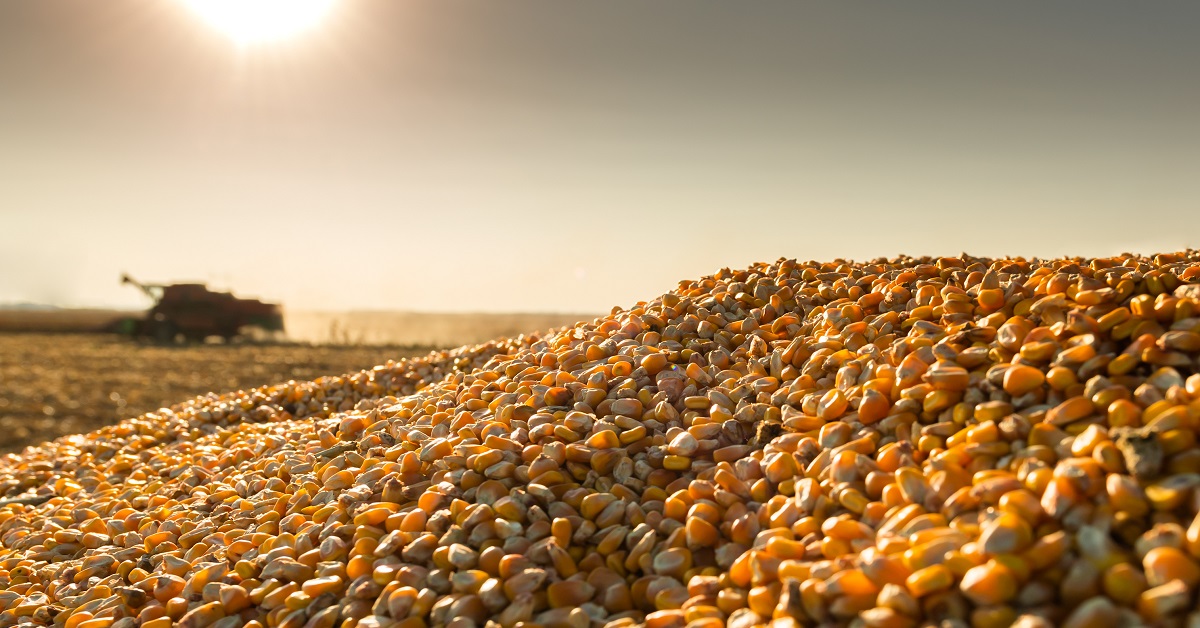
Agriculture innovation will be vital to keep feeding the world’s continuously growing population. As an agricultural equipment manufacturer, you must take responsibility and do your share. In fact, you have no other choice if you want to stay in business. Through electrification and digitalization of your offering, you must make farmers more productive, profitable, and sustainable at the same time. Read below which challenges agriculture innovation will bring along and how Siemens Predictive Performance Engineering for Heavy Equipment can help you overcome those with powerful solutions for real-world physics simulation, computer-aided engineering (CAE) automation, and performance predictions continuity.
We need more food with fewer resources
It’s a boy!
On November 15th, 2022, Damián Ferrera was born in Santo Domingo, the capital of the Dominican Republic. The United Nations Population Fund (UNFPA) announced the healthy newborn on Twitter, making him the child symbol for their ‘Day of Eight Billion’, the day when the world’s population was projected to reach 8 billion people.
The population growth goes on
It’s really going fast! In only 50 years, our global population has doubled. 11 years ago, we reached 7 billion people. Now, we’re 8. And even though the growth rate seems to slow down, it’s estimated we’ll be around 10 billion by 2058, before reaching the peak of 10.4 billion towards the end of the century. Can we handle this? Especially given that we will also see some major demographic shifts, including regional ones and between age groups.
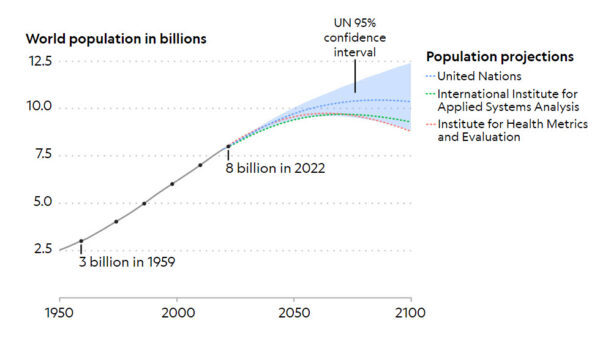
The food system is under pressure
This evolution puts enormous pressure on our infrastructure and resources. Those include water and energy, but also food. How will we soon feed 9-10 billion people in a sustainable way if today, we don’t even manage to do so for 8? UN says today around 10% of the global population goes hungry. And while evidence shows there could be enough for everyone, it is still a reality. Food just somehow doesn’t reach all the right places in the right way due to inefficiencies in all aspects of the food system, from production to consumption.
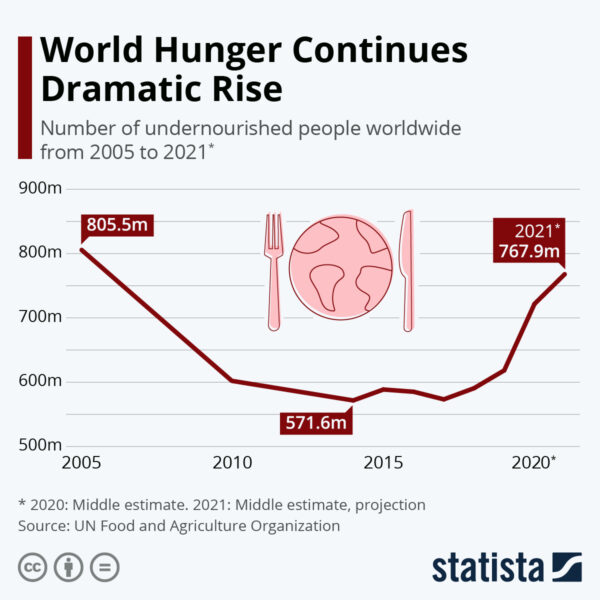
A disastrous environmental impact
On top of this comes the environmental impact of current food production is disastrous. Pollution and overfishing are degrading oceans. Land is being overexploited. Wildlife is disappearing. Buffers that protect humans from viruses like COVID-19 are being removed. Forests and other wildlands are being wiped out. And access to water for drinking and farming is being threatened, partly due to some nasty side effects of global warming. Current food production is estimated responsible for one-quarter to a third of global carbon emissions and for 90% of deforestation worldwide!
Agriculture innovation to the rescue
We must reshape the food system
It’s time to rethink the entire food system. National Geographic summarizes it well: “The risks and opportunities of our population boom and parallel resource crisis depend largely on decisions we’ve not yet made. Which will control our future more — the billions of mouths we’ll have to feed, or the billions more brains we could employ to do so?” We can’t just intensify current practices and continue in that vicious circle of clearing land for expanding agriculture and thereby increasing the occurrence of exactly those meteorological events that lead to more food insecurity. Instead, we need agriculture innovation.
The boundaries are being set
Meanwhile, authorities are tightening their grip on all actors in the agricultural industry. They are steering agriculture innovation by deploying regulations and financial incentives. Especially regarding greenhouse gas emissions, of course, the laws and guidelines are becoming increasingly stringent. Around the world, an overwhelming majority of governments and decision-makers are taking action to mitigate climate change. It’s something we owe to the 2015 Paris Agreement, which was in that respect a real game changer.
A historic deal: 30 by 30
Inspired by the success of that one, on December 19th, 2022, negotiators from around the world reached a historic deal at the United Nations (UN) Biodiversity Conference in Montreal, Canada. In an ambitious agreement, they committed to protecting 30% of land and water considered important for biodiversity by 2030, known as 30 by 30. This is a breakthrough as till now, only 17% of terrestrial and 10% of marine areas were protected. But it was time. We were heading to a tipping point. The deal will obviously have a massive impact on the agriculture industry, even in short term.
Agriculture innovation must accelerate
If we want to keep food affordable and accessible for everyone despite these constraints, we need massive agriculture innovation. And to be clear, there is progress in several promising areas, from innovative ideas to reduce food loss and waste, to water management technologies, to numerous biotechnology applications, to the introduction of disruptive concepts like vertical farming. Important among those agriculture innovation applications are digital advancements, for example using collected data for smart farming applications, such as precision farming and farm automation. The latter brings together agricultural machinery, software, electronics, chemical sensors, and data management to improve equipment operation and decision-making.
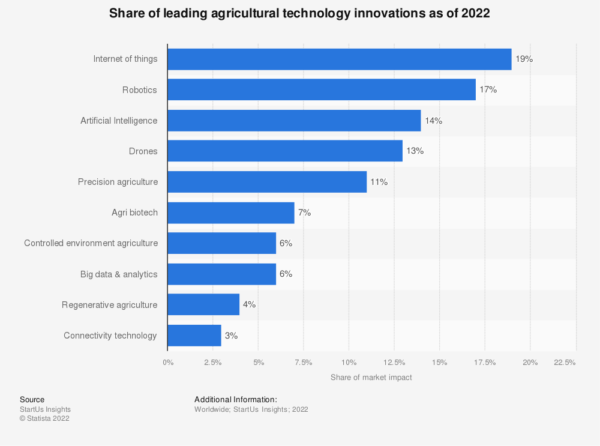
Making agriculture equipment in the era of innovation
Digitalization and electrification of farming machines is necessary
As an agricultural equipment manufacturer, you must realize that in this agriculture innovation context, upgrading your offering and bringing a totally new generation of machines will be vital to survive the next decade. Farmers will need those innovation capabilities like drones, sensors, automated harvesters, autonomous tractors, and alike. Only those let them be productive, profitable, and sustainable at the same time, which is necessary to stay in business. Through electrification of your machines and massive introduction of agriculture innovation based on emerging digital technologies, you must help them meet their yield targets while complying with increasingly stringent regulations.
Challenges related to engineering equipment for agriculture innovation
Agriculture innovation will explode engineering complexity
This will have massive consequences for the requirements of your design and engineering processes. To successfully turn these new technologies into applications for agriculture innovation, you must find a way to master the complexity that comes along with them.
Electrification, for example, is more than replacing a component. It touches on many aspects, including mass distribution, overall energy management, thermal management, and more. Technologies like batteries, fuel cells, hydrogen, and alike are so different from an engine and their application is so impactful to other subsystems that all established engineering practices must be reconsidered.
The same goes for agriculture innovation applications that make use of emerging digital technologies like 5G, IoT, cloud, artificial intelligence, and the like. Those come with an enormous amount of software and electronics as complex embedded systems. In everything the machine does, multiple disciplines play a role, as well as numerous parameters which mutually interact and whose values depend on the machine’s operational status.
You can’t manage all that with a classic engineering process, where you typically optimize disciplines one after the other, with lots of iterations, manual data handovers, and recurrent prototyping. Instead, to master the complexity of agriculture innovation, you need a new integrated approach, aiming at first-time-right-design. In this one, physical testing is still essential, but realistic simulation becomes the real design driver.
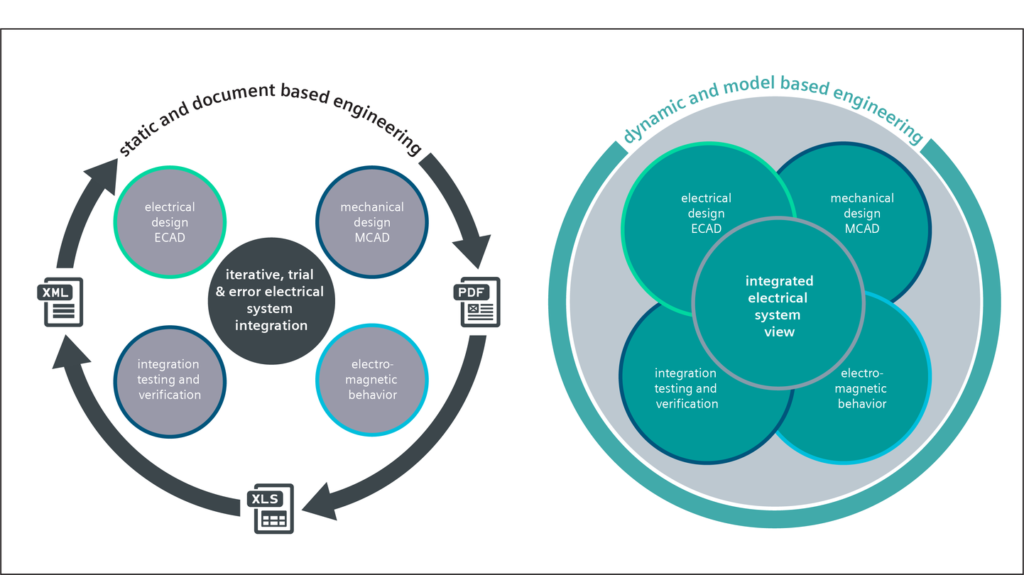
You must become successful with simulation-driven design
To be successful with that, you must take control over your engineering problem from the start. Already in concept studies, you must work with comprehensive models, including all components and all relevant physics. By using those in multidisciplinary analyses, you can start balancing all your performance requirements already at this point, possibly using design exploration techniques.
The outcome won’t be perfect. But the better you can outline the boundaries for all the variables in your engineering problem during this stage, the lower the chance that complexity makes it derail afterward. That’s what we mean by ‘frontloading design decisions’ or ‘shift left’.
Later on, you can add details as they become available and further optimize machine performance using increasingly complete and realistic models. That process will be way more effective now, exactly because of the good starting point you created during earlier stages.
When following such a process, the work of departments whose activities usually take place at different stages of the engineering process gets connected. Such a vertical integration gives people earlier in the process more tools at hand to contribute to decisions that are otherwise taken during later stages. That is in essence how simulation can drive design and enable agriculture innovation.
Quote: “If the simulation at the beginning of the process is robust, then many functional testing loops, which are meant to improve the system, can be skipped. To find a new solution, it only requires acting on some parameters using Simcenter Amesim and validating them during the testing phase, instead of starting the complete development phase over like we did some years ago. By using Simcenter Amesim, the development phase can be reduced significantly, up to 30 percent in some cases.” (read more…)
Riccardo Bonacina, Base Engine Validation and Reliability Lead Engineer at SDF
Digital agriculture innovation applications call for a different approach of the product lifecycle
Finally, when you think about which types of agriculture innovation are possible with emerging digital technologies, you automatically think about examples like smart machine functions that can upgrade performance based on real operational conditions, autonomous operation, connected worksites, predictive maintenance, and more.
Those agriculture innovation applications typically require bi-directional information exchange between design on one hand and the physical asset in the field on the other, often even real-time. In other words, the classic boundaries between the various lifecycle phases are getting blurred. Product delivery is no longer a single discrete event and performance optimization becomes a matter of individual products, over their entire useful life.
To enable this, and thereby drive agriculture innovation, you must start by making the necessary infrastructure available. Therefore, you need to connect many dots, combining the knowledge of very diverse engineering areas, such as sensors, electrical and electronics (E/E) systems, Internet of Things (IoT) hardware and software, and more.
A huge challenge thereby is the acquisition, management, and exploitation of the enormous data streams that are generated in the sensors by your equipment while it is operating in the field. It takes powerful data analytics solutions to convert those data into information that is useful in a design context.
Transform your processes and become a leader in agriculture innovation
Turn complexity into a competitive advantage using the Digital Twin
Showing leadership in agriculture innovation and upgrading your capabilities accordingly is vital for your agricultural machinery business. These trends of electrification and digitalization are clearly here to stay. There is no escape. In the future, there will only be more parameters, more physics, and more interactions between design and machines out in the field. Those who can master this better will turn complexity into a competitive advantage. The only way to do that is to deploy methods and processes that enable a Digital Twin and a Digital Thread, two typical Industry 4.0 paradigms that have a few prerequisites.
Prerequisites for a successful Digital Twin and Digital Thread
Remove silos and simulate real-world physics
At the heart of the Digital Twin is a set of models and data that can mimic real machine behavior and stay in sync with any parameter change that would apply. The Digital Twin represents the machine at any stage in the best and most complete possible way.
To achieve this, you need various technologies, from multidisciplinary system simulation to discipline-specific 3D CAE and specialized computational fluid dynamics (CFD). In addition, to leverage real data on boundary conditions, duty cycles, and physical properties in your simulations, you must complement these premium simulation technologies with powerful physical testing solutions.
Real-world physics simulation requires that you apply those methods in coupled models and co-simulations. That can be challenging if teams responsible for various design aspects keep working in silos, using their own tools and data. To avoid that, you must integrate their activities into a common digital platform to which everyone has access and where every decision is traceable.
Deploying real-world physics simulation will help you gain more confidence in your designs and reduce risk. Moreover, you will save an enormous amount of time and cost by simply avoiding expensive iterations of testing and failing with multiple prototypes and field testing.
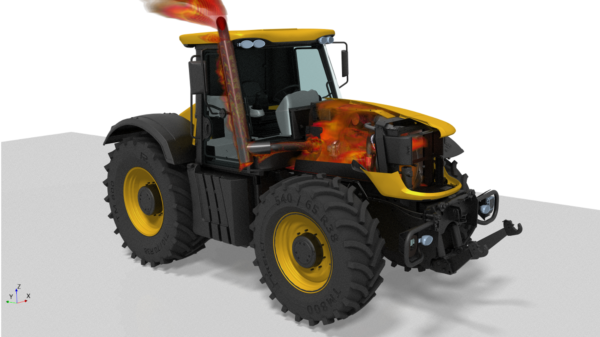
Accelerate and automate your simulation process
As part of the Digital Twin, as simulation must drive design, it defines the pace of machine development. This requires the next level of efficiency, to be achieved by applying advanced technologies wherever possible. Examples are fast data processing, meshing, and solving, reduced-order modeling, and high-performance computing.
Besides, you can save a huge amount of time by identifying recurring tasks and putting those in templates. The larger the scope of those, the better. Comprehensive templates that vertically integrate the work of various departments help to standardize processes and enable large-scale workflow automation, which you need for applications that require many runs.
By doing so, you are also unlocking a massive opportunity to shift left. When thinking about a process that includes computer-aided design (CAD) and CAE, for example, such templates make expert engineering solutions accessible for analysts and designers, so they can do early simulations.
The true power of CAE automation comes however when it lets simulation participate in large-scale design exploration to discover totally new designs with unprecedented performance, fully tuned to the requirements. Or when it is used to enable agriculture innovation capabilities that require an enormous amount of simulation runs for validation and certification purposes, which is for example the case for autonomous equipment.
Extend the scope of simulation to the entire lifecycle
Many agriculture innovation capabilities rely on input from simulation models. Those must be up to date, including all post-delivery information like updates, maintenance history, and field data. As every machine’s history is unique, the Digital Twin will automatically split into serial-number-specific versions.
Managing this requires digital continuity over the entire product lifecycle. You need a shared environment where you can keep all data related to individual machines throughout their entire useful life and where you can organize a Digital Thread, a digital mechanism that tracks all requirements, decisions, parameter changes, and their corresponding impact for every individual serial number.
If you can integrate this Digital Thread with powerful IoT and data analytics capabilities, you can exploit simulation to its full capacity, putting you in a pole position to create equipment that will revolutionize your industry. You will deliver functionalities that just 10 years your customer deemed unthinkable.
Besides, with constant access to performance predictions and capabilities to efficiently convert those into design insights, you will get continuous feedback on how to improve the next generation of your machines. In this way, you will be leading the digital transformation of your industry in no time.
Siemens Predictive Performance Engineering for Heavy Equipment
Real-world physics simulation. CAE automation. Performance predictions continuity.
The solutions that are bundled in Siemens Predictive Performance Engineering for Heavy Equipment are exactly those prerequisites for a Digital Twin and Digital Thread as we have discussed above. With our tools, you can successfully transform your processes, deliver the next generation of tractors and harvesters – smart, autonomous, and connected – and become an agriculture innovation leader.
With Predictive Performance Engineering, you will unlock the massive potential of electrification and emerging digital technologies to design equipment and business models that will revolutionize your industry.
Conclusion
We are now 8 billion people on this planet, and we are heading for over 10 billion. Meanwhile, resources become scarce and regulations increasingly stringent. We need agricultural innovation to survive.
With electrification and digitalization of machinery, you can help farmers be more productive, profitable, and sustainable. But it will dramatically increase your engineering complexity.
To keep up, you must invest in 3 areas: real-world physics simulation, CAE automation, and performance predictions continuity. This will help you successfully deliver the next generation of machines and support agriculture innovation.
Learn more
Do you want to hear more about this topic?
- Check out this on-demand webinar on the value of predictive performance engineering
- Read the ebook Predictive analytics software for the heavy equipment industry
- Read how our customer Amazone uses our solutions to drive agriculture innovation
- Read how we help AGCO reduce the amount of physical field tests
- Read how we helped SDF compress their development cycle by 30%