An introduction to Composite Structures, with Elston Engineering Services
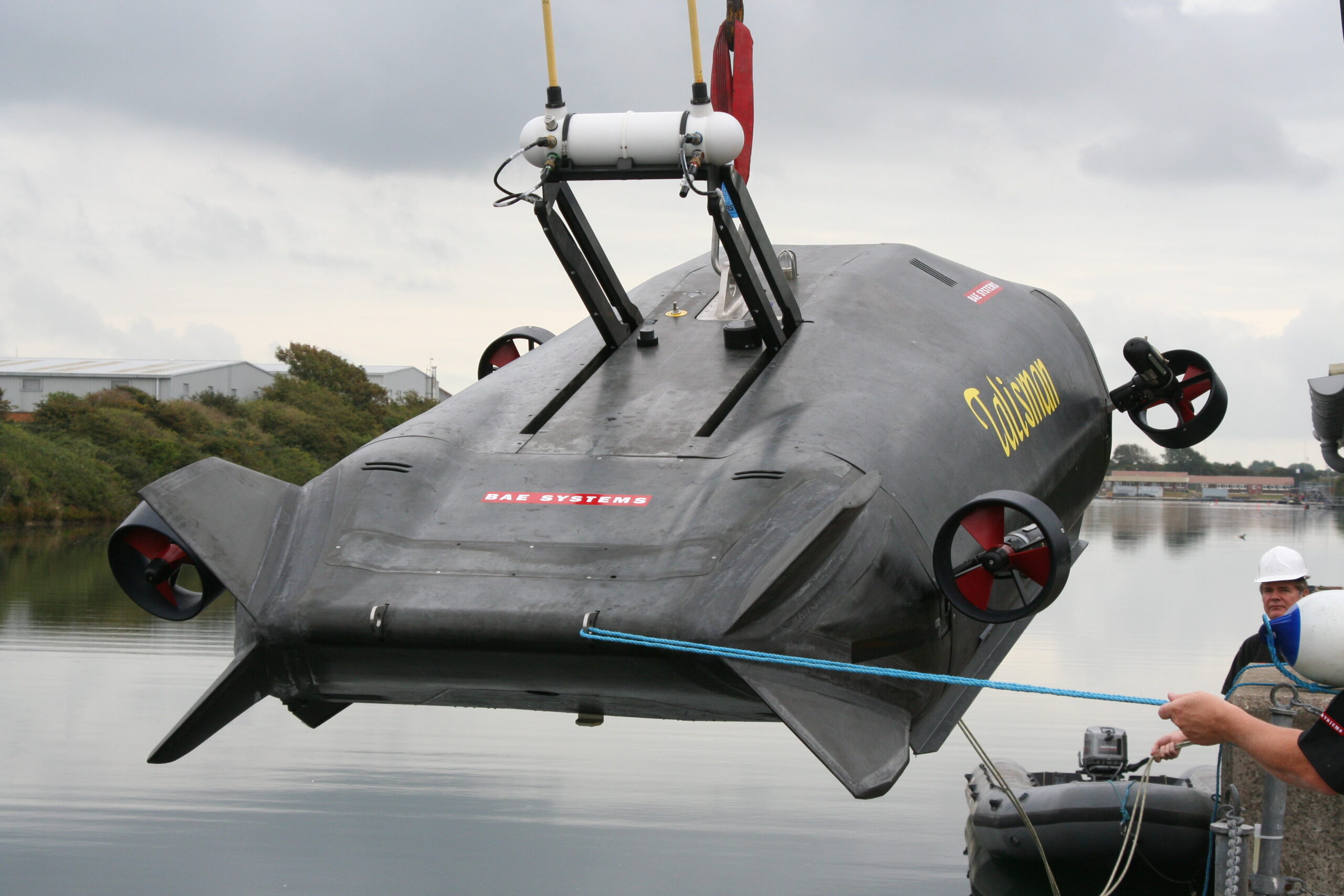
We live in a world where nothing stands still. Companies and individuals across the world continue to push the boundaries of composite structures. After all, it was an engineer, not a scientist, that first set foot on another world. Elston Engineering Services (or EES) are most certainly classed in that bracket of innovators.
Based in Knebworth in the UK, EES operate in the world of mechanical engineering services. The company specializing in the development of fibre reinforced plastic composite structures. Ron Elston, Managing Director, proudly owns the company. Ron has a wealth of experience spanning over an illustrious 60-year career. His career began as an apprentice draftsman at ML aviation, before eventually overseeing the creation of small integrated circuits and large earth station antennas. Rons’ varied experience means he is considered a specialist within mechanical engineering and composite manufacturing.
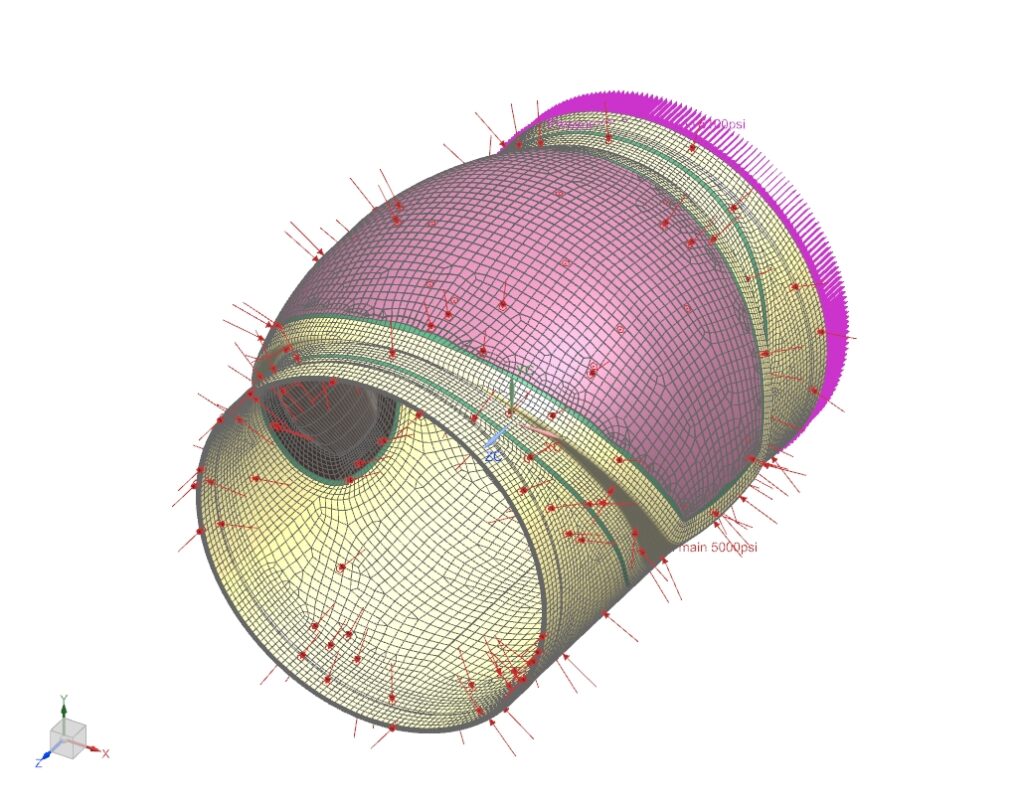
To provide context, composites are a combination of non-metallic and metallic materials to create a structure, or range of structures. These structures create strong, lightweight, stiff and low-density components. These components lay the groundwork to create incredibly strong assemblies across a wide range of sectors, including architecture, automotive and aerospace to name a few. It’s an approach which has accelerated the capabilities of society to take our engineering capabilities to the next level.
What to expect
Throughout this blog, we’ll be looking at the history of composite manufacturing through the eyes of Ron Elston. We’ll be exploring how advanced manufacturing applications have continued to develop over the past few decades, and how this enables specialists like Ron to continue to innovate and bring their ideas to life. In addition, we’ll also cast our eyes to the future, looking at what we could expect to see in the years to come and how the next generation of engineer will push the boundaries even further.
21st century advanced manufacturing and composite applications; how did we get here?
There was a time when composite manufacturing applications were unable to meet the needs of many companies. Companies had a broad understanding of how new processes and materials would revolutionize the manufacturing workflow to include composites. The problem was, companies weren’t pro-active enough in order to facilitate change.
Ron had an opportunity to merge the testing and analysis of composite structures with the design office during his time at the Marconi Research Centre. Why was this so important at the time? It enabled a specialist like Ron to implement an integrated approach; whereby one team oversaw conceptual design, geometric design, structural analysis, tool creation, part creation and testing. By connecting the dots, composite manufacturing companies were able to achieve greater product innovation to improve production efficiencies. In addition, companies reduced the time to the final iteration, whilst simultaneously pushing the capabilities of their respective industries forward.
Technology was a gamechanger for composite structures
Ron’s experience contributed to a change to processes which resulted in improvements within advanced manufacturing. However, it was the improvements in technology that really pushed the industry into a new era. Modern day capabilities means graphical analysis is completed at a much faster pace. In addition, multiple composite materials can be handled simultaneously; mainly due to improvements we have seen in computer hardware performance and storage.
Shock and vibration studies are now more accurate than they’ve ever been; when you combine all these elements, the user is receiving far more real-world data than previously. Teams who have the experience and/or a knowledgeable will really pay dividends. Composite manufacturers are able to reduce mass, cost and production times for their structures. As a result, the same manufacturers are ultimately reducing their lead time to market.
Sustainability in composite manufacturing
Processes and technological innovations have continuously pushed industry standards to where we are today within composite manufacturing. However, a global transition towards a more sustainable society is needed; composite manufacturing is not immune to this.
Thankfully, composite manufacturing companies are already considering the practicalities of implementing sustainable technologies into their workflow. Companies are beginning to reclaim carbon fibre from decommissioned, out-of-use products in some instances. In addition, there’s been a switch towards the use of thermoplastics as opposed to thermo-setting plastics. Thermosetting plastics for composites typically incorporate one use epoxy resin, Thermoplastics such as polyethylene don’t have this problem; their chemical structure means that they can be re-melted and taken back out of composite structures for re-use. It’s essentially an early stage of a ‘circular economy’ within the composite manufacturing industry.
Fibre-reinforced plastics can produce structures with strength to weight ratios greater than traditional materials, such as steel and aluminium. Reinforcing the thermoplastics using either re-used carbon fibre or ‘virgin’ fibre can achieve strength and stiffness properties approaching those achieved with thermosetting composites. We are seeing continuous improvement of raw materials to create strong products, whilst not compromising on quality and reducing carbon emissions in parallel. This is truly the start of composite manufacturers recognizing the dangers posed by carbon emissions moving towards a more sustainable model for the future.
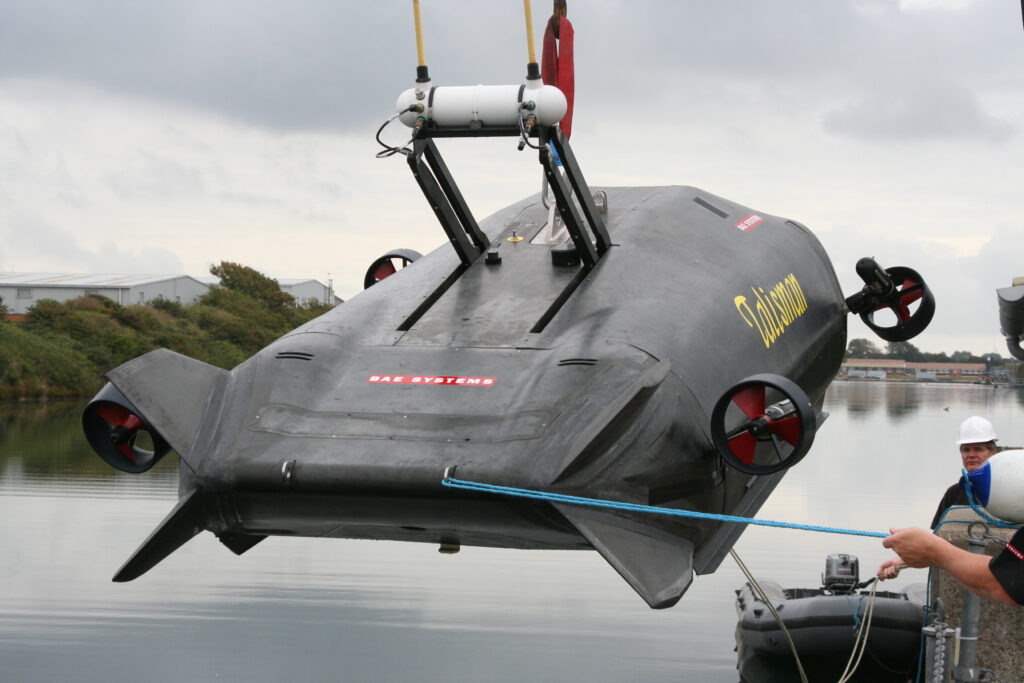
Why Siemens for composite structures?
For someone with Rons’ experience, using a powerful software application is just as important as having a strong understanding of the science behind composite structures. 50 years in the industry means Ron has seen, used and mastered a range of software applications. It is therefore testament to Siemens that NX continues to be the package of choice for Elston Engineering Services. Why is this the case?
The integrated approach of Siemens NX
Ron believes that Siemens has an integrated approach with NX; different features with different purposes are packaged into the same application to enable users to stay on one platform for their whole workflow. Design engineers can lose precious time during their workflow exporting datasets to another application, if their primary application doesn’t come equipped with the correct features they need for their use case. Siemens NX eliminates this problem. Factoring in a consistent development strategy which add a range of features into future NX releases lays the groundwork for NX to meet the needs of multiple companies across a range of industries.
Understanding the science behind composite structures
The user may have a strong understanding of the science behind composite structures. They then need to have the tools available to accurately simulate the science within their application. It’s an important aspect to any application when analyzing how a range of composite structures will behave in real-world scenarios. This is especially true when the scenario becomes extreme and place enormous external pressures on the structures! NX accurately analyzes composite and metallics structures in accordance with real-world scenarios. It’s a feature that came into its own when Ron developed radar antennas with EASAT for use in intense weather zones.
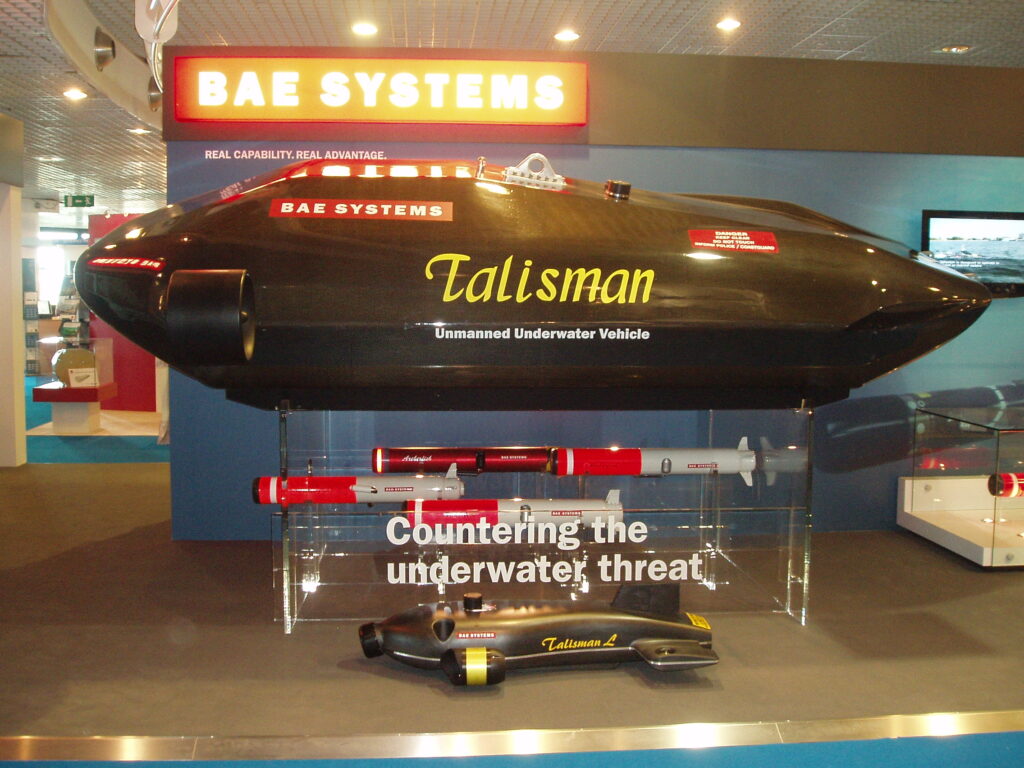
In addition, NX’s integrated finite element analysis and laminate analysis tools ensured Ron could successfully engineer the structure of an Unmanned Underwater Vehicle (UUV). The structure had to withstand intense water pressures when descending into the depths of the ocean. NX allows the analysis of flow-diverting devices to withstand extreme temperatures, pressures and abrasion in the bores of deep oil and gas wells.
Inspiring the next generation of engineers
The worlds’ brightest minds are involved in composite manufacturing and advanced engineering. The capabilities of companies continue to accelerate at apace as we move through the 21st century. The next big challenge is to engage the next generation of young people to become the engineers of the future; how can the industry achieve this?
“Don’t talk about the science or engineering” is one approach Ron has encouraged throughout his illustrious career. Instead, show them illustrations and get them excited by achievements. Engineering is pioneering, capable of pushing us toward a more advanced society. Because of this, it’s also incredibly complex, underpinned by advanced scientific fundamentals, formulas and theories; these can all act as a deterrent for the younger engineers during the early stages of their career.
Focusing on examples to underpin the science behind complex projects is an interesting way to engage the next generation of engineers. Recognizing the importance satellite comms stations played during the 2010 World Cup is one prime example. In addition, learning the fundamental basics of engineering using Minecraft is another approach aspiring engineers can take. The complex science remains hidden, and engineers can focus on what can be created. It’s an approach which keeps young engineers engaged through identifying tasks that are relatable to them; but also builds the fundamental knowledge needed to become specialists in their chosen field.
Take that knowledge, and apply it to an application
Of course, being passionate about niche projects grabs an aspiring engineer’s attention, but this is just the beginning. It’s important that these young individuals channel this enthusiasm to have a strong understanding of dynamic and composite analysis. New engineers need to study the basic formulas before using the application of their choice. Ron has encountered engineers beginning to use their software package before understanding the science which the package is built on. It’s an approach which leads to incorrect composite structures created, resulting in costly reworks. This inevitably leads to the total number of iterations increasing, impacting on the effectiveness of the total workflow.
Summary
Fortunately, young engineers of the future continue to recognize the inherent skills that go into becoming competent engineers. A positive trend has emerged throughout the pandemic; aspiring engineers continue to recognize how important science and engineering are. More and more students are studying science and engineering than ever before.
It’s clear that engineers continue to recognize the importance of materials science and composite manufacturing in play in todays’ society. They also understand how a career in science can enrich their lives and create structures they can be proud of.
Continue your journey with Siemens technology
Register today to learn how NX, Simcenter and Fibersim used in an integrated workflow during product development result in an improved outcome.
Comments
Leave a Reply
You must be logged in to post a comment.
Download Fake Bitcoin Sender Software