Bridging the gaps in electronic systems design Blog series | Closing the loop: Extending the digital thread to manufacturing – Part 4
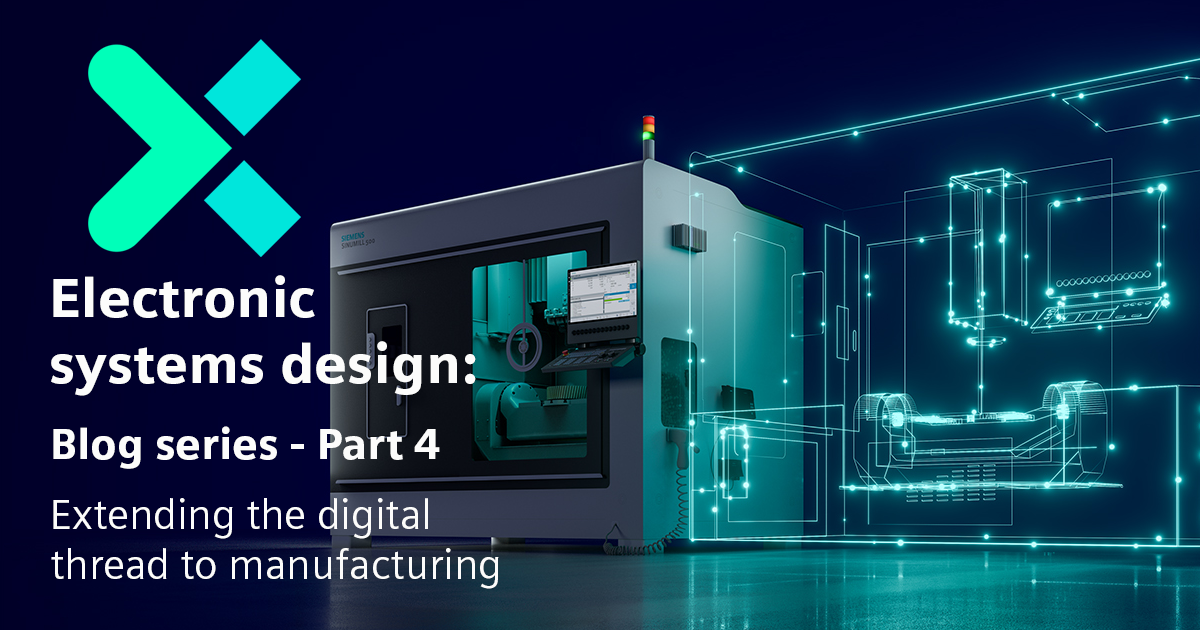
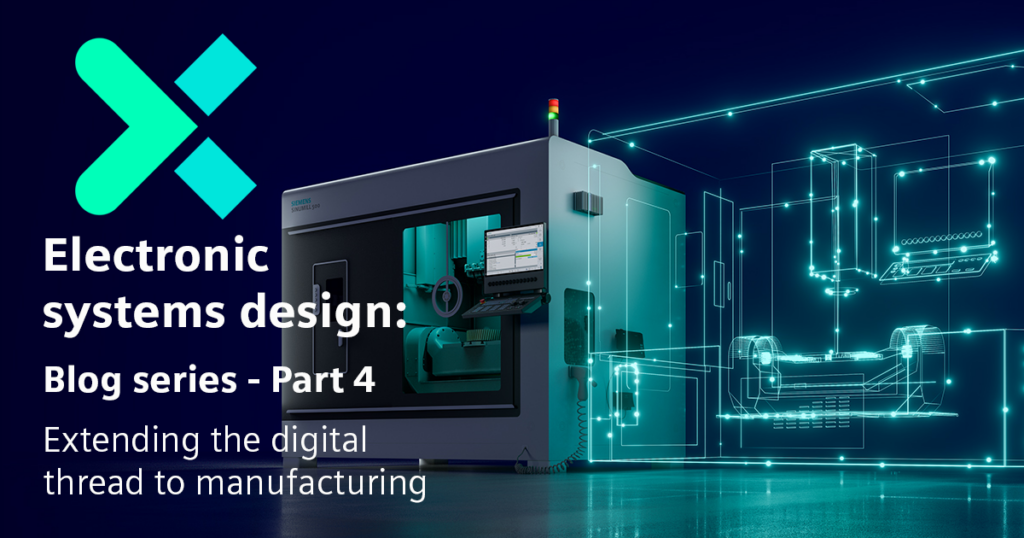
Time is the one resource that electronics companies can never have enough of. In an industry where product lifecycles are measured in months and competition is fierce, every delay, inefficiency and disconnect between design and manufacturing can be the difference between success and failure.
Consider this: a recent study found that electronics companies spend an average of 33% of their time on non-productive activities, such as searching for data, waiting for approvals, and reworking designs. That’s a staggering amount of wasted time and resources that could be better spent on innovation, quality improvement and getting products to market faster.
But what if there was a way to eliminate these inefficiencies? What if you could create a seamless, end-to-end digital thread that connects every stage of the product lifecycle, from concept to production?
In this final installment of our blog series on electronic systems design, we’ll explore how extending the digital thread to manufacturing can help electronics companies close the loop, eliminate waste and accelerate innovation. We’ll dive into the power of the digital twin, examine real-world success stories and show how Siemens Xcelerator enables companies to unlock the full potential of their products and processes.
Did you miss the previous posts in this series? Here’s a quick recap:
- In our first post, we explored the challenges of electronic systems design and the power of an integrated platform like Siemens Xcelerator to break down silos and drive innovation.
- In our second post, we examined how seamless ECAD-MCAD collaboration can accelerate design and reduce errors.
- In our third post, we delved into simulation and how it can help companies optimize designs, reduce physical testing and improve product quality.
Let’s dive into the final puzzle: extending the digital thread to manufacturing.
The power of the digital twin
A digital twin is a virtual replica of a physical product or system, complete with all the data, models and processes that define it. By leveraging the digital twin, electronics companies can optimize manufacturing processes, identify potential issues, and ensure the highest levels of quality and reliability.
However, creating a comprehensive digital twin is challenging. It requires a unified, integrated approach that combines design, simulation, and manufacturing data into a coherent whole.
That’s where Siemens Xcelerator comes in.
Extending the digital thread with Siemens Xcelerator
Throughout this blog series, we’ve explored how Siemens Xcelerator enables electronics companies to break down silos, accelerate innovation, and improve product quality. From seamless ECAD-MCAD collaboration to powerful simulation capabilities, Siemens Xcelerator provides a comprehensive suite of tools and solutions that drive digital transformation.
But Siemens Xcelerator’s true power lies in its ability to extend the digital thread to manufacturing. By leveraging tools like NX, Teamcenter, and Tecnomatix, companies can create a comprehensive digital twin that spans the entire product lifecycle.
With NX, engineers can embed Product and Manufacturing Information (PMI) directly into 3D CAD models, ensuring that design intent is communicated to manufacturing teams. NX Mold Connect streamlines the mold design process, reducing the risk of costly tooling modifications and production delays. With its powerful additive manufacturing preparation tools, NX helps companies optimize designs for 3D printing, unlocking new levels of innovation and flexibility.
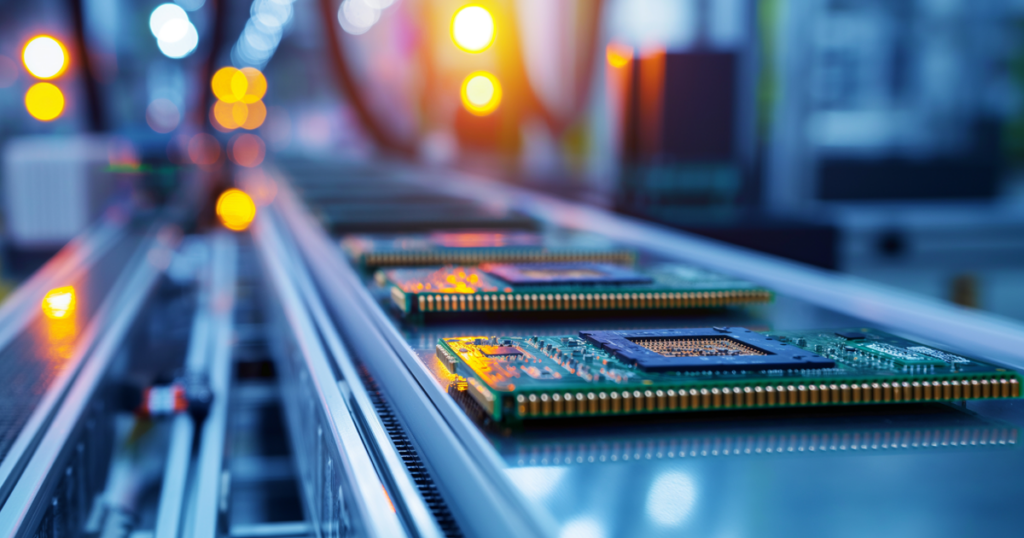
Real-world success story
GE Aviation, a global leader in aircraft engines and systems, has seen firsthand the transformative power of extending the digital thread to manufacturing. By leveraging NX and Teamcenter, GE Aviation has created a comprehensive digital twin of its products, from design to production.
“The digital twin is not just a model; it’s a living, breathing entity that allows us to simulate, predict, and optimize our products and processes,” says Vic Bonneau, President of Electrical Power Systems at GE Aviation. “By extending the digital thread to manufacturing, we’ve reduced development time by 30%, improved product quality, and increased our agility in responding to customer needs.”
The future of electronics manufacturing
As the electronics industry continues to evolve, companies that embrace the power of the digital thread will be well-positioned to thrive. By creating a seamless, end-to-end flow of data and processes, these companies can drive innovation, improve quality, and respond to market demands with unparalleled agility.
So, if you’re looking to close the loop between design and manufacturing, it’s time to explore Siemens Xcelerator’s transformative potential. With its comprehensive suite of tools and solutions, Siemens Xcelerator enables electronics companies to unlock the total value of the digital twin, driving digital transformation and competitive advantage.
As we’ve seen throughout this series, the key to success in electronic systems design and manufacturing lies in breaking down silos, creating a seamless flow of data and processes, and leveraging the power of digital tools and technologies. By extending the digital thread to manufacturing, companies can close the loop, eliminate inefficiencies, and unlock the full potential of their products and processes.
If you’re ready to take the next step in your digital transformation journey, we invite you to explore the capabilities of Siemens Xcelerator. With its proven track record of success and its comprehensive suite of tools and solutions, Siemens Xcelerator is the partner you need to navigate the complex world of electronics design and manufacturing.
Thank you for joining us on this journey through electronic systems design. We hope this series has provided valuable insights and inspiration as you seek to drive innovation, improve quality, and accelerate time-to-market. Please reach out if you have any questions or would like to learn more. We’re here to help you unlock the full potential of your products and processes and thrive in the fast-paced world of electronics manufacturing.