Why impose PCB design constraints?
This is the first in a three-part series examining rule and constraint definition and management that supports a correct-by-design methodology.
Constrain, restrict, limit…we have so many different design requirements that we impose on our PCB tools; it surprises me that we are ever able to actually finish a design at all.
And, these terms all imply severity when, in fact, we are just attempting to achieve compliance (conform to all of our system specifications and rules for high speed performance, manufacturing, power distribution, heat dissipation, etc.).
We need to be able to define, modify, edit, manage and validate our constraints, so we use constraint management and editing tools. That said, why don’t we have a compliance or conformity editor instead? I suppose conformity manager simply does not quite roll off the tongue as well.
The Importance of Rule Definition and Management
As we strive to meet all of these diverse rules while designs continue to increase in complexity and time-to-market remains critical, it is imperative to have a single rule entry system that is central and integral to your design flow. From pre-schematic through PCB layout and routing to manufacturing, that system should be:
- Easy to use – even for casual users
- Consistent so you can enter or modify rules in the same editing environment at an point in the design cycle, anywhere on the design
- Efficient to maximize productivity so that you spend more time designing
- Accurate so you can validate actual design data against required rules
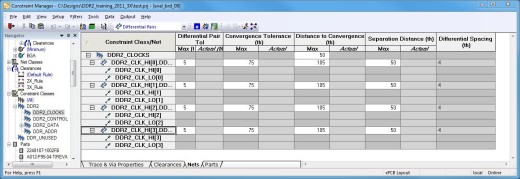
Constraint Definition
All PCB design constraints should be equally accessible from the schematic, layout, and routing environments. There are also several areas of rule and constraint definition and management that should be considered, including the following:
- Defining net classes and constraint classes that are used across the entire design flow
- Different specific constraint types such as topology, matched lengths, differential pairs and clearance rules that adhere to your system specifications
- Adhering to these rules during placement and routing to minimize post layout editing
- Post-layout validation and verification to ensure that all of your constraints are met
More on this topic in the next two posts. In the meantime, I have a question for you – what is the most challenging aspect of design rule/constraint entry and management that you face today? Are there new and upcoming technological requirements that are difficult to address?
To learn more about the importance of PCB design constraints, check out this white paper, “Why PCB Design Constraints Should Drive Your Design Flow.”