Building up supply chain resilience
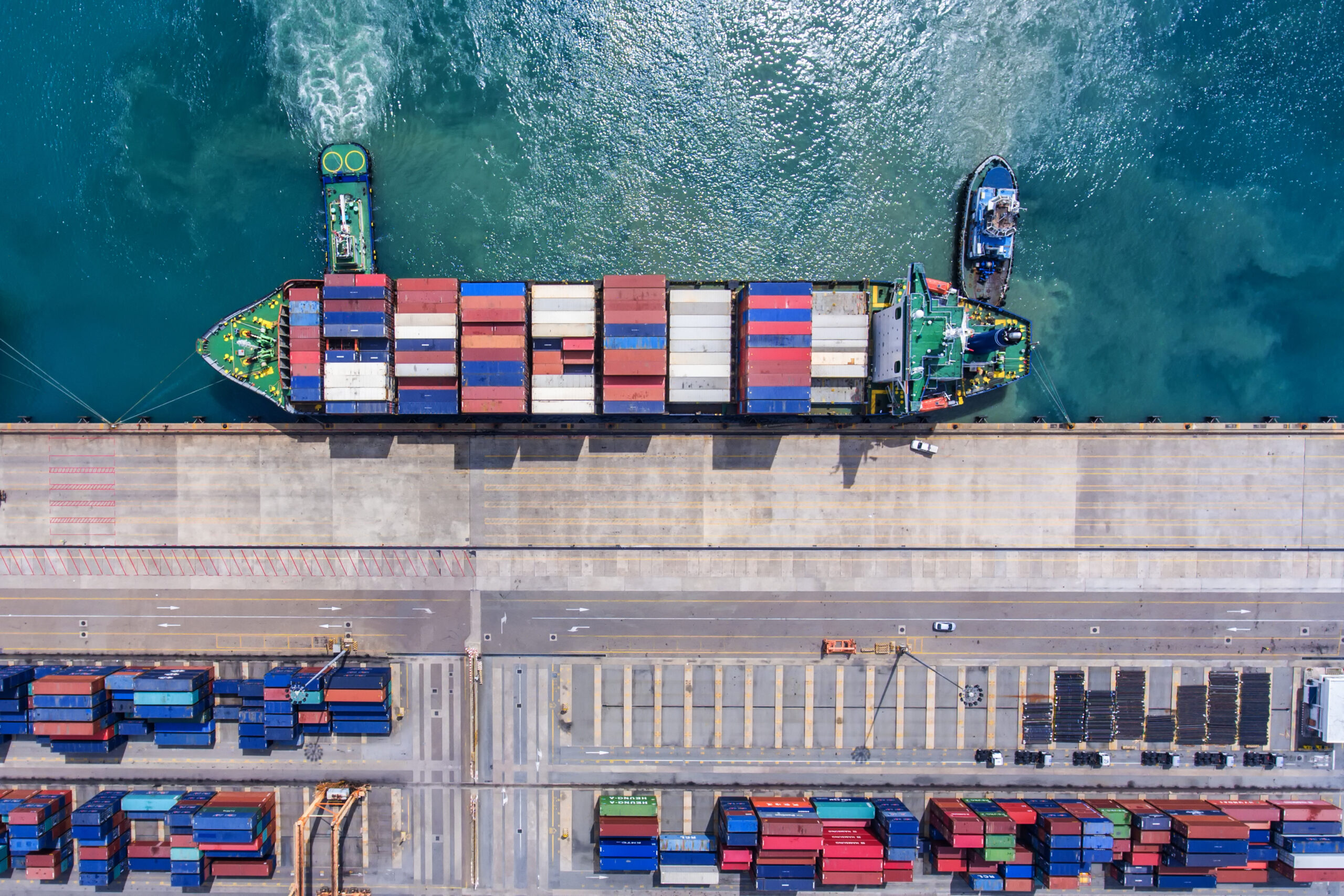
Supply chain design is the key to creating robust and competitive supply chains as disruptions become the new normal
The last few years have been marked by numerous supply chain disruptions, which still pose extreme challenges for supply chain managers. The flood disaster in Germany in 2021, the Russia-Ukraine conflict or the blockade of the Suez-Channel are just a few examples. Such events occur unpredictably and with short-term effects, sometimes completely shutting down individual nodes in delivery networks for an indefinite period. In addition to that, a further increase in complexity is predicted. Global networks are partly limited to a few sources of supply, climate change is leading to an increase in extreme weather events, and the number of cyberattacks has risen rapidly in recent years – with no prospect of change. Companies must adapt to this new normal scenario. In this context, supply chain resilience is often cited as an answer. But what exactly is behind the buzzword, and how can a resilient supply chain can be achieved?
The resilience of supply chains
Resilience is a versatile term these days. In the supply chain sector, resilience refers to the ability to avoid and/or mitigate the effect of certain supply chain disruptions. Supply chain risks can be broken down into operational and disruptive risks. Operational risks occur in daily business and usually cause limited damage (e.g., quality problems or delayed deliveries). Disruptive risks are individual events that are associated with a high potential for damage and a high degree of uncertainty. Such events as natural disasters or geopolitical conflicts can occur unexpectedly and cause long-lasting disruptions and delays.
Although operational risks are usually mitigated by appropriate processes and qualified employees in day-to-day business, disruptive risks require new approaches. In this context, supply chain design is an essential process to ensure the long-term stability of supply chains.
Diversifying risks through robust network design
Supply chain design ranges from defining the general supply chain structure to location selection or defining of transport modes, delivery rhythms and inventory levels. Traditionally, the dimensions of costs, service, quality and emissions are considered. Although resilience is often not integrated in a structured way, the effects of network design activities are closely linked to the resilience of supply chains.
The network structure, segmentation and number of locations influence the risk distribution in the network as well as the responsiveness and adaptability of a supply chain. The inclusion of risk indicators in location selection (for instance, natural or political risks) can minimize the probability of site-related disruptions. Furthermore, by considering redundancies, safety stocks and free capacities, the effects of disruptive events are mitigated, and flexibilities are created to quickly restore the original network performance in case of disruption.
Since the individual levers have different effects, combining measures makes sense. In practice, this poses various challenges for decision-makers.
Meeting challenges and fulfilling requirements
Disruptive risks often come with a high degree of uncertainty, as it is unclear whether a particular event will occur and how long its effects will last. As a result, it is difficult to quantify the consequences of potential disruptions. This challenge of an objective risk assessment is further reinforced by the lack of a solid database. At the same time, the amount of relevant data is continuously growing, which makes it difficult for many companies to effectively link and analyze the right data. This makes the objective balancing of the relevant network criteria even more complex. Before an effective network configuration is possible, the following prerequisites must be met:
- Technology: Use specialized software that can be used to combine different data sources, process big data, and provide features such as location optimization or risk analysis.
- Data: Integrate advanced data sources that provide insights into the risk profile of locations (suppliers, warehouses, ports, etc.) within the supply chain.
- Transparency: Link the relevant data via appropriate technologies to digitalize the physical supply chain and ensure transparency – from the supplier to the final customer.
- Know-how and methods: Develop suitable models and methods to gain a comprehensive picture of the as-is situation and to identify bottlenecks at an early stage.
Based on this foundation, supply chain network changes can be defined and evaluated that:
- Avoid and/or mitigate the occurrence of disruptions (robustness)
- Offer the possibility to react quickly to interruptions and start regeneration early (agility)
- Restore the original performance as quickly as possible (flexibility)
Since it is difficult to precisely quantify the risks, strategic guardrails are important, which can be derived by integrating the topic of resilience into the supply chain strategy.
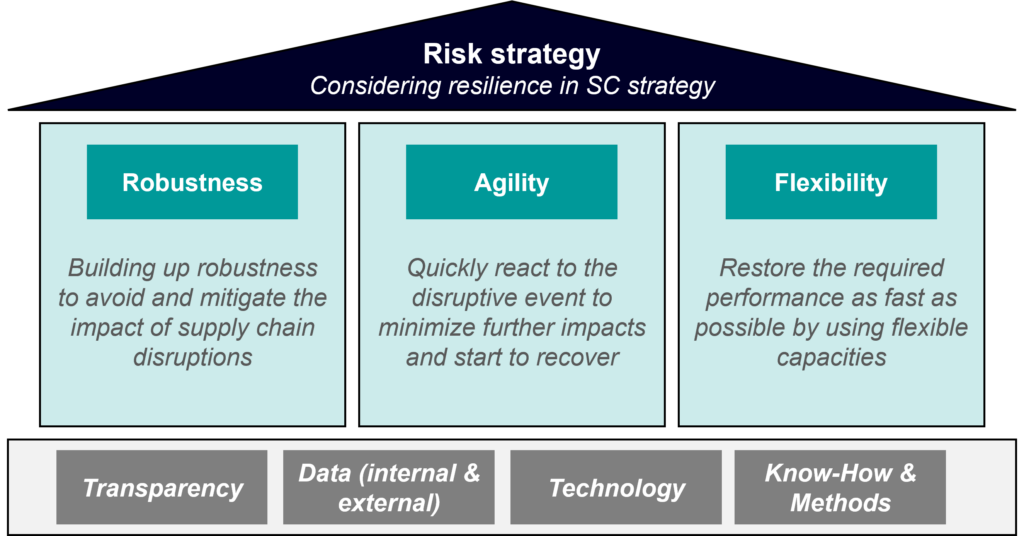
Siemens’ approach to designing resilient and competitive supply chains
Siemens Digital Logistics have developed targeted solutions based on the current developments. The approach, focusing on supply chain design, follows four phases:
Phase 1: End-to-end (E2E) Visibility
The first step is to create comprehensive network visibility. Various data sources are linked, including transaction data, master data or inventory levels. Using this data, a digital twin is created in the Siemens Digital Industries Software’s Supply Chain Suite. This digital twin is a virtual representation of the physical supply chain and makes it possible to identify potential bottlenecks at an early stage. It is also enriched with external data to gain insights into the risk profile of suppliers, locations, transport routes and markets in addition to internal vulnerabilities and bottlenecks. This can include data to assess natural risks, political risks, and more.
Phase 2: Insights and status quo
The digital twin, cost models and risk models are used to gain important insights into the status quo of the current network. Resilience-related risk key performance indicators (KPIs) are collected, which are fed by external risk data, demand data, inventory data or bill-of-materials (BOM) structures. These risk KPIs can be individually assigned to supply chain nodes, products or materials and can be categorized according to damage potential and probability of occurrence. The probability of occurrence can be estimated based on external data and provides valuable input for the derivation of realistic scenarios, such as: What happens if the central warehouse is on strike for three weeks? What happens if supplier X can no longer supply component Y for a month? The impact of the defined scenarios can be quantified in various dimensions using the digital twin.
Phase 3: Strategic resilience
Based on the analyses and with the help of a morphological box, network changes and strategic frame conditions can be defined. The framework can be used to answer risk related questions, such as: What should be the degree of decentralization? What flexibility should be assigned to individual locations? Which risk areas should be excluded as possible locations?
The defined configuration options are simulated and assessed. Afterwards the influence of certain network changes on the defined risk KPIs and costs can be determined. In addition to that, selected scenarios can be stress-tested using sensitivity analysis. Such sensitivity could relate to the integration of maximal allowed risk scores. Comparing the configuration options on the one hand, and the stress tests on the other, provide an optimal decision base.
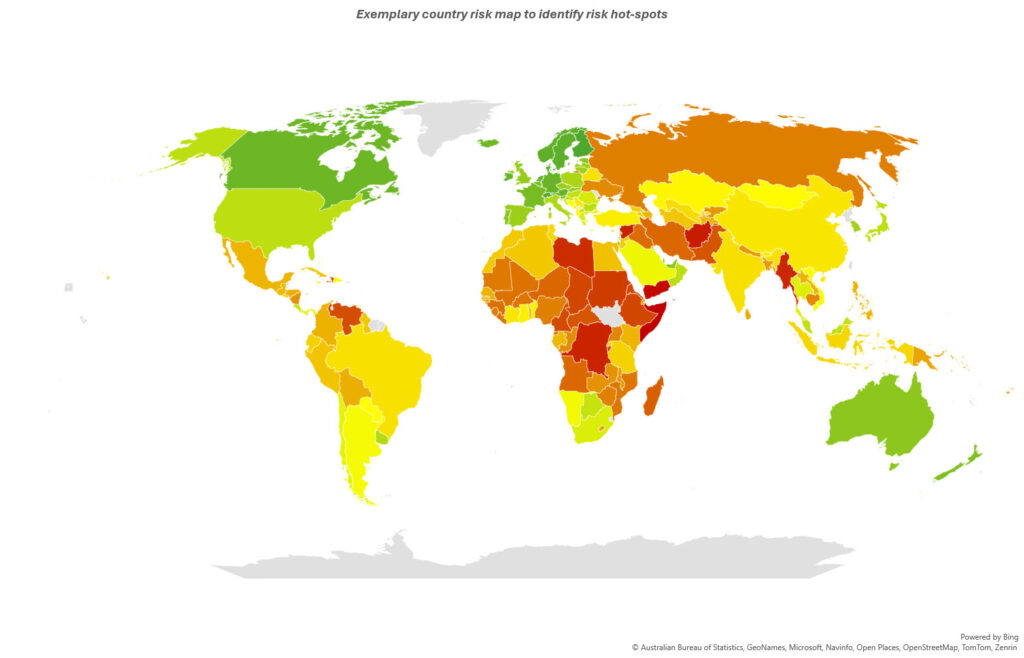
Phase 4: Operational resilience
After a certain network structure has been determined, a residual risk will remain. In principle, this cannot be prevented, but the level of this residual risk can be influenced. To minimize the risk, tactical optimizations can be made. These options include adjusted inventories of critical components, relocated suppliers, shortened delivery times, or increased order frequencies.
Once the network design is completed, the supply chain can be made operational. Siemens offers the option of switching from a digital twin (Supply Chain Suite) to a control tower (AX4™ software), which monitors supply chain activities in real time and provides important insights.
Although supply chain design is an effective way to increase the resilience of the supply chain, it does not eliminate certain risks. This is due to the presence of critical raw materials and/or components that can only be supplied by selected sources. At this point, the power of supply chain design is limited, which leads to the need to shift left and to bring supply chain resilience to the upstream level.
If dependencies and risks of the countries of supply are already considered within the product development process, serious disruptions can be avoided at an early stage and planning can be relieved. Using Teamcenter® Product Cost Management software, Siemens offers a complementary solution that supports engineers in the design phase with integrated risk analysis.
Results and key takeaways
The topic of supply chain resilience has gained importance in recent years and will continue to play a central role in the design of supply chains in the future. Using Teamcenter Product Cost Management, risk data can be integrated into the product development process to reduce the dependency on critical suppliers and/or raw materials. Using Supply Chain Suite, the remaining risks can be minimized at the strategic and tactical level as part of the supply chain design process. Finally, interruptions can be identified in real time by control tower solutions and possible effects can be mitigated (AX4). This interaction and the provision of the necessary decision base create an optimal balance in the supply chain networks.
Conclusion
- Supply chain resilience is mainly related to disruptive events with a low probability of occurrence and the potential for severe damages
- Companies must adapt to new frame conditions, expand existing data sources and approaches, and consider resilience in early planning phases
- Supply chain design is an effective measure of making supply chains more resilient in the medium and long term. Ideally, this is complemented by resilient product design and control tower solutions.
- By using tools (Supply Chain Suite, AX4, Teamcenter Product Cost Management), external data sources and many years of consulting know-how, Siemens Digital Logistics can help to optimally balance the network criteria of cost, service, emissions, quality and risk.
Want to learn more?
Contact Siemens Digital Logistics today to discuss how our solutions can help your business thrive in the face of these new regulations. Learn more about our Consulting services.
More information
- Contact us (select “Digital Logistics” as Product)
- Get our eBook “Building up supply chain resilience”
- Download the comprehensive infographic: “Mastering Vulnerable Supply Chains”
The Experts

Consultant | Siemens Digital Logistics

Principal | Siemens Digital Logistics