Brewed for Adaptability: Digital Twins as the Key Ingredient in Future-Proofing Process Industries
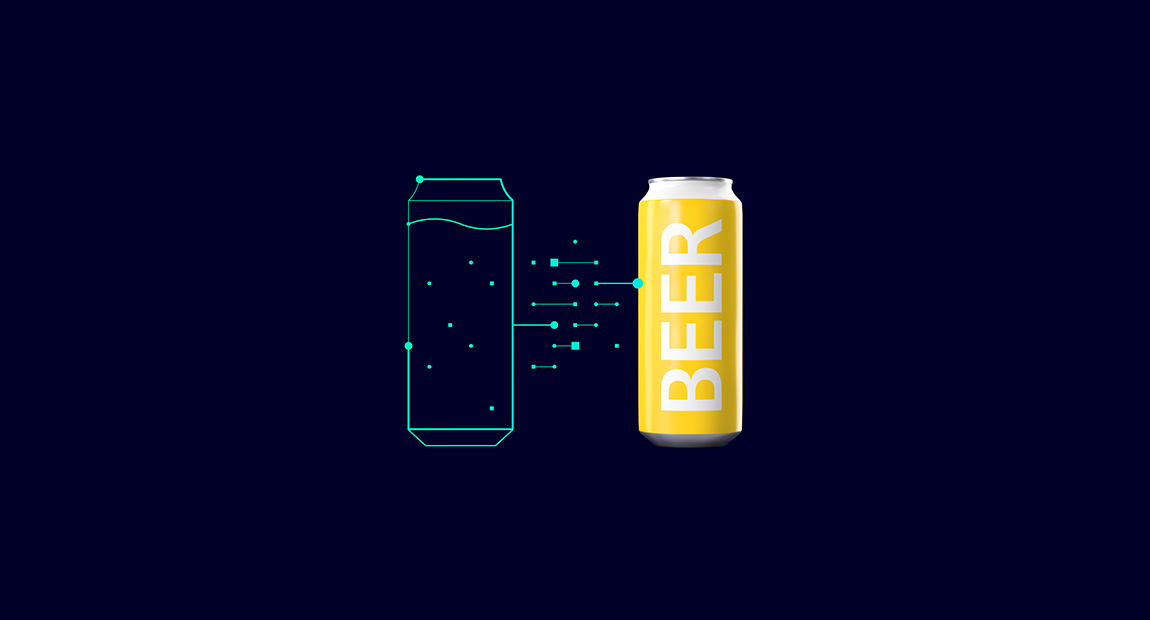
The process industries – chemicals, metals, beverages, and more – are facing a period of significant change. Rising costs, evolving consumer preferences, and a volatile economic landscape demand innovative solutions for long-term success. This is part two of a 2-part series. We’ll explore how Siemens Digital Logistics can empower your process industry business with digital twin technology and consulting services.
We have pinpointed a number of practical applications that demonstrate the effectiveness of digital twins:
Evaluating and proposing product line adjustments from a production point of view
As described in part 1, breweries are diversifying their offerings, introducing non-alcoholic drinks to their line-ups. This strategic move presents a significant challenge to their production capabilities. As they incorporate these new options, they still need to allocate tank and bottling resources to their traditional beer production. To accommodate these additional non-alcoholic items, breweries may find themselves facing the need to expand their production capacity, possibly by investing in new tanks, to handle the varied production – even though the overall volume of beverages produced isn’t increasing. Such expansion can inflate fixed costs, potentially tipping the scales towards a loss on some products. An option to overcome this issue could be to remove a small number of the traditional beers from the line-up. A digital twin can help to select the best removal candidate in terms of both business and production impact. Key is to avoid investments and higher costs without losing profit. Additionally, it allows us to observe the impact on warehouse operations and the inventory of finished goods.
Facility scaling and expansion
Although the overall consumption of alcoholic beer may be on the decline, certain high-demand alcoholic and non-alcoholic products are anticipated to experience growth, potentially influenced by fresh marketing approaches. Breweries, often established in historical locations with fixed facilities, now face the challenge of determining how to strategically expand their operations. This might involve investments in both production and warehousing. The key lies in choosing the correct production strategy. We’ve observed instances where warehouse capacity historically was a bottleneck, necessitating a just-in-time production model to prevent overflow. Yet, persisting with just-in-time production in the face of growth would have required major investments. By modifying the production strategy to build stock with a push production approach, breweries were able to avoid hefty investments into tanks and achieve a more cost-effective expansion of warehouse capacity.
An alternative approach may involve relocating portions of the production and/or bottling processes to different sites. This change would introduce transportation and handling activities, the costs of which can be accurately modeled using a digital twin simulation.
When it comes to determining the optimal size for facilities, such as production and warehousing spaces, digital twins have revolutionized the process. They enable the modeling of various growth scenarios at no additional cost and facilitate the evaluation of key performance indicators. This capacity to navigate uncertainty empowers decision-makers to choose the most profitable course of action in situations that have a significant influence on the bottom line.
Overcoming capacity constraints: Strategic roadmap for a brewery from 2022 to 2026: Overcoming capacity constraints by combining product line adjustments with facility scaling strategies in a digital twin
![[Percentage utilization of tanks per process step in an illustrative brewery]](https://blogs.sw.siemens.com/wp-content/uploads/sites/71/2024/05/capacity2-1-1024x519.png)
Tour planning and optimization
Whether embarking on a weekend hiking adventure or savoring the ambiance of a warm summer evening, a visit to a biergarten is a beloved activity for many. Local breweries often supply these venues, ensuring patrons can enjoy a chilled beer. However, behind the scenes, that refreshing drink has journeyed from brewery to biergarten. In addition to serving eateries, breweries also distribute to beverage retailers, their second primary outlet. Both channels necessitate meticulous transportation and route planning, with deliveries to restaurants being particularly intricate due to frequent, small-volume stops that are cost-intensive to service. Employing advanced routing algorithms within a digital twin framework can lead to significant cost savings. This was particularly noticeable during the Covid-19 pandemic when restaurant closures and reduced patronage forced breweries to recalibrate their delivery strategies. Breweries that used digital twins were way more agile in reacting to those changed conditions, saving costs.
In the realm of distribution logistics, digital twins offer a valuable tool for locating depots, developing fleet strategies, optimizing delivery routes, including scheduling within specific time frames, consolidating shipments, and enhancing truck. In the next section, we will see how we can further utilize this.
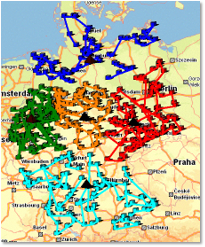
Sustainability and reduction of carbon dioxide emissions
Process industries such as breweries are under increasing pressure from customers, stakeholders, and investors to reduce carbon dioxide emissions and maintain high sustainability standards. By simulating various transportation scenarios, ensuring optimal load utilization, configuring delivery fleets with respect to their emissions, and assessing the transition to electric vehicles with considerations for charging networks and infrastructure, digital twins can help companies to facilitate more environmentally friendly transport planning, reduce their carbon footprint and move towards sustainable logistics practices.
Management of empties
Whether due to growth, the introduction of new bottle types, or external shocks like the COVID-19 pandemic, breweries have been grappling with the challenge of obtaining a sufficient supply of empty bottles and kegs for their production. A shortage of empty bottles can halt the filling process and therefore the production as a whole, leading to potential losses in sales and profits. Managing the return of bottles and kegs, maintaining an ample inventory of reusable containers, and ensuring efficient logistics for the collection and distribution of empties have always been crucial for streamlining processes. A digital twin can be a valuable solution in this scenario, helping to accurately determine container circulation times, estimate the required amount of empties for a specific production period, and forecast the needed container quantities for future growth. It can also aid in planning the collection and transportation of empties back to the breweries.
Looking beyond
Although the brewery sector is highlighted here, similar obstacles and prospects are prevalent across the broad spectrum of process industries. Encompassing sectors such as chemicals, metals, and beverages, they have recently transitioned from a period of growth to one of uncertainty influenced by several factors. These industries are grappling with challenges stemming from inflation, evolving consumer preferences, the pressure to become more sustainable, and unstable energy prices, which have been exacerbated by geopolitical events like the Ukraine crisis. These disruptions have led to increased production costs and shifts in market demand, particularly as consumers become more cautious with spending during times of high inflation.
Key Takeaways:
- Digital twins have become a critical tool for process industries to address the complexities of supply chain management, enabling strategic planning and precise scenario analysis that surpass conventional methodologies.
- The technology facilitates the evaluation of new product additions, adjustments in product lines, and production strategies without significant upfront investments, leading to optimized operational efficiency.
- Within distribution logistics, digital twins optimize delivery routes and improve freight consolidation and vehicle capacity utilization, which is particularly valuable during periods of market volatility.
- Process industries are facing pressure to reduce carbon dioxide emissions and maintain high sustainability standards. Digital twins can help facilitate more environmentally friendly transport planning, reduce carbon footprint, and move towards sustainable logistics practices.
- A sufficient supply of empty containers, barrels and bottles is crucial for the production. Yet, companies still have issues with managing the corresponding processes. A digital twin can help manage the return of empties, maintain inventory of reusable containers, and streamline their collection and distribution logistics.
The agility provided by digital twins allows process industries to swiftly adapt to changing market conditions, maintain competitiveness, and make data-driven decisions that safeguard profitability in a fluctuating economic landscape.
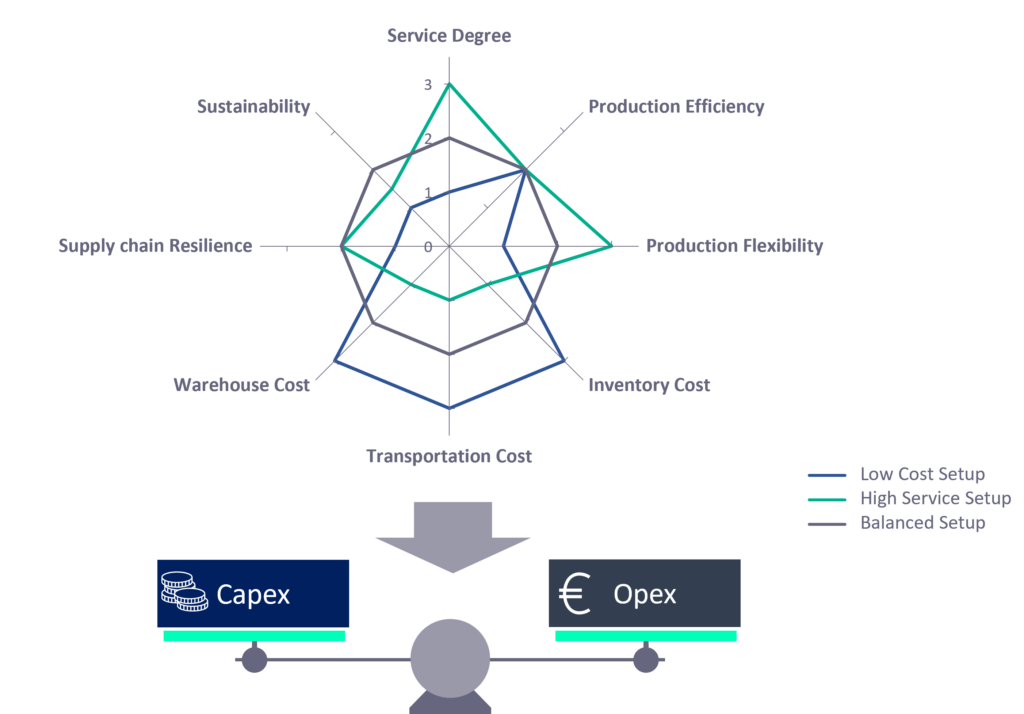
The Expert
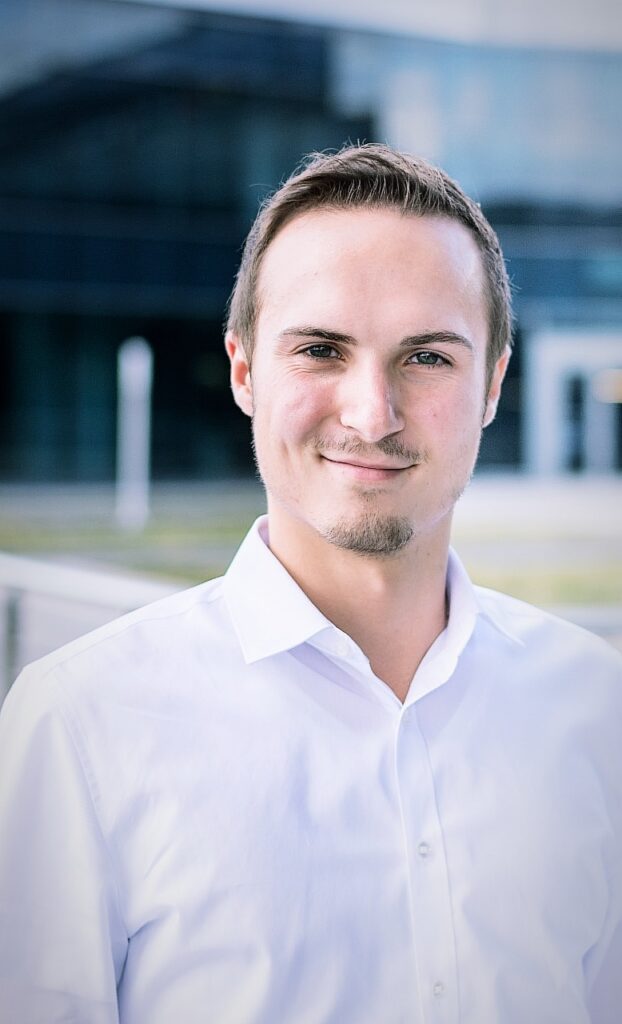
Senior Consultant | Siemens Digital Logistics
Want to learn more?
Read the first article in this series: “The Drought of Tradition: Embracing Digital Twins in Process Industries Amidst Rising Challenges“
Contact Siemens Digital Logistics today to discuss how our solutions can help your business thrive in the face of these new regulations. Learn more about our Consulting services.
More information
Contact us (select “Digital Logistics” as Product)