Erschließung von Innovationen in der Fahrzeugsystemtechnik mit MBSE
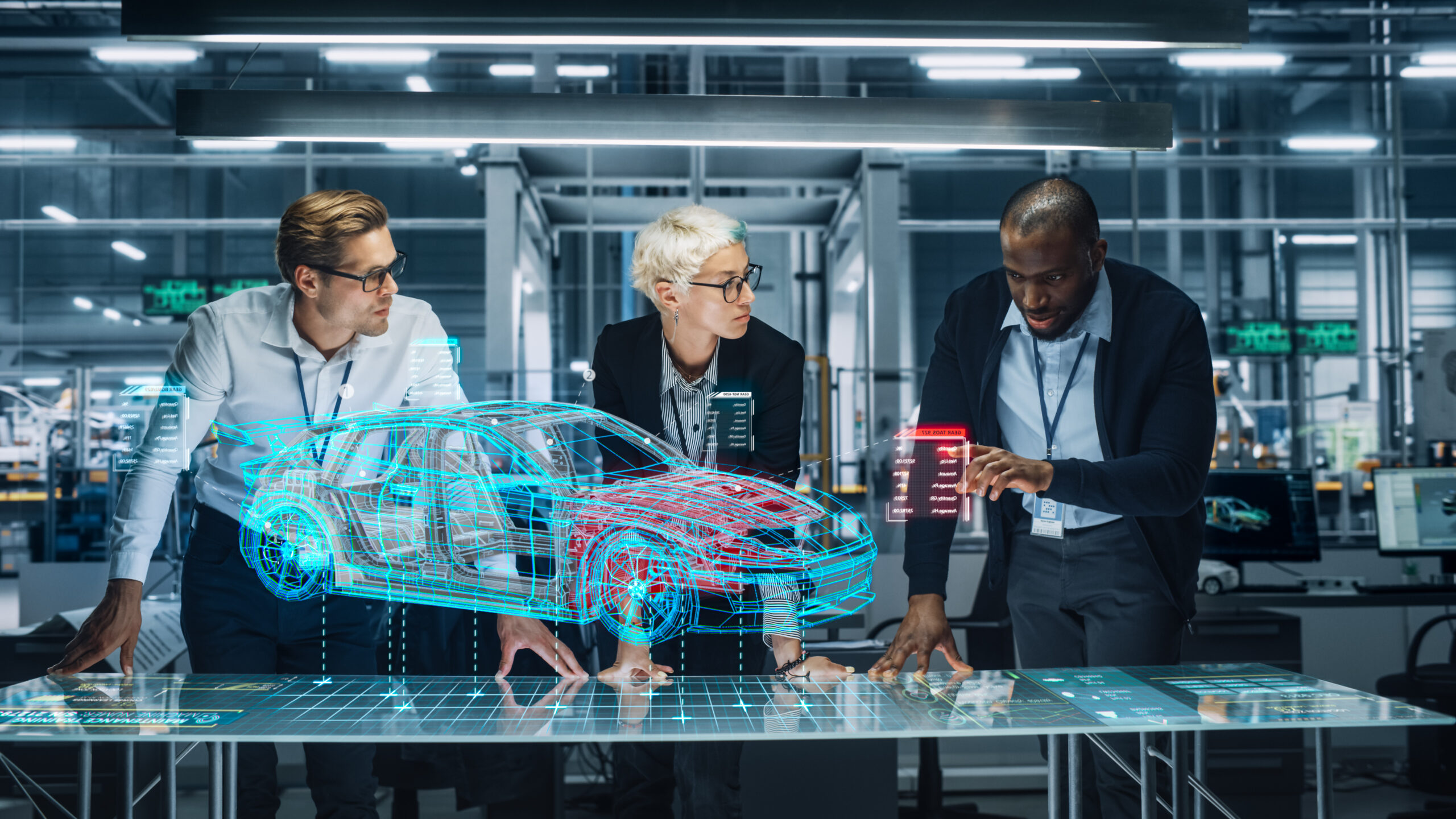
Modellbasiertes Systems Engineering (MBSE) bietet die Tools, um die zunehmende Komplexität der Fahrzeugsystementwicklung auf dem sich schnell entwickelnden Markt für Elektrofahrzeuge zu bewältigen.
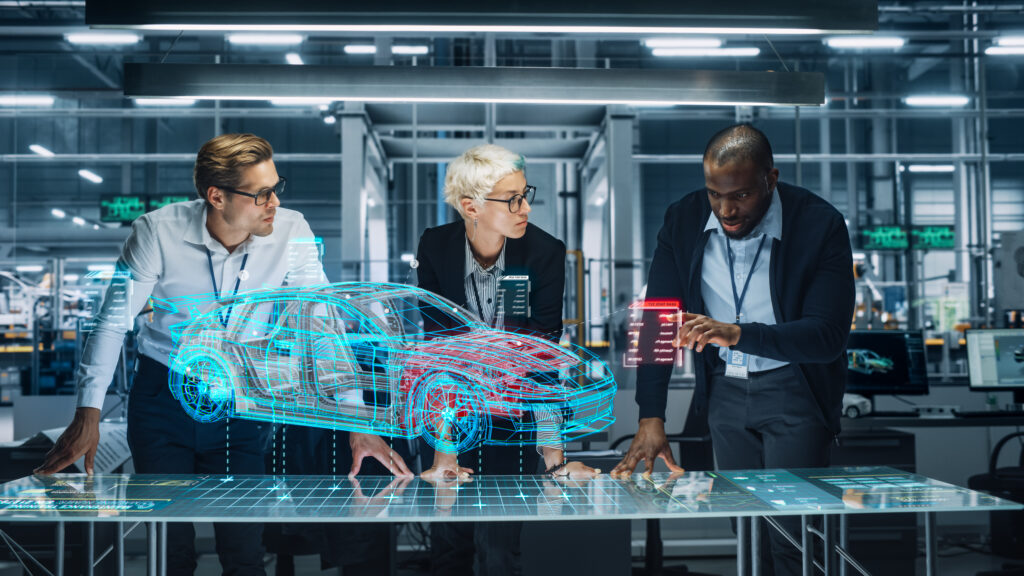
Der Umstieg auf elektrische Antriebe treibt den Wandel in der Automobilindustrie in einem beispiellosen Tempo voran und führt zu einer bisher nicht gekannten Produkt- und Prozesskomplexität.
Da immer mehr Hersteller auf den Markt kommen und sich die Verbraucher über die Marke hinaus auf die Funktionalität und die Anwendererfahrung von Elektrofahrzeugen konzentrieren, wächst der Druck ständig, schneller zu innovieren und gleichzeitig die Kosten zu senken.
Um dieser neuen Herausforderung gerecht zu werden, ist ein neuer Ansatz in der Produktentwicklung erforderlich. Einer, der Herstellern die Tools an die Hand gibt, um wettbewerbsfähig, flexibel und kostengünstig zu bleiben und gleichzeitig die Anforderungen an Qualität, zunehmende Regulierung und Nachhaltigkeit zu erfüllen.
Kürzlich hielt unser Experte Vijay Singh ein Webinar über die Einführung von MBSE, um wettbewerbsfähig, flexibel und kosteneffizient zu bleiben und gleichzeitig Herausforderungen wie Qualität, zunehmende Regulierung, Nachhaltigkeit und Kosten zu bewältigen. Er erklärte, wie man Herausforderungen meistert und sicherstellt, dass der digitale rote Faden der Anforderungen von den Anforderungen über die Konstruktion bis hin zur Analyse, Verifikation und Validierung in der Modellierungsumgebung verbleibt. Wenn Sie mehr wissen möchten, können Sie sich hier für das Webinar anmelden: Komplexität in der Automobilindustrie mit einem systemtechnischen Ansatz bewältigen.
MBSE ermöglicht einen neuen, funktionalen Ansatz in der Automobiltechnik
Anstelle des traditionellen dokumentenbasierten Informationsaustauschs zwischen Teams verwendet MBSE ein Systemmodell als primäres Mittel der Kommunikation und des Informationsaustauschs zwischen technischen Disziplinen und Interessengruppen während des gesamten Lebenszyklus der Systementwicklung.
Dadurch lässt sich alles von den ersten Anforderungen über die Konstruktion und die endgültige Validierung bis hin zu späteren Lebenszyklusphasen unterstützen und verfolgen. MBSE erreicht dies, indem es einen digitalen roten Faden erstellt, der sich durch den gesamten Entwicklungsprozess zieht.
Wichtig ist, dass der MBSE-gesteuerte digitale rote Faden es den Herstellern ermöglicht, die Entwicklung von Automobilsystemen auf eine andere Art und Weise zu betrachten, nämlich einen funktionalen, ganzheitlichen Ansatz für die Produktentwicklung zu verfolgen. Mit anderen Worten, sich auf die Funktionalität zu konzentrieren, die Sie suchen, und nicht auf die mechanischen Systeme dahinter. Damit können Hersteller ein wirklich softwaredefiniertes Fahrzeug einführen, das durch Systemupdates kontinuierlich verbessert werden kann.
Erkunden Sie die Architektur zu einem früheren Zeitpunkt im Konstruktionsprozess
Die Definition des Produkts umfasst die Erstellung eines detaillierten Anforderungskatalogs und eines Systemarchitekturmodells, das jeden Aspekt des Elektroantriebsystems beschreibt. Die Architektur des Elektroantriebsystems bildet die Grundlage für den gesamten Entwicklungsprozess. Sie definiert die Struktur des Systems und die Beziehungen zwischen seinen Komponenten.
Das Erkunden elektrischer Antriebsarchitekturen in einem frühen Stadium der Konstruktion versetzt Konstrukteure in die Lage, alle möglichen Kombinationen von Wechselrichter, Motor und Getriebe zu kennen und zu bewerten, die den definierten Anforderungen, Randbedingungen und Leistungszielen entsprechen. Dieser Prozess stellt sicher, dass das elektrische Antriebssystem so konstruiert ist, dass es ein optimales und effizientes Leistungsvermögen bietet, was letztendlich zu einem besseren Endprodukt führt.
Nehmen wir das Beispiel eines E-Drive-Systems. Es können verschiedene Arten von Elektromotoren verwendet werden, darunter Induktions- und Permanentmagnetmotoren. Die Auswahl des richtigen Konzepts in der Anfangsphase des Konstruktionsprozesses ist entscheidend, da falsche Entscheidungen später im Entwicklungsprozess erhebliche Nacharbeiten notwendig machen können. Dies kann dazu führen, dass die Entwicklungszeit viel länger dauert als ursprünglich angenommen, was letztlich die Kosten erhöht und die Produkteinführung verzögert.
Für die architektonische Exploration eines elektrischen Antriebssystems verwenden Hersteller die leistungsfähigen Tools Simcenter™ Amesim™ und Simcenter™ Studio. Diese Software-Tools kombinieren erstklassige Systemsimulationen, um eine leistungsstarke Plattform bereitzustellen, die sich zum Erkunden von Optionen für die E-Drive-Architektur eignet. Dies ermöglicht es den Konstrukteuren, das Leistungsvermögen jeder Architekturoption zu simulieren, einschließlich Faktoren wie Effizienz, thermisches Verhalten, Lärm und Vibrationen, Kosten und Gewicht.
Darüber hinaus können Konstrukteure mit der Implementierung von MBSE über die integrierte Simcenter-Umgebung den Design-Space mit Hilfe von künstlicher Intelligenz (KI) massiv erweitern. Mithilfe von KI können Konstrukteure jetzt Dutzende oder sogar Hunderte von potenziellen E-Drive-Architekturen anhand eines einzigen Systemarchitekturmodells bewerten.
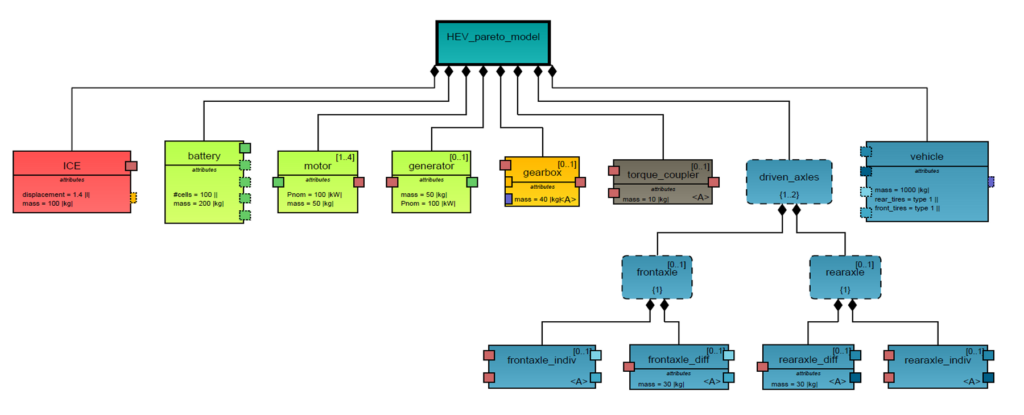
Einen detaillierteren Einblick in den Einsatz von MBSE- und Simcenter-Tools zur Optimierung elektrischer Antriebssysteme erhalten Sie im White Paper: Einführung von MBSE in der Fahrzeugentwicklung.
Anbindung der Architektur an die nachgelagerten Entwicklungsprozesse
Sobald die optimale Architektur identifiziert wurde, wird dasselbe Modell verwendet, um alle produkt- und nachgelagerten Beziehungen zu steuern. Dies ermöglicht die Verwaltung und Kontrolle aller Artefakte über den Entwicklungsprozess, Änderungen, Konfigurationen, Workflows, Variationen und mehr.
Hier kommt der MBSE-Ansatz ins Spiel, der einen robusten Rahmen für die Integration der verschiedenen Modelle und Simulationstools bietet, die von verschiedenen Engineering-Domänen benötigt werden. Modelle werden in den verschiedenen Anwendungen wiederverwendet, und die Auswirkungen von Änderungen, z. B. eine Änderung der Anforderungen, können in der gesamten Entwicklungskette effektiv verwaltet werden.
Was auch immer Sie auf der Seite der Systemarchitektur tun, wird automatisch von den von Ihnen gestellten Anforderungen geprägt und spiegelt diese wider. Und was Sie auf der Seite des Parametermanagements tun, wird automatisch in die Simulations- und Engineering-Workflows integriert.
Wenn Sie mehr darüber erfahren möchten, wie generatives Engineering bei der Erforschung der EV-Architektur eingesetzt werden kann, lesen Sie diesen Artikel von Charged EVs.
Integrierte Workflows durch Vehicle Systems Engineering und den digitalen roten Faden
Der digitale rote Faden bei MBSE sorgt für einen nahtlosen Informations- und Datenfluss zwischen den verschiedenen Phasen der Produktentwicklung. Auf diese Weise können die Simulationsingenieure jederzeit auf die Daten zugreifen und ihre Ergebnisse dann in dieses System zurückübertragen, um die Parameter mit der Ausgabe der Simulation zu aktualisieren.
Dies ermöglicht eine bessere Zusammenarbeit, eine höhere Effizienz und ein besseres Leistungsvermögen während des gesamten Produktlebenszyklus.
Mit Simcenter-Lösungen können Hersteller beispielsweise die Leistungsfähigkeit des HEEDS-Software-Workflow-Managers™ in Verbindung mit der Teamcenter-Simulationssoftware® nutzen, um eine nahtlose Integration zwischen der Systemarchitektur, den Anforderungen und Parametern mit den Simulations-Workflows in der Simcenter 3D- oder Simcenter Motorsolve-Software zu erreichen.
Optimierung und wiederverwendbare Workflows
MBSE und der digitale rote Faden ermöglichen die digitale Kontinuität von der Anforderung über die Entwicklung bis hin zum Endprodukt und verbinden die technischen Disziplinen im gesamten Unternehmen.
Aber Automotive Systems Engineering ist linearer, schrittweiser Prozess. Es ist ein sehr rekursiver und iterativer Prozess mit Endlosschleifen. Durch die Aktivierung wiederverwendbarer Workflows bieten MBSE- und Simcenter-Tools einen robusten und wiederholbaren Prozess für die Konstruktionsoptimierung und kontinuierliche Leistungsausrichtung und ein effizientes Management dieses komplexen, iterativen Prozesses.
Machen Sie etwas einmal, nehmen Sie es auf und es steht dann als Prozess zur Verfügung, der fast automatisch ausgeführt werden kann. Wenn sich also Geschäftsanforderungen oder andere Parameter ändern, können Tests und Analysen erneut durchgeführt werden, ohne dass technische Spezialisten und technische Experten hinzugezogen werden müssen.
Das spart massiv Entwicklungszeit und -kosten und eröffnet neue Möglichkeiten für Innovation und Fahrzeugoptimierung.
Wiederverbindung der Engineering-Domänen
Mit dem Wachstum des Marktes für Elektrofahrzeuge suchen die Kunden nicht nur nach einem Elektroauto, sondern konzentrieren sich gleichermaßen auf Fragen der Qualität, Leistung und Kosten. Geachtet wird auf Aspekte wie Haltbarkeit, Fahrdynamik, Geräusche und Vibrationen sowie die Reichweite des Autos.
Um das notwendige funktions- und domänenübergreifende Systems Engineering zu ermöglichen, das für die Entwicklung eines Elektrofahrzeugs erforderlich ist, das den Markterwartungen entspricht, ist es notwendig, die traditionellen Entwicklungssilos der Vergangenheit hinter sich zu lassen.
Nur ein vernetzter Engineering-Ansatz mit einem integrierten, wiederverwendbaren Workflow und einem digitalen Zwilling bietet Herstellern die erforderliche Toolchain, um die Komplexität der Elektrofahrzeugentwicklung zu bewältigen – sowohl in Bezug auf das Produkt selbst als auch auf den gesamten Entwicklungsprozess.