Simcenter Battery Design Studio
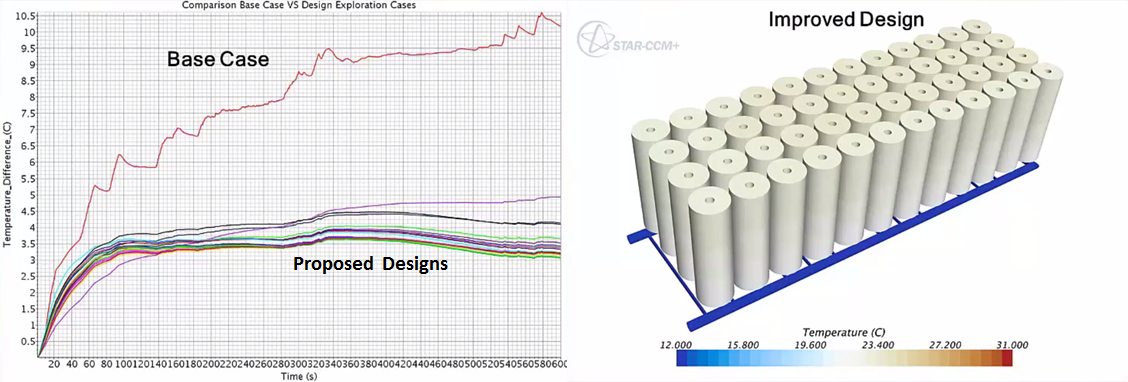
Nov. 2017 „Die wichtigste Produktionseinschränkung besteht bei weitem in der Montage von Batteriemodulen“, sagte Elon Musk in einer Telefonkonferenz mit Analysten nach der Bekanntgabe der Ergebnisse. „Wir hatten einen Subunternehmer, einen Subunternehmer für die Systemintegration, dem leider wirklich ein grober Fehler unterlaufen ist, und wir erkannten erst vor kurzem, welche Auswirkungen dieser Fehler zur Folge hatte“, fügte er hinzu.
Danke, Elon, für diese Einführung. Wie in den letzten fünf Jahren haben wir mehrere relevante Punkte aus der Elektrifizierung des Automobilmarktes verstanden:
- Zudem sind die Entwicklung und die Leistung von Batteriezellen zentral für die Entwicklung mobiler Geräte. Leistung, Energiedichte, Sicherheit, Alterungsprozess, Kosten – Jede Auswahl eines Zelldesigns kann Ihre Position auf einem dynamischen Markt beeinflussen.
- Die Lösung einer technischen Schwierigkeit ist kein Problem (als Konstrukteure lieben wir es, Probleme zu lösen, seien wir ehrlich). Bevorstehende Schwierigkeit nicht zu erkennen, ist das Problem. Die Verwendung einer leistungsfähigen Modellierungsgebühr ist jedoch zwingend erforderlich, um Ihre Entscheidungen zu treffen.
- Selbst wenn Sie die Zellenkonstruktion beherrschen, müssen die Systemintegration und die Produktion mit der gleichen Bedeutung betrachtet werden.
Das bedeutet, dass die Teams der Batteriezellenentwickler die Auswirkungen ihrer technischen Entscheidungen mithilfe einer umfangreichen CAE-Simulation vorziehen müssen.
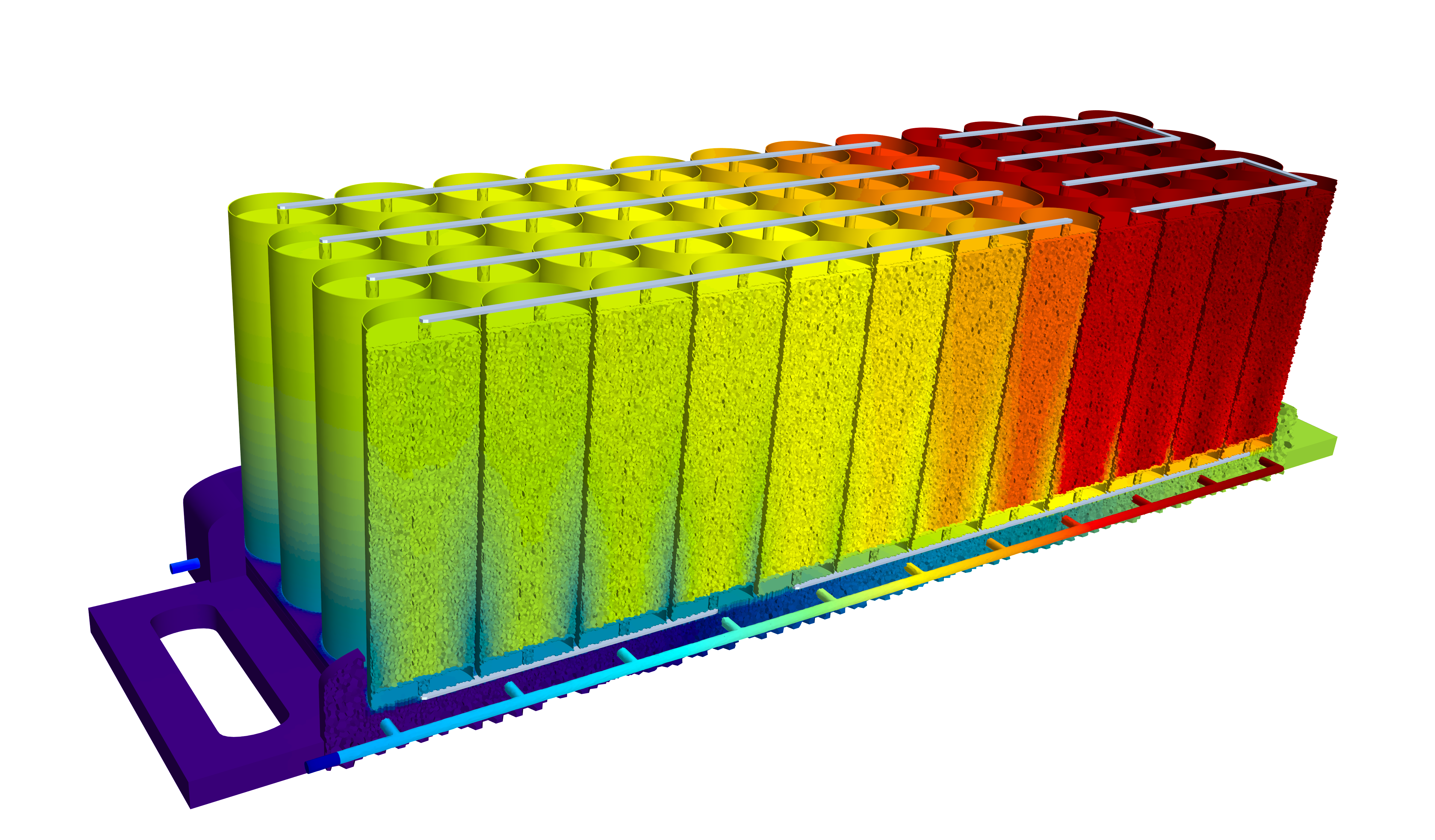
Simcenter Battery Design Studio unterstützt Konstrukteure bei der digitalen Validierung der Konstruktion von Lithium-Ionen-Zellen dank Details, geometrischen Zellspezifikationen und Zellleistungssimulationen. Umfangreiche Komponenten einer Batteriezelle stehen zur Verfügung, ebenso wie eine Materialdatenbank, die den Anwender bei der Modellentwicklung unterstützt.
Vorteile und Features auf einen Blick:
- Beschreibung der physikalischen Zelle: nahtlose GUI mit parametrierbaren Vorlagen verfügbar
- Integrale Kopplung von Zellenkonstruktion und -modell: Simulieren Sie die Auswirkungen von Konstruktionsänderungen auf die Zellenleistung
- Multi-Physics-Software-Anbindung: Modellexport nach Simcenter STAR-CCM+ über TBM-Datei
- Design-Exploration: Automatisches Optimieren von Konstruktion und Leistung der Batteriezellen
- Simulation auf Systemebene: Export von Zellmodellmerkmalen nach Simcenter Amesim
Beschreibung der physikalischen Zelle
Der erste Schritt in Simcenter Battery Design Studio besteht darin, die Geometrie und die Eigenschaften der Zellkomponenten zu spezifizieren. Abhängig von den Verantwortlichkeiten Ihres Teams sind diese entweder zugänglich, werden entweder vom Zelllieferanten bereitgestellt oder sogar über Komponenten-Reverse Engineering bezogen.
Simcenter Battery Design Studio bietet standardisierte Spezifikationen für Lithium-Ionen-Batteriekomponenten. Der Anwender kann Zellformen aus einem Beutel, zylindrisch oder prismatisch auswählen und dann einzelne Komponenten wie Elektroden, Laschen, Stromabnehmerdesigns usw. auswählen. Jede Komponente kann mit Merkmalen wie der Mittellaschenkonstruktion für die Elektrode oder der Steuerung des Materials und der Dicke der Stromabnehmer feiner definiert werden, und die Liste geht weiter, um die Zelle vollständig aufzubauen.
Mischungsformulierungen sind in der Regel zwar bekannt, genaue Werte basieren zu Beginn jedoch oft auf Vermutungen. Ausgehend von den Gleichgewichtsspannungskurven des aktiven Materials, die in der Literatur oder bei der experimentellen Charakterisierung verfügbar sind, kann der Anwender das Gemisch jedoch so anpassen, dass es eine gute Anpassung an die Niederstromentladungskurve erhält und so eine sehr genaue Kapazitätskorrelation erhält. Der berechnete „Build Report“ kann auch sehr hilfreich sein, um Ihre Eingaben zu validieren, indem Sie beispielsweise die endgültige Energiedichte oder das Gewicht der Zelle überprüfen.
Der Anwender kann auch automatisch eine grafische Ausgabe des Gelroller-Abschnitts generieren, um zu überprüfen, ob die Elektrodenwicklung wie erwartet ist.
Simulation der Zellenleistung
Simcenter Battery Design Studio bietet mehrere Ebenen von Leistungsmodellen: ein physikbasiertes, makrohomogenes Modell, um Einblicke in die elektrochemischen Mechanismen der Zelle zu erhalten, wie z. B. den Spannungsverlustmechanismus während des Arbeitszyklus einer Zelle, oder um die Konzentration oder Wärmeerzeugungsverteilung über die Elektrode zu verstehen; und ein äquivalentes RCR-Schaltungsmodell, bei dem es sich um einen empirischen Ansatz zur Modellierung des Verhaltens der Zelle auf sehr rechenintensive Weise handelt.
Die Simulation kann uns auch sagen, was in der Zelle in Bezug auf die Verteilung des Potentials und die Stromdichte passiert, die sich in der Nähe der Laschen über die Elektrode konzentriert.
Verteilung der Zellstromdichte für eine 10A-Entladung
Wenn Sie mich oder meinen Hintergrund als Siemens Engineering Services-Team kennen oder wenn Sie meinen vorherigen Beitrag über die Simcenter SPEED-Software gelesen haben, kennen Sie meine nächste Frage. Was ist das tatsächlich erwartete Ergebnis eines solchen modellbasierten System-Engineering-Ansatzes? Antwort: Verstehen Sie die Auswirkungen von Konstruktionsentscheidungen auf Ihre Systemleistung während Ihres Entwicklungszyklus und stellen Sie diese vor. Ihre Tools sollten Sie dabei unterstützen, die optimale machbare Wahl zu treffen.
Schauen Sie sich als Beispiel dieses On-Demand-Webinar über Silizium-Graphit-Zellen an, in dem die Firma Saft zeigt, wie sie das Simcenter Battery Design Studio verwenden, um eine Zelle mit Hochenergieanode zu entwerfen.
Nicht nur Ihr System. Die Wechselwirkung zwischen parallelen/seriellen Zellmodulen und umgebenden Elementen, die Teil des Batteriepakets sind, muss ebenfalls berücksichtigt werden.
Nahtlose Verknüpfung mit Multi-Physics-Software
Zu diesem Zweck empfehlen wir unseren Kunden in der Regel, Simcenter Battery Design Studio zu verwenden, um ein empirisches RCR-Modell zu erstellen, das das Verhalten der Zellspannung darstellt und dann für die elektrothermische 3D-Simulation des Akkus vorgesehen ist. Ein physikbasiertes Modell kann verwendet werden, aber ein empirisches RCR-Modell verbessert die Rechenkosten, indem es eine gewisse Genauigkeit in Ihren Ergebnissen beibehält und besser für Laien geeignet ist, die auf Batteriemodulebene arbeiten. Daher werden HPPC-Tests (Entlade- und Regenerationsimpulse zur Charakterisierung des Widerstands, der vom SOC, der Temperatur und dem Strom der Zelle abhängt), entweder synthetisch oder aus Messungen, als Eingangsdaten verwendet, und Simcenter Battery Design Studio generiert automatisch die empirischen RCR-3D-Modellparameter, die für das 3D-Verhaltensmodell des Batteriepakets innerhalb von Simcenter STAR-CCM+ auf sehr recheneffiziente Weise verwendet werden.
Die Verknüpfung zwischen den beiden oben genannten Simcenter Portfolio-Softwares erfolgt über eine Ausgabedatei des Simcenter Battery Design Studio, die Text Battery Model (TBM)-Datei. Die TBM-Datei wird vom Add-on Battery Simulation Module für Simcenter STAR-CCM+ verwendet, um das gewünschte 3D-Modell des Batteriemoduls zu erstellen. Durch die Kopplung der Geometrie, des Zellleistungsmodells und des thermischen Solvers von Simcenter STAR-CCM+ können Batteriemodulingenieure eine elektrothermische Simulation des gesamten Batteriepakets über transiente Szenarien durchführen.
Der Anwender kann weitere Komponenten des Batteriepakets hinzufügen, wie z. B. die Stromschienen, das elektrische Isolierpad, die Kühlkanäle und das Batteriegehäuse (mit STAR-CCM+ 3D-CAD oder einer CAD-Software von Drittanbietern) und eine automatische Vernetzung durchführen sowie Material-/Kühlmitteleigenschaften festlegen.
Der letzte Schritt besteht darin, eine transiente Simulation über ein Tastverhältnis oder eine beliebige Funktion des transienten Erregungsprofils des elektrischen Stroms des Anwendungsbereichs durchzuführen. Nachfolgend finden Sie ein Beispiel für die Temperaturverteilung eines Batteriemoduls über einen US06-Zyklus bei einer Umgebungstemperatur von 25 °C und einer konstanten Kühlpumpendrehzahl.
Beispiel für ein 4P12S-Modul mit 18650 Zellen, das auf einer Aluminium-Flüssigkeitskühlplatte positioniert ist (hier nicht dargestellt). Die Ergebnisse zeigen einen großen Temperaturgradienten über das Modul, der darauf zurückzuführen ist, dass das Kühlsystem nicht in der Lage ist, eine harmonisierte Temperaturverteilung aufrechtzuerhalten
Ziel ist es, die integrierte Konstruktion zu validieren und mögliche Defekte, unerwünschtes Steuerungsverhalten oder Sicherheitsprobleme frühzeitig im Entwicklungszyklus zu erkennen, indem dieser sozusagen „digitale Multiphysik-Zwilling“ des Batteriemoduls verwendet wird, ohne Zeit während der Hardwarephase zu verlieren, wenn Probleme zu spät im Prozess entdeckt werden könnten.
Automatisierte Design-Space-Exploration und Optimierung
Ausgehend von diesen Simulationsergebnissen können Konstrukteure Design-Space-Exploration-Studien auf Zellenebene beginnen, um die Kapazität zu maximieren, indem sie z. B. eine feste Konstruktion des Batteriepakets in Betracht ziehen, aber an der Zellenchemie arbeiten, oder auf der Ebene des Batteriemoduls, indem sie an dessen Geometrie und Eigenschaften arbeiten. Diese Design Space Exploration-Studien können sowohl mit dem Design Manager als Teil von Simcenter STAR-CCM+ als auch mit der HEEDS-Software als Teil des Simcenter Portfolios durchgeführt werden. Das nenne ich die Magie des digitalen Zwillings. Simulationsingenieure können halbautomatisch, effizient und sicher Hunderte von Entwürfen untersuchen und versuchen, die Leistung mehrerer Attribute auszugleichen und Systembeschränkungen zu berücksichtigen.
Man kann schnell erkennen, dass die thermische Leistung des Batteriepakets verbessert werden kann, da die Temperatur nicht gut über das Batteriemodul verteilt ist, sicherlich aufgrund einer ineffizienten Kühlmittelströmungsverteilung, die sich mit Sicherheit auf die elektrische Leistung von überhitzten Zellen auswirkt und sogar die Lebensdauer oder Sicherheit der Zellen beeinträchtigen kann.
Im Folgenden finden Sie ein Studienbeispiel, in dem wir unsere Eingaben für die Design-Exploration, Variablen wie Kanaldurchmesser, Kanalnummer und Strategie für die Kühlmitteldurchflussrate eingerichtet haben. Für die Ziele der Design-Exploration wurden ein Zelltemperaturunterschied in Jellyrolls von weniger als 2 °C und eine Reduzierung des Druckabfalls festgelegt. Unten sehen Sie die Studienergebnisse, die eine verbesserte Temperaturhomogenität über das Modul zeigen.
Vergleichende Temperaturhomogenität ergibt sich zwischen Basisgehäuse und verbesserter Konstruktion über den Fahrzyklus US06
Anwenderbericht: Samsung R&D Institute
Ein konkretes Beispiel ist eine Arbeit des Samsung R&D Institute über die Verwendung von Simcenter Battery Design Studio in Kombination mit Simcenter STAR-CCM+, um die Auswirkungen von Konstruktionsentscheidungen auf die Leistung von Batteriepaketen zu untersuchen.
Wie andere Hersteller von Lithium-Ionen-Batterien ist auch das Samsung R&D Institute immer auf der Suche nach Werkzeugen, die sie bei der Herstellung von Batterien mit höherer Energiedichte und Haltbarkeit unterstützen. Zu diesem Zweck konzentrierten sie sich auf die Optimierung der Wärmemanagementsysteme dank eines gekoppelten elektrothermischen 3D-Modells des Batteriepakets.
Parameter des empirischen Modells nach Simcenter Amesim exportieren
Das empirische Modell von Simcenter Battery Design Studio RCR eröffnet die Möglichkeit, die notwendigen Parameter zu extrahieren, um ein Batteriemodell auf Systemebene einzurichten, das in der Simcenter Amesim-Software verwendet werden kann, und so das Batteriepaket als integrierte Komponente betrachtet, die Teil eines „größeren“ Systems ist: ein elektrisches Radfahrzeug, ein Flugzeug, ein Kraftwerk oder sogar ein Smart Grid für ein Haus.
In Simcenter Amesim haben Anwender Zugriff auf ein Tool zur Vordimensionierung von Batterien, das automatisch die Funktion Ihres Batteriepakets für die Zelleneigenschaften (z. B. aus Simcenter Battery Design Studio) und die technischen Anforderungen konfiguriert, was in diesem Video gezeigt wird.
Das generierte Batteriepaket kann dann im endgültigen System verwendet werden, einschließlich anderer Multiphysik-Komponenten wie elektrischer Antriebsstrang, des Wärmemanagementsystems, des elektrischen Bordnetzes usw. und deren Steuerungen. Ziel ist es, die Zellen-/Batterieleistung auf Systemebene vorherzusagen und zukünftige Wechselwirkungen zwischen der Batterie und ihrer Umgebung vorzuziehen. Sehr nützlicher Simulationsprozess zur Verbesserung der Zusammenarbeit zwischen Zellen-/Batterielieferanten und OEMs, die die Interaktion zwischen ihren Produkten einfach modellieren, simulieren und validieren können.