Adapt and scale faster when you centralize and streamline recipe management
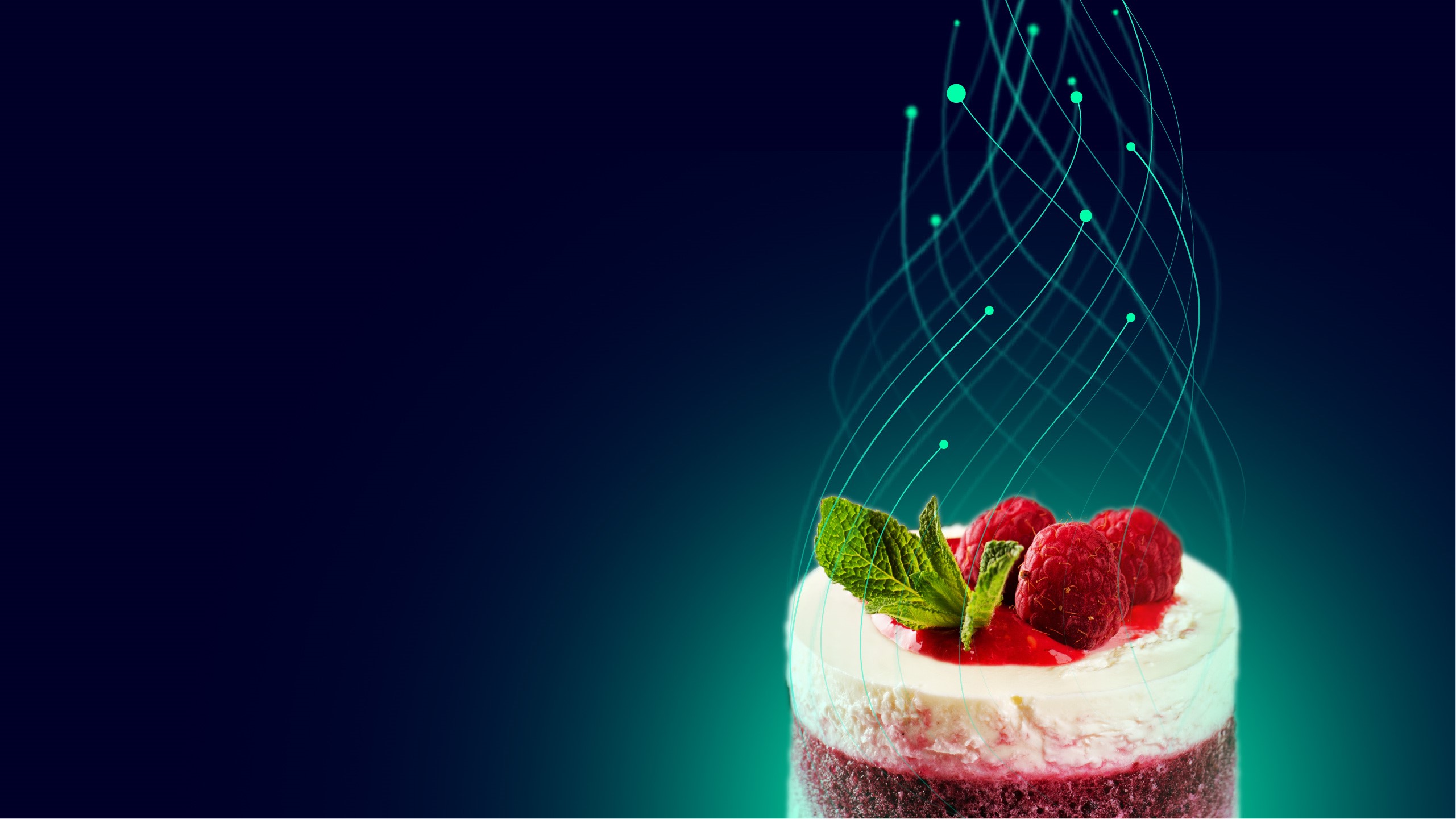
Equipment usage, ingredient availability, local regulations and brand quality are some of the factors that make the scaling a recipe for production or changing manufacturing locations complex. It can take months to accomplish, if it’s even possible at all.
While digitalization is the key to managing this complexity, it’s also important to centralize all recipe authoring knowledge and product information currently spread across the company in a digital platform. With this recipe authoring knowledge available from a central point, you’ll be able to effectively manage:
- Product formulations
- Bill of ingredients
- Recipe lifecycles and procedures
- Production asset capabilities worldwide
The challenge of manufacturing anywhere
Is your enterprise recipe management system providing the flexibility and adaptability needed to meet a change in demand, a climate-related crisis or an update to your recipes? This question is crucial for today’s manufacturers facing global challenges.
Sometimes the ability to manufacture anywhere is more than just bringing your products closer to the market – it’s a necessity or a reaction to an evolving situation. When you streamline your enterprise recipe management processes, you can enhance efficiency, quality and adaptability so that the ability to ‘manufacture anywhere’ is truly available when you need it.
Siemens’ solution for recipe management
With Centralize Recipe Authoring Knowledge, part of Siemens’ Enterprise Recipe Management software solutions, you can accelerate your processes by virtually validating recipes, optimizing formulation development, improving batch control and ensuring flexible, high-quality production across your global facilities.
Our solution is designed to integrate seamlessly with our broader portfolio, including Product Lifecycle Management (PLM), Manufacturing Execution Systems (MES), and automation technologies. This interconnected ecosystem allows you to maintain a single source of truth for recipes throughout the entire product lifecycle, from initial formulation development through production execution.
The system intelligently accounts for equipment variations between manufacturing sites, automatically adjusting recipes based on specific equipment capabilities while maintaining final product consistency. This helps reduce waste and improve first-time-right production rates.
Advanced capabilities for technical teams
For technical teams, our solution offers advanced capabilities including:
- Virtual recipe simulation to validate manufacturability without costly physical trials
- Intelligent scale-up algorithms that automatically adjust recipes based on equipment capabilities
- ISA-88 compliant batch control that ensures consistent execution of master recipes
- Real-time production data integration for continuous recipe optimization
- Ingredient substitution management to accommodate regional availability challenges
- Formula versioning and comprehensive change management with full audit trails
Our intuitive user interface ensures operators can easily access the information they need on the shop floor, while robust role-based security controls ensure proper access management. The system supports both on-premises and cloud deployment options to fit your IT infrastructure requirements.
Real results: customer success spotlight
To see these benefits in practice, consider the experience of Yanghe Distillery, a leading global spirits producer that implemented Siemens’ Opcenter solutions including APS, MES, and LIMS as part of their digital transformation initiative.
By centralizing production planning, execution, and quality data, Yanghe achieved remarkable results: reduced changeover times, automated scheduling, real-time KPI reporting, detailed cost accounting, and comprehensive quality traceability. These improvements dramatically enhanced their manufacturing flexibility and efficiency.
You can read the full Yanghe Distillery case study here.
The power of centralized recipe management
The best way to ensure consistency and quality across all production batches is to centralize and streamline your recipe management. You can improve efficiency and reduce errors by taking a unified approach to managing formulations and ingredient lists.
Centralized Recipe Authoring Knowledge solutions enhances data accuracy and accessibility so that stakeholders in recipe development and production can make better decisions faster and accelerate response times when changes must be made quickly.
Key benefits of Siemens’ solution
The benefits to Siemens’ Centralize Recipe Authoring Knowledge solution include:
- Unified recipe management which centralizes all recipe data to foster consistent and high-quality production
- Error reduction because, let’s face it, no one likes to make errors. This centralized recipe solution will minimize manual errors with a standardized approach to formulation management
- Realize improved efficiency when you streamline processes that enhance productivity and reduce downtime
Improving production through enterprise recipe management
When it comes to consumer expectation regarding food and beverage quality, it’s critical to remain consistent. Unless it’s for a specific reason, the taste of one product should be uniform regardless of where it’s manufactured.
As the food and beverage industry faces increasing challenges from supply chain disruptions, sustainability requirements, and shifting consumer preferences, centralizing recipe knowledge becomes even more critical. Companies that can quickly adapt formulations to accommodate alternative ingredients, meet regional regulatory requirements, or scale production across different facilities will gain a significant competitive advantage.
Enterprise Recipe Management software improves production by centralizing recipe data and ensuring consistency across all production batches. It streamlines formulation development and enhances batch control, leading to reduced errors, increased efficiency and consistent quality. Additionally, real-time data collection and analysis enable proactive decision-making and optimization of manufacturing processes.
Maintaining Central Recipe Authoring Knowledge and ensuring information and data are available to those who need it, when they need it, will allow food and beverage companies to scale faster and adapt to market changes. This approach provides the means to manufacture anywhere while maintaining high standards and efficiency across all production sites.
Explore more insights—visit our resource page today.