The value of manufacturing process validation: thinking both process design and product design
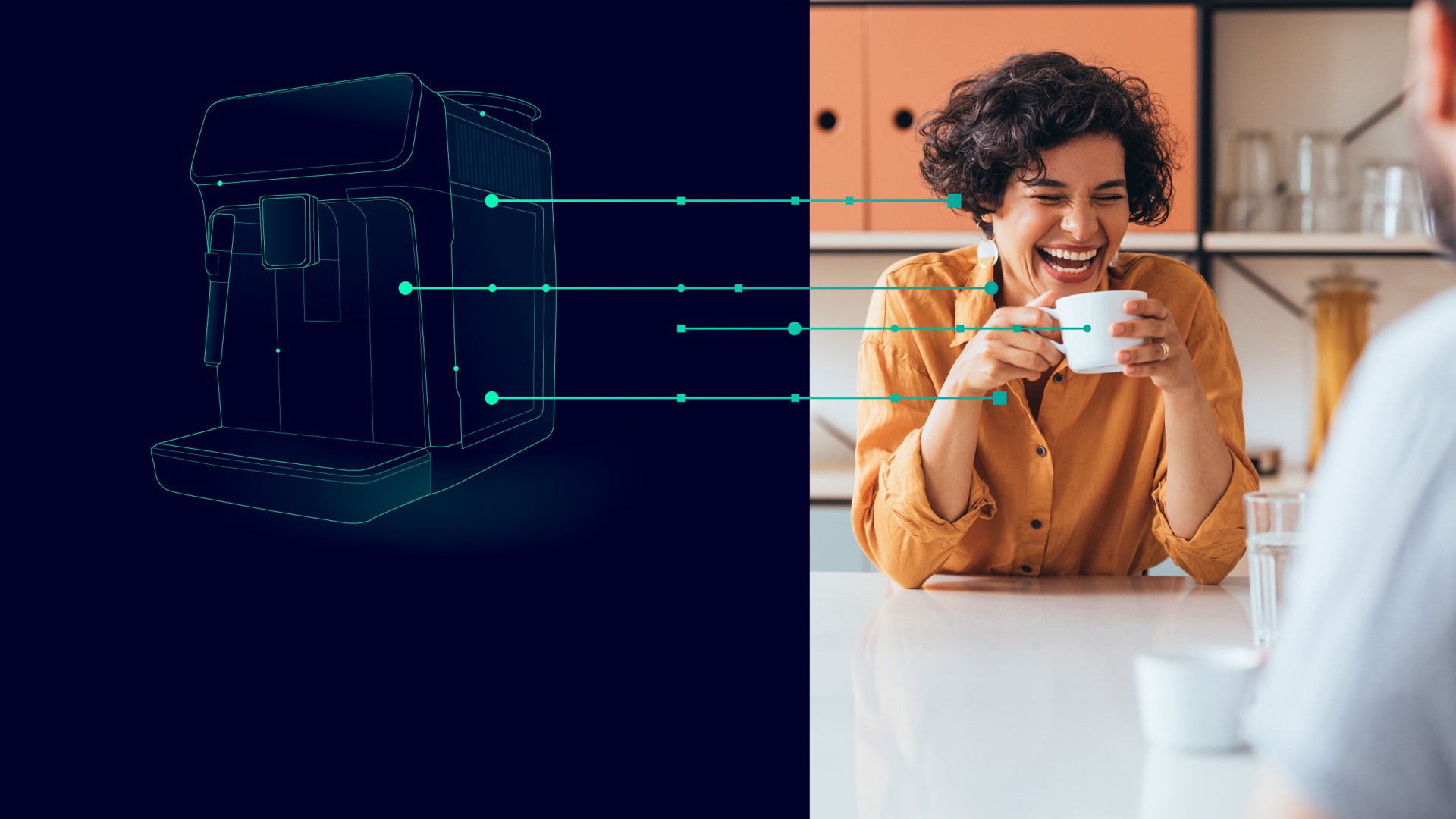
Today’s Consumer Products & Retail companies are struggling to keep up with current disconnected and manual development, validation, and optimization processes at their manufacturing locations around the world. Many companies have invested in digital tools to support individual department operations, however, this manual and siloed approach to product and process design leads to difficulty in achieving the digital thread required for a flawless new product launch.
- 75,000 new consumer goods products are developed every year
- Only 40 percent (or 30,000 products) will make it to market
- 95 percent of new product launches fail
How can you out-innovate your competitors and provide people with the consumer product goods they want?
Early manufacturing process validation to accelerate production launch
What if you could validate that your products can be produced, tested and packaged virtually to eliminate the time spent in physical prototypes?
In today’s competitive marketplace, your customers demand more product variety, sustainability and want to be able to influence the innovation process. To bring new, innovative products to market faster and more efficiently it’s critical to validate that the products can be manufactured during the development phase. With the ability to eliminate physical testing, you’ll have the possibility to execute hundreds of iterations faster to find the optimal product and process design for quality, cost and manufacturability.
This approach will help your teams focus on meeting customer demands faster than your competition or take advantage of new trends.
Imagine executing 200 iterations compared to 5 or 10
Manufacturing process validation can help you optimize your product and process design for quality, cost and manufacturability.
How can early verification enhance product manufacturability?
- Use simulation to validate if your products can be integrated, assembled and packaged virtually
- Reduce the number of physical tests required to verify consumer product design and process feasibility
- Execute hundreds of simulation iterations instead of dozens at a faster speed to help optimize your process design
- Validation of manufacturability and optimization of assembling operations including human ergonomics and packaging processes using simulation of plant-specific equipment
How a company conducts their consumer product design and how it is manufactured is at the heart of the consumer experience and is the foundation for delivering on a company’s promise to consumers. These solutions allow you to meet the demand and create new personalized and sustainable products faster, anywhere, all the time.
Validating and simulating machines, lines and production systems virtually increases product design efficiency and has proven to that companies can benefit greatly when they try and simulate several options, refine and perfect the process.
- Reduction of machine validation time from 24 weeks to 3 weeks
- Time saving ratio to build line of 10:1
- Automation has provided more output with fewer stops and less energy
Electrolux: Manufacturing process validation for 60 million products
Based in Stockholm, Sweden, Electrolux produces 60 million products per year for customers in 150 countries at 53 different production sites worldwide. Having the ability to simulate and streamline their global production process and validate their manufacturing process ensures they have the capability and capacity to produce anywhere. With Siemens software, Electrolux can run production virtually and solve problems before committing to the real production lines.
Electrolux is standardizing safe, modular operations. They are now getting to market 20-30 percent faster and saving 15-20 percent in costs.
Simulation and test solutions to predict performance across all critical attributes
By combining physics-based simulations with insights gained from data analytics, you can optimize consumer product design and process design in these primary application areas:
- Structures and mechanisms
- Vibration and acoustics
- Electro-magnetics
- Flow, thermal, particles and chemistry
- Energy management
- Systems modeling and controls
- Design exploration/balancing
When you can combine system simulation, 3D CAE and test, you’ll be able to predict performance earlier and throughout the entire product and process lifecycle so that you can get your new product reliably to market.
Real-time feedback through manufacturing process planning
How can you reduce costs and risk of issues in the factory to compete in global markets, while delivering more innovation in less time? With Siemens assembly planning and validation solutions, you get real-time feedback during manufacturing planning so that decisions can be made with smarter, more reliable and validated data.
Key features to the manufacturing process planning solution:
- A comprehensive digital thread that contextualizes product design and assembly information including 3D visuals of your product and factory
- Tools to simulate and virtually assess the feasibility of your decisions while developing your process plans
- Plan, optimize and validate manufacturing processes before the start of production
- Use of a broad range of tools to streamline process planning workflows, automate nonvalue-added planning tasks, integrate electronics and mechanical assembly, and validate the best plans for making products.
These features can benefit your manufacturing process and give you greater freedom to innovate because it allows you to:
- Share insights easier with key stakeholders across functional domains
- Ramp-up to production faster
- Continuously improve your business
- Achieve today’s and tomorrow’s manufacturing goals
Control the product and production lifecycle from process planning and detailed engineering to full production by connecting the entire manufacturing value chain and helping you build the best production strategy.
3 steps to manufacturing process validation
- Integrated BOM management and validation. Product modularization is the foundation of creating a new family of products.
- Integrated product validation. Virtual verification and validation of system and subsystems can determine that the product is behaving as described while the engineering of the different modules and integration points get validated and optimized
- Manufacturing planning. A significant effort to optimize the production time of a variation of products can be achieved and planned after product design and manufacturing validation are connected and synchronized
What’s the connection between customer loyalty and manufacturing?
It’s time.
Consumer demands for smart, connected and personalized products have made the speed of product and process development extremely important even as complexity continues to explode.
Failure to produce quickly means your customer might seek a similar product from a different company. Manufacturing process validation can enhance manufacturing capabilities and ensure that the most optimal processes are in place when it’s time to produce the product.
With manufacturing process validation solutions, you have the ability to optimize your product and process design for quality, performance, cost, safety and manufacturability. And with that, you can cut the time it takes to bring your products to market.
Want to reduce production risks and accelerate product launches?
Discover how leading manufacturers simulate, test, and optimize their production processes—before committing to real-world production.