Harnessing predictive maintenance to transform your plant’s operations
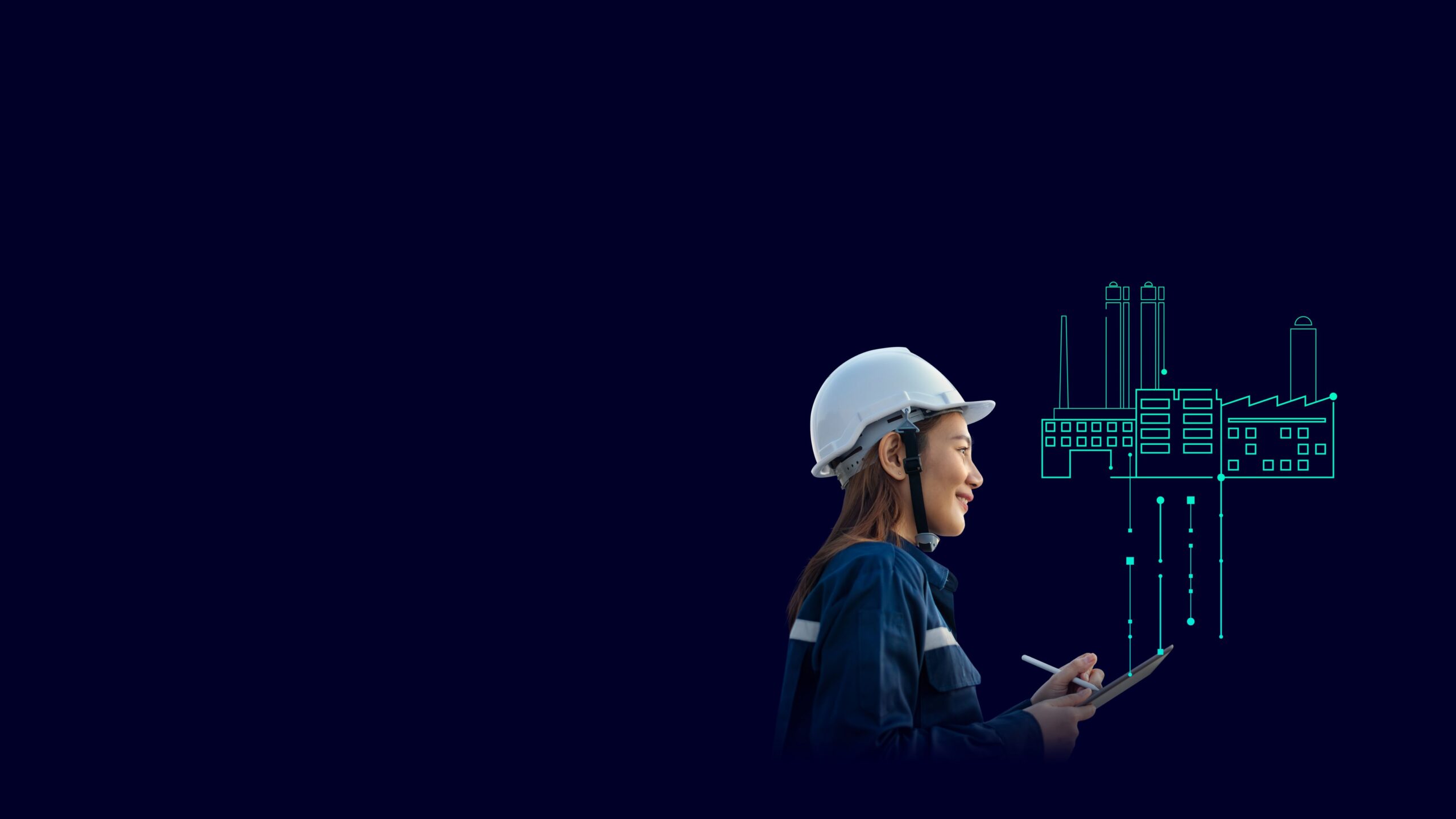
Managing critical assets in industries such as food and beverage, energy, and infrastructure is no small task. Unplanned downtime, equipment failures, and maintenance challenges can lead to costly delays and inefficiencies. To tackle these challenges, businesses are increasingly turning to AI-based condition monitoring to gain real-time insights and predictive capabilities that go beyond traditional approaches. In this blog, we’ll explore how AI is revolutionizing condition monitoring, dive into real-world applications, and showcase advanced tools like SITRANS SCM IQ and Senseye that are helping companies stay ahead of potential issues.
How AI-Based condition monitoring works
In traditional condition monitoring systems, fixed Key Performance Indicators (KPIs) are set to trigger alarms when thresholds are crossed. While effective in many scenarios, KPI-based monitoring comes with significant limitations:
- Deep Expertise Required: Operators need an in-depth understanding of every asset to set accurate KPIs.
- Static Thresholds: KPIs don’t account for varying operational states, leading to potential inaccuracies.
- Inaccuracy: Static thresholds often result in false alarms or missed issues when assets operate under different conditions.
AI-based condition monitoring is changing this landscape. By employing machine learning algorithms to analyze raw vibration data, AI allows for the continuous learning of asset behavior. This dynamic approach leads to more accurate insights and anomaly detection, enabling operators to respond proactively instead of reactively.
Learn more about how AI is transforming condition monitoring in this short clip:
Revolutionizing condition monitoring with SITRANS SCM IQ
AI-driven condition monitoring is a significant advancement, but to harness its full potential, you need robust tools that can seamlessly integrate into your existing systems. SITRANS SCM IQ is designed to provide end-to-end condition monitoring, offering real-time insights that help operators detect potential issues early.
Here’s a breakdown of the key components of SCM IQ:
- Sensors: Small, rugged, wireless vibration and temperature sensors (MS 200) transmit data via Bluetooth to the gateway.
- Gateway: The SITRANS CC 220 gateway connects up to 12 sensors and transmits data to the Siemens cloud.
- Cloud Platform: Siemens Insights Hub analyzes data and provides actionable insights to improve asset management.
One of the standout features of SCM IQ is its ease of use. Plant operators don’t need specialized IT or vibration knowledge to set up and monitor the system. With intuitive commissioning and real-time data integration, this tool provides dynamic monitoring that adapts to the operational states of each asset.
Explore how SCM IQ makes condition monitoring more accessible and effective:
Real-world impact: Minimizing downtime and reducing costs
The benefits of predictive maintenance aren’t just theoretical—they translate into real-world savings. For instance, at a beverage bottling plant, the implementation of SITRANS SCM IQ saved over €5,000 by preventing just one incident of unplanned downtime. By identifying potential failures early, businesses can schedule maintenance before an issue escalates, avoiding both costly repairs and lost productivity.
See how predictive maintenance saved time and costs in this real-world application:
The role of Senseye in automated predictive maintenance
In addition to SCM IQ, Senseye offers another layer of predictive maintenance capabilities. As an automated asset intelligence tool, Senseye uses AI to monitor critical assets such as motors, pumps, fans, and conveyors across a wide range of industries. By learning the normal behavior of assets and identifying trends and anomalies, Senseye helps companies perform maintenance only when necessary—saving both time and resources.
The strength of Senseye lies in its ability to provide actionable insights without requiring data scientists or extensive technical knowledge. With real-time monitoring and early detection, Senseye reduces unplanned downtime, enabling operators to focus on critical tasks while the AI system handles asset analysis.
Watch how Senseye automates asset maintenance for efficiency and uptime:
A future-ready approach to maintenance
AI-based condition monitoring and predictive maintenance are paving the way for more efficient and sustainable operations in capital asset-intensive industries. Whether it’s avoiding unplanned downtime, optimizing maintenance schedules, or integrating condition monitoring into existing ecosystems, tools like SITRANS SCM IQ and Senseye are helping businesses make smarter decisions.
Both solutions are scalable and adaptable, capable of integrating with Siemens’ platforms and third-party systems for a comprehensive approach to asset management. With these tools, companies can leverage the power of data to enhance operational efficiency and reduce costs.
Ready to Take the Next Step?
The adoption of AI-based condition monitoring is no longer optional—it’s becoming a critical strategy for companies looking to stay competitive in fast-moving industries. By leveraging advanced solutions like SITRANS SCM IQ and Senseye, you can unlock predictive insights, optimize your maintenance processes, and reduce the risks of unplanned downtime.
Curious to learn more? Watch our on-demand webinar to see these solutions in action and explore how they can benefit your operations.