Sustainable manufacturing: Redefining flexibility in Consumer Packaged Goods
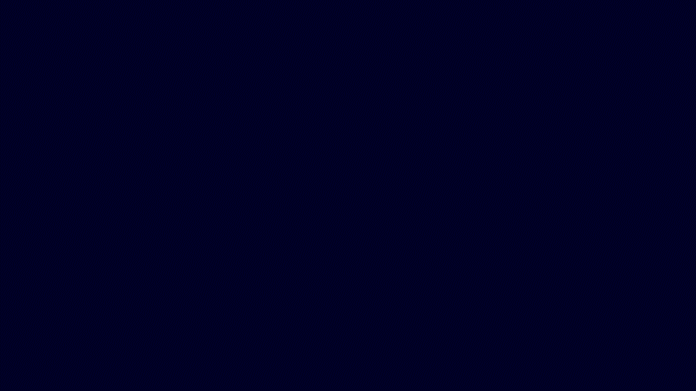
Sustainable manufacturing has moved far beyond just being a buzzword—it’s fundamentally changing how we approach manufacturing in the Consumer Packaged Goods (CPG) industry. I’ve watched as companies have not only adopted eco-friendly practices but have also begun rethinking their overall set of production processes. This shift towards sustainability is paving the way for greater flexibility within manufacturing plants, and to move to a model where many different products can be manufactured in many different plants. This facilitates a model where products are manufactured geographically closer to the actual demand.
Sustainable manufacturing as the catalyst for change
Over the past few years, sustainable manufacturing has moved from being a nice-to-have to a must-have. Consumers are making purchasing decisions based on a brand’s environmental impact, forcing brands to adapt. However, sustainable manufacturing isn’t just about reducing waste or energy use; it’s about creating a manufacturing environment that is agile, responsive, and ready for the future. I’ve seen firsthand how smart manufacturing, through the integration of automation and digitalization, empowers brand manufacturers to quickly adjust their operations, reducing their environmental impact while maintaining efficiency. This kind of adaptability is no longer a luxury—it’s essential for thriving in today’s dynamic market.
As manufacturers strive to meet these new sustainability benchmarks, they’re discovering that flexible manufacturing isn’t just beneficial—it’s necessary.
Introducing flexibility in manufacturing
Traditionally, manufacturing lines were designed for efficiency—producing large volumes of a single product with minimal variation. But today, that model is being challenged. In response to the growing demands for personalization and sustainability, manufacturers are rethinking their operations to be more flexible. Smart manufacturing shines here, using technologies like automated guided vehicles (AGVs) with vessels that transport ingredients directly to various production lines as needed. I’ve seen how these AGVs enable real-time reconfiguration of production lines, making it possible to switch between different products or variants without lengthy setup times or significant downtime.
The ability to quickly adjust production lines is a game-changer, especially in an industry where an estimated 70% to 75% of all CO2 emissions are directly related to logistics – shipping products around the globe. Flexible manufacturing is no longer a distant goal—it’s happening in plants, leading the charge toward a more sustainable future.
However, flexibility in manufacturing involves more than just introducing AGVs—it requires a full overhaul of core manufacturing and logistics business processes that support agile, data-driven decisions.
Watch this video to see how flexible and predictable manufacturing can transform your production processes:
Digitalization and automation: the backbone of flexible manufacturing
The good news is that these business process changes can be enabled by technology – specifically by leveraging today’s automation and digitalization capabilities. By integrating advanced data analytics, IoT and AI into manufacturing processes, smart manufacturing achieves real-time visibility and control over every aspect of production. I’ve seen how automation streamlines operations while digitalization provides data-driven insights to make smarter, more informed decisions.
But to fully realize the potential of these technologies, we need to take a step further—into the realm of digital twins.
This concept extends digitalization beyond automation and data analytics, creating a virtual replica of the manufacturing environment that allows for detailed simulation and optimization. With digital twins, manufacturers can simulate and validate changes before implementation, ensuring everything runs smoothly and sustainably. This digital approach allows for precise adjustments, closer manufacturing to demand, a reduction in the overall logistics footprint, a decrease in inventory, and a reduction in out-of-stock.
But imagine if you could take these simulations even further—into a space where the virtual and physical worlds meet. That’s where the industrial metaverse comes into play.
The industrial metaverse: where the virtual meets reality
The industrial metaverse takes digitalization to the next level by creating a digital twin of the entire manufacturing environment. This is not merely animating the factory floor. We are talking about representing an entire manufacturing plant – walls, equipment, people, products and more – in a highly detailed simulation of the actual plant. In this immersive simulation, manufacturers can modify production processes on the fly, test different scenarios and validate the effectiveness of new technologies or configurations without disrupting actual operations. The industrial metaverse enables manufacturers to explore complex manufacturing scenarios involving people, processes and technologies—all in a risk-free environment.
This capability is significant for ensuring that sustainability goals are met alongside overall manufacturing objectives. By validating virtual and simulated shop floor changes, companies can make informed decisions that optimize sustainability and operational objectives before any real-world implementation.
Simulation and validation: ensuring success every step of the way
No one wants surprises on the production line, and that’s where simulation and validation come into play. Smart manufacturing uses these tools to test different scenarios, optimize resource allocation and ensure that processes meet sustainability and flexibility goals. Simulating production in a digital twin can identify and address potential issues before they impact the real world. This proactive approach ensures that when changes are made, they lead to improvements rather than disruptions while maintaining a sustainable manufacturing operation. This saves time and resources and ensures that sustainability targets are consistently met.
As we move forward, it’s clear that the future of manufacturing lies in this blend of sustainability, flexibility and smart technology.
Join the conversation and explore smart manufacturing with Siemens
How is your manufacturing process adapting to the demands for sustainability and flexibility? I’d love to hear your thoughts. If you’re curious about how Siemens can help you integrate these principles into your manufacturing and logistics operations, let’s connect. Together, we can shape the future of smart manufacturing.
To see how Siemens is helping a subsegment of consumer packaged goods – food & beverage – companies transform their operations, check out our resource page on smart manufacturing solutions for food & beverage. Discover how you can leverage these technologies to enhance sustainability and flexibility in your production processes.