Redefining agility in food & beverage manufacturing: The critical role of smart manufacturing

Agile manufacturing solutions are critical for the evolving food and beverage industry, which faces challenges like rising costs and greater demand for variety. Manufacturers find themselves at a crossroads as the industry struggles with fluctuating raw material costs and a growing consumer demand for diversity and sustainability. Adopting smart manufacturing solutions isn’t merely a technological upgrade—it’s a strategic necessity that promises resilience and flexibility in production processes.
Gain insights into how smart manufacturing is transforming the food and beverage industry, with a focus on agility and innovation. This video provides a closer look at real-world applications and the strategic benefits they offer.
The complexity challenge
In an industry that demands rapid adaptation to ever-evolving consumer preferences, food and beverage manufacturers face the difficult responsibility of managing extensive product lines with precision and efficiency. These complex operations require a high level of flexibility to successfully cater to global markets while balancing cost minimization and sustainability. Siemens’ agile manufacturing solutions are not only useful but also necessary for efficiently managing this diversity.
Reflecting on the industry, it’s evident how daunting it can be to balance these competing demands. The introduction of smart manufacturing solutions has made a significant difference, enabling companies to adapt quickly without sacrificing quality or efficiency.
Taking a stand on agile manufacturing engineering
Agile manufacturing engineering transcends traditional optimization of asset performance. It is a transformative approach that ensures scalability, maximizes utilization, and, most importantly, adapts rapidly to new market demands. This strategy allows for rapid adaptation and reduces the costs involved with commissioning and integrating new technologies into existing frameworks—a key benefit in preserving a competitive edge and operational cost efficiency.
In my professional journey, I’ve seen how transformative agile manufacturing can be. It’s not just about technology; it’s about rethinking how we approach challenges and opportunities in the industry. This mindset shift is essential for staying competitive and meeting evolving consumer demands.
Key strategies for implementation:
- Plant and line design, simulation, and optimization: Using digital twins enables precise verification of process and plant designs, ensuring optimal capital use. This method is crucial for flexibly adapting production lines to suit various product demands without sacrificing time or cost efficiency, significantly reducing risks associated with physical trials and errors.
- Automation engineering and virtual commissioning: By allowing mechanical, electrical, and automation systems to evolve simultaneously, these technologies drastically shorten the time to market. The streamlined setup process ensures that machines and production lines are flexible and tailored to meet production demands quickly and efficiently.
Insights from the field: Ferrero’s leap with the digital twins
Ferrero’s strategic adoption of digital twins to improve their production processes is a remarkable success story. By embracing these advanced simulations, Ferrero has achieved substantial reductions in time to market and enhanced their operational agility. This case demonstrates the significant cost savings and efficiency gains across their global operations, demonstrating the practical benefits of implementing smart manufacturing technologies.
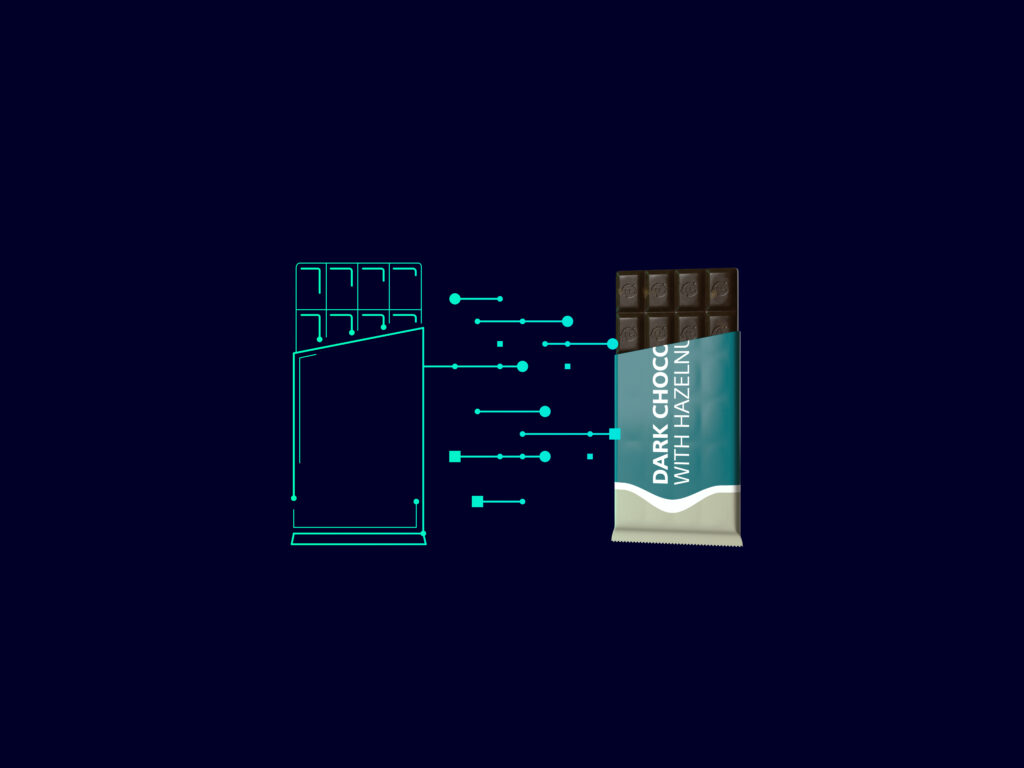
Maintaining agility and ensuring smooth operations
The ability to remain agile and responsive to new developments in production is vital. Automation standardization improves efficiency during both the development and post-sale phases, allowing new machines to be seamlessly integrated into production lines and making maintenance easier. Additionally, efficient maintenance and virtual commissioning reduce the complexity and cost of plant maintenance, which is crucial for getting production systems up and running correctly the first time and reducing errors and downtime.
In my personal experience, the emphasis on automation standardization and virtual commissioning has been a game-changer. These strategies not only streamline processes but also ensure that we are always ready to meet new production demands head-on.
Conclusion: Embracing a bold future with agile smart manufacturing solutions
Embracing agile manufacturing solutions is not just about adopting new technologies—it’s about transforming operations to become more responsive and sustainable in a competitive marketplace. Siemens is committed to leading this transformation, helping food and beverage companies meet today’s demands and anticipate tomorrow’s challenges. Looking ahead, it’s clear that companies who embrace agile manufacturing solutions today will lead the industry tomorrow and change the fundamentals of food and beverage production for generations to come.
Reflecting on the journey and the transformative impact of smart manufacturing, it’s clear that the future holds immense possibilities. By embracing these innovations, we’re not just enhancing processes—we’re shaping a more sustainable and efficient industry for future generations.