Maximize CPG ROI with a Production Digital Twin
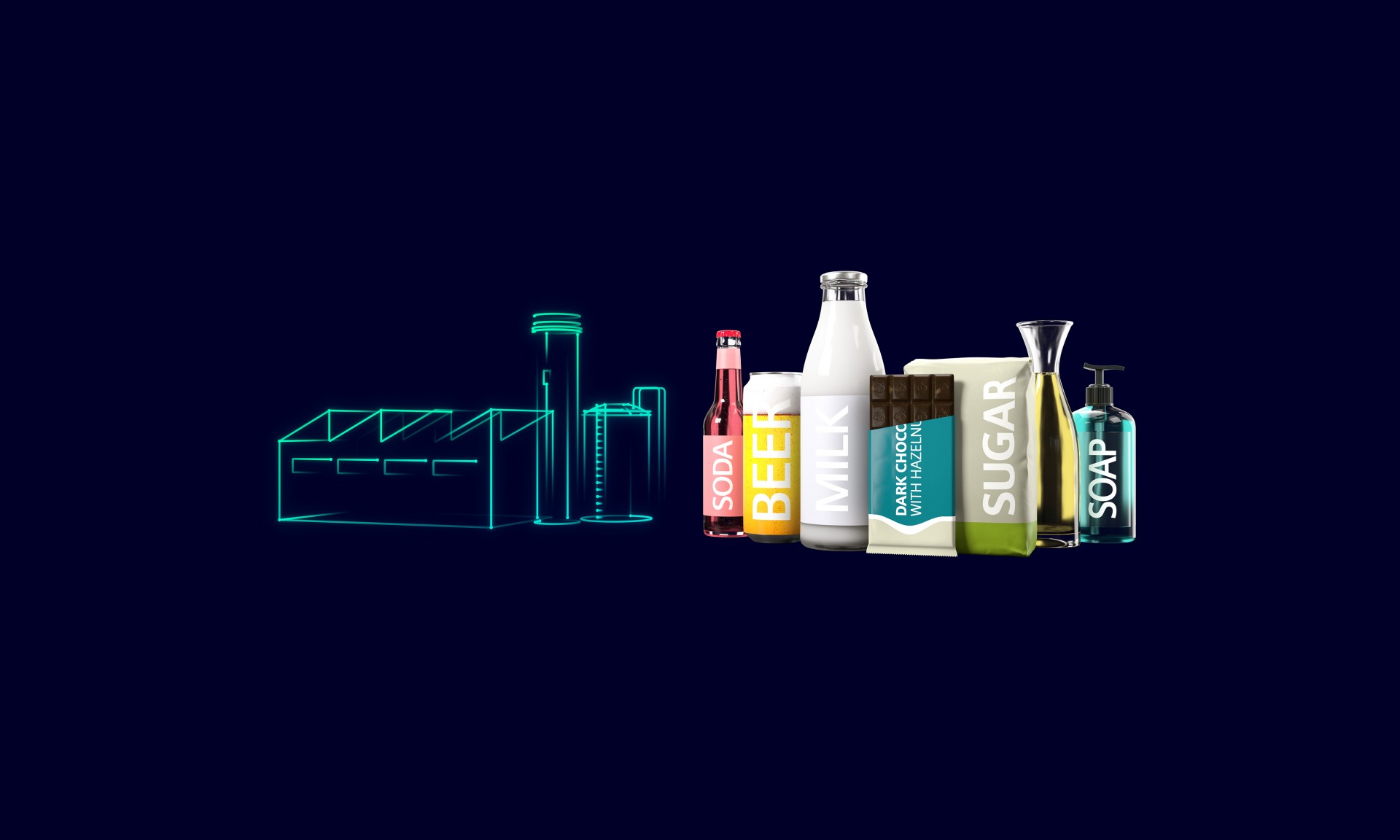
The CPG industry, like most others, is driven by speed to market, lower costs, and higher quality. In today’s competitive environment, businesses must constantly improve in order to survive. Companies must meet consumer expectations while meeting ROI requirements by designing, configuring, commissioning, and operating high-speed, flexible production lines as effectively as possible. The increasing complexity of products and required product lines is driving the CPG industry’s digitalization trend.
Leading companies have recently invested in digital transformation, a new, high-potential approach to business improvement, in addition to traditional continuous improvement initiatives. To overcome these obstacles, digitalization is required, with the digital twin playing an important role.
Digitalization is key
Digital transformation is the process of digitizing processes and data in order to achieve dramatic rather than incremental improvements in business performance. Documents are typically used to manage information, which is represented as a collection of discrete data elements linked by workflows from concept to end of life. Workflows are digital representations of processes that aid in the creation, management, and distribution of appropriate information to the appropriate people at the appropriate time. This includes the product as well as its packaging and manufacturing processes, which can range from individual pieces of equipment, workcells, and production lines to entire factories and factory networks.
What is a digital twin, and why does it matter?
As products become more complex and buyer habits evolve, you’ve probably heard or read the term “digital twin.” The term has gained traction in technological and manufacturing discussions, with many companies touting the benefits of their “digital twin” offering. Each of these digital twin variations is founded on the same fundamental idea: the digital twin is a virtual model of a physical object or product. This virtual representation may include design, simulation, or other models that evolve and change over time as the product it represents matures. In other words, the digital twin connects the virtual and physical worlds, blurring the distinction between engineering and process domains. enabling manufacturers to improve product design, troubleshoot issues, and make more informed decisions
A digital twin should dynamically expand and reorganize across development and manufacturing processes to get the most out of it. As the product evolves, it will be used in a variety of ways by various functional departments.
Many people overlook the significance of digital twins for products and plants. When used correctly, this link can assist manufacturers in improving and even optimizing their products and processes by providing actionable design insights and significant operational efficiencies as digital transitions to physical.
The role of the digital thread in digital transformation
A digital thread is a more recent concept than a digital twin. The digital thread is the digital representation of individual business processes (activities, tasks, and decisions) that supplement and expand the digital twin. These procedures also contribute to efforts to automate, trace, and standardize.
Some companies are digitizing manual, paper-based, or email-based processes so that they can be integrated into the digital thread. This helps to reinforce the digital thread. Processes that could be converted include supporting digital activities in a system of record, as well as automating or routing tasks based on defined logic and constraints. One tangible advantage of these examples is that project stakeholders can be automatically notified of key decisions or activities that are running late.
Another way manufacturers are capitalizing on the digital thread is by automating processes and exposing more information in other business systems, including those used by supplier partners. Such efforts may employ a variety of system types, including product lifecycle management (PLM) platforms and manufacturing execution systems (MES). By sharing critical data across different business systems, organizations can improve communication and collaboration, support key decisions, and activate triggers to activate contingency procedures.
Adopting the digital thread enables an organization to connect previously siloed and difficult-to-access sources of information. When this data flows freely, it can aid in automation and improvement efforts at all stages of the product development lifecycle.
Start your journey towards digitalization to maximize ROI
The CPG industry is rife with competition. Product and process innovation are the only long-term competitive strategies. Digital transformation is a key strategy for applying advances in IT and OT to product and process innovation, and this trend is expected to continue for the foreseeable future.
While simulation technologies have been available for decades, their application in CPG is relatively new, with significant opportunities for business improvement. Companies can use digital twins enabled by a digital thread to plan, develop, and optimize equipment, production lines, and factories more efficiently than ever before, maximizing their return on investment.
To learn more about how digital twin technology can help your business overcome today’s challenges, read the CIMdata Report.