MBOM management: Building a successful smart manufacturing strategy for aerospace and defense
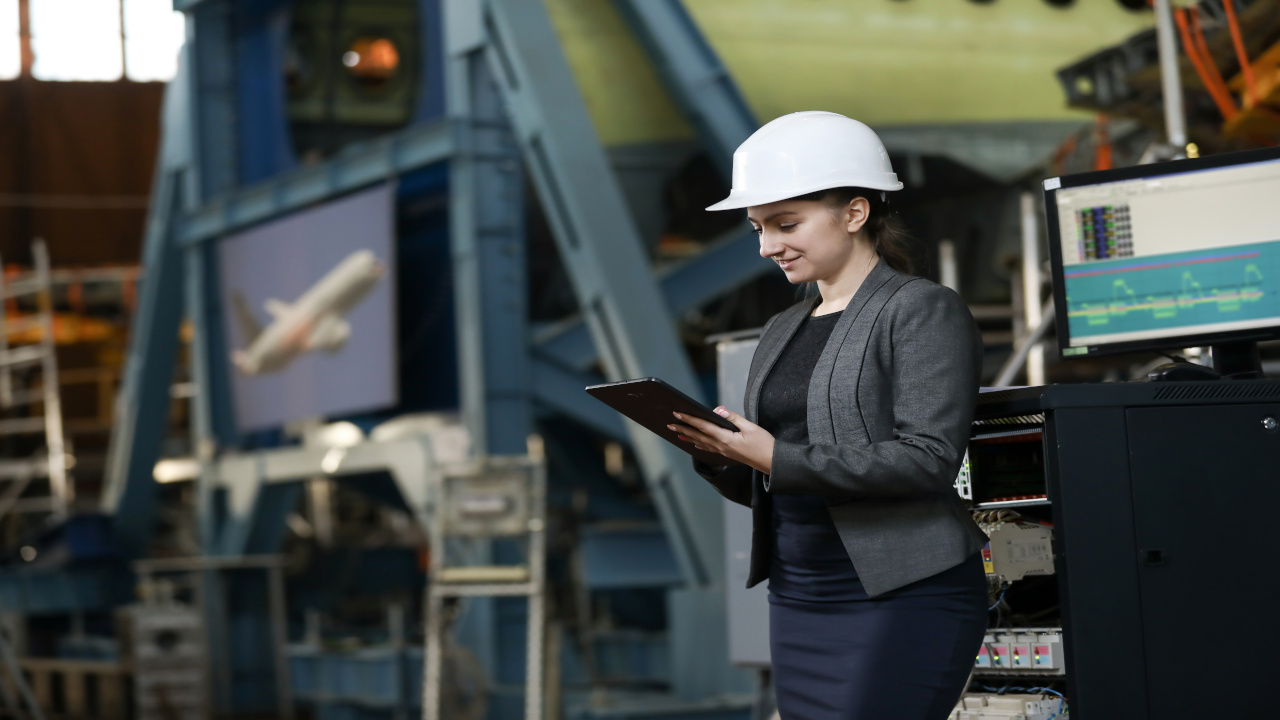
Aerospace and defense manufacturers are facing a challenging environment. Beyond fierce competition, they’re facing increased part complexity, rigorous quality standards, labor shortages, supply chain interruptions and compressed lead times. It’s an environment that requires a drastic change in product and process development.
What does this drastic change entail? It means shifting away from linear, document-driven processes and toward a concurrent, collaborative approach to manufacturing development. Engineering must be connected to the shop floor, and this is particularly true when it comes to the manufacturing bill of materials (MBOM). Read on to learn more.
Challenges to productivity in aerospace manufacturing
For many aerospace manufacturers, one of the most common disruptive issues to manufacturing operations productivity is the lack of necessary materials to produce products. While many times these inventory shortages are due to influences outside your control, such as supplier delays or global disruptions in the supply chain, other shortages and issues are completely within your control. For example, data gaps and errors created by disconnects between engineering and the supply chain. Forgetting to populate a make/buy value or using an incorrect unit of measure may seem inconsequential, but this can drive incorrect inventory levels or required parts to not be ordered at all. Many times, these unintended inventory gaps won’t get discovered until there is demand for incoming orders, creating the potential for serious disruptions. Beyond understanding the material requirements, there is also the need to evaluate the bill of materials (BOM) for manufacturability and understand the potential impact on your production processes and equipment. These issues are only going to increase with the growing complexity of aerospace products.
You may have implemented some level of manufacturing bill of materials (MBOM) management that provides the orderable BOM within your enterprise resource planning (ERP) system. However, this MBOM, if manually replicated and based on the related engineering BOM, provides plenty of potential for human error. Even when automated transfers of data are implemented, they typically lack the necessary processes and accountability to ensure the accuracy of the data. Another common pitfall is relying on your design engineering department to manage the MBOM definition based on the manufacturing and supply chain requirements. This can incur unnecessary design changes and costs. In fact, this could likely create new issues and delays due to the volume of change, increasing the chances of error.
This creates a complete disconnect and lack of traceability to the engineering intent, introducing the possibility of significant quality or compliance issues. Another disconnect that stems from not leveraging integrated manufacturing tools is the lack of collaboration between engineering and manufacturing domains. With limited collaboration, you reduce your potential for early manufacturing validation, which helps to identify critical issues sooner. This disconnect can also drastically increase the time required to produce new products or implement changes due to the sequential “throw it over the wall” nature of this approach.
Integrated manufacturing bill of materials for aerospace and defense
By implementing an integrated, collaborative manufacturing BOM within your product lifecycle management (PLM) system that is directly linked to the engineering definition, you get a mechanism for manufacturing and design engineering to collaborate much earlier in the product lifecycle. This linkage also provides enhanced re-use of existing information, beyond just part metadata. Early on, you can provide manufacturing with controlled access to design details such as 3D models and drawings, as well as access to associated requirements and specifications (some refer to this, as “model-based manufacturing”). This access can allow manufacturing engineering to assess manufacturability and provide feedback to influence the designs while the cost of change is low. It supports a real manufacturing engineering analysis and turns the MBOM definition business process into an engineering-oriented one – rather than an operation-oriented one – in case, this is fulfilled in the ERP system. Thus, it enables, for example, optimization of the sequence of assembly and manufacturing. Additionally, this linkage can provide design engineers with a clearer understanding of the impact of potential changes and the ability to coordinate with relevant manufacturing stakeholders based on the related MBOMs. Beyond just enabling earlier collaboration, managing the MBOM within your PLM system allows for the implementation of formal change processes. This will trigger adequate validations or signoffs to ensure the quality and accuracy of the data prior to releasing it for use downstream. A broader Manufacturing Change Notice (MCN) process could also be introduced to ensure all necessary supply chain stakeholders will be notified to acknowledge any potential impacts. This means faster and more reliable change cycle implementation.
Ensuring manufacturing efficiency
As you look to improve your manufacturing efficiency and address new challenges, it’s critical to ensure that you have a common understanding of your products’ part requirements across your organization. Without this basic foundational data and an ability to ensure the traceability and accuracy of your MBOM data, you have the potential for delays, certification/compliance risks and quality issues. By introducing a solution that enables an integrated manufacturing BOM as part of a broader digital manufacturing strategy, you can provide significant benefits to your organization including:
- Avoiding costly changes with early identification of issues across the supply chain through improved collaboration between manufacturing and engineering
- Improving accountability through clear visibility of BOM impacts, ensuring inclusion and signoff from required stakeholders
- Improving customer satisfaction with improved quality and compliance through direct linkage and validation to engineering intent
- Reducing inventory costs through clear visibility into the latest part requirements, minimizing inventory holds and reducing scrap of obsolete parts
- Avoid rework with accurate and consistent transfers of MBOM data to downstream systems (e.g., ERP, MES), ensuring the quality of BOM data across your supply chain
Teamcenter Easy Plan
Teamcenter Easy Plan is a powerful solution to digitalize your manufacturing bill of materials. With Easy Plan, you can standardize and reuse assembly processes across multiple plants, capture work instructions for the shop floor, perform detailed time analysis, balance production lines and much more.
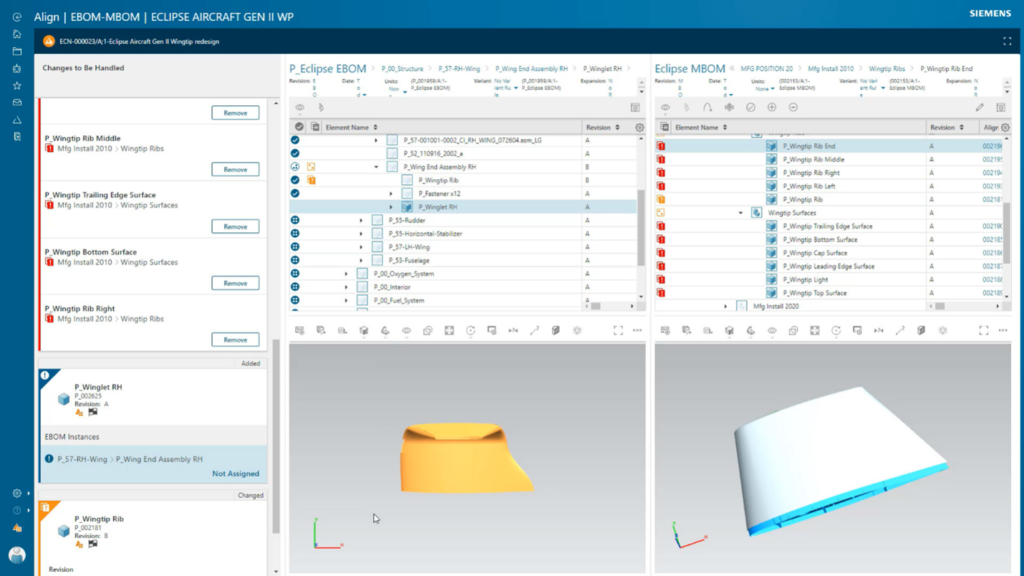