The Digital Twin for CNC training
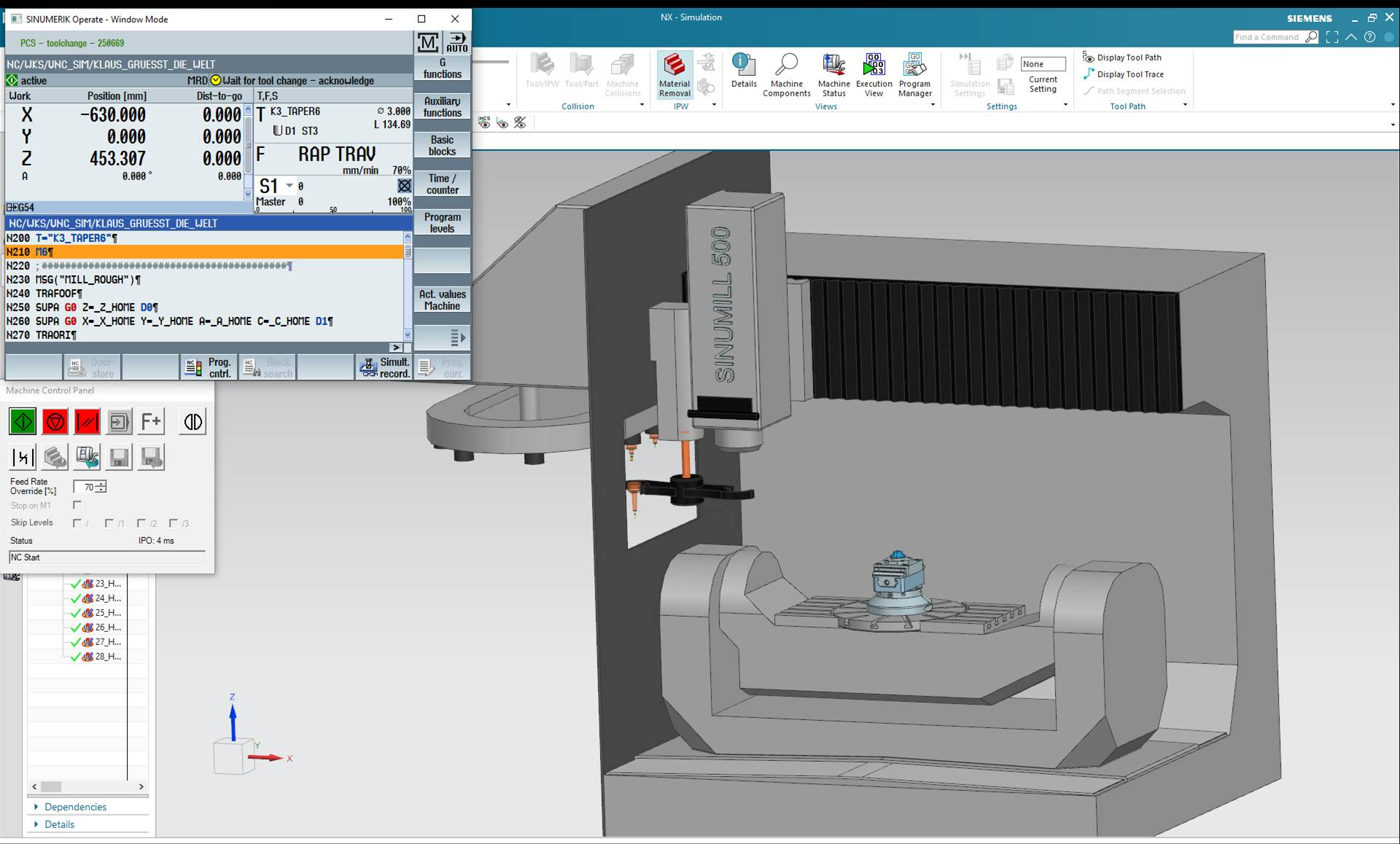
Adapted from blogs by Stefan Hirsch, Managing Director, Bengcon and Peter Kemptner.
Industry 4.0 , Internet of Things (IoT) and the Digital Twin are the buzzwords that cannot be avoided when talking about digitization in manufacturing. In order to maintain their competitive in an international market, manufacturing companies must introduce modern digital process chains. This is usually a lengthy and technically complex process. From data storage, internet security, networking and the CAD-CAM-CNC process chain – there’s many different aspects of digitalization within manufacturing to consider.
In order to be able to master these processes and to be well positioned for the future, existing employees must be trained for the new challenges. Even more important? Future employees should be familiar with the tools of digitization and have the technical skills needed to allow them to bring in fresh ideas to the company. Siemens Digital Industries Software is collaborating with engineering schools and educators to bring industry-grade software and curriculum to classrooms around the world. This enables Siemens to provide the industry with skilled graduates familiar with a fully digitalized approach to end-to-end product creation.
CAD-CAM-CNC process chain
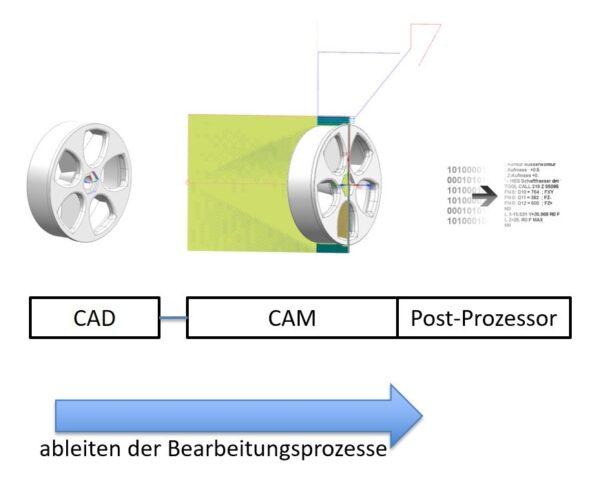
To reduce standstills and improve productivity, more and more companies create NC programs using computer-aided manufacturing (CAM) software. They are turning to simulation and using the digital twins of their products, the production machines, and the machining tools to test manufacturing processes before executing the CNC programs.
The CAD–CAM–CNC process chain is an important digitization component in production. In this, the machining paths for CNC machining (CAM) can be created from the digital model of the product (CAD) using offline programming.
After checking the tool paths in a visualization and, if necessary, optimizing this digital phase, the so-called post process generates the NC code for the machine from the data calculated in the CAM program. This code can then be transferred to the machine tool in order to manufacture the workpiece (see figure above).
One problem with this approach is that with complicated set-ups or machining, especially with 5-axis machining, collisions between tool, workpiece and setup can occur. In most cases, these collisions lead to damage to all parts that are involved in the collision. Since CNC machines are highly complex and precise devices, the follow-up costs of a crash are quite high.
To avoid this, the digital process chain is expanded to include the component of the digital twin of the machine tool (see figure below).
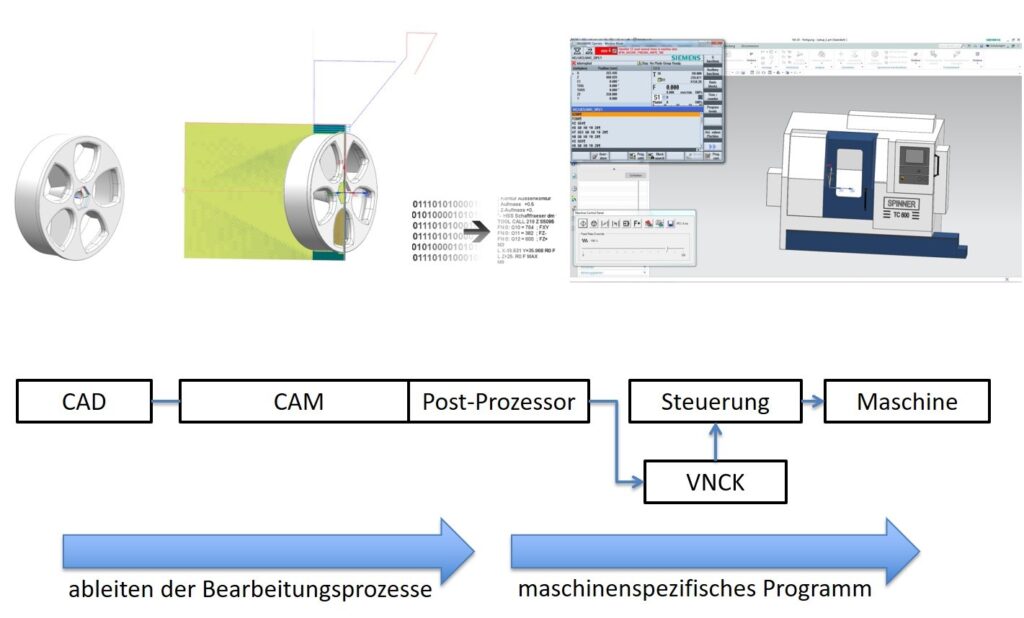
Here the NC code that is loaded onto the machine is extensively tested in the virtual CNC machine beforehand. This process takes place offline and the real machine tool is not used during the verification process. This is particularly important for long-running programs in one-off production.
CNC simulation versus digital twin
Many CAD-CAM software providers offer that you can check the results of the machining planning with their software through simulation. Often, however, this is only a representation of the tool paths before the post process is carried out and the machine code is generated.
This is often not precise enough and, above all, does not secure all tool paths and movements that are subsequently generated by the postprocessor. In order to really get an exact statement about the movement taking place on the machine, it is advisable to use a digital twin of the machine.
The digital twin is a true-to-life digital image of the real machine tool that is used in the workshop, namely with regard to all geometries of the machine, devices and tools, as well as the control system used in the real machine, including the version and all parameter settings .
For this purpose, all machine data and parameters can be extracted from the machine tool in a Sinumerik control and transferred to the PC version of the control. This option is called VNCK (virtual NC kernel) and is only available for Sinumerik controls. The VNCK is then coupled with the output of the CAD-CAM software and thus all movements of the machine with tools, clamping devices and components can be shown kinematically using the virtual machine.
Digital twin for training on CNC machines.
With products SINUMERIK 840D, and the CAX system NX, Siemens AG and Siemens Software have developed an ideal platform for creating and operating a digital twin. Training on virtual machines has proven to be advantageous to students in the classroom and beyond.
Students can safely test and optimize NC programs without causing damage to a real machine. Another advantage is that every student can operate the digital twin at their own PC workstation. Under certain conditions, this is also possible online from home. With conventional training, it is almost impossible for the teacher to have each of his students programmed on the machine. Most educational institutions lack the resources to run more than one CNC machine. Often you still have to decide between turning or milling. With the digital twin, almost any machine type and any kinematics can be simulated, provided the CNC control is a SINUMERIK 840D.
Like a CNC machine, a digital twin is an individual product and is created and adapted upon customer request. To ensure that the machine behavior is as accurate as possible, a precise CAD model including all physically available components must be modeled and an individual postprocessor must be created for the real machine tool and its digital twin. Clamping devices and tools as well as the parameters of the real machine control flow into the model. The creation of a digital twin requires expert knowledge and is only carried out by different partners of Siemens PLM and Siemens AG.
The educational partnerships between Siemens and schools around the world is execrating the digitalization of manufacturing and helping to create a more efficient and cost-effective workforce that is ready to tackle the problems of tomorrow.