Darmstadt University of Applied Sciences uses Siemens software for Industry 4.0
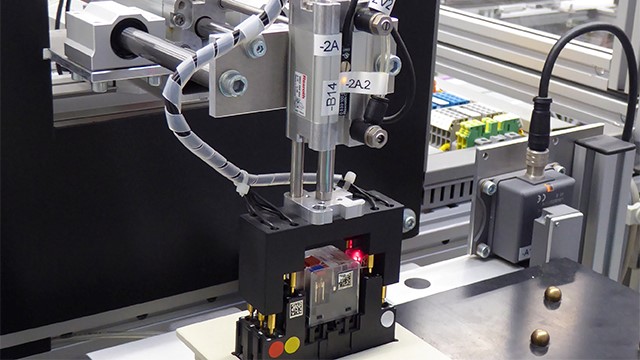
By: Hannah Straub
In the world of technology, software drives innovation in constructing an engine, creating a heart catheter, or in Darmstadt University of Applied Sciences’ case, designing and operating a smart learning factory. Students learning about automation and control technology at Darmstadt use Siemens Digital Industries Software products to “run an assembly plant that reproduces the automation processes in a real factory,” says Dr. -Ing Stephan Simons, professor of automation and control technology.
Darmstadt University of Applied Sciences is one of the largest universities of applied sciences in Germany with approximately 16,500 students, 320 professors, and over 70 degree programs. The university’s range of programs and research capacities extends from engineering sciences, mathematics, information science and computer science to management, social sciences, and social work, as well as architecture, media and design.
Taking us through his process, Dr. -Ing Stephan Simons says, “Tecnomatix and Mechatronics Concept Designer allow us to teach students to select the right software for a task.”
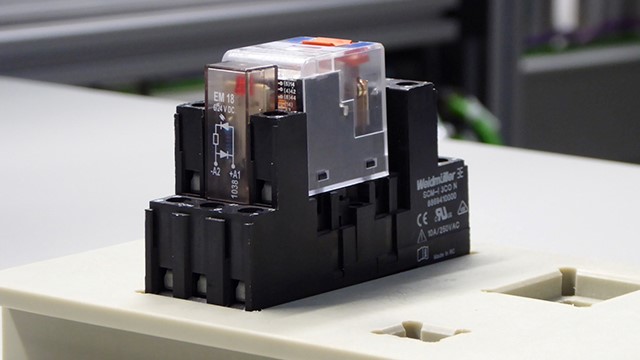
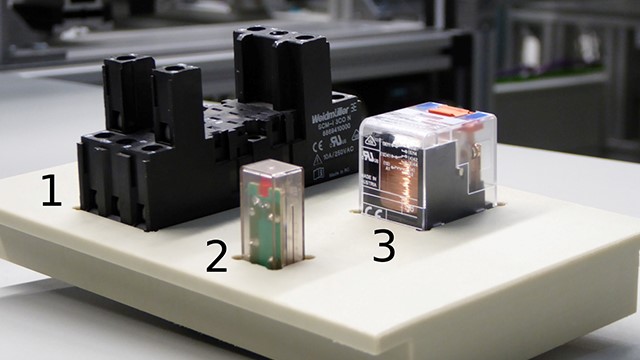
“This small smart factory is an Industry 4.0 demonstrator and a research and tutorial platform where interdisciplinary teams of students learn how to design, commission, operate and maintain future production facilities utilizing the Internet of Things,” he adds.
Students from various disciplines leverage the digital factory, including electrical and mechanical engineering with image processing and opto-technologies.
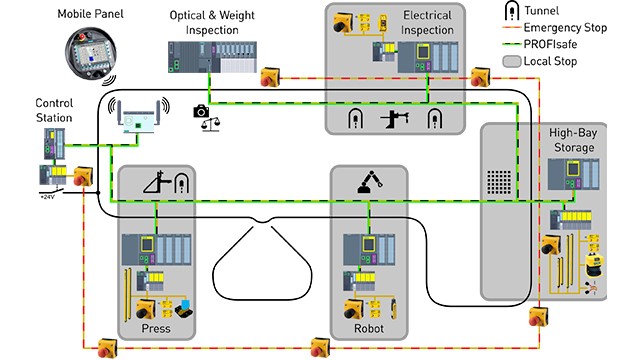
The main goals of the university’s program are:
- Teaching industrial automation and control as it will be in the future
- Preparing students for future challenges in systems development
- Using various software tools to build comprehensive solutions
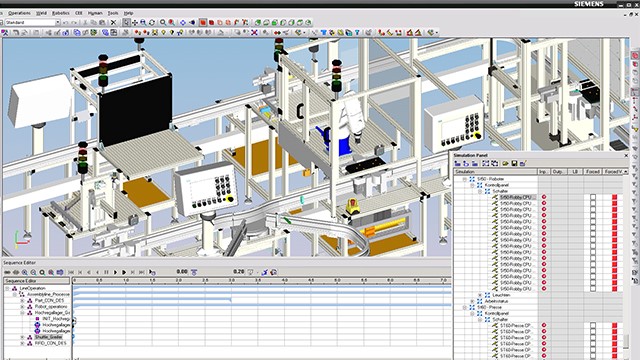
Professor Simons wanted to use a digital twin from the start, which in turn led him to Tecnomatix, a comprehensive portfolio of digital manufacturing solutions that help digitalize manufacturing. The smart assembly line teaches students how to create comprehensive systems, and to familiarize themselves with knowledge outside their own specialization focus. It combined the virtual and real world for students and taught them how to handle constant change in automation.
As a result, students learn how to design, commission, operate and maintain future production facilities. Their education expands their view with future oriented, comprehensive systems design. They develop methods for easy implementation in future industrial production facilities based on the Internet of Things.
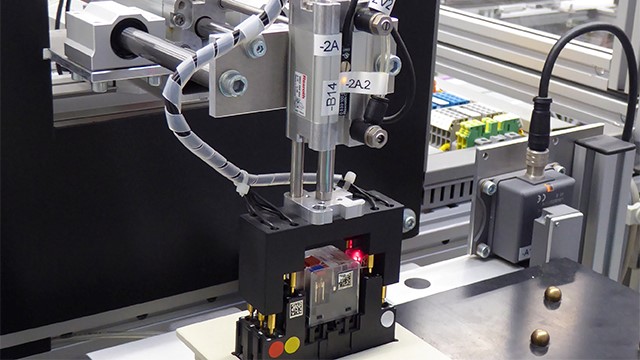
To read the full story, click here.
Check out more academic case studies.