Digital Twin Sophistication at 2019 Formula Student Germany
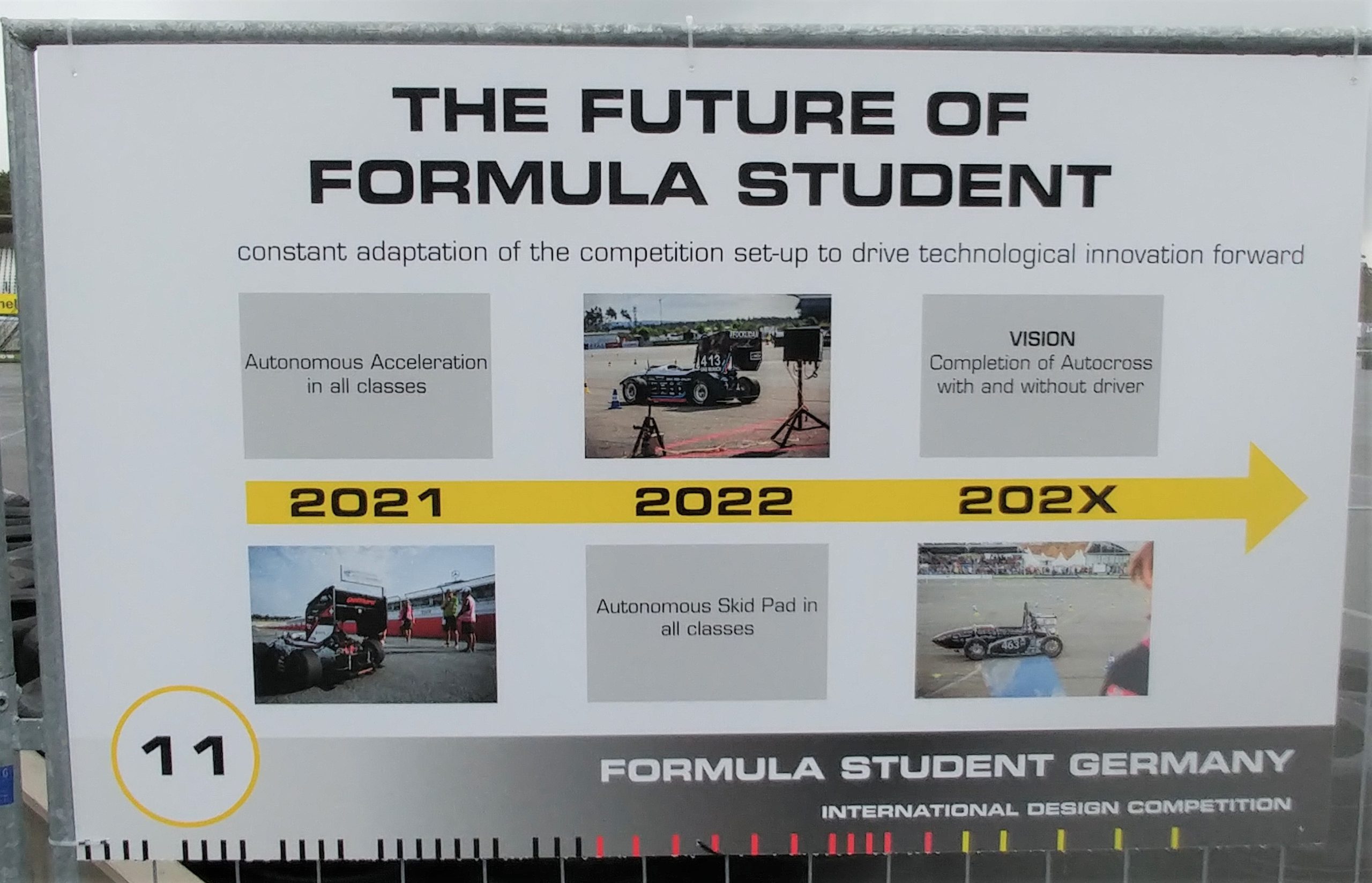
Siemens Digital Industries Software’s academic program has been supporting Formula Student Germany (FSG) teams with engineering software, training, and collaborations for many years. Siemens was again a sponsor of the 2019 FSG event held at the Formula 1 track in Hockenheim, Germany, August, 2019, including the second year of the prestigious “Siemens Digital Twin Engineering Excellence Award”.
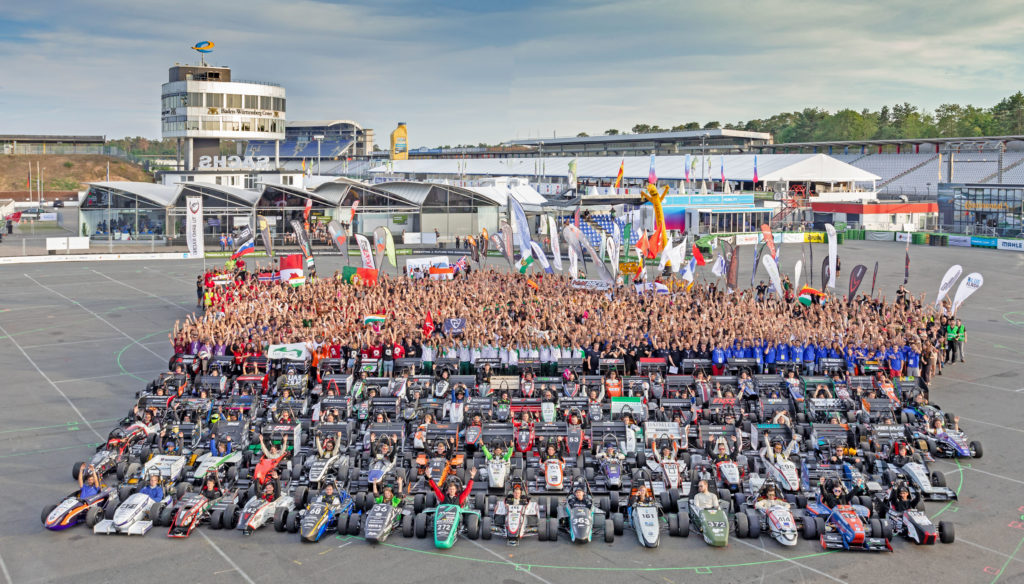
Quote from first place Digital Twin winner GreenTeam Uni Stuttgart: “Using digital twins in Formula Student is one of the key factors to be able to win competitions, save money and keep teams organized. With more than 8000 manufactured parts, 120 processes and 4.5 TB of CAD data, the need for a structured organization arises.”
This world-class FSG university real-world student competition not only includes combustion and electric powered racecars, the event features the most advanced student-built autonomous formula racecars in the world, in its fourth year. The autonomous racecar class is called Formula Driverless.
All the top-tier autonomous electric, and combustion teams at FSG use a Digital Twin style engineering methodology with extensive use of virtual models, simulation and product data management, and virtually every top-tier team uses Siemens’ engineering software.
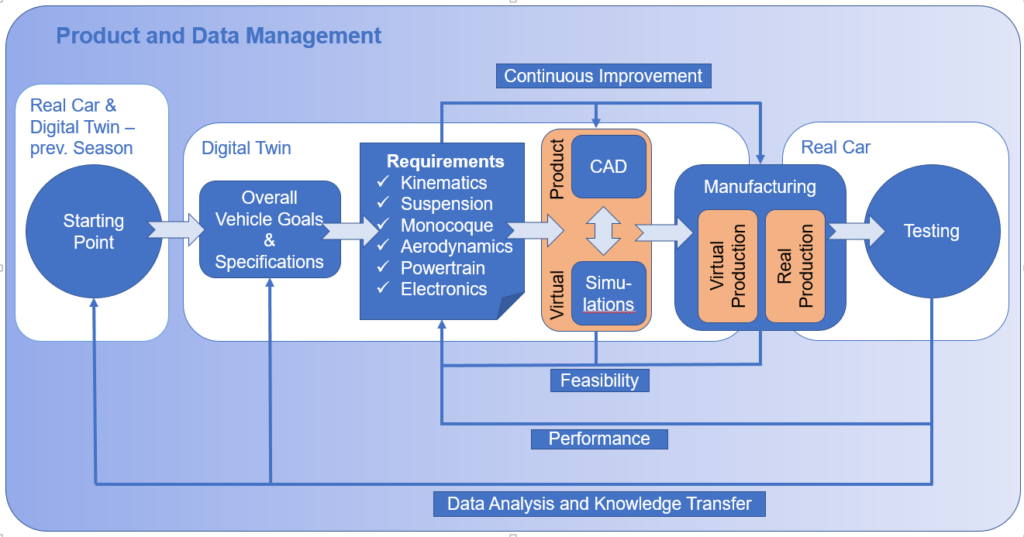
Siemens Digital Industries Software’s Global Academic Partnering group, as well as local country staff, offers software grants, technical support, workshops and online training at no cost to Formula Student/SAE teams worldwide, so they can implement Digital Twin engineering methodology with a powerful and integrated software suite. In addition to extensive training workshops at the FSG event, Siemens also hosts workshops in the Fall at two Siemens training centers. Online/on-demand software training courses, and Formula Student-specific tutorials and expert tip articles are also available year-round. For Mentor online courses see this link (teams can access at zero cost.)
FSG Event Overview
The Formula Student Germany 2019 competition challenged university undergraduate and graduate students in 119 European and international teams to conceive, design, fabricate, develop, test, and compete with formula-style racecars. Teams compete in static presentations such as design, business, and cost to judges from the auto industry, then compete in dynamic events on the tarmac such as acceleration, skidpad, autocross, endurance, and energy-efficiency. Using best-in-class, integrated engineering software from Siemens helps with all aspects of the competition.
First let’s meet some of the top teams and their stunning cars to set the stage for the 2019 Digital Twin award and then see some technology examples.
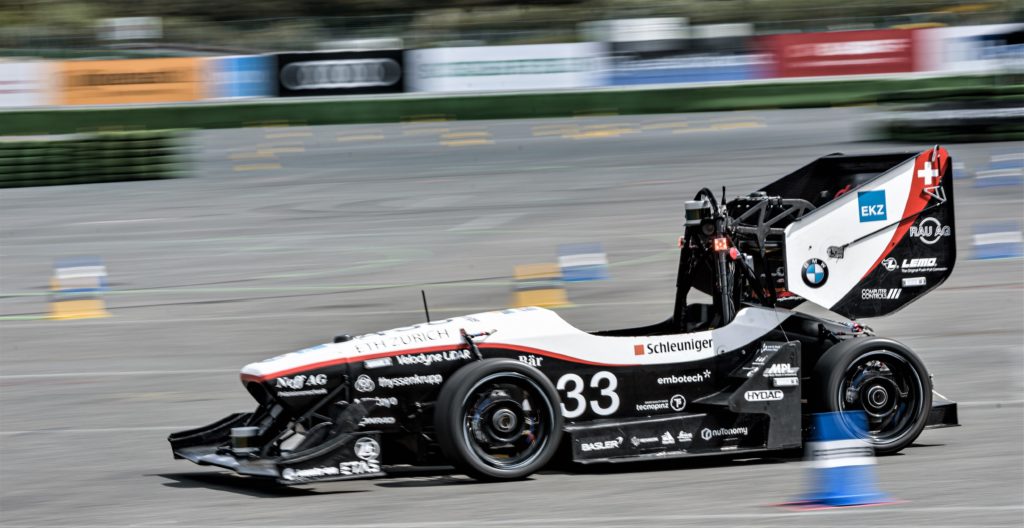
overall Formula Driverless class was won by AMZ Racing from ETH Zurich
University. No hands on wheel – no driver! Photo by AMZ Racing
This electric-drive vehicle is the fastest student-built autonomous car in the world! Also featuring a super light carbon-fiber composite chassis, and a potent carbon aero-downforce package for rapid cornering, this car was also optimized with Siemens’ STAR-CCM+ 3D-CFD simulation software well before the racecar was fabricated, definitely a Digital Twin method.
Digital Twin Engineering Excellence Award
Siemens sponsors a prestigious award at FSG – the ‘Siemens Digital Twin Engineering Excellence Award’, which honors student teams for their achievements in this most modern and effective engineering methodology. In fact, without the advanced simulation and design practice of Digital Twin, it’s simply impossible for teams to compete at the highest levels of FSG!
Watch this video of the 2019 Siemens Digital Twin Award Ceremony (skip to the video time stamp of 54:35).
Siemens also recognized the ‘Most Rapid Progress Toward Digital Twin’ Honorable Mention by the Dynamis PRC team from Politecnico di Milano university – and the Special Mention of the fourth-place expert Digital Twin team, AMZ Racing from ETH Zurich university, which also won 1st place in the Formula Driverless class.
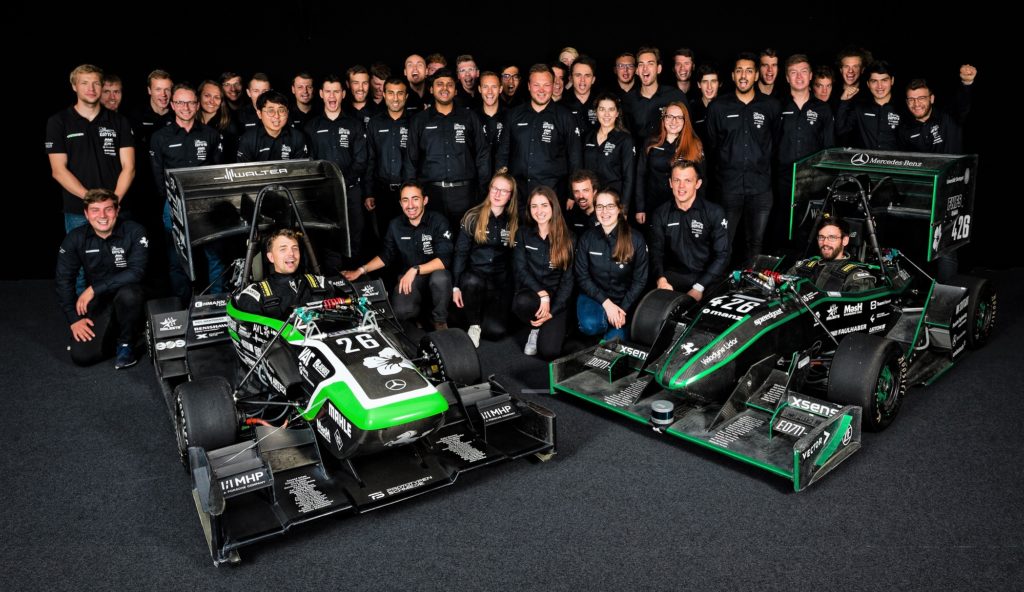
Formula Electric car on left, Formula Driverless car on right. ©FSG, Photo by Johannes Klein
The First place winner of the 2019 Digital Twin Award, for the second year in a row, was Greenteam Uni Stuttgart. GreenTeam also achieved 7th place in the highly competitive Formula Electric class, and 6th place in the extremely difficult technology challenge of the Formula Driverless class.
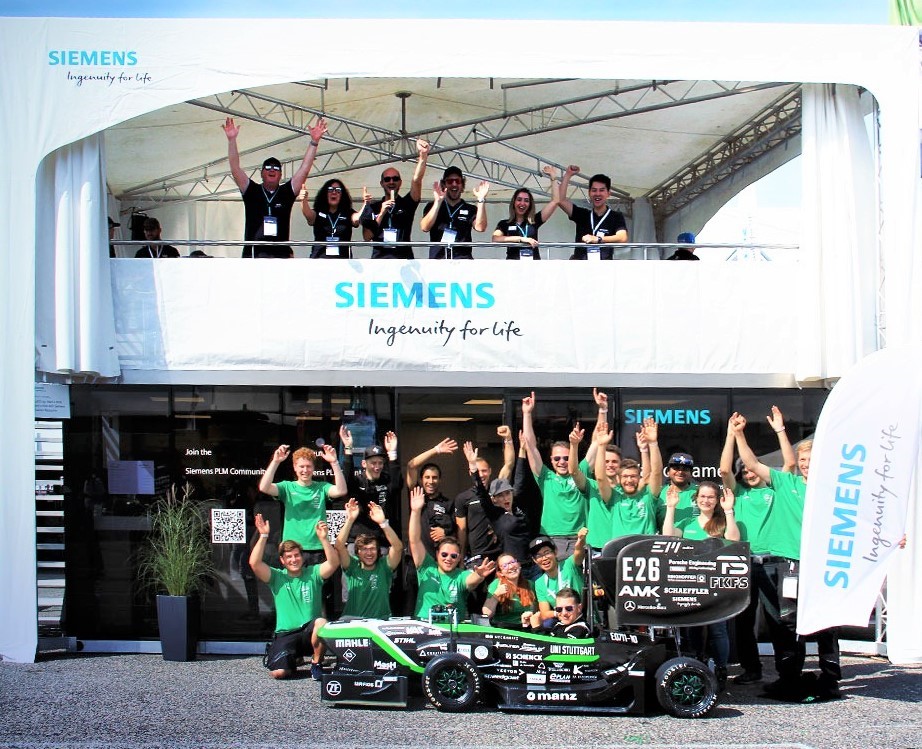
Stuttgart in front of the Siemens Software booth at FSG
The team also improved their self-developed PDM (product data management) system, such as a weight-management tool, an aerodynamic toolbox, a new smartphone app application to upload construction, production and testing data, directly linked to car components. Using new camera-link with visual recognition of vehicle components, accessing part information is quick and easy. For reliability, every part is logged with mileage, driving and weather conditions for preventive maintenance prediction. They even made a mobile phone version of their PDM software.
The GreenTeam car’s all carbon-fiber composite chassis and aero downforce package were designed and simulated with NX for 3D CAD and STAR-CCM+ for 3D computational fluid dynamics (CFD) simulation. They even designed their own electric, in-hub motors with a sophisticated embedded cooling design. This enabled these powerfully compact motors to perform throughout the lengthy endurance event – in their rapid all-wheel-drive racecars.
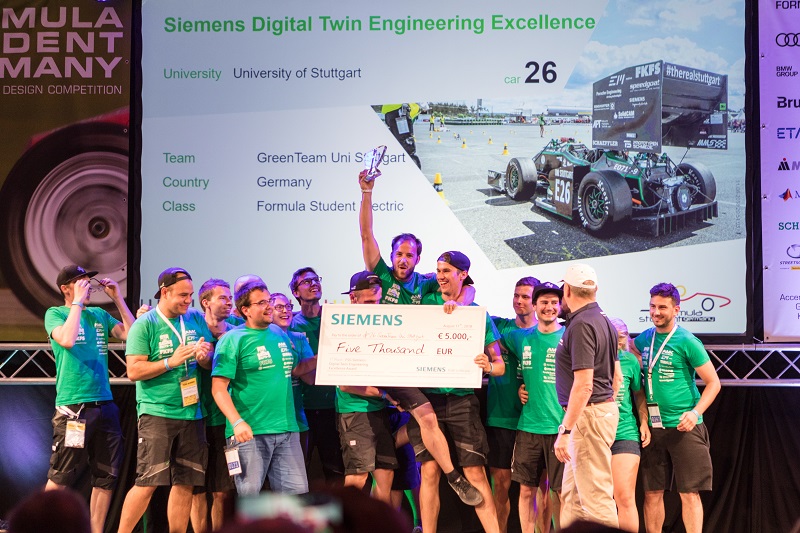
Digital Twin Award in 2018. © FSG, Photo by Vivek Maru
The KA-RaceIng team from Karlsruhe Institute of Technology earned a close second place in Digital Twin excellence – earning a total score across the 7 judging metrics that was a mere 1% behind First place.
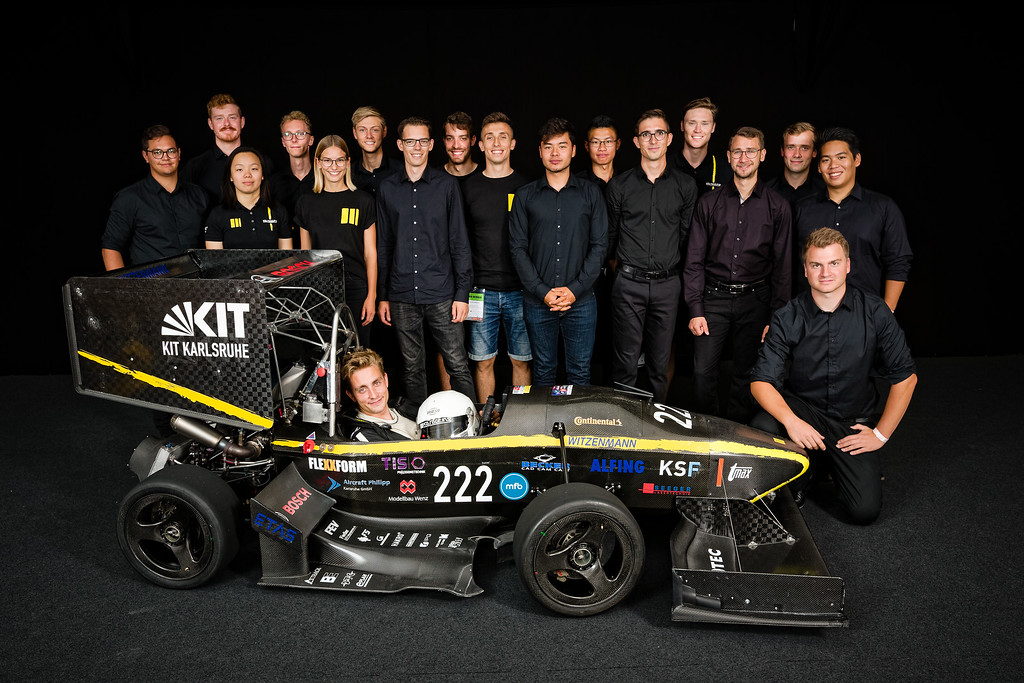
The KA-RaceIng team presented their sophisticated use of 3D design, 3D-print-prototyping and intricate metal-printed parts to Siemens’ judges. These advanced digital twin style parts propelled them to second place in the hotly competitive Formula Electric class, and another outstanding second place in the extremely difficult technology challenge of the Formula Driverless class! … plus a strong 19th place in the large and competitive Formula Combustion class. Like the GFR team, this team pulled of the quite difficult feat of designing, building and competing three (3!) racecars in one year – made possible only with Digital Twin methods and effective software with training and support!
The unique Global Formula Racing team (GFR) was awarded the Digital Twin third place – GFR is the only fully international Formula Student team in the world – including DHBW Ravensburg University students in Germany synched up with Oregon State University students in the U.S.
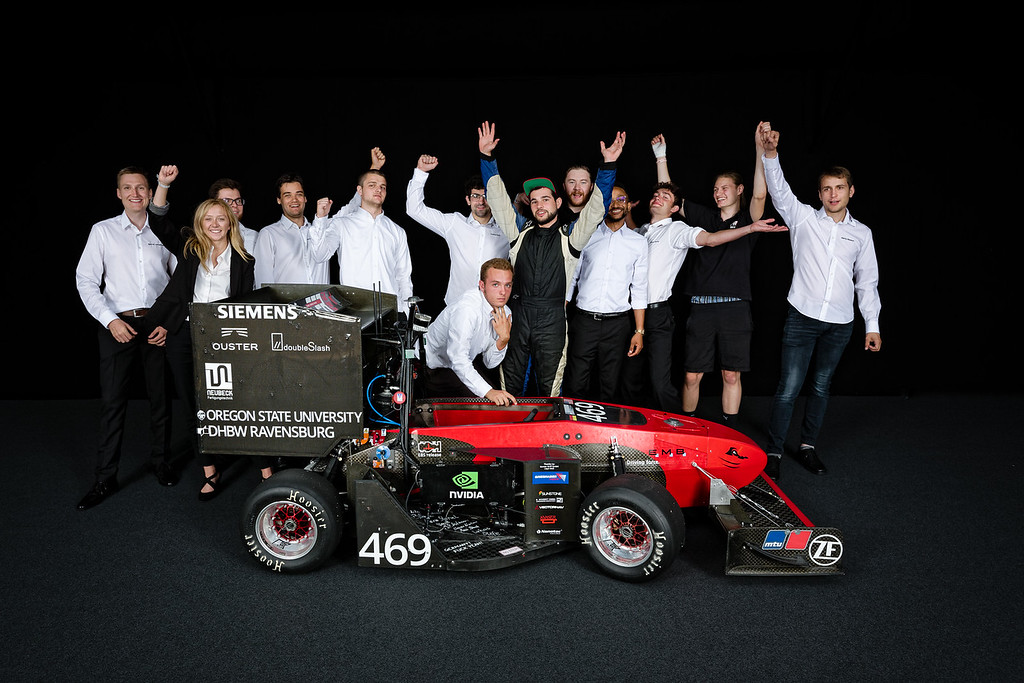
Twin Award makes extensive use of Siemens design and simulation tools in all
aspects of their racecar design, simulation and fabrication. © FSG, Photo by Johannes Klein
GFR’s motto is “TWO NATIONS. ONE TEAM. ONE MISSION”. They co-design/co-simulate/co-fabricate and co-competed a total of three racecars (Electric, Combustion and Driverless). They coordinated this effort across 8,000 kilometers and the Atlantic Ocean, which is only achievable with Digital Twin methods. GFR uses the entire range of Siemens software tools. Against 60 other teams, many that have significantly larger budgets, GFR earned an impressive second place in the hotly-contested Formula Combustion class.
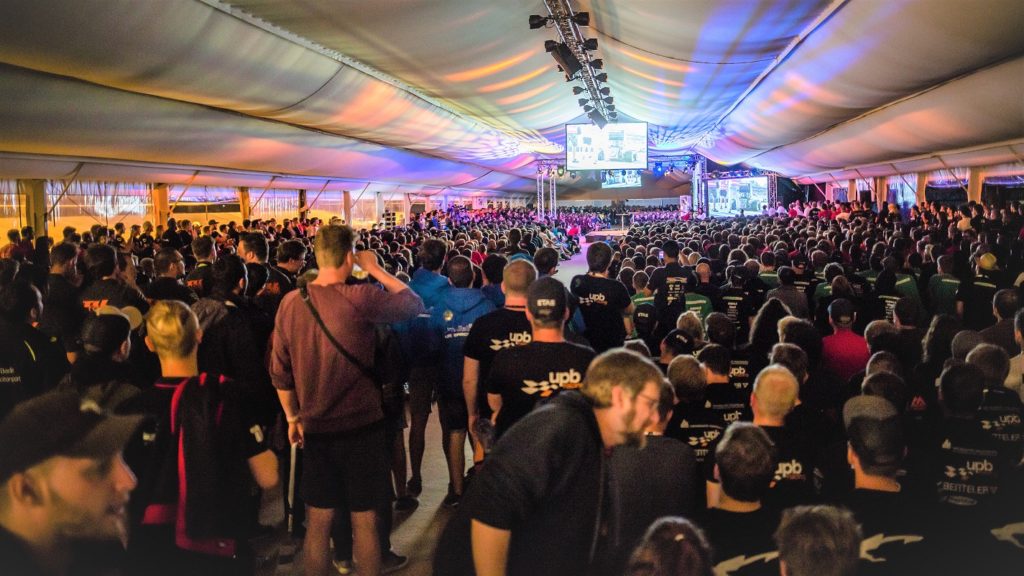
win Siemens’ Digital Twin Award and the other special awards.
(This photo mainly shows just the near half of the very large room.)
Industry commitment
FSG is the most intensely industry-supported university competition in the world. These students are highly sought after by industry because they are prepared to do real engineering immediately – teams not only design and build a new race car from the ground up, they must work as a team to do this while handling business, project and cost management, marketing, recruiting and training new members, and logistics.
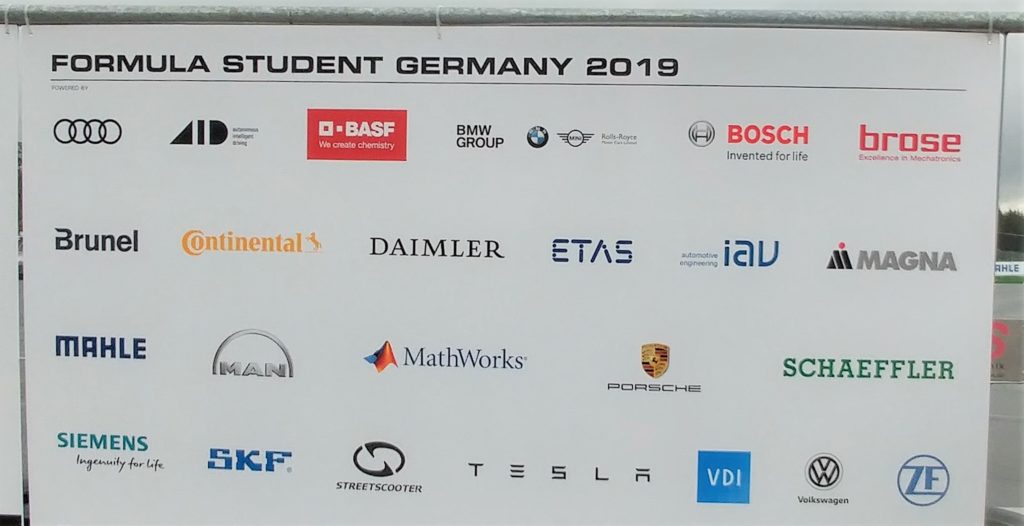
many volunteer judges to help make FSG a success every year,
plus erecting temporary buildings and tent-booths for recruiting
The German auto industry strongly supports FSG. Every major automaker has a significant presence, including volunteering many of the 450 judges, safety inspectors and course workers. For example, Continental and Volkswagen both had large 2-story temporary buildings for recruiting and brand-building with the invaluable talent of FSG students. Many FSAE event sponsors are among Siemens’ engineering software customers. We are pleased to aid in preparing students for their careers through Siemens’ support of FSG!
Engineering Students Depend on Siemens Software
Siemens Software supports ~300 Formula Student/SAE teams worldwide. This includes nearly every top-tier team in the world. Teams are turning to Siemens because they realize that every team that has risen to top-tier uses Digital Twin methods and that Siemens can help them implement Digital Twin methods with Siemens engineering software.
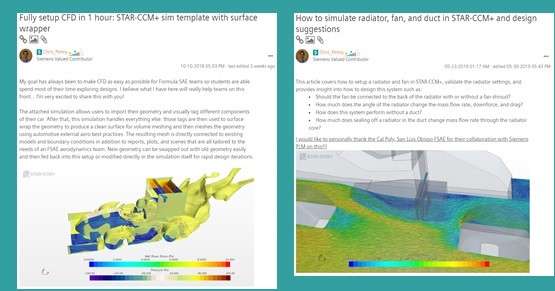
For example, Siemens collaborated with four student teams to develop a STAR-CCM+ simulation template so that students can build a complete 3D-CFD aerodynamics simulation in 1 hour.
Another collaboration with the California Polytechnic San Louis Obispo team led to the development of an article that shows how to setup a radiator duct and fan sim in STAR-CCM+. This includes a Digital Twin style experimental validation and design exploration studies.
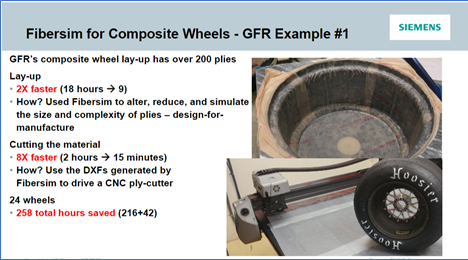
The top photo is of a wheel during fabrication; and the
bottom photo shows an assembled wheel+tire sitting on the ply-cutter table.
Siemens’ Fibersim software saves a lot of money, labor and materials cost, using it’s unique fabrication-simulation ability Also see the Global Formula Racing example – report on how Fibersim helped them develop their composite parts while saving time and material cost.
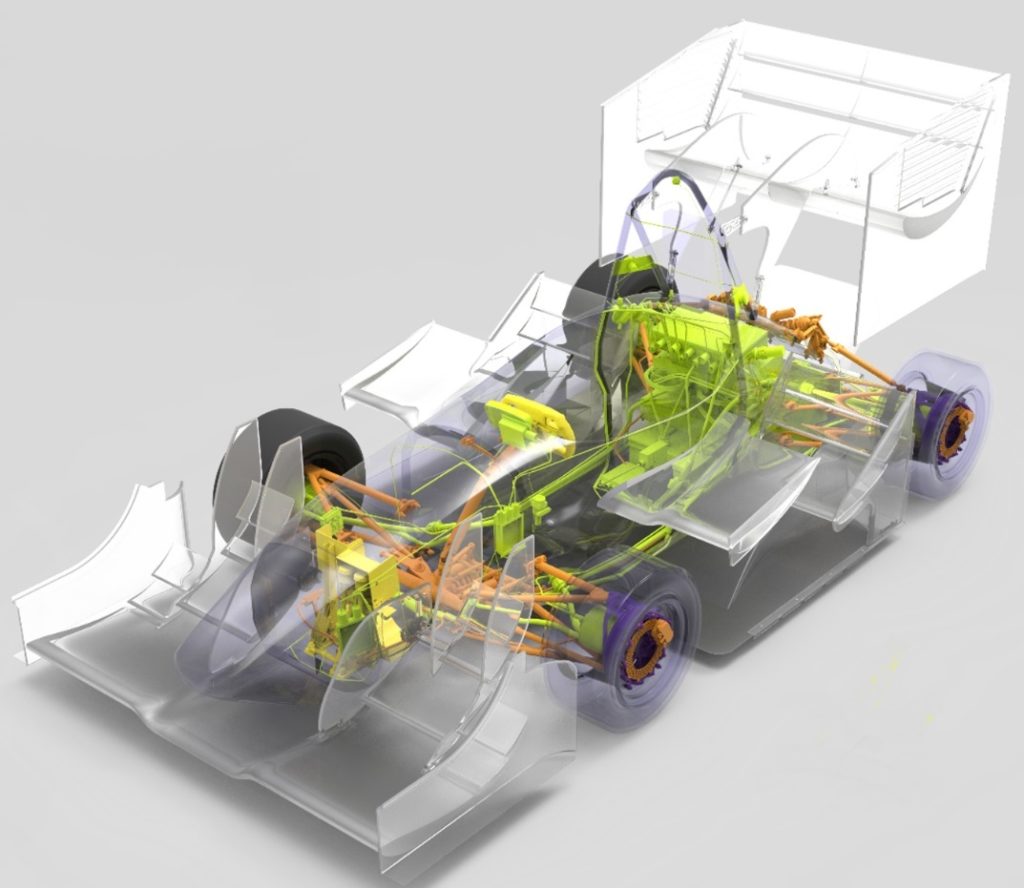
& wiring harness, designed with Siemens NX and VeSys sofware The
virtual car was fully-designed before fabrication Digital Twin style, with digitally-driven fabrication of many parts
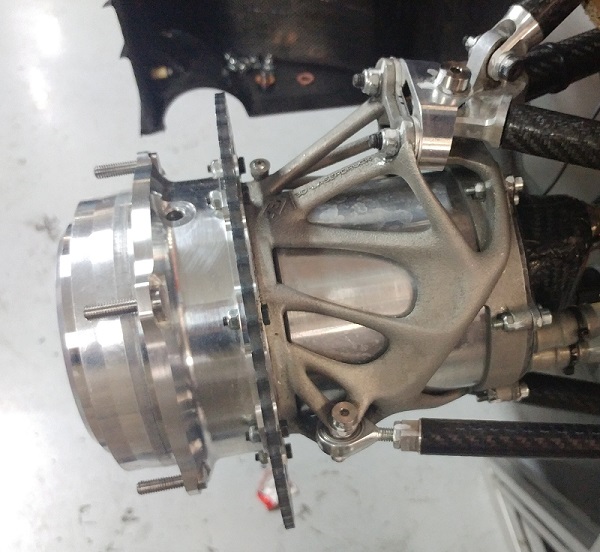
More and more teams ask for Siemens software tools along with product data management, mechatronics, and our other software. We also provide supported teams with no-cost on-demand/online training and FSAE-specific design tutorials – all the better to enable Digital Twin methodology. Siemens’ Formula Student and FSAE forum has many valuable tips for designing, simulation, guidance for accessing e-learning, and much more.
Appendix
of Digital Twin Engineering
Technology Examples from FSG
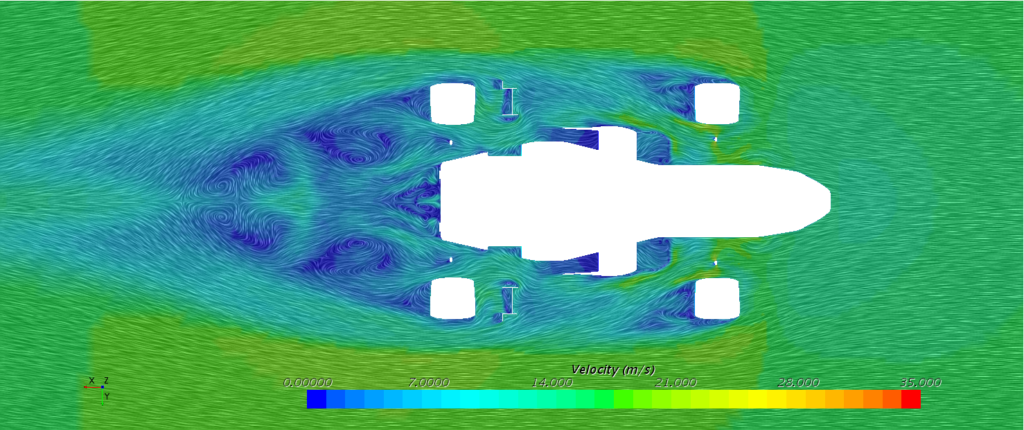

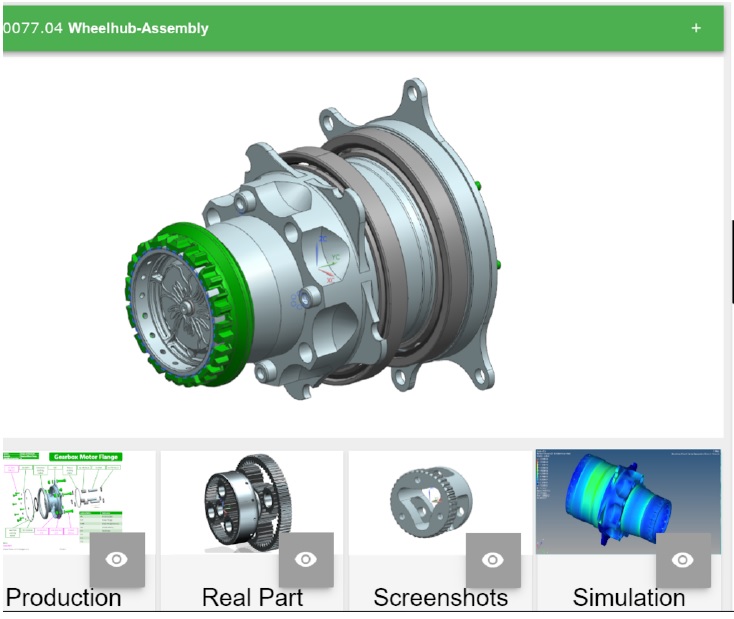
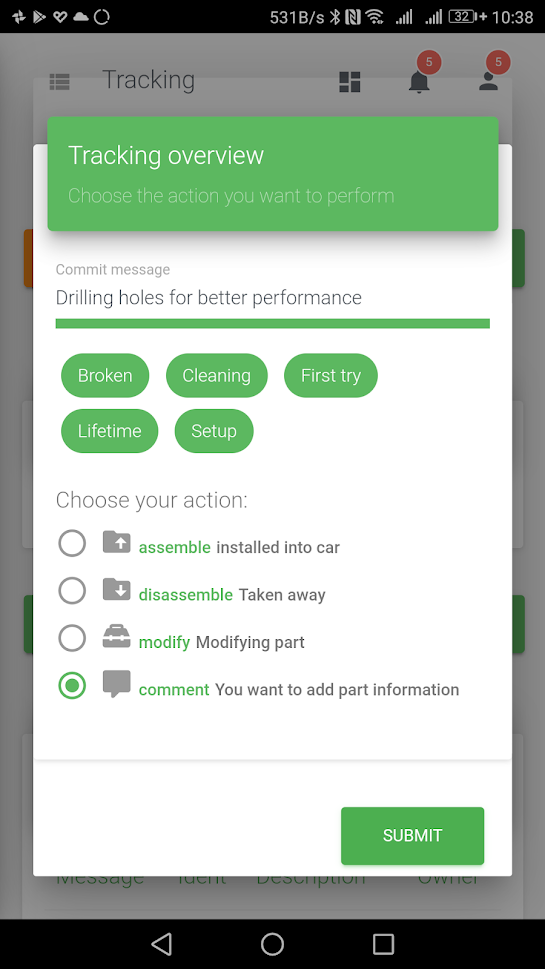
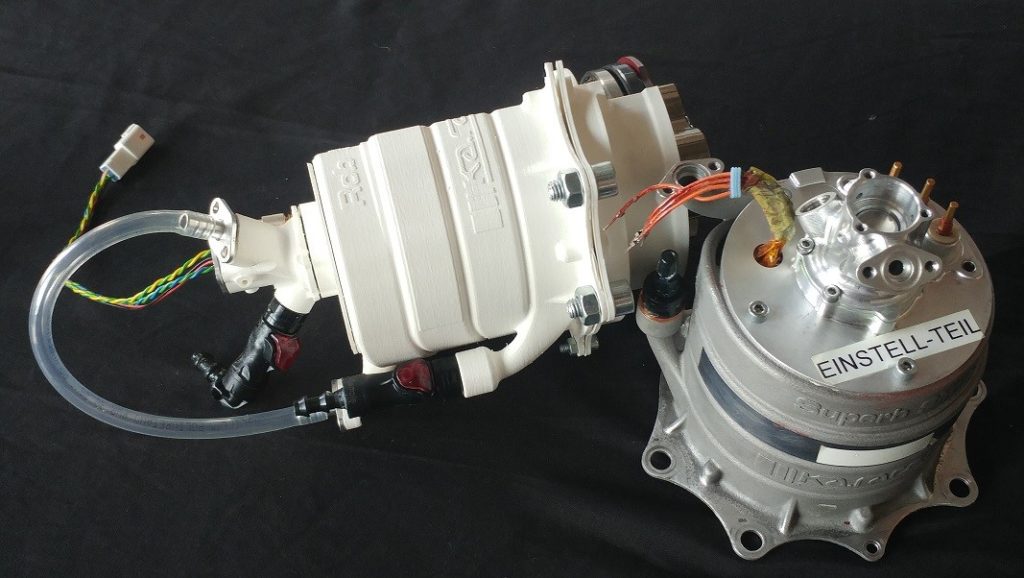
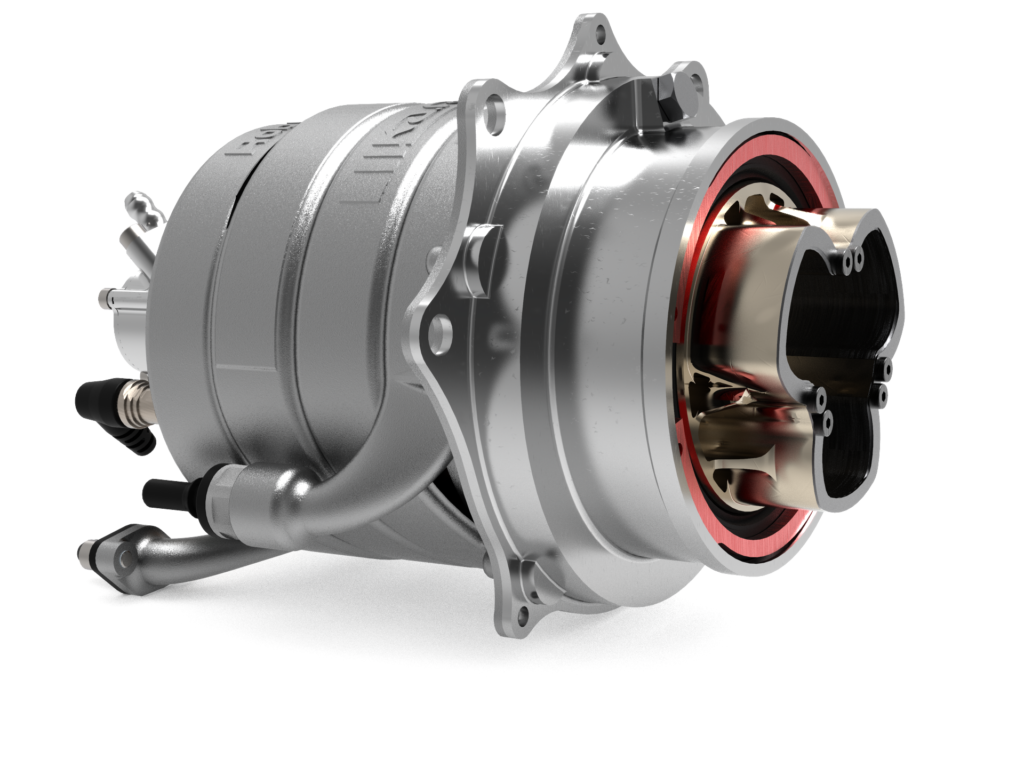
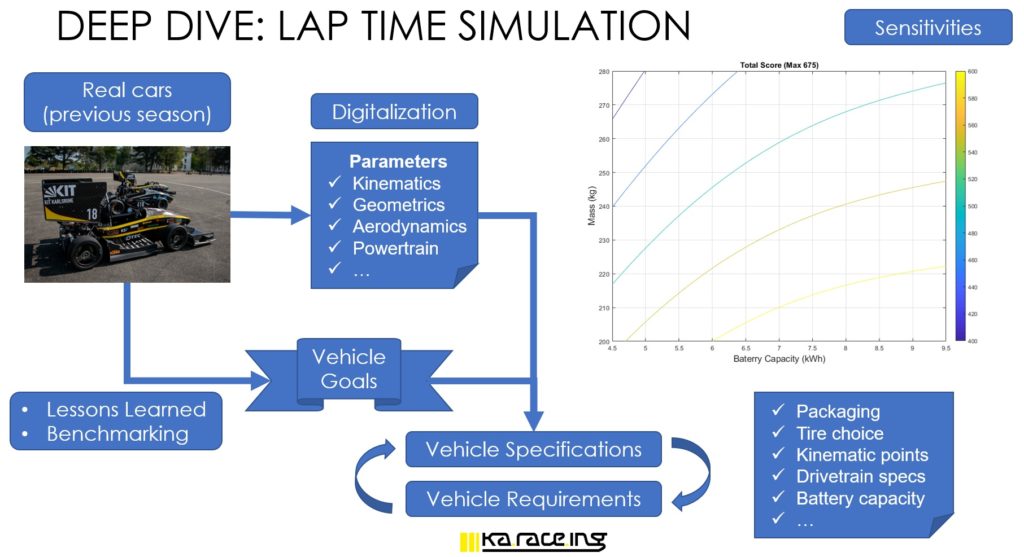
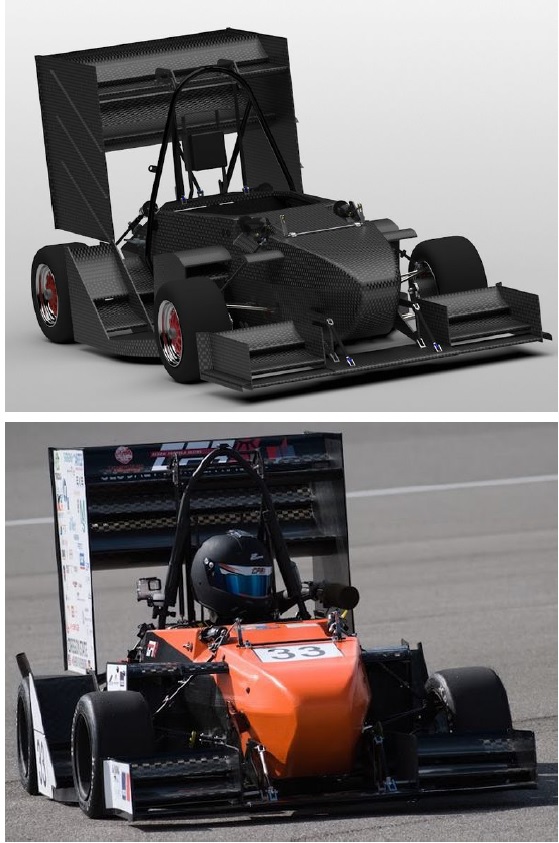
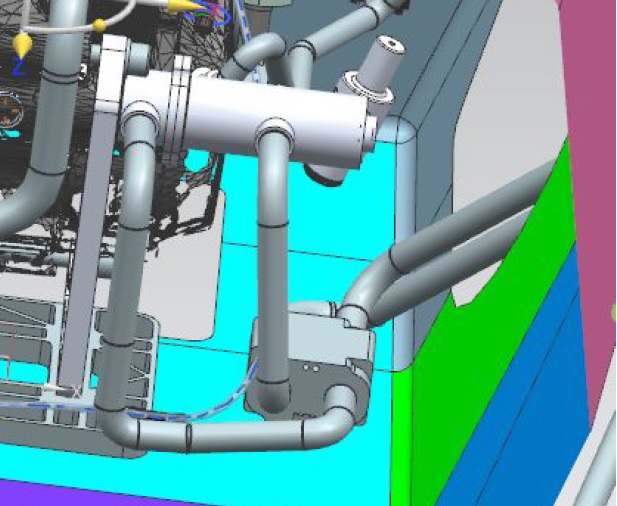
carbon fiber composite chassis would be extremely difficult
without virtual 3D design. Siemens’ NX software is used throughout.
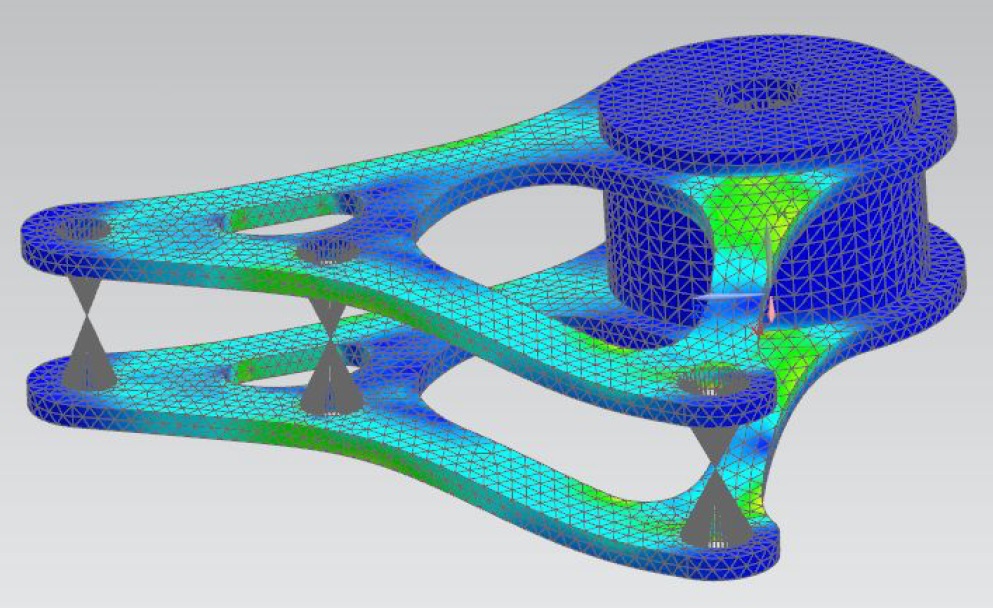
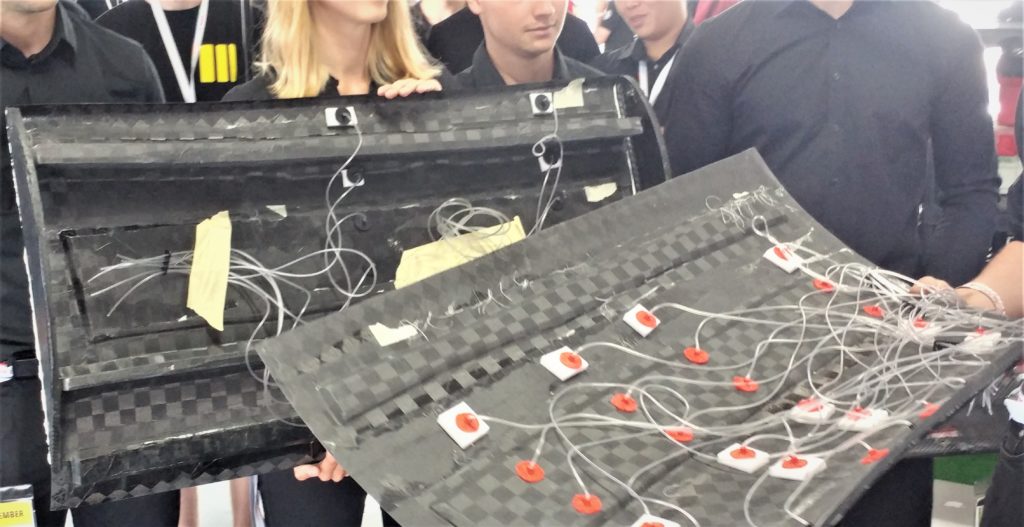
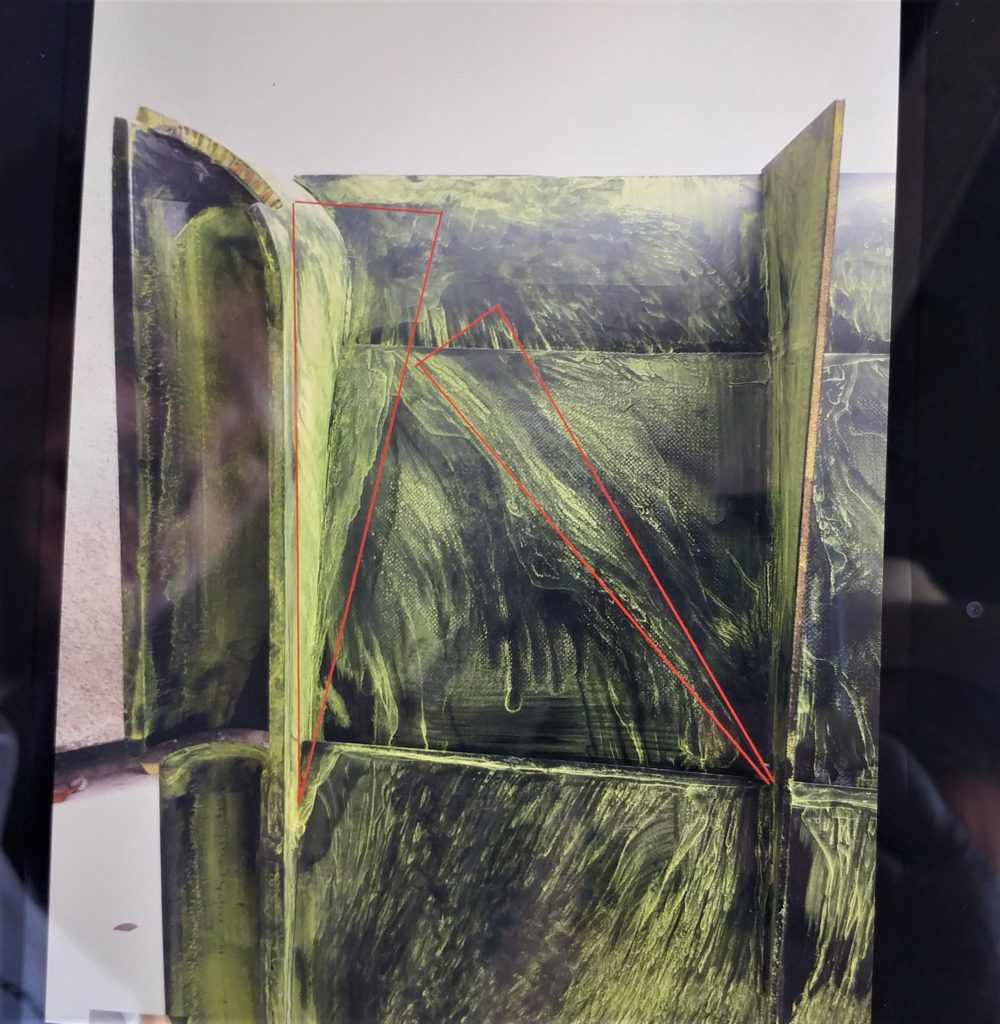
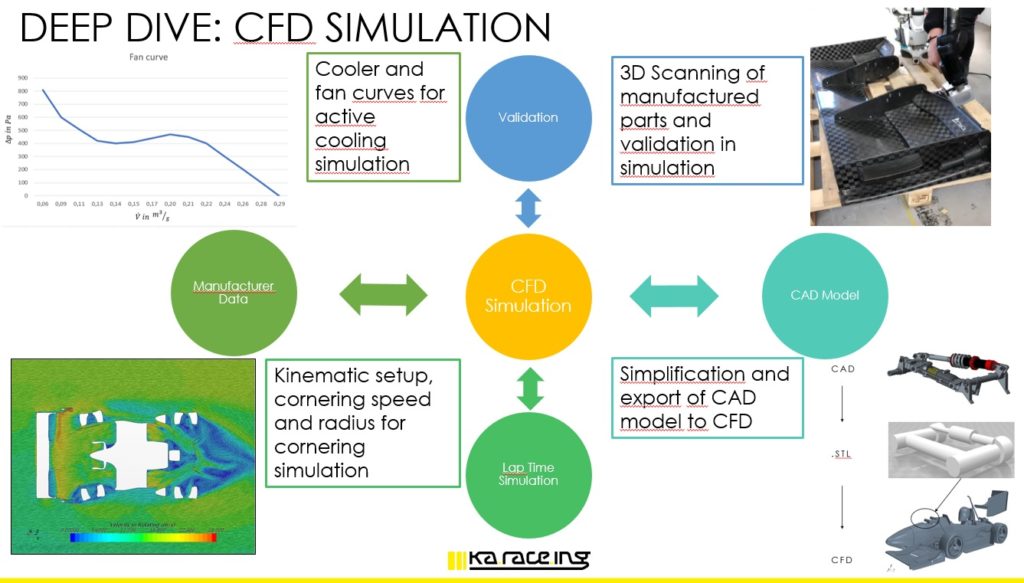
role of CFD simulations, using Siemens STAR-CCM+.
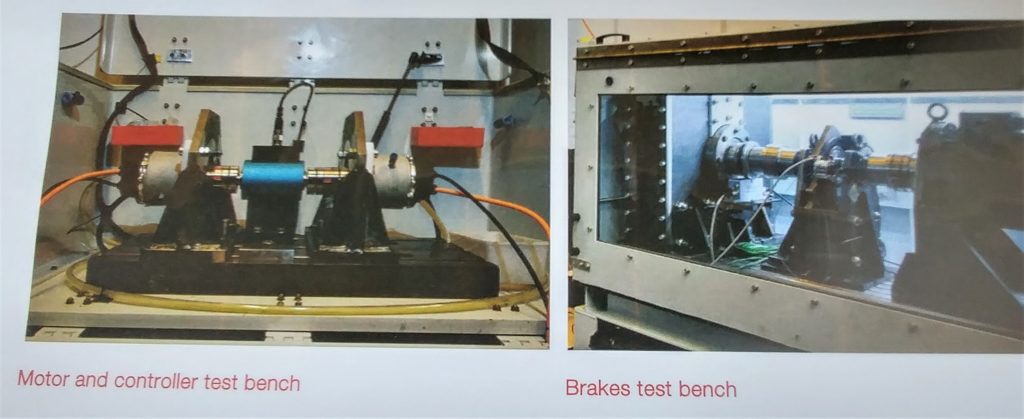
physical and back to virtual. By AMZ team from ETH Zurich university.
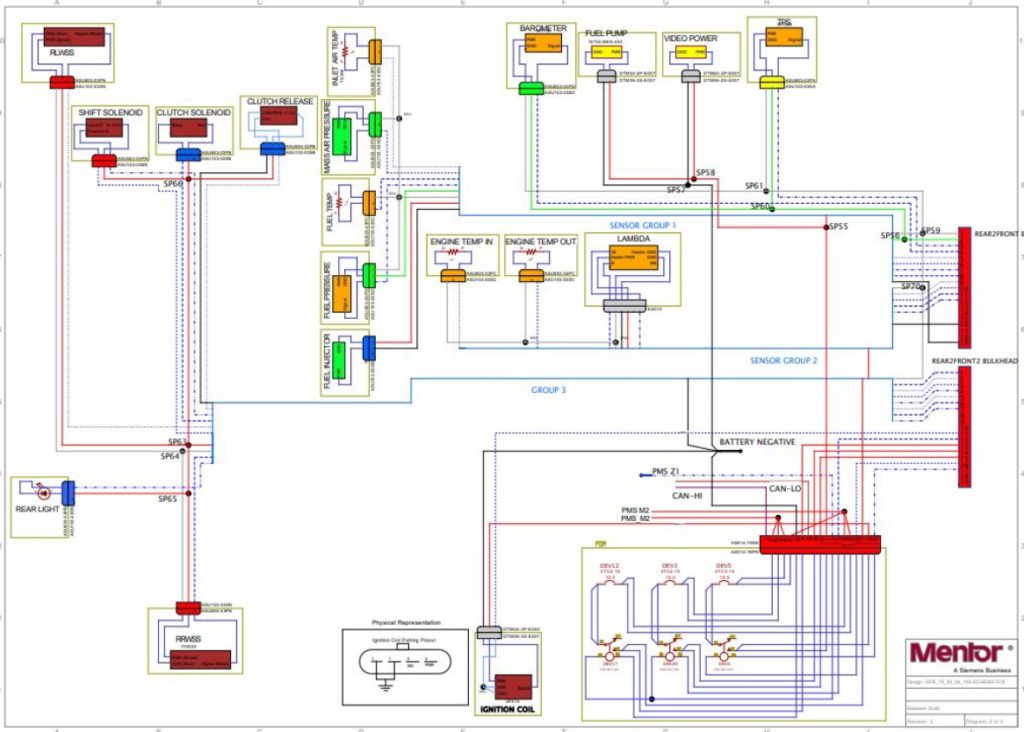
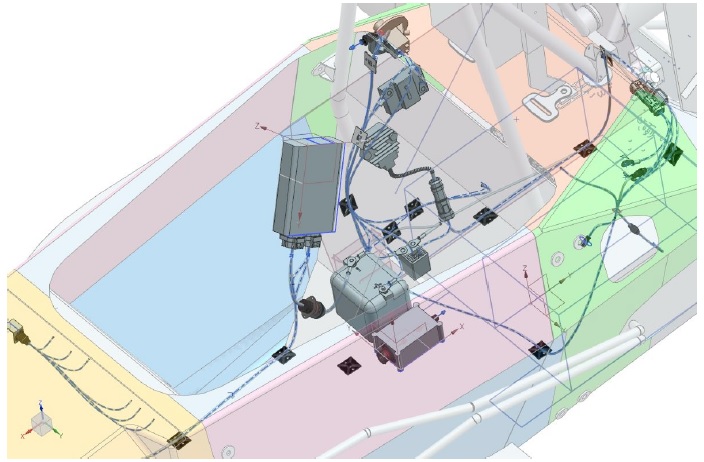
by adding connectors, wire specs. Even the 3D wire-lengths were determined
virtually, using the integration between Siemens-Mentor VeSys/Capital
software and the chassis design in Siemens NX CAD software.
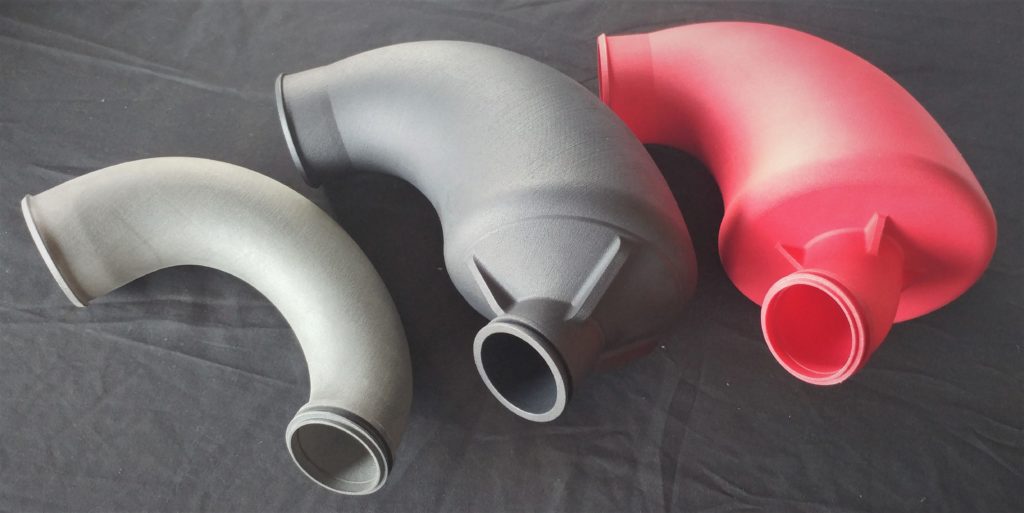
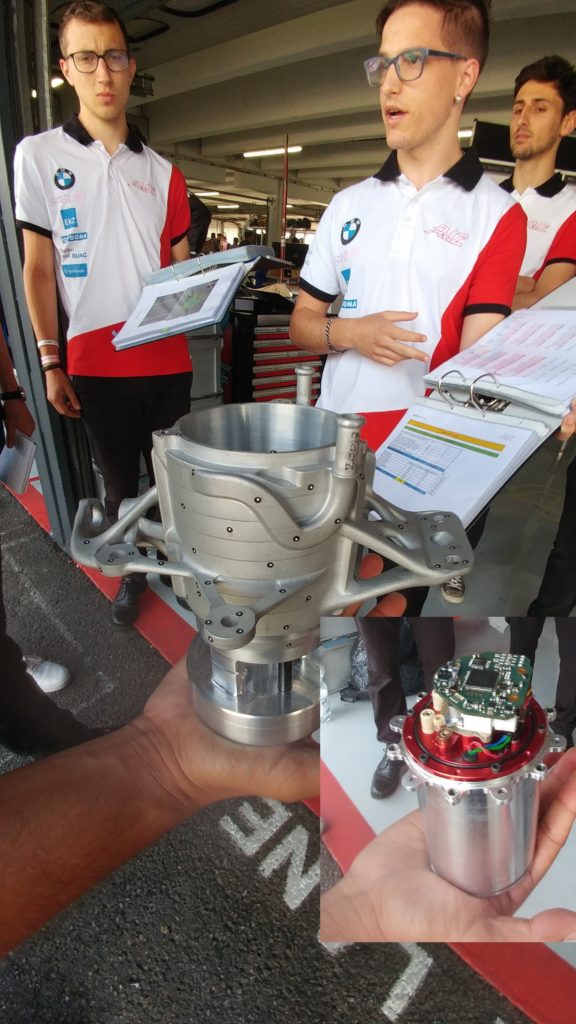
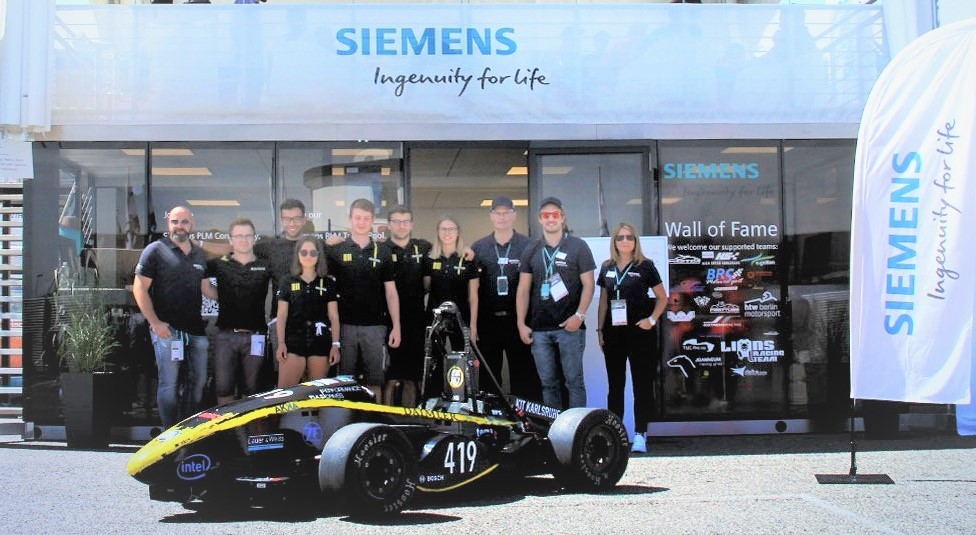
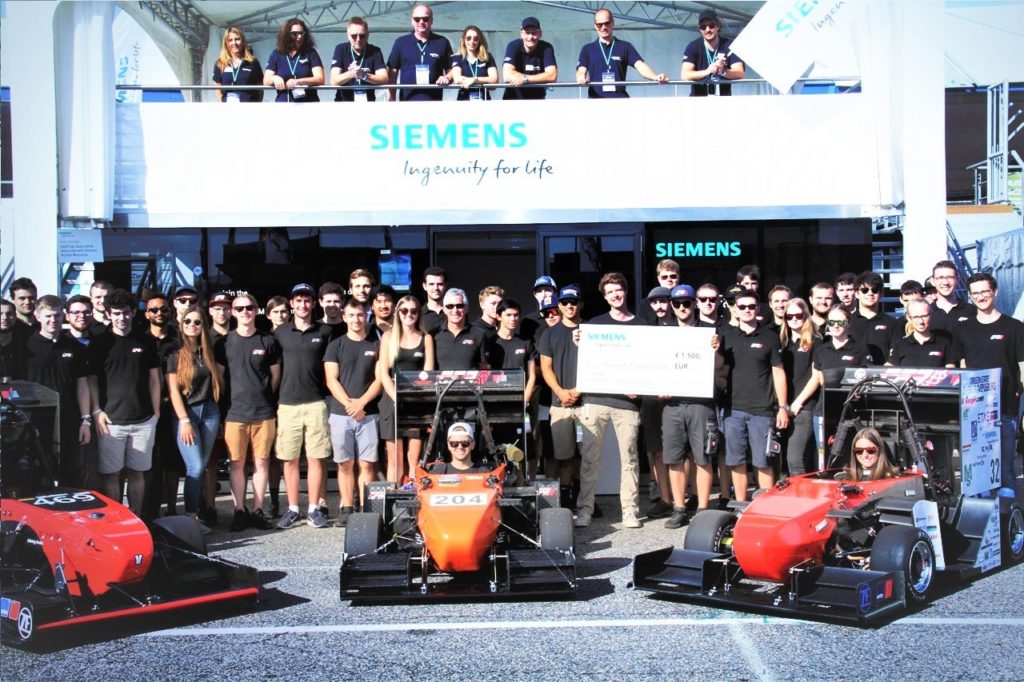
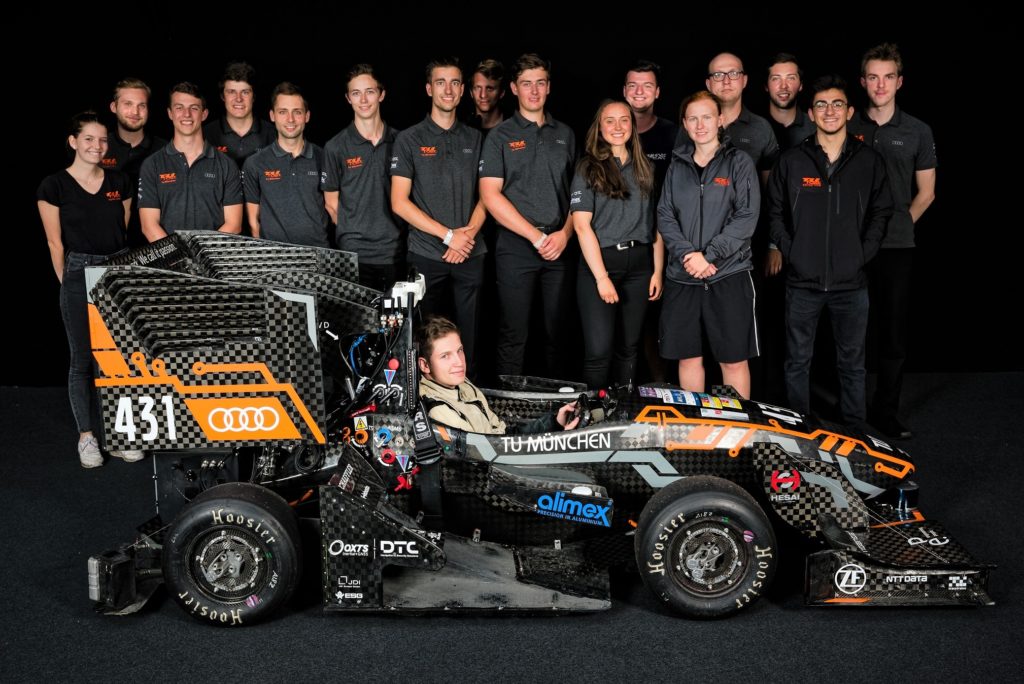
Munich won 2nd place of the Siemens Digital Twin Award in 2018, and the
2019 FSG 1st place overall in the highly competitive Formula Electric class,
with extensive use of Siemens software. ©FSG, Photo by Johannes Klein.
TUfast’s downforce aero package was optimized with Siemens’ STAR-CCM+ 3D aerodynamic simulation software. NX software was used for CAD/CAM/CAE/3D-printing, and VeSys for electrical system/wire-harness design. Note the all-carbon-fiber construction and sophisticated aerodynamics package that enables cornering-power in excess of 2.5 g.
[end]