确保氢能交通的安全性
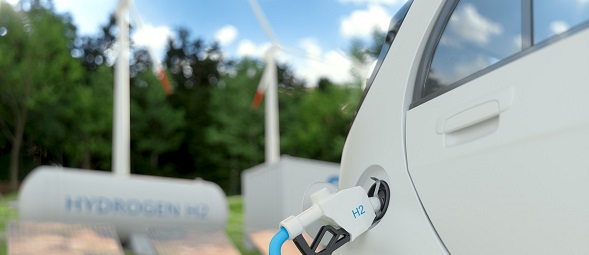
电池还是氢燃料电池?
移动出行电气化并非一种趋势。而是事实。大多数主机厂已经在计划淘汰他们的内燃机车队。但是,谈到电气化,我们通常会将其与锂离子电池及许多固有挑战联系在一起。稀有材料、里程焦虑、充电站匮乏、电池安全、低回收率就是其中一部分挑战。尽管目前正在进行广泛的研究来解决这些挑战,但人们在考虑一种替代方案:氢燃料电池汽车。在本文中,我们将探讨仿真如何帮助主机厂和供应商虚拟 设计和 认证用于氢储存的复合材料压力容器。
氢:未来移动出行的神奇能源供给?
氢是地球上最常见的原子之一,是一种无限的资源;氢能汽车的续航里程通常高于电池电动汽车;氢燃料电池仅排放水蒸气;氢气罐可以在几分钟内重新充满。因此,我们认为燃料电池逐渐成为正式的电池替代品。
在汽车行业,丰田 Mirai 和 现代 Nexo 一直是先驱。宝马即将发布他们的 iHydrogen NEXT,而戴姆勒卡车公司和沃尔沃于 2021 年成立了一家合资企业,“目的是加速推广氢燃料电池的使用”。越来越多的移动出行初创企业也押注氢能。在航空航天业,空客于 2020 年启动了一项 ZEROe 计划,目标是到 2035 年开发出氢能商用飞机。西门子等铁路行业领导者也在开发氢能列车。
这一趋势让许多政府纷纷资助相关研究以发展氢能交通。最近的一个例子是法国于 2020 年宣布“到 2030 年,将投入 70 亿欧元的资金,让法国成为绿色氢能的先锋”。
看起来前景光明......但是,为何“自 2020 年首次销售以来,到 2020 年底,只售出了 27.500 辆氢燃料电池汽车呢”?
需要解决一些技术挑战......
不幸的是,尚未发生任何奇迹。每千瓦时能量的生产都离不开大量的氢气,这就引出了限制氢能规模化的两项技术挑战。
- 氢气生产通常通过化学反应 (SMR) 完成,开始是由甲烷和水生产氢气......还会产生大量的二氧化碳!现在,通过电解法可以更清洁地生产氢气,电解是将水分离成氢气和氧气......但是要用到电!
- 氢气储存必须体积紧凑,才能嵌入车辆中,适应有限的可用空间。这意味着压力会非常高,显然,存储系统必须在任何情况下都能保证完全安全。
这将需要对充电站进行大量投资,导致氢能汽车的成本居高不下。出于所有这些原因,用于电动汽车的氢燃料电池技术仍处于孵化阶段。但这些并非不可逾越的障碍。
在车辆中储存大量氢气
紧凑的储罐技术,在任何情况下都能确保安全
现在,让我们将重点放在解决上述第二个工程挑战:在行驶的车辆上安全储存少量氢气。解决这一挑战的前沿技术就是以 700 巴加压的氢气罐!真正的嵌入炸弹......

一次事故就可能会对乘员及周围相关人员造成致命伤害。显然,这会破坏氢作为未来移动解决方案的品牌形象。这样的事故发生在 2019 年,位置不是在车辆上,而是在充电站,结果造成了两人死亡,摧毁了周围的一切。让我们来反思一下,相较于固定充电站,行驶中的车辆在其生命周期内通常要应对哪些情况(碰撞、误用、数万次充电和放电、极端温度、干旱、潮湿等),这样来看,安全必然是这些储罐的设计挑战。
现今正在开发的 700 巴储罐包含一个确保密封的聚合物内衬,周围环绕着很厚的高强度连续碳纤维复合材料,这为储罐赋予了非常高的机械性能,此外,还有一个带阀门的金属凸台,用于关闭系统及确保与车辆的集成。我们将这项技术称为“IV 型”,指的是第 4 代加压罐,或“复合材料压力容器”。

认证复合材料压力容器需要多少年及多少美元?
确保氢能汽车安全的绝对必要性导致了全球标准均规定了非常高的安全裕度。全球技术法规标准 N°13 是全球主要参考标准之一,例如,对环境温度下的爆裂规定的安全裕度为 225%,这意味着 700 巴的储罐在达到 1575 巴之前绝不会爆炸。可变性导致制造商需要额外增加自己的裕度,最高可达 1700 或 1800 巴。这样可以确保认证测试的成功,并通过数百次复杂的高成本物理测试来检查其储罐的完整性。
环境温度下的爆裂、极端温度下的循环、表面损伤的影响、对化工产品的抵抗力、不同角度和高度的跌落、蠕变、子弹射击和火灾只是安全标准施加的部分测试。许多储罐制造商以典型的迭代方式在内部执行其中部分测试,并假设(或希望)其他测试结果良好。在一个竞争激烈且不断增长的市场中,这种方法早已不再可行。这就是数字化发挥作用的地方。
复合材料压力容器的虚拟设计和认证
容器技术的复杂性和各种认证测试要求我们采用新的方法,我们可以将这些方法集成到 CAE 解决方案中,以实现完全精准的数字孪生为目标。Simcenter 解决方案将工艺与技术融为一体,旨在找到尽可能紧凑、轻量化和经济的理想设计,能够在遵守所有法规的同时,使氢储量达到预期,并在原型制作之前,实现对制造设计的虚拟认证。
CAE 方法的可扩展性
这些创新型 CAE 方法并不属于所谓的“标准 CAE”方法。它们必须将许多不同的物理场纳入考虑之中,有时,在业内尚未达到完全成熟的水平。然而,从事储罐认证的 CAE 分析师的数量通常相当少,而且企业并不具备所有领域的专业知识。Simcenter 解决方案即可以提供简化的自动化方法,使非专业人士能够更快地确定早期概念设计,也可以通过与工业客户合作的研究项目所开发和评估的先进高端方法来对复杂性进行建模。
通过仿真实现的氢气罐早期设计:在几个小时内评估数千个设计
借助 Simcenter,储罐设计师通常会从非常广泛的设计空间探索研究开始,然后得出一个或几个初始设计。我们并未使用常规的近似分析方法,而是将自动化 FEM 工作流程集成到 Simcenter Heeds 的问题中。非专业人士将能够在几个小时内根据认证和设计要求评估数千种设计(具有不同的内衬心轴几何形状、凸台几何形状、材料、复合材料铺层、纤维缠绕策略等)的性能。然后非专业人士就可以确定最终采用的理想候选设计。在这个阶段,仿真仍保持线性特征,或者包含一些简单的几何非线性特征,非专业人士可以使用遵循基本材料定律的简化的高效模型来处理所有部件。后文将介绍通过自动执行集成的第三方工具来考虑光纤铺放。这比分析方法准确得多,同时让效率保持在非常合理的范围内。

Simcenter Engineering 团队(前身为 LMS Samtech)参与了 OSIRHYS IV 研究项目。该项目旨在开发和验证这些方法,与使用分析方法设计的容器相比,这些方法不仅使质量减轻了 30%,还不会影响性能和容量。
复合材料压力容器端到端制造流程仿真对精准虚拟认证的重要性
复合材料压力容器的制造流程将对其最终性能以及这些性能的可变性产生非常大的影响。一旦被忽视,储罐甚至可能在我们第一次使用之前就会失效。Simcenter 解决方案可精准模拟端到端制造流程,对所要制造的容器的性能进行后验评估。
从滚塑成型......
第一步是生产聚合物内衬,采用滚塑工艺完成。内衬的最终几何形状和机械性能在很大程度上取决于该工艺。太薄或设计错误的内衬会破裂,然后在储罐中造成泄漏。而内衬尺寸过大会降低储罐的容量并增加其质量。我们使用 Simcenter STAR-CCM+ 来模拟滚塑成型的过程。这包括温度控制,旨在实现预期的内衬几何形状和机械性能。
......到纤维缠绕......
然后,通过纤维缠绕,将碳纤维按照预定义的方向顺序缠绕在内衬周围。这个过程涉及将纤维缠绕在内衬周围的大型机器。必须处理许多与过程控制相关的变量,这些变量将对复合材料壳体的局部方向和厚度产生非常大的影响[图 6],从而对储罐的整体性能产生显著影响。Simcenter 3D 允许集成第三方专业纵向解决方案,旨在准确模拟纤维缠绕过程。随后,所有需要的制造参数都可以通过特定的 GUI 获得。

......和固化
然后,对储罐进行固化,使复合壳体聚合,但这可能会影响内衬性能并在装配中产生残余应力。在固化过程中,组成储罐的不同材料对温度变化的反应方式不尽相同。Simcenter 3D 集成了热求解器和机械求解器及方法,这些求解器及方法会在固化过程中考虑材料历史,确定工艺诱发的变形,并评估残余应力对产品性能的影响。

复合材料压力容器虚拟认证:完全精准地对复杂性进行建模
您可以使用 Simcenter 3D( Simcenter Mechanical 平台)对认证测试的全部复杂性进行建模。
复合损伤模型以原生方式集成到 Simcenter 3D 中。它能够预测加压和减压过程中发生的局部现象,如分层或刚度降低。其中包括用于复合材料的创新型静态和疲劳方法,这些方法通过工业项目得到开发和验证,适用于复合材料压力容器。
热机械模型可用于评估温度与不同机械载荷工况下的影响。瞬态动力学求解器用于计算标准跌落测试中储罐的强度。通过研究项目 FireComp,我们也对防火性进行了研究。最后,Simcenter 嵌入了多尺度仿真,旨在说明材料在宏观仿真中的微观行为。这样一来,模型的最大保真度便可一目了然。
以上所列并未穷尽所有情况。集成式平台的优势是我们可以在一个平台上执行所有载荷工况。一个用户可以访问同一环境中的所有 KPI。

氢能交通的未来发展之路
如果大多数分析师都预测电池电动汽车将在小型私人乘用车中保持领先地位,那么我们预计氢能解决方案将会越来越多地 在公共汽车、卡车、火车、轮船或叉车等大型车辆中实施。原因是它们有足够的空间容纳压力容器,而用于为它们供电的锂离子电池太重。
参与生产用于储氢的复合材料压力容器的企业需要预见到这种扩张趋势。竞争将会非常激烈。成功的企业是先驱,而不是追随者。借助 Simcenter,他们可以对其压力容器的数字孪生建立完全的信任。Simcenter 团队持续在研究方面投入大量资金。我们正在与本田汽车研究开发有限公司等工业客户合作,以尽可能降低预测的不确定性,创建一个真正的数字孪生。这些合作有助于减少认证前需要执行的物理测试,且有望有朝一日完全抛弃所有这些物理测试,以可靠、经济、即时的仿真和优化将其取而代之,所有这一切都集成在一个仿真平台中。
显然,安全性还与容器集成到车辆中的方式和位置有关。它必须要能避免典型碰撞场景,同时,还要保证车辆重量、NVH 或动力学行为也不会受到影响。Simcenter 可提供集成而精确的{86}电动汽车数字孪生{87},用于解决所有车辆领域中面临的挑战。但那是另一回事了!