Open your shop’s doors to new markets with adaptive systems
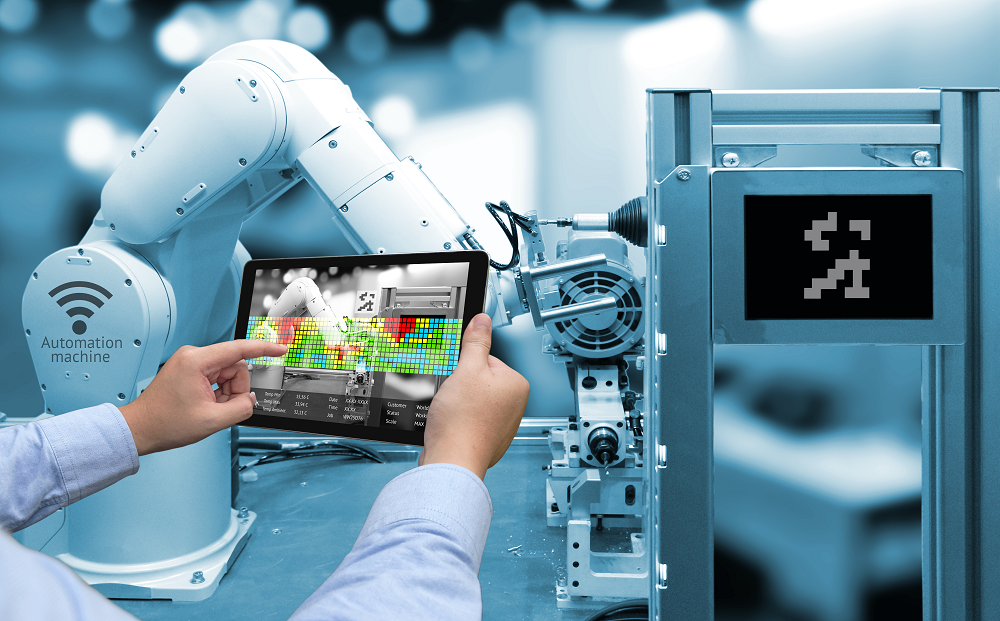
Machine shop owners hate waste. They are hawks on machine downtime, bristle at the time lag during functional hand-offs and go ballistic when mistakes threaten delivery delays. Yet too many machine shops get by with time-wasting workflow workarounds that leave little time for improvement, let alone for scouting new markets or creating new innovations.
The problem machine tool owners face is similar to what lean manufacturing practitioners call “islands of excellence,” which describes a situation where each step in a production process is optimized, leaving the hand-off between processes disconnected.
In the digital world, a similar problem arises from “islands of automation.” For example, the CAD, CAE, CAM and ERP systems are routinely upgraded, yet communication among the applications remains a manual process. Data is maintained in spreadsheets and shared on paper, memory sticks and other uncontrolled file systems. Critical information, such as the engrained and emerging knowledge of team members, remains undocumented. With no data available or easily accessible from previous projects, each new project starts from scratch, needlessly lengthening time-to-delivery.
But using a product management platform that integrates these islands eliminates the waste created from disconnected data and, in doing so, builds a system that is inherently adaptive, ensuring machine shops meet increasingly stringent—and fast-changing—market expectations and customer demands.
At the heart of modern product management and manufacturing are digital twins, virtual replicas of planned or existing products that are part of an integrated digital thread that connects functions and applications—from costing to production.
This end-to-end integrated system offers:
• Real-time communication and data sharing
• High-performance computing that enables fast analysis of data and easy-to-understand derivative guidance
• A secure, unified data store where accumulated knowledge is preserved and made accessible
Such a system can share data with every software application, machine, robot and other equipment, as well as with people. When teams work together with the same data, process and resources, and share their collective know-how, machine shops more easily solve problems, improve shop performance and prepare to capitalize on new manufacturing technologies.
Solving shop problems
Reducing process errors is among the first and most obvious problem that an integrated product platform solves.
Because the digital thread captures and stores all data related to all stages of a product’s development and production, the design and analysis information is always available. This eliminates process variability and errors caused by inefficient data hand-offs and inaccessible best-practice information.
As well, by eliminating data flow gaps between job functions and shop floor equipment, the digital thread increases accuracy and efficiency. Process owners, for example, can immediately access data in the digital thread through an integrated application to quickly confirm machine set-up.
Finally, with a digital thread, machine shops are able to quickly respond when their client requests a design change. With all the data integrated into a unified system, digital machine shops work with one set of data, so the change automatically propagates throughout the process.
Consider Freeform Technology’s approach. The UK-based company supplies composite-parts manufacturing services and parts for the Formula 1 automotive industry. Leveraging a unified platform for design, production planning and machining of parts, the company was able to standardize processes and shorten cycle times. Today they can go from CAD drawing to finished part in less than 24 hours.
This “locked down” model is enabling Freeform to expand into the general automotive industry, as well as the medical and leisure industries. The shop is now like a well-tuned engine with consistent, reliable performance so that variation is easier to absorb, whether it’s from a change order from an F1 customer or a customer from an entirely new industry.
Improving shop performance
But solving problems is just the start. By adopting an integrated product-lifecycle platform, machine shop owners are able to focus on improving shop performance and growing the business. Owners that have digitalized their business report shifting their attention toward the following:
• Growth and innovation: With traditional disconnected data systems, machine shops are forced to deploy their most valuable assets—their manufacturing experts—to produce and deliver product through seemingly never-ending fixing, fire-fighting and expediting. With advanced knowledge available to everyone at all times in the digital thread, experts are freed up to focus on finding new customers and new markets.
• Upskilling inexperienced workers: As new best practices are captured and made available to everyone, not just manufacturing experts, less experienced workers take on more advanced work.
• Driving profit: With fewer errors, better accuracy, increased efficiency and more effective resource utilization, machine shops deliver more complex and higher quality products more quickly at less cost. These savings can both improve competitiveness and boost margins.
• Preparing for the future: Industry 4.0 systems are inherently ready to work with new manufacturing technologies, because they digitally and seamlessly connect with additive manufacturing, advanced robotics and automation, as well as emerging technologies such as artificial intelligence and virtual reality.
Siemens’ customer Hoedtke GmbH & Co KG, for example, describes how Siemens NX software suite is crucial to its successful move to additive manufacturing. Hoedtke employs a laser cladding process, an additive process that quickly produces “coarse” components three dimensionally. Then the parts are milled to ensure accuracy.
“Only with Siemens NX are we able to prepare the data accordingly for the additive and ablative processes,” according to the company, which stressed that software simulation is critical to the process because even minor shocks on the spindle or laser-head would cause enormous damage.
“We have a dream that we want to realize little by little, to proceed fast from a virtual model easily to the production of 3D contours on the machine,” Hoedtke said. “This is only possible when using excellent software and data with parameters that fit for additive processes.”
Bottom Line: Adaptive systems feed growth and survival
The digital machine shop—one that uses integrated product development and production solutions—is better able to adapt to meet fast-changing market expectations and customer demands, and move quickly to exploit new manufacturing technology.
This concludes our introduction to the digital machine shop.
About the author
Sashko Kurciski is a senior marketing manager at Siemens PLM Software. Sashko leads the marketing of the part manufacturing software solutions to help companies transform their production processes through digitalization. He has been in the CAD/CAM/PLM software industry for almost 20 years, working in a range of roles, including product management and software development. Sashko holds a master’s degree in Mechanical Engineering from the University of Arizona and lives in southern California, USA.