Automotive regulatory compliance in need of a new approach (pt. 3)
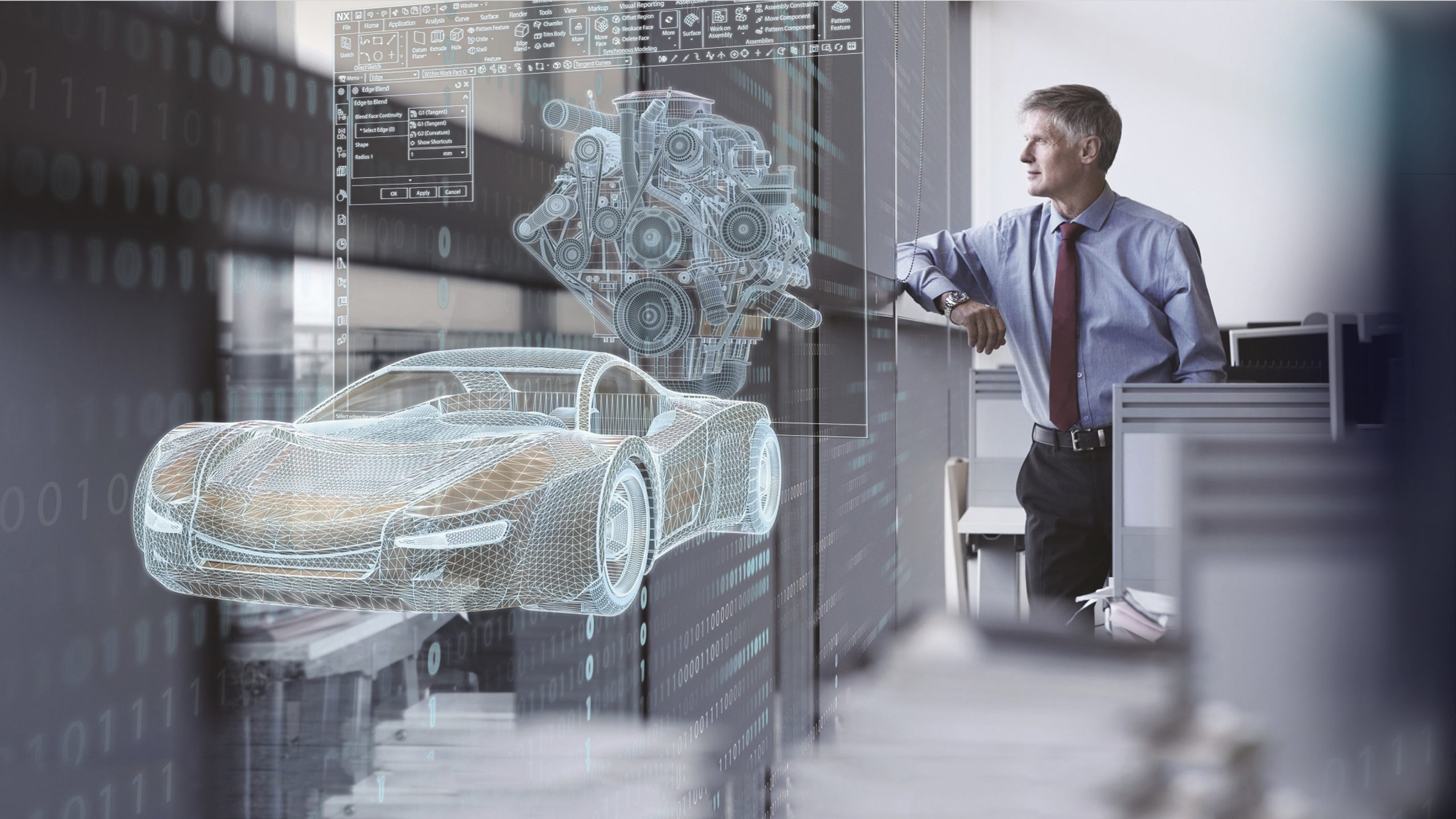
In parts one and two, we explored the changing landscape of the automotive industry due to growing vehicle complexity, and mounting pressure from regulatory bodies. Automotive technologies such as electrification, autonomous drive, ADAS, and vehicle connectivity are driving significant growth in vehicle complexity from sophisticated electronics and the embedded software they require. The development and integration of these technologies into new vehicles creates new safety requirements that contribute to, along with climate change, an increasingly stringent regulatory environment.
As vehicle complexity and the consequences of missed requirements grow, automakers must build a holistic management structure for vehicle verification processes. This is no longer optional, as evidenced by recent, highly publicized punishments, including heavy fines or criminal prosecutions, handed to automakers that failed to meet requirements. Even a small spike in warranty claims from a temporary error can impact companies economically and, more importantly, damage their reputation.
The method and scope of managing vehicle verification is even more important. Many automakers have been using some form of verification management for years, even decades. However, these legacy processes are not holding up to the challenges of developing tomorrow’s vehicles.
Past methods will not hold up to future challenges
Traditional verification management fails to organize information coherently and, therefore, will no longer meet the demands of an evolving regulatory environment. In traditional verification management processes, documents are distributed and stored in email systems, records are maintained locally on laptop hard drives and test results are stored in network attached storage (NAS) devices or, worse, on paper in filing cabinets. None of this information is tracked or managed in a consistent or structured manner. This method of verification management does not offer a robust process for managing today’s technology and compliance demands.
Due to its unstructured nature, traditional verification management often creates confusion and uncertainty in the process of testing and verifying vehicle systems. Verification engineers are frequently left wondering:
- Where relevant data is stored
- Is the data up-to-date
- Have they verified everything
Where is my data?
The first critical issue verification engineers must address is locating all of the data, information, requirements and targets they will need to complete a request. Typically, when a verification request is submitted, the engineer is informed about a given part or system to be tested. Whether the request is for a CAE simulation or testing the performance of a physical part, the engineer has to locate additional critical information before they can complete the test. This information may include simulation requirements, parameters and targets for virtual testing, or the correct design level of parts to order and instrumentation calibration for a physical test.
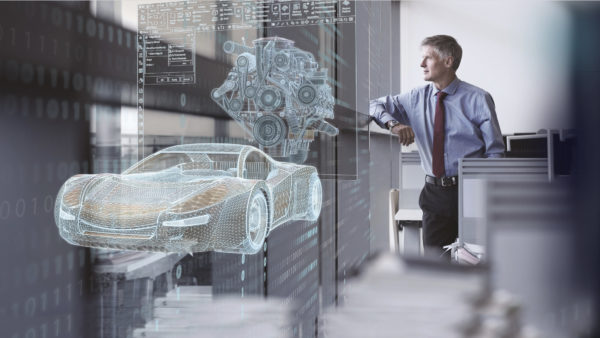
More often than not, locating the critical information needed for verification requires a full-fledged expedition, taking days and even weeks. This can include phone calls, emails, in-person visits to colleagues or digging through NAS drives and even file cabinets. What should be a straightforward task quickly becomes multiple days-worth of effort, delaying development.
The imminent arrival of EVs and growing ADAS and autonomous features will only make locating relevant information more difficult. These technologies are expected to flood engineering and development teams with additional design and development work. Without a coherent verification management methodology, engineers will endure these data scavenger hunts with unacceptable frequency. The result is lost time, greater development cost and, of course, frustrated engineers. The vehicles of tomorrow require more robust verification management today.
Is my data current?
Once the information is found, the engineer is not yet out of the woods. The digitalization of the product development cycle enables companies to become more agile in response to change. Requirements, targets, design levels and part numbers all start to evolve as development progresses. In the past, the product development cycle was lengthy and resistant to change. This often resulted in products that were antiquated or obsolete the minute they hit the market because engineers were unable to adapt to dynamic market demands. In the current consumer-driven era, product requirements, targets and designs are now in constant flux as companies attempt to meet market demands as they evolve. A growing trend towards enterprise-level digitalization has enabled faster product design and iteration, but it also allows for constant design change.
This is also true for automotive companies. As vehicle programs begin, change will become a constant. The requirements, targets, design levels, part numbers and other information the verification engineer worked so hard to collect will all evolve as development progresses. By the time the engineer can test, verify and validate a product, system or part, the critical information or physical part is often out-of-date. This leaves the verification engineer to repeat the process, further delaying product verification.
Did we verify everything?
Finally, traditional verification management processes cannot provide a comprehensive picture of the completeness of vehicle verification. Modern vehicle development programs contain hundreds-of-thousands of requirements, tests and targets across engineering domains and virtual and physical testing environments. Today, program managers and verification engineers do their best to certify that each of these myriad of tests is completed (and done so accurately), and that the results meet requirements and targets. But, the sheer number of elements that need to be managed and the lack of organization in how or where information is stored prevent managers and engineers from constructing a complete picture of the status of verification. Errors and mistakes are bound to slip through the cracks.
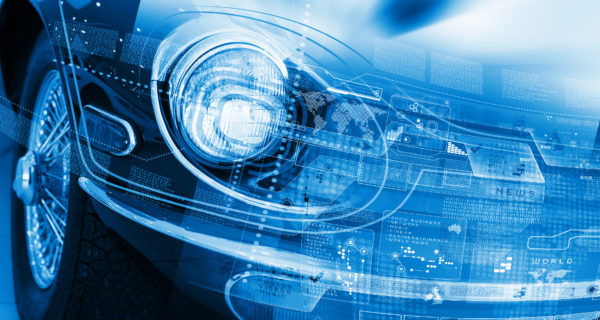
What is needed?
Companies that continue to rely on inconsistent, ad hoc methods of verification management will put themselves at significant risk of releasing faulty or non-compliant vehicles in the future. Today, the entire product development ecosystem needs to have access to all product data, requirements, targets and more, stored in a digital environment.
What is required is a real-time digital thread that ensures every stakeholder has access to the latest information, which is accessible in a unified and user-friendly environment. In sum, ‘just-in-time’ information. Furthermore, this digital thread should integrate with design, simulation, testing and lifecycle management solutions, blurring the boundaries between engineering and process domains and guaranteeing that information is accurate and constantly updated to reflect design changes.
In part four, we examine these and other characteristics that will make up a modern verification management solution.
Comments