Bringing clean and profitable batteries to Europe through Norway
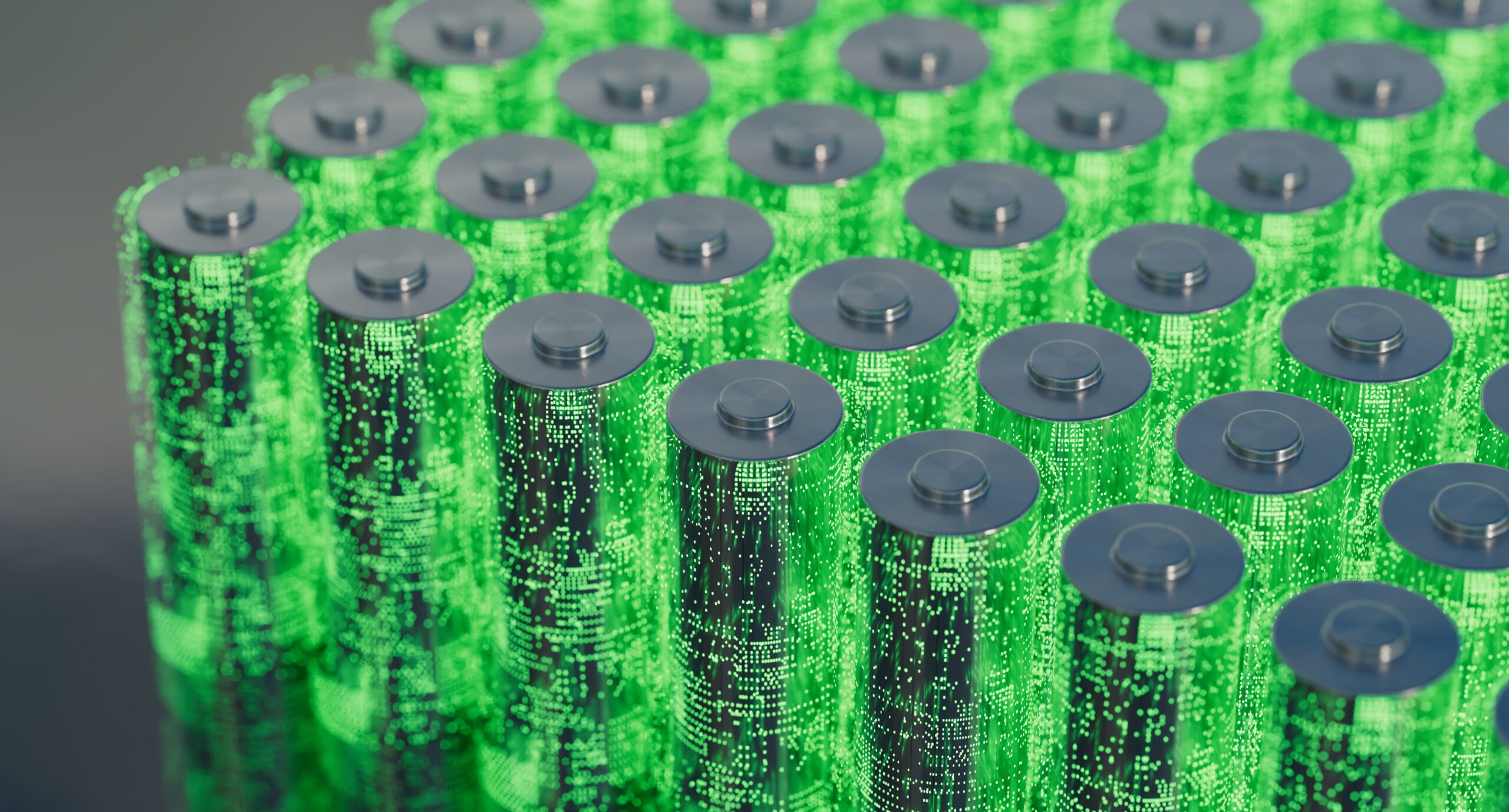
Electric vehicles have occupied a very prominent spot in our collective understanding of the growing battery market. While it is a very important sector given the volume of cells needed to meet the goals of transportation and it represents a major shift from the most common applications of batteries in electronics, EVs are not the complete story. Batteries have a role to play in the whole energy transition as we move away from carbon intensive systems. But there is a challenge in fighting climate change with battery storage – it can be a very energy intensive manufacturing process.
To talk about this challenge and how businesses are working to make green batteries a reality in Europe we sat down with our customer Morrow Batteries out of Norway. You can listen to the complete conversation below, but continue reading to get a summary of some of the most important points from their discussion at Hannover Messe 2024:
There are two general areas on battery manufacturing that need to be improved for the delivery of green batteries. The part often talked about in public is the impact of mining these resources. Much of the work that can be done here lies in creating collaborative and transparent supply chains to give manufacturers and customers both insight into their products and an incentive for each step of the value chain to work towards greater sustainability outcomes. That is impossible for an individual company to handle, but there are actions to limit impact once materials reach a factory floor.
Yield is a very important metric for battery manufacturers, denoting how well a business can meet customer demands, throughput requirements, and for green batteries – efficiency. Higher yields lower the scrap and remanufacture rates of manufacturers saving valuable material, lowering operational expenses, and reducing the impact of the raw material extraction on a per unit basis. Making this a reality starts with digitalization and the use of simulation to iterate on designs and processes in the virtual world. By understanding how machine or feed stock will interact with the wider system, businesses can work out some of the very expensive lead times for new products, lines, and factories.
The other major area for improvement in battery manufacturing is energy use. Creating a unit of battery capacity is very energy intensive. Depending on where it is being manufactured, the energy mix on the grid can dramatically change how sustainably a cell can be manufactured. This is part of why EVs are so popular in Norway and why Morrow Batteries has such opportunity to bring clean batteries to more of Europe. The use of hydroelectric power generation in much of the country brings lowered carbon emissions and lower costs for electricity. Cutting out the Scope 2 emissions from energy providers makes batteries and the products they power more sustainable as well.
But cheap and clean power only goes so far, it doesn’t solve the problem of growth. There are only so many liters of falling water that can produce electricity. The other half is making everything more efficient – the manufacturing processes, lines, and plants – even the creation of additional manufacturing capacity to meet market demands. Morrow is commissioning their first giga-factory in the region, but even the giga-scale can only deliver batteries for 15,000 vehicles. The goal is to find what works and optimize the models they use for scaling operations.
The last point in making batteries more sustainable is the distances they travel. While there are regulatory and political motives for moving manufacturing closer to Europe for European customers, the impact of logistics is a real boon for localized production. Reducing the distance traveled as freight reduces the consumption of fossil fuels and associated emissions from the deliver vessels.
There is so much more these experts covered in their discussion and if you are interested in the world of sustainable battery production I would recommend listening to the complete discussion. If you want to dive deeper or in a different direction in the battery industry, be sure to check out our website Siemens.com/battery.
Siemens Digital Industries (DI) is a leading innovator in automation and digitalization. In close cooperation with its partners and customers, DI is the driving force for the digital transformation in the process and manufacturing industries. With its Digital Enterprise portfolio, Siemens provides companies of all sizes with all the necessary products, along with consistent solutions and services for the integration and digitalization of the entire value chain. Optimized for the specific requirements of individual industries, this unique portfolio enables customers to enhance their productivity and flexibility. DI continuously extends its portfolio to include innovations and the integration of future-oriented technologies. Siemens Digital Industries, with its headquarters in Nuremberg, has a workforce of around 72,000 people worldwide.
For more information on Siemens Digital Industries products and services, follow us on LinkedIn, Facebook, Twitter, and YouTube.