Manufacturing Reimagined: Siemens and Deloitte’s Smart Solutions Drive Efficiency and Sustainability
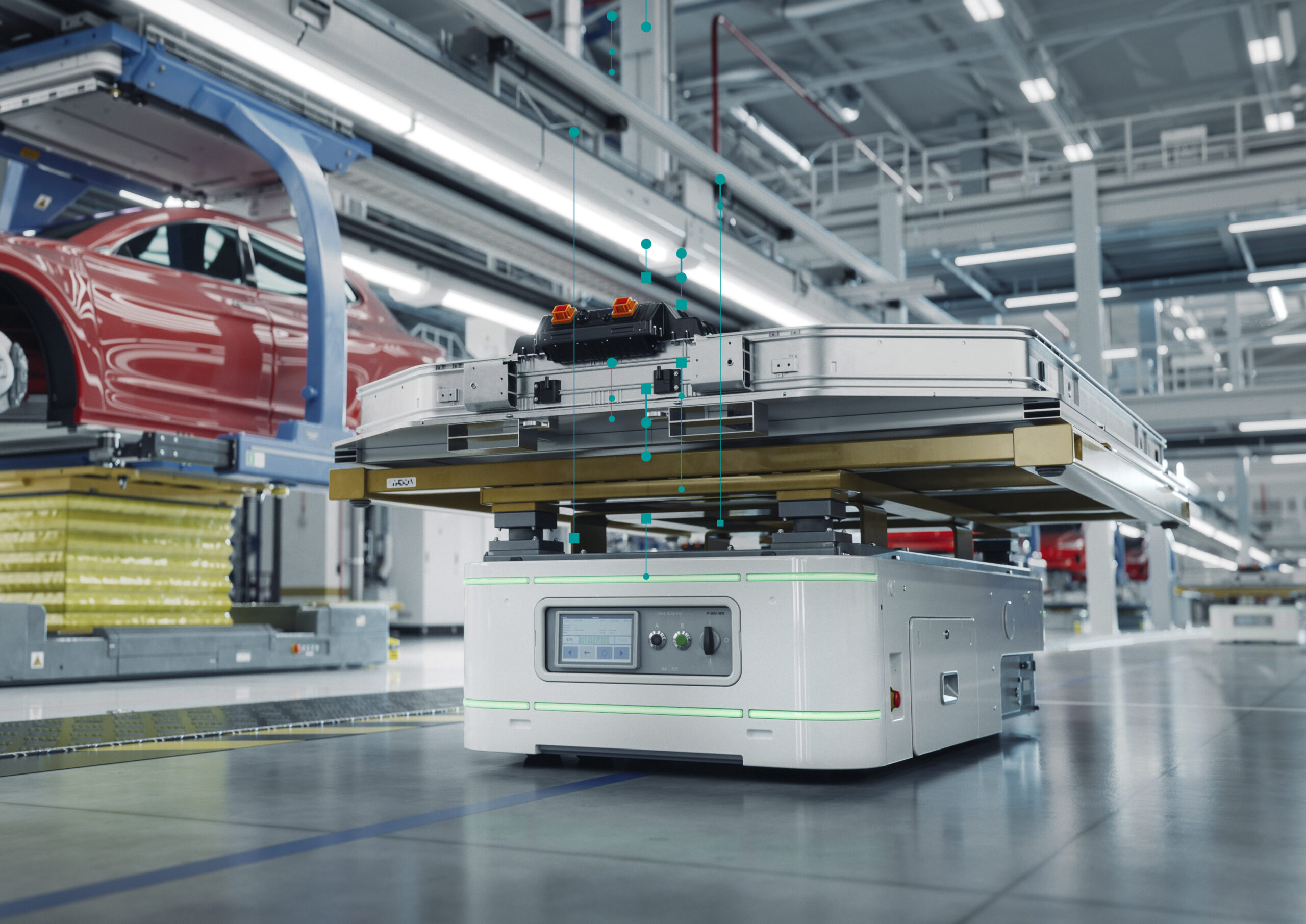
Today’s manufacturers are under considerable pressure. They must bring new products to market quickly to remain competitive. But they must balance that speed with cost reductions while addressing customer and investor demands to minimize environmental impact.
Conventional manufacturing business models, however, offer companies few opportunities to make significant improvements to bolster efficiency, economy, or sustainability. Siemens and Deloitte both recognize these shortcomings. The Siemens and Deloitte alliance provides manufacturing organizations with smart manufacturing capabilities to distribute their manufacturing, reduce production inefficiencies and simplify supply chains. Then they can manage costs, shorten delivery timelines, and maximize sustainability across the product lifecycle.
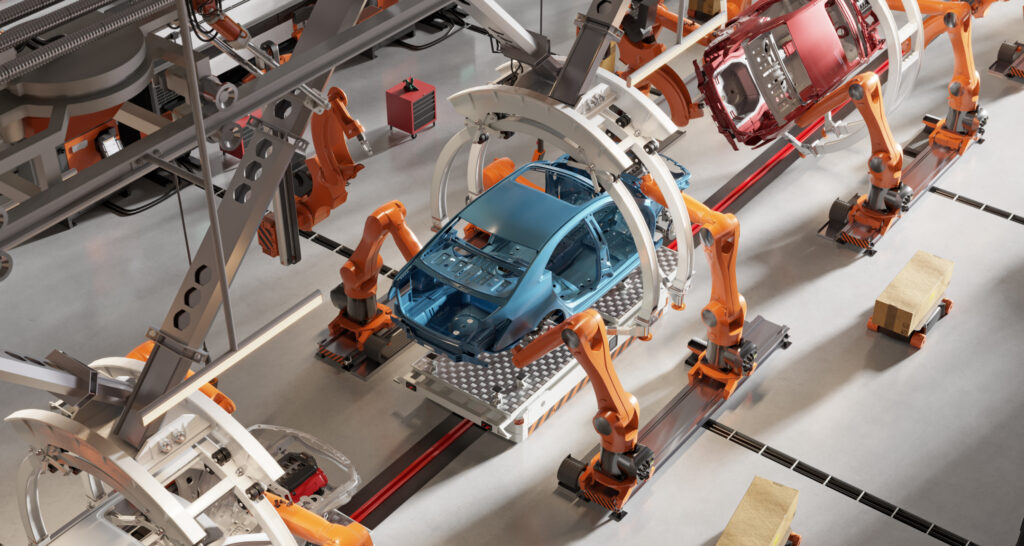
THE DRAWBACKS OF THE CONVENTIONAL MANUFACTURING APPROACH
Traditional manufacturing strategies rely on large, centralized factories as well as complex, often sluggish supply chains.This makes it difficult for the average organization to identify opportunities to reduce costs, minimize its carbon footprint, strengthen its supply chains, and prevent or mitigate the risk of any business disruptions.
In the traditional approach, factory production lines, usually found at a fixed, centralized location, are typically inflexible and capable of making only a single product. Once made, products are then shipped thousands of miles, only to be stored in warehouses before being delivered to buyers. This traditional approach directly contributes to high (and unnecessary) costs, increased carbon emissions, and complex supply chains prone to disruption.
This model relies on two key assumptions: that borders will always remain open and shipping costs will remain stable. But, as recent years have shown, these factors often change without warning. Then companies must scramble to find alternate, often more expensive methods to manufacture, ship, and store their products. Supply chain disruptions, which are becoming more and more frequent, lead to longer delivery timelines and delays that increase costs and can put customer relationships at risk.
This traditional model also boasts a large carbon footprint. Given its general lack of flexibility, companies face an uphill battle as they look to improve production efficiencies, reduce environmental impact, and meet both internal sustainability goals and external government and industry regulations. Companies that continue to adhere to this model risk damaging their reputation and losing business to competitors.
Digitalization provides manufacturing organizations an opportunity to make marginal improvements in efficiency and sustainability. However, these incremental gains simply aren’t sufficient to address the challenges that manufacturers face presently—and will face in the future.
TAKING A MORE PROGRESSIVE APPROACH
Siemens and Deloitte have come together to enable an alternative to this outdated manufacturing model. They are promoting the use of software-defined manufacturing to help manufacturing organizations design and operate more efficient and flexible factories, and to unlock the ability to make anything, anywhere.
This both shrinks the distance between where a product is made and the location of the buyer who needs it and reduces the time between when the product is made and the moment that the buyer needs it. A real time production network of software-defined facilities enables on-demand manufacturing at point of need, that minimizes both supply chain complexity and the risk of disruptions as economic and geopolitical conditions continue to evolve.
Siemens’ suite of manufacturing solutions can help companies quickly adopt and deploy industry 4.0 technologies and solutions, including predictive analytics and the industrial internet of things (IIoT) capabilities. Then companies can create comprehensive digital twins of products, modular machinery, production processes, and production facilities, all of which empower them to plan, simulate, and optimize operations without wasting resources on physical builds and testing.
Digital twins allow executives and engineering teams to explore numerous “what-if” scenarios to determine the optimal factory layout and throughput, manage costs and materials handling, and reduce complexity. They can also use the digital twin to support more efficient supply chain management. With these technologies in place and the support of Deloitte’s extensive digital transformation expertise, companies can develop a distributed network of flexible smart factories that are no longer bound by hardware constraints. Instead, companies can update the behavior of a facility to create custom products on demand without the costs and disruption associated with traditional methods.
This new progressive model also empowers manufacturing organizations to identify new ways to minimize emissions. They can shrink their carbon footprint while simultaneously increasing their flexibility, simplicity, and efficiency.
CONCLUSION
Balancing production, costs, and sustainability remains an ongoing challenge for today’s manufacturers. Traditional models of fixed factories and long, complicated supply chains do not permit the agility required to compete in today’s market. Siemens and Deloitte, however, have formed a unique alliance to help manufacturing organizations take a more modern approach. Using a winning combination of advanced technology solutions and digital transformation expertise, the partnership empowers companies to gain the flexibility needed to increase efficiencies, reduce costs, and become more sustainable over the long term.
To learn more about how Siemens and Deloitte are transforming manufacturing and pursuing a more sustainable future, watch the video by Tim Gaus, Deloitte Smart Manufacturing Business Lead, Principal, Deloitte and Alastair Orchard, Vice President Digital Enterprise, Siemens:
For more, visit: https://www.sw.siemens.com/en-US/partners/find-a-partner/deloitte/ or Deloitte and Siemens Alliance | Deloitte US