A decade of battery innovation – The Battery Podcast S01E07 – Transcript
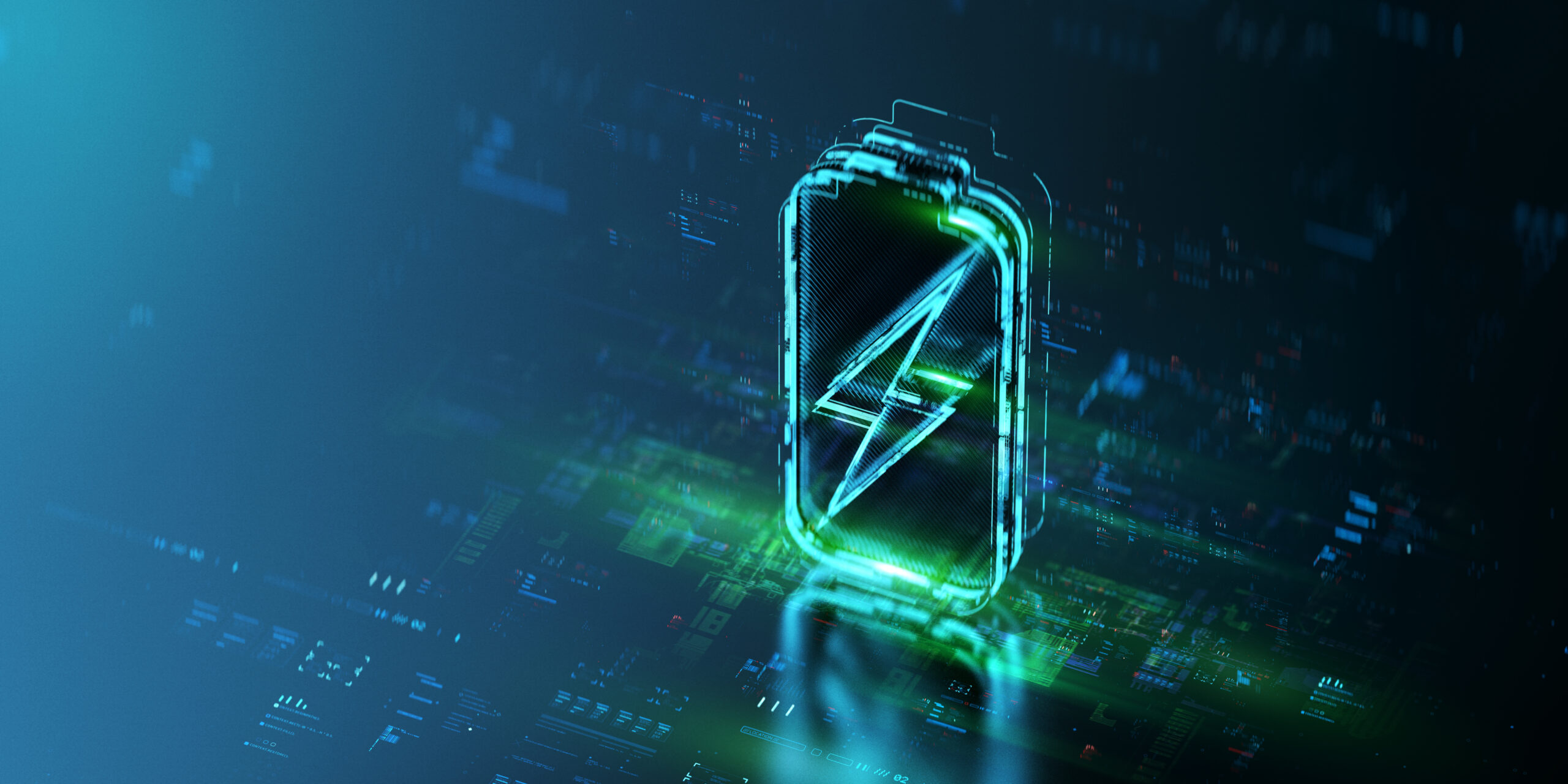
For S01E07 of The Battery Podcast, our host Marc Deyda sits down with Adrian Spillmann – the Market Segment Director of Battery at Bühler. Listen in or read along to these experts talk about the world of battery.
Nick Finberg:
Welcome to The Battery Podcast from Siemens Digital Industries. As part of our running series from battery events around the world, we have Marc Deyda to talk batteries and production from the show floor. Here is Marc and Adrian Spillmann, the Market Segment Director of Battery at Bühler, to talk about cell production.
Marc Deyda:
Sit down, Adrian, it takes the time, 15 minutes, we just talked about the real life, so real machines. And therefore we invited our customer, Bühler, who already delivered a lot of machines and real battery production sites. And we know us since 10 years, longer than 10 years, so it’s already a long journey. And yeah, he lost hairs, my ones are getting gray, so that’s life in battery. But my first question would be, so Adrian, why have you chosen from chocolate to battery? So I myself would prefer chocolate definitely, you see it, right, private wise, from business it’s definitely battery. But what was the intention to move from chocolate to battery?
Adrian Spillmann:
Well, I think that’s a very good question, thank you. I can fully understand that you prefer chocolate over battery slurry, but I must say a lot of it can also be very exciting. But let me put this a bit in the context of what Bühler is doing. So Bühler is a process solution provided with the food, feed and advanced materials industries. This means we are dealing with many different applications, products and materials to be processed. However, in the background very often we have very similar processes which are used. And one good example is the extruder technology, which we have taken for example from the breakfast cereal production and have adapted it for the continuous mixing of electrode slurries, which is ending up in the battery cell.
Marc Deyda:
Well, so in terms of battery business, so we mentioned 10 years, right? So what value in the development have you recognized in the last 10 years? So what was really the impression for you? That battery would be a future technology?
Adrian Spillmann:
Well, so if I look back 10 years ago, obviously the market was heavily dominated by the Asian cell manufacturers from Japan, Korea and China. Over the years we have seen a growing interest also building up production capacities in Europe, mainly driven by the automotive industry. But of course we also see other interesting segments, growing segments, for example what we call high value applications. So these are battery cells with special requirements in terms of safety, performance or a lifetime. And this is definitely also an attractive field to be in. Yeah, and which major changes and moments have you arrived in this last 10 years? So I myself, the diesel gate was definitely an enabler.
Marc Deyda:
What is your moment, your special moment?
Adrian Spillmann:
Well, yes, the diesel gate in Europe. So the turning point for me in Europe actually was when the car manufacturers started to invest, to build up their own capabilities and know how for battery cell production. So this was for me clearly a key point here in Europe. On the other hand, if I look to Asia, what simply was very impressive and mind-blowing, how fast the Chinese market built up the production capacities over the last couple of years. So this was definitely one of the key events for me in Asia.
Marc Deyda:
So that means you have really done also an impact in this development, but what exactly, so that we maybe come more to this digital solution. So what was your impact in that development?
Adrian Spillmann:
Yes, so at Bühler we have pioneered the continuous mixing solution for electrode slurry production more than 14 years ago. In the meantime we have installed more than 75 continuous mixing lines in the LIB (lithium ion battery) industry, which corresponds to about 80 GWh in production capacity. So for those of you who are not that familiar with this metrics, 80 GWh is roughly speaking about half or 50% of the total production capacity which is installed today in Europe. So the continuous mixing technology, I don’t want to go into the technical details, but basically allows to combine all the unit operations in a single continuously operated machine and this enables them to reduce the number of mixing lines, increase the productivity, get a higher consistent quality and in the end also allows to reduce the operation cost compared to the traditional batch mixing technology.
Marc Deyda:
So the battery market is volatile, we all know, so Europe and US are increasing quite fast now. Asia is already established, so there are a lot of e-cars already in movement, but the producers are totally different from the behavior, from the start-up established companies, so they have similar requirements, but what are the major requirements for machine building?
Adrian Spillmann:
Well, that’s a very good point and makes it also quite challenging for us as an equipment supplier, but basically we see two different groups of battery cell manufacturers. On the one hand side, let’s say the mass production for the commodity cells for the electric vehicles, on the other hand the high performance applications, which is probably more performance driven, but overall you can say the main requirements we get from the battery cell manufacturers, first of all is to be able to offer a stable and reliable production system for the electrode slurry production. We need to make sure that the operation investment costs are minimized for the total cost of ownership, at the same time fulfilling the quality requirements and last but not least, this is also very important, we need to increase the speed in terms of delivery time, in terms of how fast we can commission a plant, but also in the end how fast the ramp-up of the whole production facility of the customer is realized.
Marc Deyda:
So meeting all these challenges is quite not easy, it’s like Christmas with kids, right? So therefore we from Siemens, and you can see it here along this digital thread, we always support, and hopefully in the future we support you further, about this whole business process from you as a machine builder, so which starts from the customer end, customer requirements, via this design and concept, automation engineering and physical commissioning. So what did Bühler exactly do in all these steps? So we know that machine builders are usually coming from Asia for the current production sites, so to get access to this market and this relationship. So what did you do to be better than them? You’re a step ahead, right?
Adrian Spillmann:
Yeah, absolutely. So digitalization plays a key role in our activities, starting from the development of our processes and machines, all with optimizing our internal processes during execution of a project, and the end of course also to maximize the performance of the manufacturing plant for our customers.
Marc Deyda:
But this is still a design concept, you know, concepts are not relevant as long as they are not ending in a real machine. So did you make sure that this concept is applied in a real machine? What was done next time?
Adrian Spillmann:
Well, in this regard, standardization plays a key role for us. So looking at the automation part, the use of a standard hardware performance.
Marc Deyda:
Standardization for you or for the end customer, or both?
Adrian Spillmann:
In the end, it’s primarily for us, but in the end it’s a benefit for the end customer. So it’s about speed, fulfilling a project, and also improving the reliability of the manufacturing plant in the end. And of course, thanks to Siemens, we could also successfully implement this automation standard solution, which is specifically tailored also for the battery industry.
Marc Deyda:
So that means it ends up in a tailored machine, but not yet sustainable, right? So what was the sustainable impact? Because all these audience here expect an E-car, which is good for the environment, also for their own money, but what sustainable did you implement?
Adrian Spillmann:
Well, sustainability is a very good point, you know, for Siemens that’s a very important topic as well as for Büeler. So one specific example I would like to mention here, what we have implemented is a so-called inline quality control system, we call this Qualip. So this allows to inline measure all critical process and product parameters, and therefore enables to achieve the highest product quality and consistency of the electrode slurry. And this of course is important for the battery cell manufacturers in order to minimize the straps, for example during start phase of the process, but also to increase the production yield and in the end also to enable a seamless traceability of the whole electrode slurry production process.
Marc Deyda:
So saving raw materials, saving a lot of time in the whole development process of my machine, around 30%. And to make it clearly for all of us, this ends definitely in a cheaper price for a car, for a longer life of a battery, or for home energy storages. So Adrian, what would you do or would you say to other machine builders when they want to go in that battery market? So it’s quite competitive and what is your suggestion, what they should do?
Adrian Spillmann:
Yes.
Marc Deyda:
Because you are successful already and others would like to be a part. What would be your suggestion?
Adrian Spillmann:
Well, first of all, as we all know, this battery industry can be very dynamic, it’s also very demanding in various perspectives. However, I believe it’s a very exciting field to be active in and also to be part of the decarbonization of the future mobility. I think that’s absolutely great. In the end, I am convinced that there is still a huge potential to improve the overall efficiency of battery cell manufacturing. So there are several aspects such as the digitalization, the digital threads we have just discussed, but also to bring in new innovations for production processes. And last but not least, what I believe is also very important to have a holistic view on the whole process chain and optimize all the interfaces in between. So in this regard, I would like to encourage all of us to collaborate with each other and accelerate the impact together.
Nick Finberg:
Thank you Marc and Adrian for the great discussion and thanks to the audience for listening. If you are looking to learn more about battery, be sure to check out our other episodes and subscribe to get updates for future episodes. And if you are already caught up and still want to learn more check us out on our website siemens.com/battery.