Digital Part Production – highly automated CAM – ep. 2 Transcript
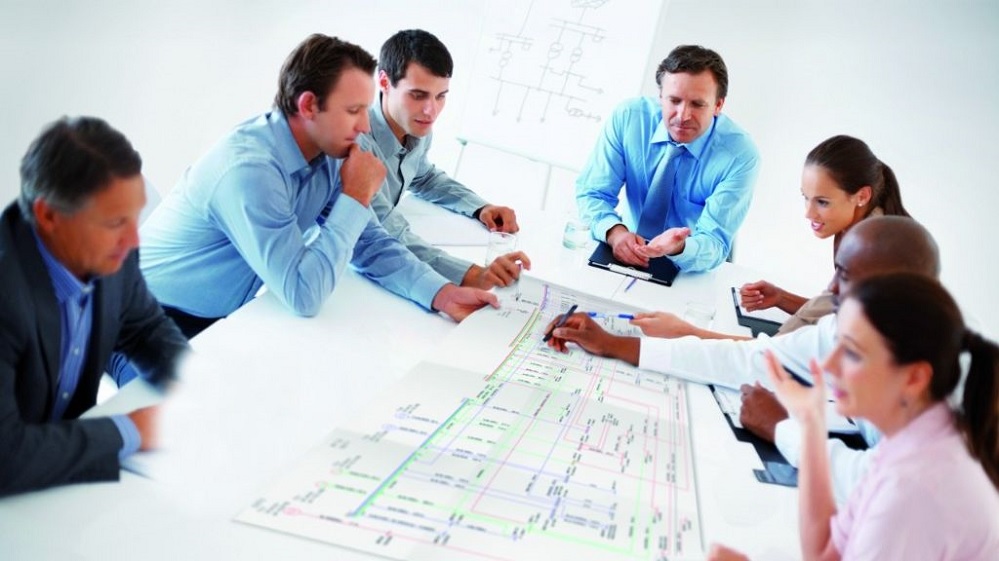
There is an ongoing challenge of increasing complexity in new machine introductions for manufacturers and machine builders. Siemens provides solutions for these challenges with Digital Part Production (DPP), the process of having a fully connected digital thread, merging the digital world and the physical world to create a continuous digitalized communication process with several differentiators.
DPP combines several solutions connected in the Siemens portfolio, including highly automated CAM, synchronized part production and additive manufacturing.
In revisiting the podcast transcript for this series, we are joined by engineering experts Rahul Garg, Vice-president of the mid-market program at Siemens Digital Industries Software, and Sashko Kurciski, senior marketing manager for Siemens Part Manufacturing Software portfolio.
This second DPP transcript and audio podcast takes a deeper dive into highly automated CAM.
Read the transcript:
Bill Butcher: Hello everyone and welcome to Siemens Digital Industries Software podcast series on Digital Part Production brought to you by the Siemens Digital Thought Leadership team. I’d like to welcome everyone back to the podcast series. Joining me again today is Rahul Garg, and Rahul was on our first session. And then joining me today is a new member – Sashko Kurciski. Sashko leads the marketing efforts for Siemens Part Manufacturing Software portfolio. Gentlemen, thank you for joining me today. Well, let me do a quick recap for our listeners. In our last podcast, we talked about the evolution of technology within the machinery industry and the key trends that continue to shape the industry. We also introduced the concept of digital part production at a high level where Rahul had brought up three key themes that are necessary to thrive in today’s highly competitive part production market.
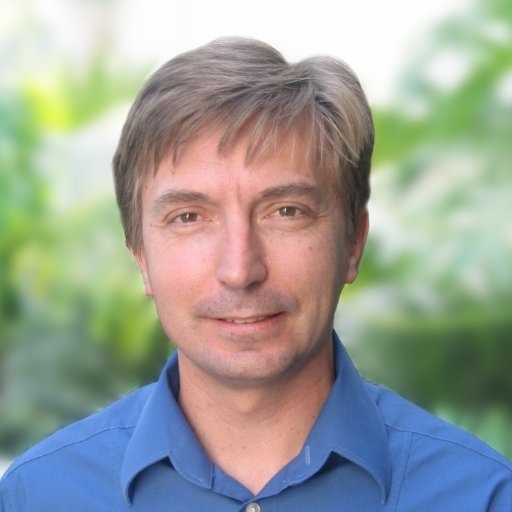
First is highly automated CAM. Rahul, you’ve talked about how highly automated CAM allows OEMs and component suppliers to automate programming and optimize the machine processes to deliver consistent results. You also mentioned synchronized part production, which increases operational efficiency by using design 3D models to simulate machine parts. This also allows teams to improve part quality and speed and the time from order to production by synchronizing the quality plans at critical points in the production processes, all while automating the planning process. Also, there is additive manufacturing. Additive manufacturing can be used to create new generations of products with complex geometries that would be difficult or impossible to achieve with traditional manufacturing methods. In this session, we’re going to take a deeper dive and focus the conversation around one of those differentiators: highly automated CAM. Sashko, before focus on specifics, let’s just take a step back and start from the beginning. Can you provide a quick explanation of what is CAM?
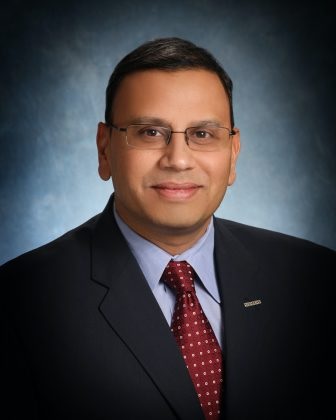
Sashko Kurciski: Sure Bill, and thanks for inviting me. I’m always excited to talk about manufacturing that it’s going through some profound transformation. We’re all witnessing these new breakthrough technologies that are changing how we are making parts and assembling these next-generation products. There are so many exciting topics that we can talk about, but today we will focus on one of the fundamental technologies – and that’s CAM – Computer-Aided Manufacturing. Part manufacturers use CAM software to program CNC machine tools and robots to perform machining operations using the 3D model of the component being made. There are many different machining methods such as milling and turning, wire EDM and many others. Different machines, sometimes very specialized and highly sophisticated, are used for these applications. Defining the machining operations in CAM software is referred to as NC programming, and it is one of the critical steps in the production process. It’s critical because it links and connects manufacturing engineering and production. Basically, it transforms digital designs into real products. So, the NC programming impacts the overall efficiency of many manufacturers. It affects how much time and effort is spent on generating programs for your CNC machines. Then it ensures creating advanced operations to accelerate the machining processes. It should ensure or enable you to avoid errors in production. Also, it maximizes the resource utilization, because these machines are very expensive, and companies make huge capital investments. So, these steps are directly impacted by the CAM software. And in turn, they affect the bottom line of manufacturers, both small parts suppliers and large multinational OEMs.
Bill Butcher: Okay, that’s a great explanation and thanks for sharing that, Sashko. So, we started at the CAM level. What’s the difference between CAM and highly automated CAM and why is that important to the industrial machinery industry?
Sashko Kurciski: Highly automated CAM solutions allow companies and manufacturers, whether it’s an OEM or parts supplier, to automate the NC programming step. I was thinking what’s the best way to explain it, so I will use a real example. On my desk, I have a machinery component, it’s a conveyor bracket for a bottling machine. This part has more than 50 features like holes, pockets, chamfers, slots, etc. To completely machine this part, you will need at least 40 machining operations including roughing, finishing, drilling, and many other operations. Traditionally, the NC programmer needs to manually select each of these features to create the machining operations. For a part like this, which is I’d say is medium complexity, it can take hours to program it. And this is only one component of this machine. So, if you do the math, and there are hundreds of these components, you can understand the time commitment. On the other side, modern CAM systems enable you to automatically recognize and program the entire part. and this is called feature-based machining. In this case, it takes less than four minutes to define the complete machining process. The system analyses the part, finds the features, picks the right cutting tools and creates the complete machining processes. This is a huge time savings. It does not only save time, but it also delivers consistencies. Modern CAM systems also provide additional ways to automate these processes. For example, using specialized operations to minimize input or capturing and reusing the company expertise to standardize the processes. So, you can see the benefits of automating the NC programming using advanced CAM are huge. And that’s the power of highly automated CAM systems.
Bill Butcher: So, Sashko, before I give you a little break here and go to Rahul, I just want to go back to something you just referenced there, and that’s automation. We’re constantly hearing how factories and plants around the world are looking at how digital transformation can help them innovate in response to changing customer demands, including the adoption of new technology. So, what do you see as the main operational goals for machine manufacturers today?
Sashko Kurciski: Simply put, manufacturers need to deliver better components or products faster to the market, right? They need to compress the manufacturing lead time. For example, when we recently did a survey of part manufacturers, almost 60 percent of the respondents identified that shortening the time to market is their main goal. So, to reduce production lead times, manufacturers have very common operational goals across the spectrum, from small to medium all the way to the largest enterprises. They are trying to reduce the planning or the programming time. Simultaneously, they want to accelerate the machining to increase the throughput. They strive to standardize the processes to achieve the required quality while controlling the production costs. So, these are some of the operational goals that we see in almost any part manufacturer.
Bill Butcher: Thanks, Sashko. So, Rahul, I’m going to shift over to you. How do the operational goals for machine manufacturers that Sashko just talked about, align with the reality of current manufacturing processes or current digital transformations that you’re seeing in the industry today?
Rahul Garg: Great question, Bill. Firstly, Sashko provided a very good introduction and good examples of what we mean by highly automated CAM. So, that really helps someone understand the value that we can bring to a part manufacturing company. When you look at an industrial machinery company that is responsible for developing many complex and customized machines, these machines require components with more challenging geometry parts that need very tight tolerances. Lot sizes of components are decreasing because the customers require a wider scope of parts, or the machines must be highly configured. It’s not possible to create one design and make thousands or hundreds of parts of it. You need to be thinking about how to get the best possible part with the best and highest possible tolerance, and you may be making just one or a few of them. So, this is true even while machinery companies are building modularized machines that are more suited for multiple use cases. So, to support these goals, many OEMs and parts suppliers (the suppliers to the machine builders) rely on separate software systems to drive each step of the process. Sashko mentioned some of the process steps that the companies typically go through, right? So, for building these parts, either in-house or through some machine shop that they have outsourced the manufacturing to, they rely on different tools to help them in that process. These standalone applications – starting from the CAD software that was used to design the original part, to the CAM software which is used to do the machining that Sashko referenced. That machining software eventually feeds into some CNC machines.
Then when the part comes out, you have some CMM software to help measure the quality of that part. In many cases, I should say there are different software providers. Each time a copy or interpretation of that data is created, it takes a lot of effort to make sure that interpretation is accurate. When you are going from one software application to another software application, you must make sure that all the information is carried over without anything getting lost in translation. So, maintaining that connectivity to the original design is almost impossible unless everything is all well connected in terms of the software applications. As a result, customers do a lot of translations, and errors get introduced in those translations. When errors get introduced, operators must spend a lot of time fixing those errors. Those errors, or translations, and challenges get further compounded when there is a change, or a revision introduced that becomes a monumental task figure out what the changes were and track the original and updated files. It results in a high amount of scrap and delays in the end products to be given to the final assembly process.
Bill Butcher: In the context of digital part production, how do highly automated CAM processes help machine OEMs and their suppliers achieve their digitalization goals?
Rahul Garg: That’s a great question, Bill. So, when you look at the equipment manufacturers, machine builders and their supply chain that are tasked with manufacturing parts and components for machine builders, the functionality on the shop floor is critical. Parts must be built quickly while ensuring the highest quality and to confirm they are meeting the highest tolerance and precision needs. Of course, while also maximizing their production throughput and production capacity. So, standalone CAM, CAD and CMM systems are the first step towards that digitalization journey; however, this does not optimize the insights in a way that can be used to improve the process and procedures for a stronger ROI. For example, some companies are using advanced design tools to include PMI – Part Manufacturing Information – in their 3D models, but unless the downstream applications can use them, they will not be able to take full advantage of this. So, that’s where a highly automated CAM solution, that Sashko spoke about, does two things. Number one, it helps eliminate some of those translation errors, and number two, it helps ensure that the programming that you’re trying to do to feed the NC machine can be done in the fastest possible way and in the most reliable, repeatable way.
Bill Butcher: So, I think we brought up a couple of good points there. Sashko, when we talk about digitalization, or the digital twin that Rahul just referenced, it’s not just the process that’s connected, it’s also the collaboration between these multiple teams and disciplines. How does digital part production leverage automation – and you spoke about that a little bit earlier – to support other areas of manufacturing including improved part quality?
Sashko Kurciski: Yes, good question Bill. For example, you mentioned part quality. Part quality is one of the key requirements for part manufacturers to stay competitive. It’s expected from them to deliver the quality requested. So, that’s the expectation today. And here we can see the role of having an accurate digital twin and how critical it is in achieving this quality. For example, when having a digital twin of your machine setup programmed in your CAM system, it helps you optimize and validate the machining process early in the process as you program the job. This helps you with many things, including ensuring that you can avoid errors in production which can be very costly. It also helps you achieve first-time yields in the 90 percentiles. Basically, companies can virtually eliminate waste on the shop floor. An additional benefit of using an accurate digital twin in your CAM system, basically a digital twin of your machine setup, includes faster setup and maximizes the machine uptime of these expensive machines. Talking about digital twin and digital thread, using the digital thread basically can connect all the key stakeholders, and connect the different domains like CAD and CAM. So, this can unify the entire production process. We leverage something that we call associativity and it refers to the associativity to the original 3D part model, and this is very important to have one consistent data across the entire process, using one unified technology that allows you to get to a new level of flexibility. For example, often we have design changes – having true associativity – with all the downstream applications from design downstream, such as CAM or CMM inspection, being notified automatically.
So, all the tool paths and all the inspection paths can quickly get updated. Also, another benefit of associativity is process changes, like when a certain CNC machine is not available, and you need to move that machining process to a different machine. When these digital threads are all connected, this change will propagate all the way back to the CAM system, so you can quickly recalculate the machining operations based on this new machine tool. This connectivity between the systems, the machines, and the people enables another level of automation. It automates the entire end-to-end process. Earlier we talked about automating the NC programming, but we can see that with integrated or unified technology, it can achieve a high level of automation. You can automate the entire manufacturing process. So, we can see that digitalization enables automation of each production step and the complete production processes.
Bill Butcher: Sashko brought up some good points when he talked about complete production processes and automating the entire process. And I assume that’s true for all technologies, right? Even the emerging technologies we’re seeing – everybody talks about additive today. I mean, is this applicable here as well?
Rahul Garg: Absolutely, Bill. Additive is an important transformational technology for part manufacturing. Additive has been thought about from a capability to be used for prototype parts, and now it’s getting used more and more in production parts as well. Especially when we spoke about earlier where customers are needing to build small, lot-sized parts, additive becomes a great alternative. When customers are looking to create new innovative designs that were perhaps not possible in the past, additives are a great alternative. It allows you to make parts that, in the past, required multiple assemblies. Now, that can be made in one part. When you reduce the number of parts, you reduce the potential failure points, thus reducing the number of breakage points. These are great advantages that additive can bring to the table. And the early adopters can differentiate themselves by reducing part complexity.
Bill Butcher: That makes complete sense. I’m thinking back to our first session, where you had referenced that the digital part production approach or strategy can be leveraged by both suppliers and OEMs. Do you have any examples of customers, either supplier or an OEM, that has embraced this digital part production as a strategy? If so, what kind of efficiencies have they achieved?
Rahul Garg: Yes, one of the customers I can think of is a company in the Netherlands. They are a manufacturer of very high-precision bearings and motion control systems positioning stages. They also supply high-end semiconductor and medical devices and other machine tool industries. When there are certain heavy parts, weighing anywhere from 200 to 500 kilograms (and even 1000 kilograms, but requiring precision of micron movements) these require very high-precision bearing movements, and that’s the bearings they produce. This company was founded in 1966 and is currently a market leader in this space. However, they were facing significant challenges driven by their end customers, where they needed to make sure that their products were launched faster, continuing to drive more, with higher dimensional accuracy for the motion systems that they were building.
Also, they needed more customized bearings and motion systems that their end customers were requesting, along with exotic materials, like ceramics, to reduce the overall weight of the movement. Eventually, looking to become a more complete system supplier as opposed to just a component supplier, those are some of the challenges they were facing. So, by digitalizing their part manufacturing process, the whole digital part production from design and simulation to machining and the system assembly, it provided them access to the latest product information at each stage of the process. It fostered collaboration between the designers, the analysts and the production shop floor engineers, all fully connected to read data from various CAD systems to ensure that it can be visualized across their entire organization. Also, they were leveraging some of the capabilities of advanced and automated CAM software that Sashko spoke about.
Bill Butcher: Sashko, how about from the OEMs’ perspective? Do you have any examples that come to mind so we can complete the circle for our listeners?
Sashko Kurciski: Yes. A great example is ASM Pacific Technology. They are one of the world’s largest suppliers of semiconductor and electronics equipment with a global operation of multiple R&D and production plants across Asia and Europe. In the past, they used disconnected software systems that had geographical separation between their facilities, causing significant gaps between their design, development and production activities. The 3D data of their machinery components that were transferred to the factories lacked the complete product information, hence not capturing the design intent. This made it difficult for the data to flow easily between the design and the manufacturing. So, ASM realized that they needed to integrate product development and manufacturing. Therefore, they deployed the Siemens software (NX software). The most immediate benefit was the automation it enabled by the feature-based machining. This company took NC programming automation, using the feature-based machining, to another level. The automatic recognition of the machine features is driven by the Product Manufacturing Information or PMI, which Rahul also mentioned earlier. The PMI data can include tolerances and surface machining precision that get attached to the 3D models by product development. So, depending on the recognized features in the associated PMI data, NX automatically creates the best and optimized machining methods, choosing the correct tools to manufacture the entire part that can have dozens or even hundreds of features. With the feature-based machining, this global manufacturer reduced the NC programming time of complex parts by up to 91 percent. They also standardized the machining operations, improving the repeatability of the manufacturing processes.
Sashko Kurciski: I would also just touch on the part quality, because we also mentioned part quality earlier. Part quality is another focus for ASM, considering the precision of these machines that they produce. So, using the integrated simulation in NX they were able to practically eliminate errors on the shop floor and improve part quality. At the same time, instead of conducting tests on physical machine tools, their engineers use a digital twin of their complete manufacturing process to validate the NC programs to ensure first-time success of the machining operations. So, this combination of high level programming automation, end-to-end connectivity and virtual validation of machining processes enables them to improve the overall production efficiency by 70 percent, so huge improvement in terms of efficiency and productivity.
Bill Butcher: From my perspective, it’s easy to see the value that part manufacturers can achieve by taking advantage of the continuous thread of information from engineering through manufacturing, planning and execution to ensure optimized schedules, control, traceability and quality. And I think both those examples are highlighted very well. I want to thank you both, Rahul and Sashko, for your comments and insights on this podcast about highly automated CAM processes. I appreciate the time you took and the responses that you gave.
I hope you will all join us again as we continue to review the digital part production solution for industrial machinery. In our next podcast, we will be taking a deeper dive into the topic of synchronized part manufacturing and why it’s so important for the industrial machinery industry to design, simulate and machine parts in one environment. Until then, this is Bill Butcher saying thank you for joining us.
Siemens Digital Industries Software drives the transformation to enable a digital enterprise where engineering, manufacturing and electronics design meet tomorrow.
Xcelerator, the comprehensive and integrated portfolio of software and services from Siemens Digital Industries Software, helps companies of all sizes create and leverage a comprehensive digital twin that provides organizations with new insights, opportunities and automation levels to drive innovation.
Listen to the DPP Podcast02 for the audio podcast.
Also, for more information on Siemens Digital Industries Software products and services, visit siemens.com/software or follow us on LinkedIn, Twitter, Facebook and Instagram.
Siemens Digital Industries Software – where today meets tomorrow.
About our experts:
Rahul Garg is the Vice President for Industrial Machinery & SMB Program, responsible for defining and delivering key strategic initiatives and solutions and global business development. He and his team are responsible for identifying key initiatives and developing solutions for the industry while working closely with industry leading customers and providing thought leadership on new and emerging issues faced by the machinery industry. Rahul’s experience and insight are derived from 25 year career delivering software-based solutions for product engineering and manufacturing innovation for the global manufacturing industry, spanning a career in R&D to program management, sales and P&L management and having focused exclusively on the industrial machinery and heavy equipment industry since 2007.
Sashko Kurciski is a Senior Marketing Manager at Siemens Digital Industries Software. Sashko leads the marketing of the part manufacturing software solutions to help companies transform their production processes through digitalization. He has been in the CAD/CAM/PLM software industry for over 20 years.