Exploring Service Lifecycle Management for profitability
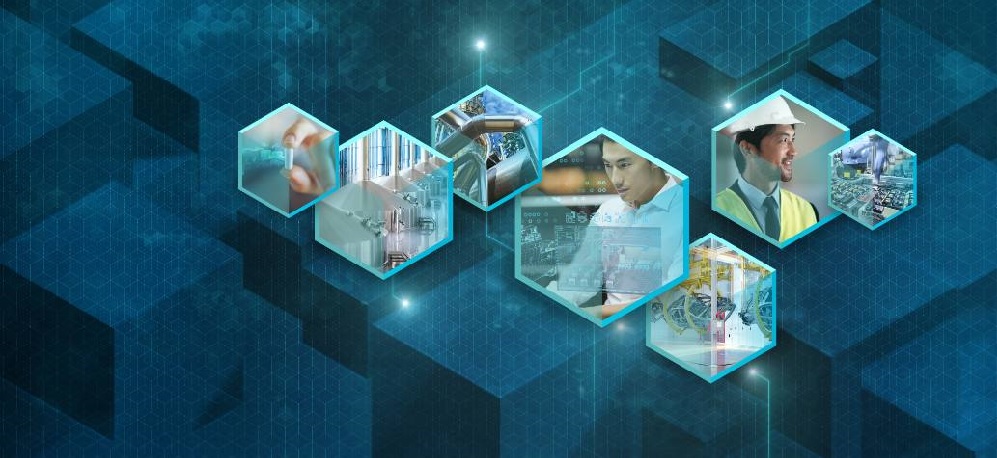
Service Lifecycle Management (SLM) is a holistic approach to all aspects of service. It maintains an up-to-date configuration of the assets in the field and leverages that information in many ways. It also uses analytics and feedback to upstream disciplines to help design for serviceability, using that information to optimize its use and service, ensuring optimum product usage. Additionally, it optimizes the scheduling and delivery of the service when required, proactively, and not when a failure occurs. SLM is a broad area with multiple organizations involved: design, development and production organizations, owners and operators of the asset and people that serve as your organization – a third-party service organization or the manufacturing company.
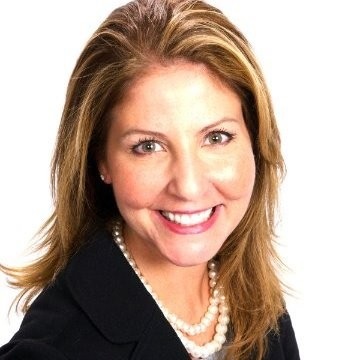
In a recent Siemens SLM podcast, Exploring Service Lifecycle Management for Profitability, Kerri Doyle interviews Yishai Barak from Siemens Digital Industries Software and Ken Amann from the PLM industry analyst organization for CIMdata.
Listen to the podcast.
SLM pulls information together using various tools, participating in different parts, and integrating it, providing the necessary information to optimize the service of the most critical assets. The focus is on reducing the cost and service time. From a manufacturer standpoint, the goal is to reduce warranty costs and perform service quickly and accurately to satisfy customers and increase their loyalty. It is essential to provide the best service so that the end-use customer reaps the most out of the asset, continuously working productively. Therefore, Service Lifecycle Management is providing the information to maintain an up-to-date view, in many cases, of a digital twin of the asset – understanding and maintaining its status.
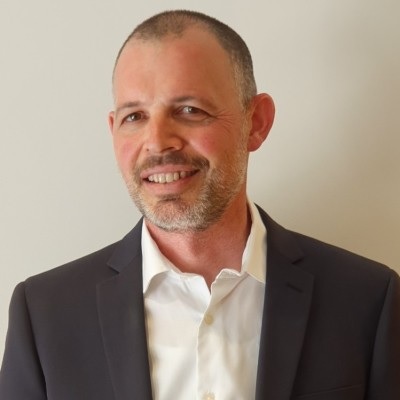
The goal of a service operator is to maximize uptime and minimize the downtime of assets. This scenario has cost and profitability implications. It can be the difference between mission success and failure. In addition, it is essential to ensure the quality of maintenance activities, provide compliance proof and manage spare parts inventory effectively. To achieve these at a reasonable cost, it is vital to identify potential failures early before they occur. This is where predictive maintenance plays a role. Most of the costs will appear after identifying a potential or existing failure until it is fixed. It is essential to ensure the quality-of-service operation that neither bolt is missing after a technician disassembles and reassembles while retaining compliance proof at any given time. Also, it is critical to immediately identify impacted assets in your fleet following a manufacturer recall on a particular part. Furthermore, it is necessary to ensure your documentation remains accurate throughout configuration changes of an asset during its lifespan. These are just a few of the most common challenges.
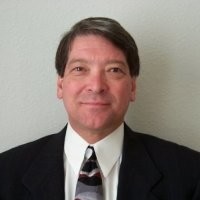
Service Lifecycle Management solution must be modular, address various areas overall as SLM implementation evolves.
As an example, Siemens has an industrial machinery customer that operates thousands of machines in various locations. They use solutions to manage the documentation as a layer on top of their data model, ensuring that it remains up-to-date seamlessly, avoiding the need to rebuild new documentation for each change. Therefore, the documentation changes based on actual asset configuration. They ensure their technicians are equipped with the correct information while performing maintenance activities. It is the difference between static versus dynamic, reflecting the replaced parts over time, including the configuration changes, upgrades, etc. Thus, it always remains up to date.
For more insights around Service Lifecycle Management for profitability and competitive advantage, listen to our SLM Podcast or please visit siemens.com/teamcenterslm for more details.
Siemens Digital Industries Software is driving transformation to enable a digital enterprise where engineering, manufacturing and electronics design meet tomorrow.
Xcelerator, the comprehensive and integrated portfolio of software and services from Siemens Digital Industries Software, helps companies of all sizes create and leverage a comprehensive digital twin that provides organizations with new insights, opportunities, and levels of automation to drive innovation.
For more information on Siemens Digital Industries Software products and services, visit siemens.com/software or follow us on LinkedIn, Twitter, Facebook and Instagram. Siemens Digital Industries Software – Where today meets tomorrow.