Adopting industrial scale additive
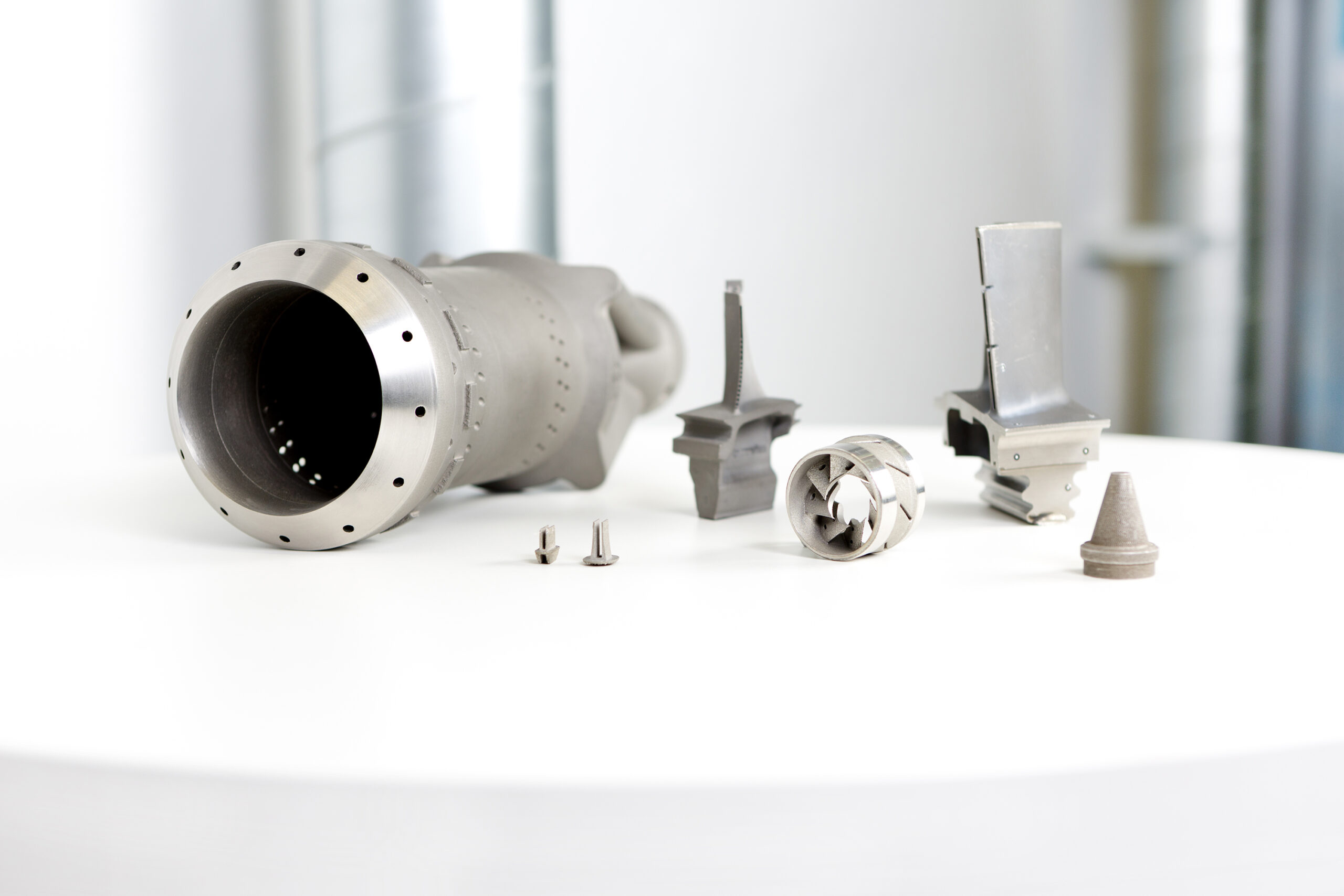
Additive manufacturing (AM), and the design processes for it, are undertaking massive changes as engineers, manufacturers and entire companies begin to understand its potential in a very mature industry. The basics of how the technologies function have been handled and now the number of useable materials is expanding almost as rapidly as the custom geometries. But to gain widespread adoption in manufacturing, AM technologies will need to scale for industrial production. This is exactly what Ashley Eckhoff covers in the Efficient Manufacturing article – Speeding the adoption of industrial additive.
But for a more cursory understanding, let’s discuss some of the key points he covered – enhanced functionality, scaling for industrial production and maximizing the investment in the technology.
Enhanced functionality
Though the total number of workable materials in additive is fewer than that of more traditional manufacturing methods, the pool is growing faster than ever. This growth is due to many parts, most notably research in the academic and commercial spaces. In the past 5 years, the number of usable materials has ballooned from a couple hundred to over three thousand. And new materials are being certified constantly. New materials means new material properties and an expanded design space for engineers.
But material selection isn’t the only path to expanding functionality – more complex geometries compared to traditional machining are enabled with AM. Not just conformal cooling channels to increase performance or longevity, but granular control or the material to produce the desired material properties in a qualified material. With enough computer processing power, that will not be a metaphor. Researchers are working with precise AM toolpaths to nearly define a metal part’s grain structure. Precision printing at this scale could remove the delineations between cast parts and printed parts when it comes to overall strength. But for now, it is enabling porous material printing and fine lattice structures to alter strength, heat transfer and many other material characteristics.
Scaling to industrial AM
The potential for additive applications is amazing, but it means nothing if it can’t be brought to market effectively. And that is why simulation is a crucial part of the additive workflow. Given AM is so new compared to other manufacturing methods, the intuition of an engineer or designer of what will work is very limited. The same goes for manufacturability, without an understanding of how the part will progress through development the likelihood of re-work is high. Simulation acts as a virtual testing ground so that when mistakes are made, very little investment is lost, and information is still gained from the mistake. This learning happens with many different types of simulation – it could be the efficacy of the final part geometry through virtual stress testing or fluid modelling, it could involve the printing path to minimize material buildup in the melt pool of a laser printing machine, or it could be a post-process step to remove print supports or un-sintered powder from an internal cavity. Regardless of the process, simulation makes optimization faster and cheaper than printing multiple parts to throw out over half of them.
Maximized investment
It is easy to get trapped in the mindset that adopting additive means using it to replace nearly every manufacturing process. While it would theoretically be possible from a technical standpoint, it would be dastardly from an economic one. High-speed repeatability will take a long time for the technology to overcome, if it ever does, but that is not AM’s value. AM is perfect for highly customized designs or creating ultra-low-weight components with internal cavities. That is why it has been so readily adopted by Formula 1 teams. And additive doesn’t need to be used to directly manufacture the part either, many companies are finding success in AM for molds – some are creating 3D printed sand molds for engine blocks, others are using large format polymer printers for composite panel molds.
Implementing additive manufacturing in an industrial environment will mean looking at the benefits an AM component can bring to a system. Whether that is a part for the final product or a custom piece of fixturing for manufacturing will depend on the company’s investment path. But regardless of how to proceed, Siemens Software has the solutions to make additive manufacturing part of everyday operations from concept through manufacturing. For the full story, make sure to check out the article in Efficient Manufacturing.
Siemens Digital Industries Software is driving transformation to enable a digital enterprise where engineering, manufacturing and electronics design meet tomorrow.
Xcelerator, the comprehensive and integrated portfolio of software and services from Siemens Digital Industries Software, helps companies of all sizes create and leverage a comprehensive digital twin that provides organizations with new insights, opportunities and levels of automation to drive innovation.
For more information on Siemens Digital Industries Software products and services, visit siemens.com/software or follow us on LinkedIn, Twitter, Facebook and Instagram.
Siemens Digital Industries Software – Where today meets tomorrow