More plugins in NX Design for AM
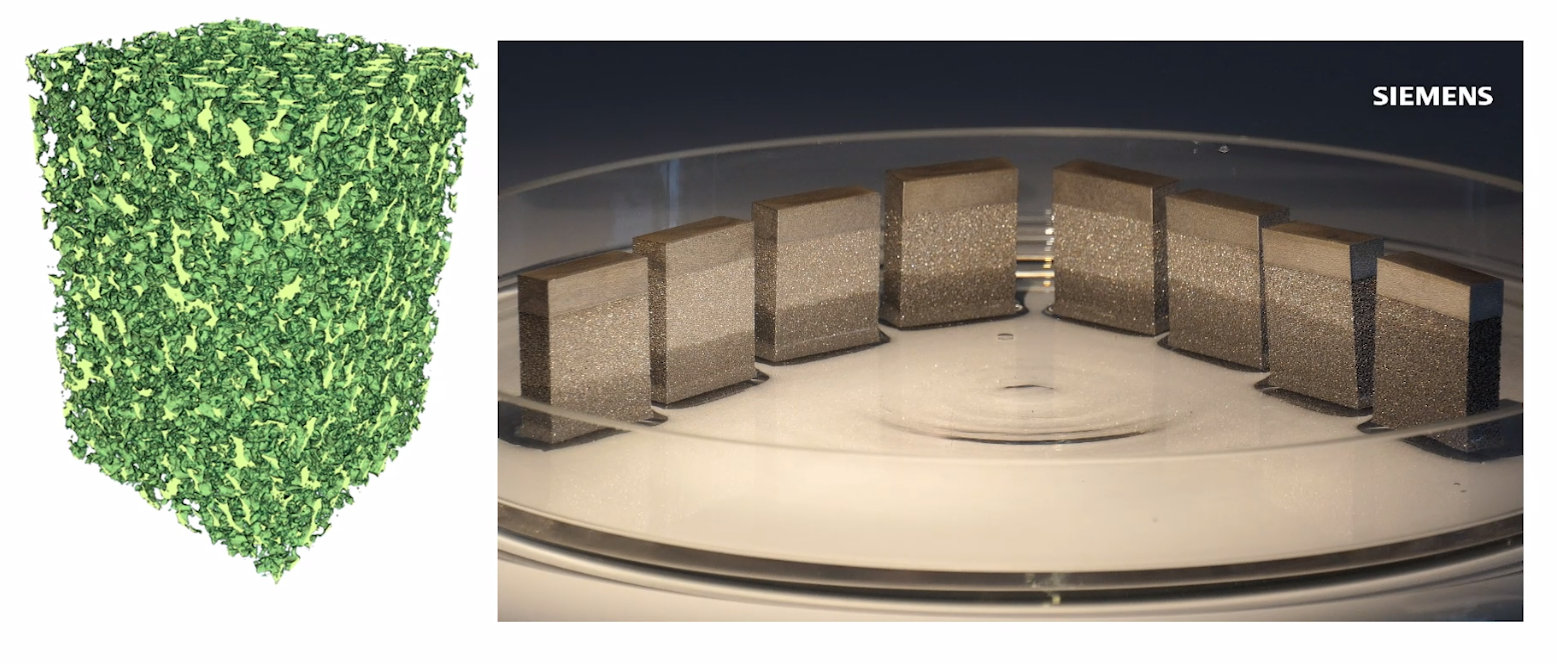
In a push to expand functionality of additively manufactured components, NX™ software has been rolling out new tools for additive manufacturing (AM) processes and a rigorous model-based definition system to support the technology. In a previous blog, I looked at some of the flashiest features in the December 2020 release, but we’re back at since that was just the surface.
For a full discussion of the additions to NX, check out Jennifer Piper and Tod Parrella’s video podcast series – Episode 1, Episode 2, Episode 3. But since the first episode has so many great tools for AM, you can watch it below.
Whether you are producing consumer products, medical implants or turbine blade for power generation, AM has a benefit. And while the surfaces of an AM part are often against the norm of manufacturing, it only gets more interesting as you delve inside. Here are a few of the more interesting features added to NX for AM.
Watertight solids
One of the greatest benefits of an AM approach is the flexibility of the technology. Apparel and sports equipment can be fit perfectly to its user while medical implants can work in harmony with a patient’s anatomy. But these applications rely on scans of the individual’s anatomy, meaning precision CAD geometries are unusable and standard tessellation language (STL) files must be used instead. Many engineers, especially those working with AM designs every day, have a distaste for STL – it is old, slow and cumbersome.
It may not be going away anytime soon, but STL’s problems are not unsolvable, especially with custom software improvements. Instead of manually modelling the scans in STL a secondary mesh can be wrapped around the object to prevent mesh incongruencies. If a wrap cannot be added for an application, filling gaps in the model is now easier. Integrating these tools directly into the modelling software cuts STL preparation times from hours to minutes, or even seconds depending on the structures.
Lattices
Below the surface is where many of the applications of AM begin to flourish. Since the machines are not taking away material, but progressively adding it, voids can be constructed within components. That is not a far-reaching benefit, instead it is how you shape that void – with lattices. Similar to the bones of birds, components can be constructed with fine connecting material. As opposed to solid structures, these internal lattices are purposeful – there is no reason to put material where it is not needed.
Though the addition of lattice structures is not new to the world of AM, it has become far easier to implement with recent software enhancements. A designer or engineer no longer has to program complex geometric functions to then implement through manual modelling techniques. Solutions from academia are also emerging – Voronoi patterning has been known for years as a means sound and energy absorption, and has recently been added as a rapidly available pattern for AM designs. The future of lattices for AM will be a great story to watch.
Porous materials
Porous materials are similar to internal lattice structures, but more closely resemble pumice in it’s geometry. Luckily for manufacturers, getting a porous material with AM does not require the same energy as a volcano and it is a far more precise process. In a demonstration at FormNext 2020, Dr. Christoph Kiener presented a custom heat transfer device made from a single AM print, using material porosity to force capillary action of a working fluid through the device.
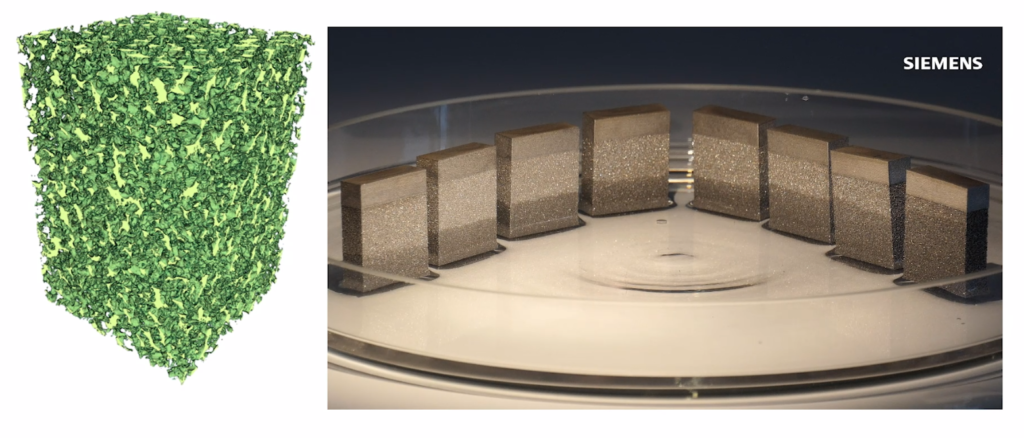
While this capability is not completely supported by software solutions, there are tools to ensure accurate fluid-flow through tight internal lattices. This can be invaluable for internal cooling of components, especially high temperature turbines – similar designs have already been implemented by Siemens facilities to great effect thanks to the work of Material Solutions.
Additive manufacturing is still a new technology compared to milling, forging and other traditional manufacturing methods. Fortunately the learning curve for the methodology is being accelerated by comprehensive software solutions on design side, on production and everything in between. And these software solutions are providing geometries unavailable to any other manufacturing technique.
Siemens Digital Industries Software is driving transformation to enable a digital enterprise where engineering, manufacturing and electronics design meet tomorrow.
Xcelerator, the comprehensive and integrated portfolio of software and services from Siemens Digital Industries Software, helps companies of all sizes create and leverage a comprehensive digital twin that provides organizations with new insights, opportunities and levels of automation to drive innovation.
For more information on Siemens Digital Industries Software products and services, visit siemens.com/software or follow us on LinkedIn, Twitter, Facebook and Instagram.
Siemens Digital Industries Software
– Where today meets tomorrow.