FormNext presentation: How Siemens software can accelerate the adoption of additive manufacturing
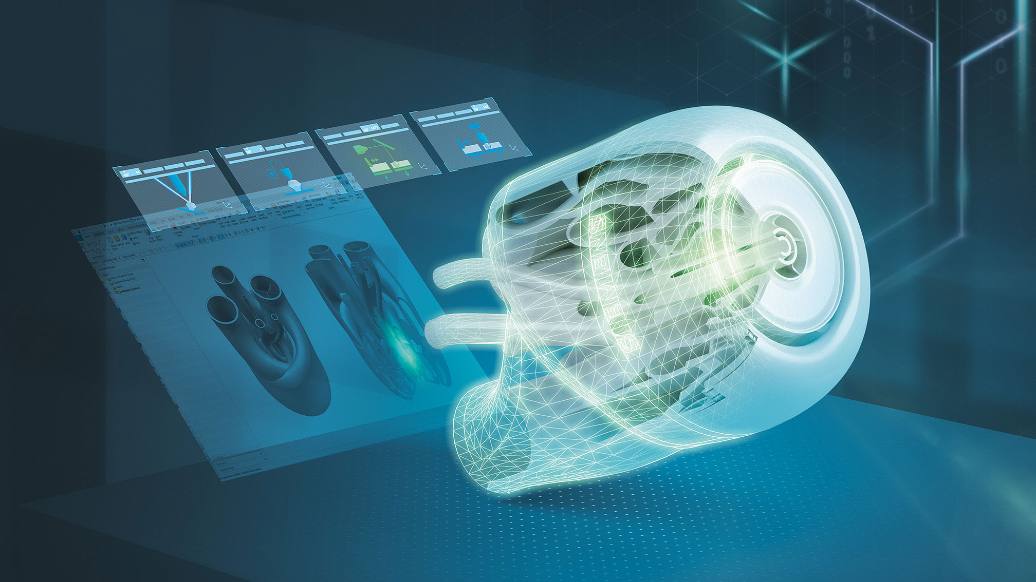
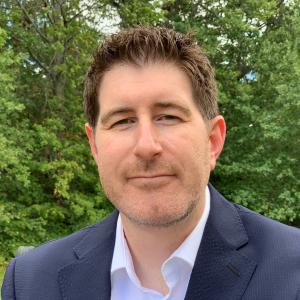
In a recent presentation last month at FormNext, Ashley Eckhoff, Marketing Manager for Siemens Additive Manufacturing Engineering group, spoke about how Siemens is accelerating the adoption of additive via outstanding software capabilities.
In 2020, Formnext Connect went entirely virtual, and leading this trade fair was additive manufacturing. In this context, Siemens also offered an exciting program – the Siemens Additive Manufacturing Summit – which shows how they transform the ecosystem together with their partners. This event is tailored to the respective industries’ requirements, presenting the Digital Enterprise Portfolio’s value, a holistic end-to-end solution covering the entire AM value chain.
Ashley presented a 30-minute session on How Siemens software can accelerate your adoption of AM. His overview addressed this end-to-end process for the AM workflow, which allows the performance of an additive manufacturing task to be more efficient while adopting AM in new ways.
Siemens AM software revolutionizes AM adoption
Siemens has worked in the area of additive manufacturing almost since additive’s inception. The Siemens AM capabilities are built into the software suite.
Many questions must be answered to produce quality parts on time and at scale. Siemens addresses these questions by developing an end-to-end AM solution that helps customers answer these queries and alleviate problems.
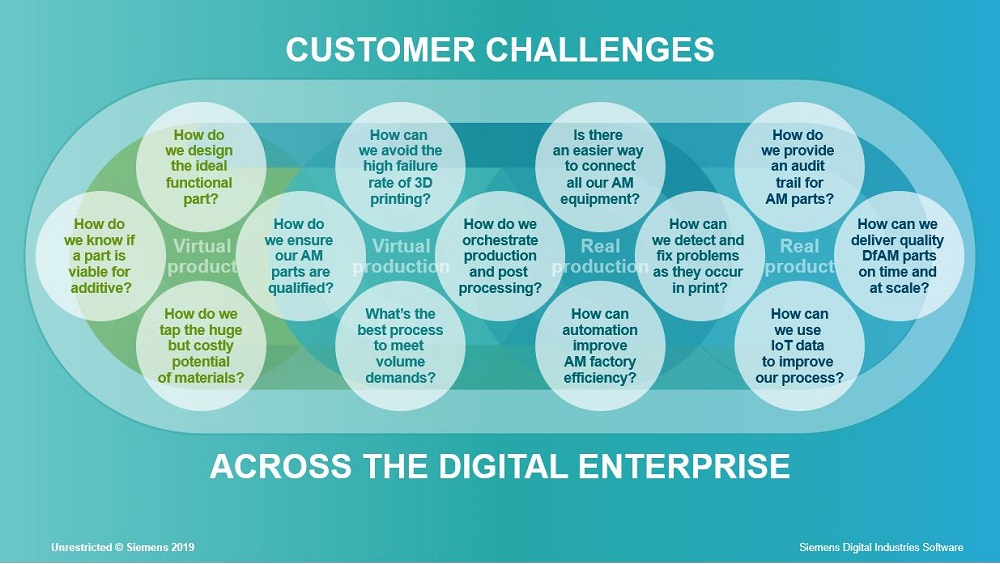
The current system software for additive manufacturing uses digital twins. There is a digital twin of the product in a CAD model that can be optimized, and one in production for print simulation in the build tray set up. Both lead to a physical world with real production and an actual product.
However, virtual production comes first, beginning with standard CAD designs. A designer will craft a part using a standard design tool (available inside the Siemens NX software). There are also tools within NX specifically for the design of AM products. For example, lattice capabilities are multi- option provided by the NX tool and topology optimization (rather than manual), where the system builds an object based on inputs and constraints. Thus, the system uses computing power to generate the optimum geometry. The resulting parts are often very organic looking, used for stamping or molding. However, suppose there is a desire for a genuinely optimized part. In that case, you can allow the system to run without constraint, resulting in a part geometry that can only result from using additive manufacturing.
There is the ability to optimize for minimum material usage and weight. Also, somebody can use topology optimization for fluid flow. Therefore, it works with facet or mesh geometry that results from topology optimization. So, with NX, you can mix mesh and standard CAD geometry. The system works on the geometry regardless of what kind of body it is. Moreover, it can include serial numbers (signifying the position, font and size) on a part to trace in the design process. It becomes a real identifier of the part during production.
Ready for 3D printing
Once you have a part ready for printing, you must optimize the printing of that part. This process optimizes actual production. Also, there is the software to optimize the part in the build tray for minimizing distortion and material usage. Therefore, the part is optimal with the goal of printing with quality the first time.
Moreover, there is an AM build optimizer, which is cloud-based. It uses parallel processing running through one hundred orientations to find the optimal one for a part in the build according to the weighted input.
Once the part is designed, and the orientation is optimized, it’s time to optimize the build tray. NX integrates 3D nesting to take a handful of parts and optimize their positioning in the build tray. This profoundly impacts how quickly the parts print based on how they’re packed in the tray. The serial numbers generate within the build tray by importing the part with the placeholder, running an automated system utility to replace with the customer numbering.
Consequently, the system makes unique 3D identifiable markers from those identifiers. It can now trace a part in the field, back through the manufacturing process to find out what machine and materials were used and where the part was positioned in the build tray. This is paramount for a tightly controlled, certifiable process.
Finally, depending on the production technology, there is sometimes a need to build support structures, which is an additional feature included in the end-to-end solution inside of the NX technology. Siemens has partnered with many third-party vendors to integrate this capability into their software. So, someone can alter the build set-up as the part printing changes or a different mix of parts is chosen within the build tray.
The goal of the product and production digital twins is the eventual production of the part in the real world. Therefore, this connection is enabled with most of the significant AM partners, linking to their hardware via NX either directly or through build processes.
Siemens NX supports the highest range of print hardware on the market, which means you will rarely need to leave the NX environment to interact with the additive hardware.
Register to listen to this presentation in its entirety for more information about other parts of the system and available capabilities.
Siemens Digital Industries Software is driving transformation to enable a digital enterprise where engineering, manufacturing and electronics design meet tomorrow.
Xcelerator, the comprehensive and integrated portfolio of software and services from Siemens Digital Industries Software, helps companies of all sizes create and leverage a comprehensive digital twin that provides organizations with new insights, opportunities and levels of automation to drive innovation.
Also, for more information on Siemens Digital Industries Software products and services, visit siemens.com/software or follow us on LinkedIn, Twitter, Facebook and Instagram.
Siemens Digital Industries Software – where today meets tomorrow.
About our expert:
Ashley Eckhoff has a background in engineering and has been with Siemens for over 20 years in various capacities. He has spent the past few years deep-diving into additive manufacturing in both product design and marketing roles.