Vehicle performance simulation and testing for better design
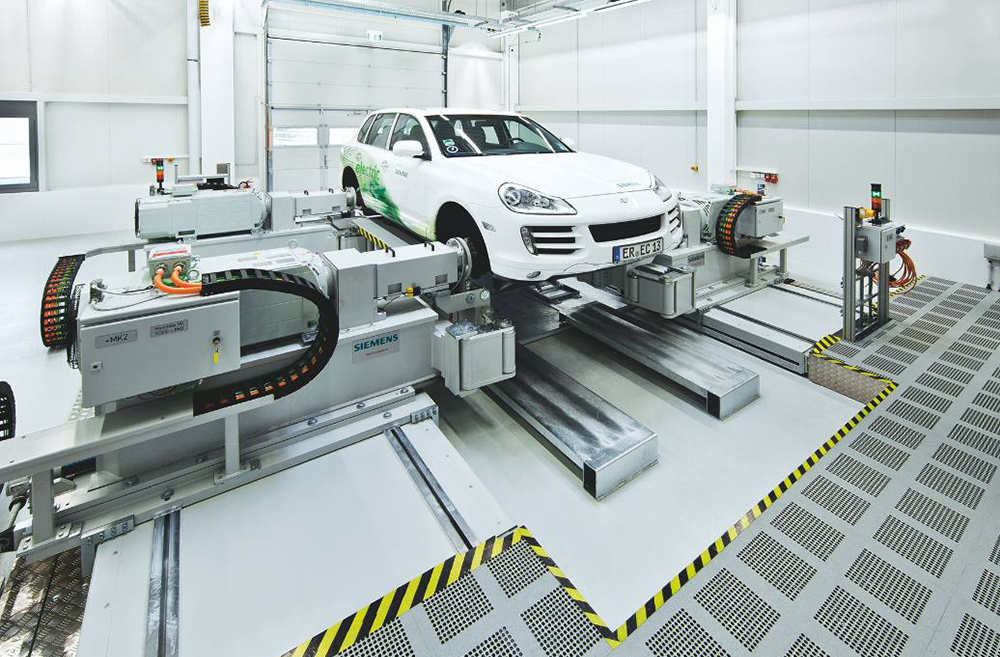
By: Fred Ross and Walter Bauer
Vehicle brand image and expected performance is unprecedented to what existed several decades ago. In an extremely competitive market, original equipment manufacturers are working hard to bring new, innovative ideas faster than their competitors.
An essential part of these ideas includes advanced driver assistance systems (ADAS) and autonomous driving features, which make the vehicles safely operate in complex traffic and pedestrian environments. Attributes which were only available on high-end cars are now becoming mandatory for most vehicles. Development, validation and sign-off of the proper functioning of these complex in-vehicle mechatronic sensor/actuation systems in the traffic environment is a significant task for the performance and control engineering departments. Next to the required testing in the later stages of the development cycle, frontloading with extensive simulation allows engineers to investigate real-world scenarios early in the design process, required to ensure safety.
The other key innovation strategy in vehicle development is driven by the ever-increasing pressure on fuel economy and emissions control, which are profoundly affecting development strategies for powertrain, electrification and cooling, and energy recovery systems. Again here, the complexity of the mechatronic systems’ interaction and the performance of these systems in actual vehicle context calls for a focused effort in frontloading with simulation-based methods to be able to meet expected time to market.
Adopting model-based systems engineering is, therefore, an important paradigm in the context of the electrification/hybridization and autonomous driving trends.
The combined use of adequately functional, detailed design-based simulation and testing methods brings these new technologies to the market sooner and decreases the number of physical prototypes to be built for physical testing – and, as a result, the total prototyping cost. Test and simulation play an important role in refining requirements and operational targets for the vehicle performances, impacted by the above trends, next to the development of efficient yet accurate modeling technologies and processes for the new challenges.
This assiduous process of design exploration, optimization, testing and validation to find performance requirements is vehicle performance engineering. It requires different levels of analyzing, testing and confirming the many domains of a vehicle, including efficiency; passenger comfort; noise, vibration and harshness (NVH); driving pleasure; and safety.
Each domain entails a phase of requirements to meet the full validation of a vehicle. In the early stages of analysis, target setting is executed and system concepts are evaluated, while later phases entail the CAD design iterations with validated models. At all phases of development, control strategy/software/system integration testing is required.
For frontloading development, a scalable simulation suite supports this challenge of validation by seamlessly transitioning from 1D to 3D modeling with testing knowledge at different levels. For us, the digital twin concept does not only include the modeling technologies, but also the processes to:
-
- Accurately evaluate the context of the real-world (actual market) scenarios, going from methods for supporting real driving emission standards to supporting realistic vehicle-in-traffic scenarios for ADAS/autonomous driving validation or using real-world durability loads for different or global markets.
-
- Provide the proper connections between the simulation tasks between separate entities in the organization that work on the crossroads of system development, controls development and performance
The process and history of vehicle performance simulation
The levels of testing, kinds of testing and granularity of that testing can be quite diverse. You can analyze and test a single component in an engine, the brake pads of a truck or the ride quality of a luxury sedan.
Before 3D simulations were available, crash simulations occurred exclusively in the physical realm. Companies were working with numerous performance requirements criteria based on different levels of geometry, or a set of CAD data, depending on the simulation functions, with numerous forms of vehicle data performed at different points of time in the process. These exercises began the concept of prototyping, or the idea that all simulations are tested on the same level of geometry, and any conflicts in data would require modifications.
With the advent of digital simulations, the development process has become more refined. In the past decade, digital simulation prototyping via digital twin integration is a critical part of the vehicle performance engineering process. A suite of products and software is provided via a digital cloud to produce the output of geometrical information and loading data as a part of this intricate process. However, most manufacturers do not have a data freeze, which is a period where rules for making the source code is more stringent. This is a pure digital prototype, or a simulated representation of a part or product before creation.
The goal of the simulation is to significantly improve the quality of results for making better design decisions. However, complex simulations can take up to three months, while management desires quick results. Time is a challenge in bringing results to the table more rapidly with a required level of predictability.
There is significant variance to validation, with hundreds of variations that you should test. These range from sports additions, to different powertrains, wheels and electronics. There is no way to test all variants with either physical or virtual models. So, a few representative cases are chosen.
Before a vehicle can be sold, there is a permissions process. The number of vehicle variants is the result of all combinations of engine type and performance, transmission type, left-hand or right-hand drive, 4-wheel drive or 2-wheel drive and so on.
There are specific load cases which identify what the vehicle needs to meet ‒ for example, high-speed highway, uphill trailer-tow, to key-off or idle simulation. Then there are also tests for drive cycles. The Worldwide Harmonized Light Vehicle Test (WLTP) is a government regulated fuel consumption test which takes nearly 30 minutes to run on the physical vehicle. Fuel consumption is reported on each variant, but this is not possible with thousands of variants, so only a few critical ones are chosen.
However, you don’t have the time or resources to verify everything on every car. Short-term testing is usually performed as a standard load case with repeatable data to find errors, while long-term testing becomes more difficult to predict the failure rate with over 100,000 kilometers of testing completed.
Each original equipment manufacturer has its requirements, multidisciplines or best practices with guidelines. These guidelines help manufacturers meet the required level of quality in preferred areas of production and development that depend on their marketing position, such as comfort, drivability and vehicle power, thus impacting the focused engineering area (aerodynamics, acoustics, energy management or durability).
The attributes of vehicle performance engineering
Some of the domains to be tested and analyzed as part of the vehicle performance attributes include:
-
- Fuel economy & emissions
-
- Thermal and energy management
-
- NVH and acoustics, pass-by-noise regulation
-
- Durability
-
- Drivability
-
- Driving dynamics
-
- Integrated safety
-
- Aerodynamic performance
-
- Water management
All these attributes must intersect with the evolution of manufacturing by aligning with Industry 4.0. To achieve this, you must focus on frontloading design decisions using digitalization for faster turnaround time. Digital twin and simulated prototyping in manufacturing have been part of the manufacturing process for several years.
However, if you’re creating a digital prototype, there is not a physical model to begin setting up the manufacturing process. To bring the vehicle to market sooner, the manufacturing process needs to start with a simulated digital twin, with the goal being to reduce time to market.
Your delivery must compile your statistical data to meet the requirements for the design, which feeds into the chief programmer so that manufacturing is built into the overall process. You can then take this data to determine what works and what fails, thus giving the opportunity for developing a better product and process.
Technologies like simulation, 3D printing and digital twin are recognizable innovations in manufacturing. Moreover, the automotive industry is no exception to implementing these technologies into their vehicle performance engineering.
The overall result of the simulation is to achieve quality results and make better decisions faster.
This completes the first blog in a series on Vehicle Performance Engineering (VPE). In future blogs, we will focus more on the specific attributes of VPE.
About the authors
Fred Ross is the director of automotive and transportation industries lead for Simcenter STAR-CCM+, where he works with clients on vehicle thermal management, aerodynamics, and passenger thermal comfort for the past 30 years. He is currently involved with the business development and product management of Simcenter STAR-CCM+ for the automotive industry.
Walter Bauer is a consultant working for simulation and test division of Siemens PLM Software. He worked at Daimler passenger car development for 38 years on CFD simulations — including VTM, passenger comfort, aerodynamics, engine coolant flow — and digital prototype process.