How cloud-based simulation addresses automation challenges
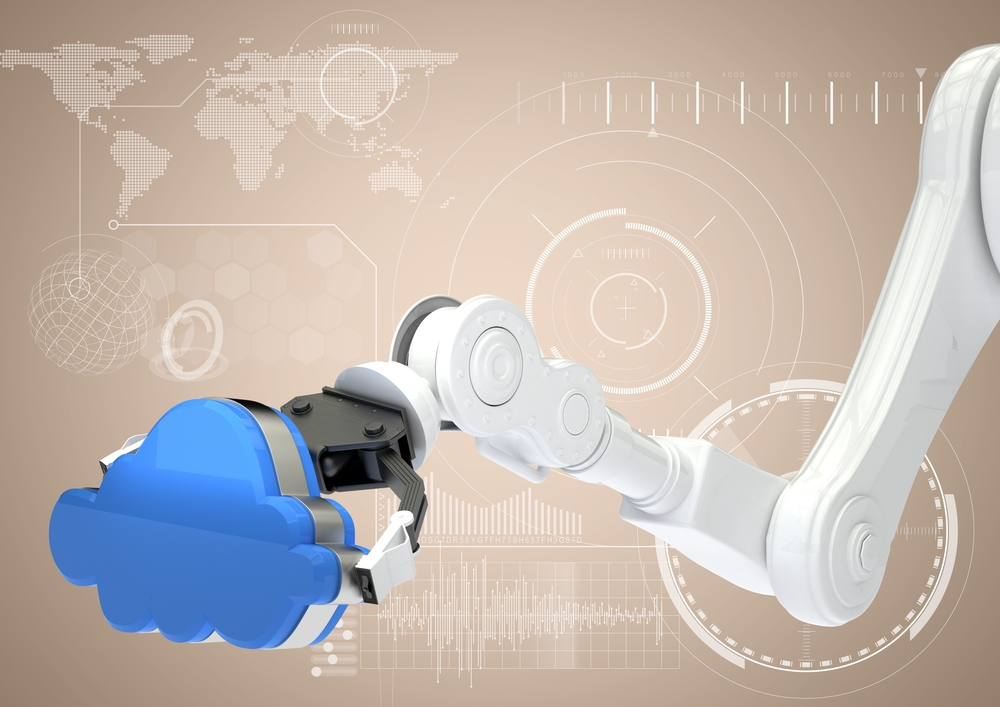
Digital simulation has become an essential capability for planning and verifying automated manufacturing processes such as robotic assembly, packaging and palletization. Simulation and process planning applications provide powerful tools that help engineers quickly and efficiently adjust automated production as needed, and more effectively manage expensive assets.
However, not all manufacturers realize that desktop versions of process simulation and planning apps simply aren’t equipped to fully realize the benefits of digitalization and Industry 4.0 technologies.
Consider IoT adoption, which is rapidly rising and requires cloud infrastructure to facilitate data-intensive communication among automated machines, equipment, devices and other endpoints. According to the Spiceworks 2019 State of IT report, 48 percent of organizations are actively exploring the use of IoT devices, and 57 percent expect to use some form of IT automation by 2020. This includes the automation behind artificial intelligence (AI), virtual and augmented reality and additive manufacturing.
In addition, the International Federation of Robotics projects that global robot density in manufacturing industries rose to 74 robot units per 10,000 employees in 2016—a 12 percent increase from the prior year.
These and other Industry 4.0 technologies require an entirely different IT system architecture that can make data available on-demand and in real-time, provide reliable always-on tools for communication and collaboration among key groups, and improve cycle time as well as responsiveness when conditions change.
Cloud can boost the value of digital simulation
A cloud-based simulation should accurately represent the process before beginning the actual commissioning of the production machine/cell/line. It can help in identifying issues and potential failures early in the process, thus reducing the likelihood of those “fatal” errors that are expensive to fix and cause big delays in commissioning.
Virtual process simulation may also trigger new ideas for optimization, validate layout and required assets, point out potential bottlenecks in production throughput and other manufacturing parameters.
When a cloud-based simulation application is used instead of a desktop application, organizations gain additional benefits.
• Simulations can use more data/knowledge and more up-to-date data. This means updates to available data happen faster and more often, and simulations can draw on more data and thus be more detailed.
• More control over resource costs. In the cloud, users are tapping into services on a per-use basis, rather than a company buying a series of licenses for a flat fee and being locked in for a specified time. Desktop simulation applications cost the same no matter how actively they are used. In the cloud, a manufacturer would pay for only what they use.
• A reduced IT burden. Cloud provides a shared security model where some of the roles are shifted to the provider. However, the customer is never absolved of security or the resource burden of application maintenance, updates and security to the provider. In most cases, the cloud provider can tackle these tasks more efficiently because it devotes its resources to ensure maximum performance and security.
• Easier integration with Industry 4.0 technologies and concepts. Augmented reality, additive manufacturing, IoT—essentially all of which are emerging manufacturing concepts—are based on cloud technology.
Time for cloud-based simulation?
Gaining a competitive advantage in today’s manufacturing environment requires an organization to put available tools to work more effectively. The cloud helps to do this. It taps into the power today’s technology, connects the digital dots, and is a better platform for fast and effective digital process simulation than yesterday’s desktop apps.
This concludes part one in our series on the cloud and simulation. In part two, we discuss how cloud-based simulation can simplify automation complexity.
About the author
Gil Chen is passionate about innovative thinking and execution of out-of-the-box ideas. In his current role at Siemens, he leads experiments around Industry 4.0, the factory of the future and innovative manufacturing processes, with robotics and automation systems as his focus and robotic simulation for the automotive industry as his main expertise. He has more than 25 years of experience in PLM in dominant market players and feels lucky to support complex manufacturing challenges and leverage his knowledge to teach others.