The benefits of consumer-grade additive manufacturing
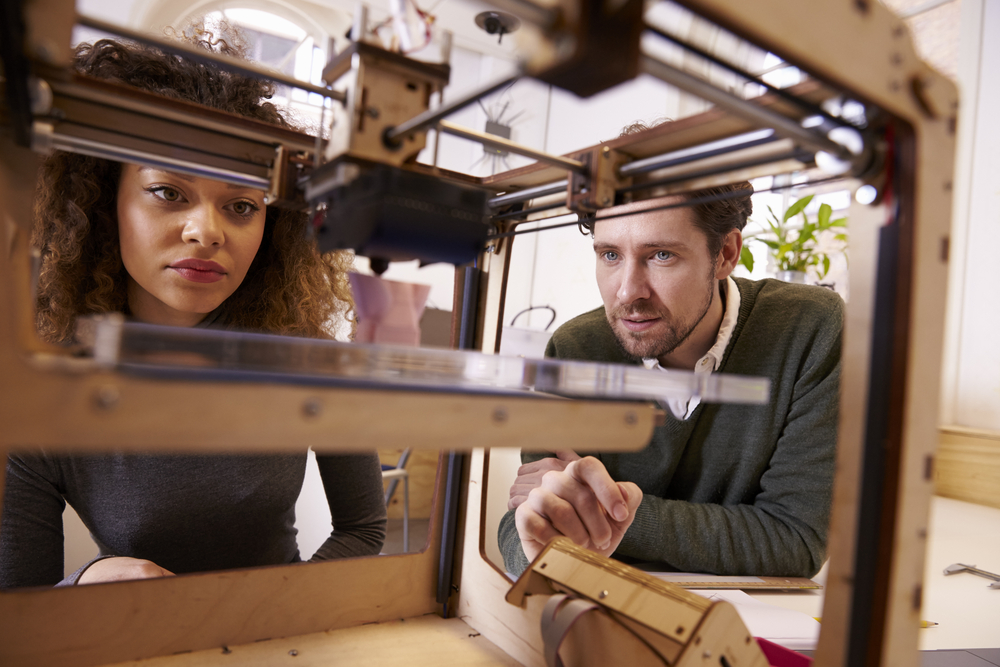
Despite all the excitement and experimentation happening around additive manufacturing, some manufacturers are still sitting on the sidelines. While companies with big budgets can forge ahead, others are stymied by the high cost of industrial-grade additive manufacturing applications. Given that those costs can be between $50,000 and $500,000 (and can still go higher), it’s easy to understand their reticence.
But some manufacturers, unwilling to let their competitors gain what could become an insurmountable lead, have gotten creative. After completing an additive manufacturing cost analysis, they’ve begun experimenting with consumer-grade printers as a conservative way to begin leveraging this continually evolving technology. Early results demonstrate these less-expensive options are effective options for a number of industrial applications, including prototyping, form/fit validation and, in some cases, even on-demand replacement of mission-critical parts.
Still, while weighing additive manufacturing advantages and disadvantages, others see the consumer option as a way to gain additional benefits beyond a lower price point. Instead of purchasing a single, expensive industrial machine, they’re opting to buy and deploy several consumer machines so the technology can be leveraged across the organization. Currently, with large, centralized industrial printers, designers commonly send off their models and wait for days or weeks for the printer operators to set up and complete the print run. To maximize the efficiency of the machine, operators often wait until they receive a “full load” of models before running them.
With a larger number of less expensive consumer printers, more people can produce parts on-site, more quickly and at minimal cost. This allows an organization to become more agile and capable of creating a greater number of designs, improving design engineering efficiency. It also means that when employees have an idea for improving efficiency through a new arrangement of tooling, fixtures or jigs, they can quickly produce the part they need on site.
Additive manufacturing cost analysis: where the consumer option works best
Generally, a consumer option works best when printing relatively simple, small parts (less than 200 x 200 x 200 mm) with PLA or ABS filaments that don’t require dimensional tolerances greater than +1 percent, a critical tolerance +/- 0.1 mm or multiple colors. Designs with extremely fine details or very thin walls or sections may be better suited to industrial processes and machinery, as are parts which undergo high thermal or mechanical stress.
Injection-molded parts are a prime example. They can be often be produced with a consumer fused deposition modeling (FDM) printer before a single tool has cut any material for the production die. This allows designers to build and deliver physical examples and variants of their design proposals to stakeholders and solicit their design feedback before any significant manufacturing investment is undertaken—which reduces rework and improves margins.
Used for this application, a consumer printer could pay for itself by avoiding just one production tooling modification.
Printing mission-critical replacement parts is another application where manufacturers find success using consumer-grade printers. One manufacturer with a plastic part on its production line that failed repeatedly invested in a $3,000 printer, with a service agreement, to make their own in-house design of the part. This option reduced the price of the part and avoided the disruption, time delay and express delivery fees. The company now prints this part and other internal replacement parts.
Where an industrial printer would have been cost inefficient for such an application, the return on investment of the consumer printer was quickly realized—and on-site engineers continue to design and print other parts as needed.
Companies that want to gain the benefits of additive manufacturing but can’t justify the investment in industrial-grade solutions would do well to consider how a consumer-grade printer could meet their needs. And, by performing an additive manufacturing cost analysis for this particular option, you will be able to lay out the monetary benefits of leveraging a consumer-grade printer.
Learn more about Siemens PLM’s work with additive manufacturing.
About the author
Josh Loughran joined Siemens PLM Software in 2014 and works in the NX Product Definition team. He is an active member of the hobbyist additive manufacturing and product design community.