The closed-loop quality imperative
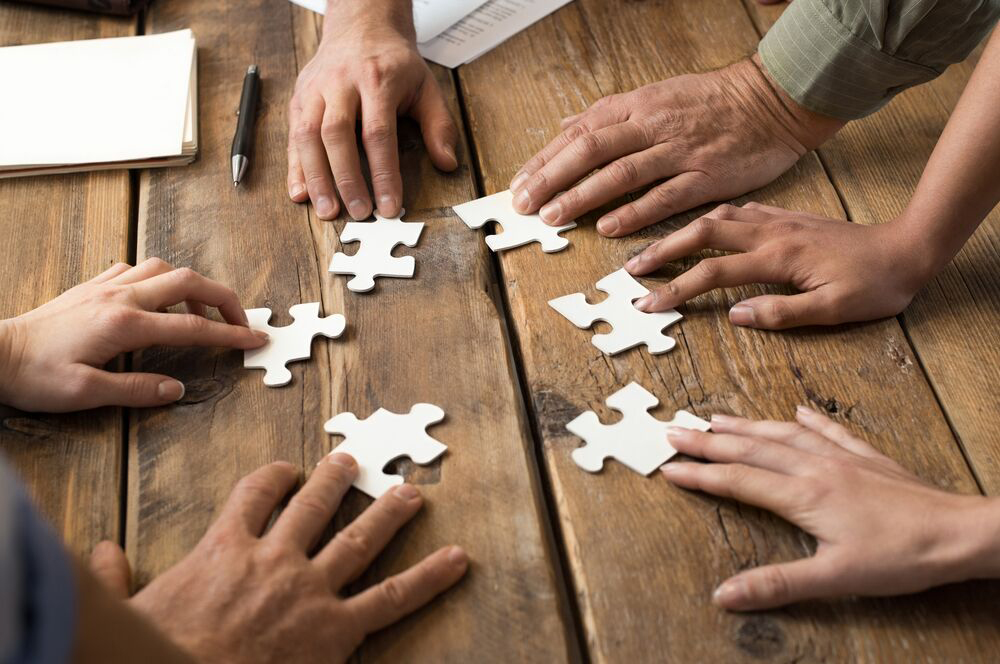
The meaning of quality has evolved over the past 10 years, and too many manufacturers are still working with the old definition.
Many manufacturers equate quality with regulatory compliance or adherence to industry standards, and that’s true to a certain extent. A good quality management system (QMS) will ensure manufacturers meet regulations and industry norms—but that’s just the beginning.
Another point of confusion is that many manufacturers still view quality through a product-centric lens. Again, they’re partially right. Building quality into the product is essential but is only one component of the quality equation.
A third way manufacturers misunderstand quality is that they view it as a departmental function. These manufacturers understand that quality must be embedded in every part of their production process, not inspected at the end before handing off to the next department. But even that’s a bit behind the times.
The new view of quality is that it must permeate every aspect of the extended manufacturing process, much like product lifecycle management does for product development. That means:
• Quality must be managed end-to-end and in a closed loop, from design, through manufacturing and to customer purchase and use.
• Quality must be considered in all aspects of the company, including in the product, process and employee training.
• Components of such a holistic quality approach must be seamlessly integrated, including critical characteristic definitions, control/inspection plans, corrective actions and complaints.
The enablers of this approach, called “closed-loop manufacturing,” are the Internet of Things, cloud technology and automated access to knowledge. Information about quality in one part of the product lifecycle is available for any other, enabling continuous quality improvement.
Smart manufacturers seeking a competitive edge view this new approach to quality not as a cost, but as an investment that will result in delighted customers and increased financial returns. With their sharp focus on satisfying customer demand, automobile manufacturers, for example, consider quality not only as adhering to safety or other regulations, but as delivering on the brand promise and what the customer wants in terms of product features.
What drives the push for pervasive quality
The push for end-to-end quality management follows closely on the heels of a similar transformation to better manage product lifecycles, and it’s not hard to understand why. Just as leading-edge systems streamline new product introductions with a digital thread for every function from design to delivery, the latest QMS systems establish a foundation for consistency and continuous improvement.
The integration of a closed-loop quality system helps manufacturers address market challenges, including demands for reduced time to market, the need for increased flexibility, improved quality, better efficiency and greater security.
Customer demands increase product and process complexity. For example, these demands include an expectation of higher quality, mass customized goods at the same cost as mass-produced, and yet delivered faster than ever before.
Complicating manufacturers’ ability to meet these challenges—and increasing their need to implement digital systems to address them—is the trend toward increased globalized manufacturing. A recent report from Frost & Sullivan, Quality in the Future of Manufacturing, concludes: “As manufacturers continue expanding their operations globally, companies are being forced to be digitally connected and follow an integrated approach toward industrial process management.”
This leads to an increased demand for systems and software that support cross-border manufacturing operations, which require a closed-loop QMS to “enable a bidirectional flow of information to and from the department across a global manufacturing value chain.”
Technology enables pervasive quality
Modern technology can make end-to-end, closed-loop quality management possible at a reasonable price and effort. Quality management systems streamline and integrate global quality-assurance work across the product lifecycle, similar to how other systems help with product development and management. While those systems synchronize product-centric processes across the product lifecycle with high efficiency, QMS systems are highly efficient at improving those processes, and thus the product. Both systems enable continuous improvement by feeding product and quality information gathered throughout the process back into the production and design processes.
QMS systems are also modular, which allows manufacturers to incrementally adopt new functionality that best meets their unique needs and schedules.
Quality as a profit center
The Frost and Sullivan report summed up the increasingly central nature of quality in driving manufacturing competitiveness:
“Quality is no longer synonymous with product integrity alone; instead, it is a company’s on-going commitment to excellence across all departments, individuals, and processes involved in developing the product (including sustainability, regulatory requirements, quality enforcement, cost reduction and efficiency, prevention of failures, standard reporting, lessons learned and know-how transfer, etc.).”
An automated, integrated closed-loop QMS is the foundation of this strategic approach to quality.
This concludes the first part in our series on the future of quality in manufacturing. In part two, we discuss how strategic technology enables a closed-loop approach.
About the author
Raffaello Lepratti is the vice president of business development and segment marketing within the Manufacturing Operations Management software business of Siemens PLM Software. After several years of experience in the car manufacturing industry, he held positions in product management, marketing and account management at Siemens AG. Since 2015, Raffaello has been part of the Siemens PLM Software organization and a member of the MESA board of directors. He holds a Ph.D. in Applied Science for Human-Machine Collaboration. He is married and has 3 children.