What will it take to make autonomous cars safe?
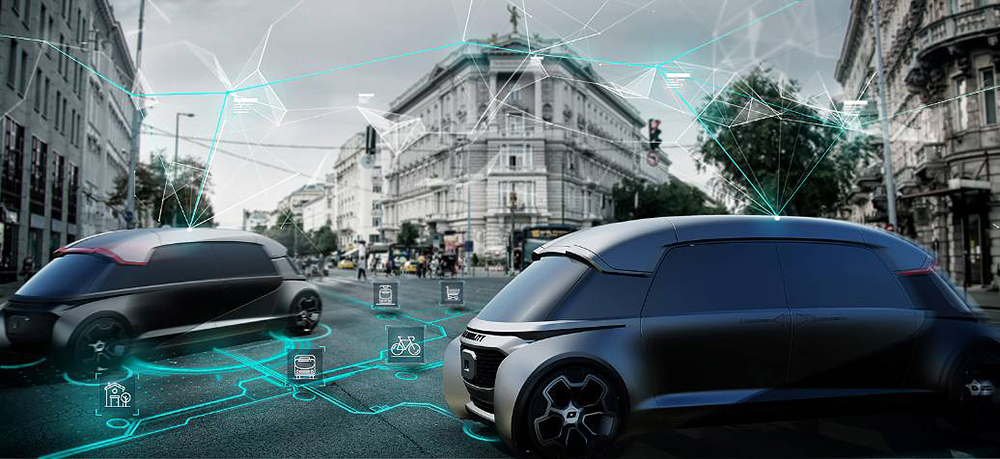
You’re driving down the road and a car with no one in the driver seat is about to pass you. It signals to change lanes and begins moving in front of you to complete the pass. Do you trust that it will safely make the lane change?
It will certainly take time for autonomous cars to gain our trust. What are engineers doing today to help build this trust?
Companies are looking into this new aspect of road safety. One such company is TASS International, a Siemens business which supports the global automotive industry in creating and testing safer, smarter cars. The company’s strengths lie in its focus on safety that is based on simulation software tools and on engineering solutions to conduct comprehensive autonomous vehicle safety testing.
To learn more about the challenges with safety, I spoke with three TASS colleagues: director of mobility center Gwen Van Vugt, director of sales and marketing Frank Litjens and marketing manager Paul Van Straten about future car technology, simulation software tools and car safety testing.
How do you make autonomous cars safe?
Edward Bernardon: What do the words “future car” mean to you?
Frank Litjens: I think at TASS, we go further than just the car and focus on the occupant, as it’s not just the future car itself, and the technology to make it as idiot-proof as possible. However, we serve the occupant by bringing it back to them with software validation tooling and testing that validates real-world scenarios.
Consider first an old car where you had no airbags, no belts, just a driver positioning the vehicle in its environment. Next, came a hip seat belt. Maybe you remember old pictures of the first seatbelt, which I think was approximately in 1955, an invention of Volvo, although it developed long before that, they were just the first to apply it.
This evolved to the three-point belt in 1959, also by Volvo, where the shoulder belt kept the occupant in position in unsafe situations. Later, came belts that pull against the body within a load limitation function. The belt was no longer just a strap; it included load limiters and firing power to strap them tightly to the body. All this to make sure the occupant comes out undamaged, as much as possible, in all situations to serve the safety needs of the occupant.
Later airbags were added, first just one in the steering wheel, then came the dashboard, in the sides, protecting the knees and then you were surrounded by airbags. However, there is a limitation to making sure that you have zero casualties, even if you put 100 airbags in the car. Smart sensors came into play to reach our goal of zero fatalities.
It comes down to the person sitting in the car, which requires sensors to help make the occupant safe. That angle I think is something new I would like to put on the table.
Edward Bernardon: It seems that TASS focuses first on the occupant, and the technology is secondary. Can you elaborate on how an occupant safety-driven approach helps TASS prepare for the car of the future?
Gwen Van Vugt: At TASS, we always think safety in everything we do. If we talk about automated or connected driving, we look at how these help the safety functions of the vehicle.
Our software and services make the entire connection between the road and the occupant of the car. If you look at an automated vehicle, it sees the world around it with all kinds of sensors. TASS has detailed sensor models that accurately model information that sensors provide so you can virtually test and build an automated driving vehicle on your desktop.
Once the vehicle understands this virtual world, you have to do something with that information using control logic, for instance, if you want to steer in a specific direction or brake with a particular force. It is the technology that sends information to the steering, brakes and eventually the tires that enable that to happen.
Since the tire is the only physical interface between the vehicle and the world, TASS has become the world leader in tire modeling. Tire modeling is essential in automated driving. For instance, a control algorithm might want to steer 90 degrees to the right, but you must know whether the tires are capable of doing that.
In the end, we look at how an automated vehicle feeds all this back into the occupant. For example, if you’re making an evasive maneuver that influences the occupant, we can use active human body models that mimic the behavior of real bodies. We can change the behavior of these human body models by setting the body to a relaxed mode. In an automated driving vehicle, if you’re reading the newspaper, you react differently than if you’re actively driving and see an accident happen because then you tense your muscles and your body responds differently.
Those are the type of scenarios we take into account in models from sensors, to tires, to occupants in the vehicle. It is the whole ecosystem that is built around safety, and that’s basically what the genes of our company are about, and makes us unique.
Edward Bernardon: What do you think, from an occupant standpoint, are the most significant challenges that we’re facing to keep the occupants safe in an autonomous car?
Frank Litjens: You see a lot of shifting at this point in time. Who is responsible for all the various links in this safety chain? Until that is crystallized and clear, I think some time will pass, and then boundaries and targets will need to be set. I think that’s a big challenge.
For instance, on the governmental side, the roads must be able to have autonomous cars. If the vehicle goes out of defined boundaries, who is responsible for it, and who is going to pay for it? Is this a concern of insurance companies or the OEM that built the car? Or, last but not least, the occupant in that car. And, what’s the occupant’s responsibility if he shifts and takes control? I think these are topics that need to be addressed– it’s a challenge that needs to be looked at.
If you focus on the safety of communication and take it to an IT level, this car has sensors in the vehicle itself, but it also has sensors to its environment. Otherwise, it’s difficult to navigate through the world and through that environment. So there is a transmission of information that is cloud-based. Also, there is always a danger of false information, data loss or even hacking. I think that is something that is a concern.
Lastly, is the whole occupant-centric concept – the person sitting in that car. What’s their age? What are their habits? What’s their ability to drive the car? All of these concepts will need to be addressed.
Additionally, what is that person’s status? Did he have a few beers? Is he too old or too young to drive? Is he sick? Is he fainting? All this information needs to be communicated to a control unit in the car. This way, the occupant is part of this whole control system, and that is a challenge in itself.
Today, we’re looking at relatively simple questions in the domain of, if my grandmother steps into my car and she has an accident, how hard should the belt force her back in the seat? How hard should that airbag explode to make sure this brittle old lady doesn’t break?
Considering the demographics of the occupant is already a challenge today and sounds simple if you compare it to a car driving autonomously, but I can tell you today that’s already a challenge. So think about these three challenges; IT, the person itself and the control shift from the occupant to the car – these are the first parts of the autonomous challenge.
This concludes part one of my discussion with the TASS International experts about autonomous vehicles. In part two, we discuss what goes into engineering these vehicles.
About the author
Edward Bernardon is vice president of strategic automotive initiatives for the Specialized Engineering Software business segment of Siemens PLM Software, a business unit of the Siemens Industry Automation Division. Bernardon joined the company when Siemens acquired Vistagy, Inc. in December, 2011. During his 17 year tenure with Vistagy, Bernardon assumed the roles of vice president of sales, and later business development for all specialized engineering software products. Prior to Vistagy, Bernardon directed the Automation and Design Technology Group at the Charles Stark Draper Laboratory, formerly the Massachusetts Institute of Technology (MIT) Instrumentation Laboratory, which developed new manufacturing processes, automated equipment and complementary design software tools. Bernardon received an engineering degree in mechanical engineering from Purdue University, and later received an M.S. from the Massachusetts Institute of Technology and an MBA from Butler University. He also holds numerous patents in the area of automated manufacturing systems, robotics and laser technologies.