The future of flight and changing supplier relationships
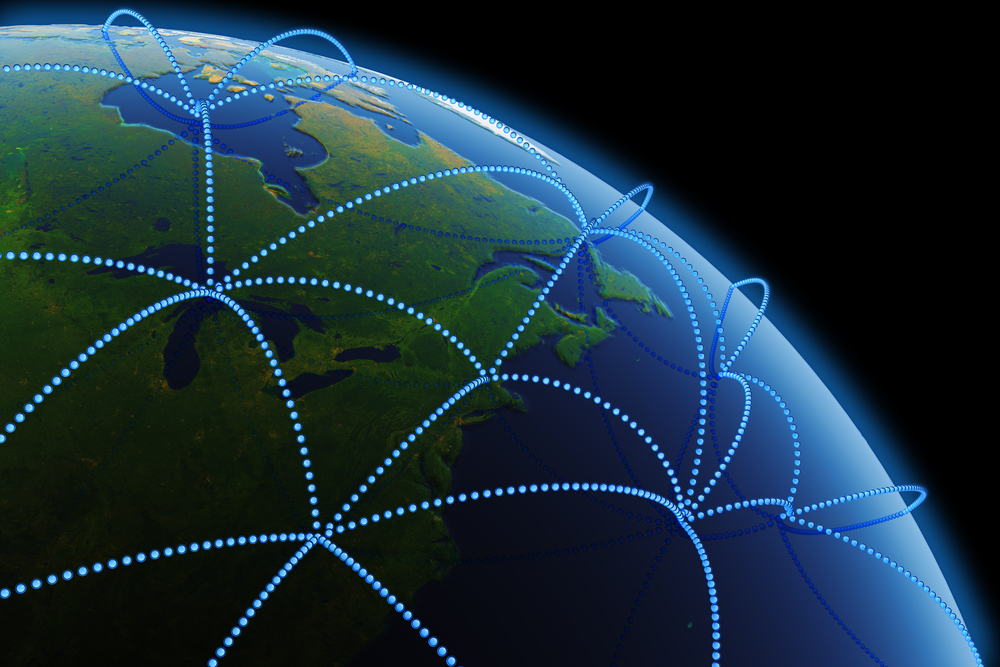
Business dynamics will change in aerospace supply chains as manufacturers incorporate new technological advances shaping the future of flight.
Advances in materials, propulsion, human machine interfaces and artificial intelligence are spawning new realities, such as civilian space travel and autonomous drone delivery. Even in standard commercial air travel, technological advances are having a big impact, such as making air travel affordable for millions of people who previously couldn’t afford it. Further, these new technologies are making flight safer, faster, more profitable and environmentally friendly.
This transformation requires rethinking the industrial structures and business assumptions that traditionally have been used to develop aerospace products. Nowhere is this more evident than in the aerospace supply chain.
As the value and relative complexity of products shift, supply chain strategies and relationships that have existed for the past century will be reconfigured, and even upended.
The insource/outsource dynamic
A new balance of what and how much to insource versus outsource will be struck based upon the level of innovation versus gains from supply chain efficiency.
Commodity products in which value is derived from efficiency in overall development activities will be pushed farther down the supply chain. Highly innovative products, including those with critical, exclusive capabilities built using unique trade secrets, will remain within vertically integrated organizations—the better to protect intellectual property and increase profitability.
The big takeaway is that all manufacturer types in the aerospace supply chain should review where and how they add value to the industry. They must consider how agile their product design and production capabilities are and make investments in technology solutions that can make them a more agile prime or supplier.
This will help manufacturers expand and strengthen their business, leading to increased profitability and the potential for market dominance.
Changing chains
Critical to understanding how the supply chain will rebalance is thinking through the impact of new technologies. One area of balance likely to change is in aircraft propulsion.
New methods of powering aircraft using electric propulsion systems rather than gas turbines will bring about significant levels of innovation. This will drive more development internal to the aero-engine prime, likely in partnership with a company that offers significant expertise in industrialized electrical systems. Indeed, Siemens and Airbus are in the midst of a program testing electric aircraft.
Another is in the area of composite sub-components. Though there is currently an extended supply chain that is used to make these, many design activities still reside within the aircraft prime.
As composites continue to mature, and as aerospace technologies and innovations become commoditized, this will shift. The extended supply chain will begin not just manufacturing these products, but also designing them. This likely will accelerate the trend of primes becoming system integrators and may enable the full outsourcing of less complicated designs, lowering obstacles for new entrants to the market.
Managing product and supply chain complexity
How products get developed across this complex web will determine the winners and losers in this reshuffling. Whether you’re the prime or the supplier, real-time collaboration across an extended supply chain increases productivity and reduces risk. It enables more effective management and more tightly compressed production cycles.
With supplier integration technologies, extended teams can coordinate processes and manage information, both external and internal, across all stages of the product lifecycle. Becoming fluent with the latest product development and management technologies will not be optional.
The global F-35 aircraft coalition is a particularly noteworthy example of the extended aerospace supply chain of the future. The aircraft is being built by a Lockheed Martin-led coalition of U.S. and international aerospace leaders, including Northrop Grumman and BAE Systems, and supported by up to 600 suppliers. The parties involved reside in more than 30 countries, spanning 17 time zones.
To coordinate the work of the coalition, Lockheed adopted Teamcenter, a 21st-century PLM technology. Among other things, the technology coordinates efforts and fosters collaboration across the extended enterprise of companies with dissimilar development environments, and it manages the multiple formats of design data involved in the project. Importantly, for the F-35 coalition, it has made real-time online collaboration a reality for both engineering and in-process and released designs, across five major partners and 35 design suppliers.
The aerospace supply chain of the future
Though the global F-35 aircraft coalition is a unique—and unusually large—collaboration network, it’s not a stretch to suggest that such close integration of large numbers of companies will be the model of future aerospace supply chains.
As the future of flight takes shape, we can envision a world with pilotless cargo planes and space tourism, along with entirely new experiences in airplane travel. Airlines will seek to offer a high level of customization and personalization, so they can differentiate their services from competitors.
Making such advances possible will be teams of extended supply chains, seamlessly working together to deliver the latest flight innovations at the most effective cost.
Any aerospace manufacturer that wants to participate in this bright future will have to ensure that they understand how disruptions in their supply chains will impact their business and change their needs. They must also ensure that their product development and management capabilities meet the challenge of increasing complexity that is an inherent part of the future of flight.
This concludes our introduction to the future of flight.
About the author
John O’Connor is the director of product & market strategy in the Specialized Engineering Software (SES) organization of Siemens PLM Software. SES develops and markets CAD-integrated, specialized engineering software for product design and manufacture in the aerospace, automotive and other design-driven industries. O’Connor has served in numerous roles at Siemens, ranging from application support and technical sales management to business development. Prior to Siemens, he was a senior design engineer at Lockheed Martin, where he led a number of product design teams. He holds a Master of Science in materials engineering and a Bachelor of Science in mechanical engineering.