Powering advanced bin-picking with Concept Analysis, Dynamic Simulation, and Virtual Commissioning
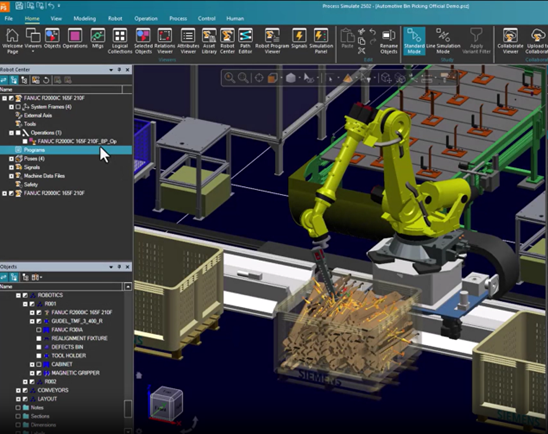
Explore how static analysis, robotics simulation and virtual commissioning technology help evaluate, debug, and validate bin-picking stations before physical hardware is deployed, reducing risks and avoiding costly delays.
Flexible bin-picking consists of handling and moving objects which are placed inside bins or pallets in a random way. Bin-picking refers to the automated process of using robots, often equipped with vision systems, to identify, pick, and place parts from a bin or container. This process is commonly used across various industries such as automotive, food and beverage, pharmaceuticals, logistics and warehousing, where handling objects from a bin is repetitive, labor-intensive, and time-consuming.

Nowadays, using robots for bin-picking is becoming increasingly common, especially with advances in motion planning, advanced gripper and computer vision. Many industries are adopting robotic bin-picking to improve efficiency, reduce labor costs, and increase automation. However, flexible bin-picking is still a challenging task in robotics due to unstructured environments, grasp planning, occlusions or blocked visibility among other variabilities such as objects varying in size, shape, texture or material.
For example, unlike structured conveyor systems or fixed-position pick-and-place operations, bins contain randomly placed, overlapping, or stacked objects. Robots must be programmed to adapt to different orientations while also keeping a collision-free path. Explore how the combination of static analysis, dynamic simulation and virtual commissioning using Process Simulate software enables industrial bin-picking, enhances efficiency, accuracy, and safety while reducing labor costs and errors.
Design, deploy and accelerate flexible bin-picking
Let’s explore an end-to-end workflow for automating a flexible bin-picking station using Process Simulate software.
Concept Analysis
In robotic bin-picking, every potential mechanical deadlock and collision in a productive cell will lead to an interruption of production processes and require staff to troubleshoot. Therefore, it is crucial to keep the error rate caused by reachability and collision as low as possible.
To address this challenge, Process Simulate offers efficient tools for creating and analyzing robotic bin-picking operations. New operations can be easily created from pick frames of each part, various tools in Process Simulate leverage 3D graphical visualization and kinematic capabilities to analyze both pick-ability and reachability within a given setup. Using this preliminary assessment, tool design and station layout can be improved, therefore ensuring the production efficiency and quality.
Dynamic Simulation
Static analysis is valuable for pre-checking configurations, providing an initial assessment of the setup. However, dynamic simulation complements this by effectively detecting interval collisions, workspace constraints, and joint singularities, ensuring safe and smooth robot motion.
One prerequisite for dynamic simulation is the path planning algorithm. Process Simulate is equipped with an inherent algorithm to reorder bin-picking locations; unattainable locations or cause collision can be quickly commented out, therefore ensuring smooth simulation. Furthermore, Process Simulate helps reduce programming effort by standardizing robot motions so the user can define pre-configured movement patterns.
To enable more realistic and reliable behavior of robots in virtual environments, physics is essential in robotic simulation. Process Simulate has a physics engine that handles collision, gravity and object interactions. It can not only emulate the random part distribution in different manner, but also show the process of part shuffling and falling during robotic bin-picking. Therefore, dynamic simulation becomes reactive and meaningful. Indicator assessment such as cycle time and pick success rate becomes possible based on simulation, manufacturers can gain deep insights into the bin-picking process and identify errors early to improve process feasibility.
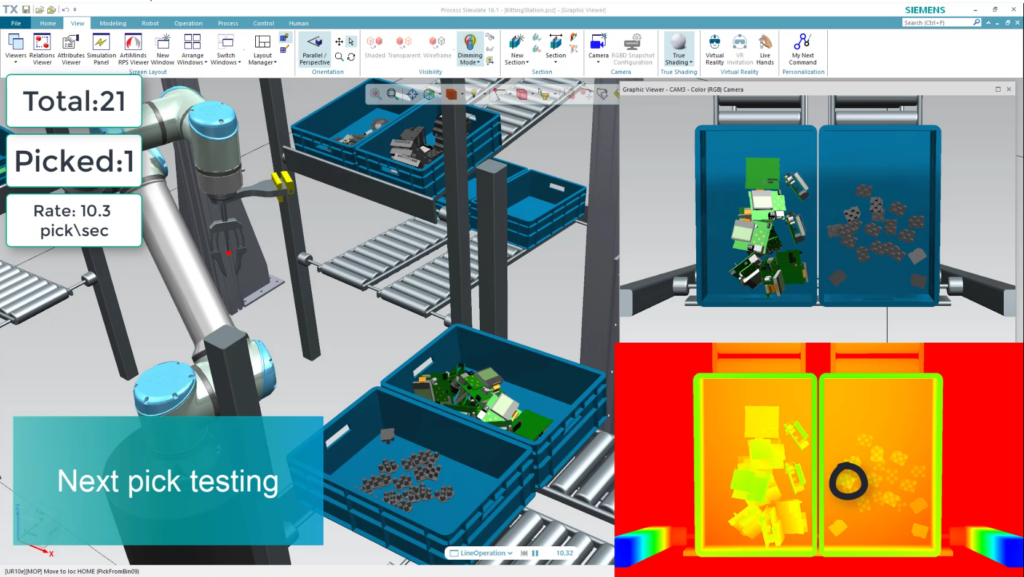
Virtual Commissioning
Nowadays, robotic bin-picking often relies on a combination of advanced computer vision, deep learning and real-time motion planning to improve performance. Vision-based virtual commissioning software is increasingly adopted for flexible bin-picking because it enables accurate and adaptable robotic operations before real-world deployment.
To achieve this, Process Simulate supports RGB-D camera, which is used for simulating depth perception and vision-based robotic applications. RGB (color) and Depth (D) data generated by Process Simulate can be sent to any deep learning model via open API, allowing to plan collision-free motion with high realism and validate vision algorithm before deployment.
Based on simulated depth images, a robotic arm is driven to adjust its picking approach for randomly distributed parts. By simulating vision data and robotic behavior, manufacturers can optimize bin-picking performance in a virtual environment before implementing it on physical hardware, leading to a faster and more reliable bin-picking process.
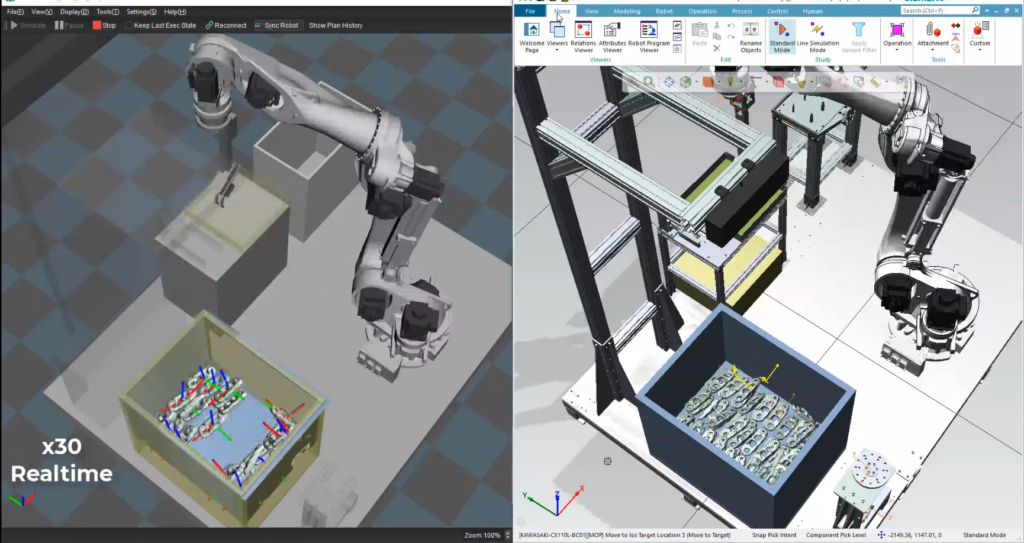
Advancing toward smarter and adaptive bin-picking with Process Simulate
The successful implementation of automation and robots is critical to enable manufacturers using bin-picking application in various industries to address market challenges, gain a competitive advantage, and meet ever-changing customer demands. Concept analysis, simulation, and validation with Process Simulate reduces risk while automating manual operations in the bin-picking process.