Why Do You Need a Simulation Data Management System?
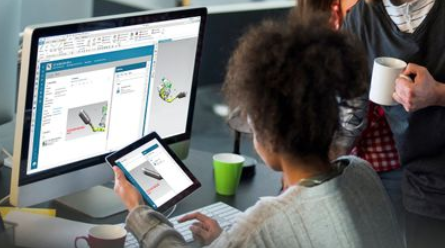
Simulation Data Management is the answer to boosting analyst productivity
There has been a significant need for a Simulation Process and Data Management (SPDM) system due to an increased usage of CAE simulation in PD processes. According to a CIMData report, in 2018 Simulation & Analysis revenues grew to nearly $6.5 billion worldwide, an increase of 13.1% from previous year. It continues to be one of the “rapidly growing segments” and is expected to reach $11 billion in 2023.
This rise is not surprising as more companies are seeing the benefits of incorporating CAE simulations in their PD processes.

However, with this increased usage, companies frequently face the following system and business challenges:
- Inefficiencies in Product Development: Simulation analysts spend a significant amount of time searching simulation data and sharing it with others. There is also lack of traceability and poor visibility of simulation results.
- Poor Collaboration: Collaboration between teams working in different locations and time zones is difficult and un-secure.
- Lack of Data Reuse: Simulation teams within an organization use different simulation tools and processes. Due to lack of data management, they end up redoing entire analyses instead of reusing past data.
To overcome these challenges, it is essential to employ an SPDM system. Best described by NAFEMS, SPDM is “a technology which uses database solutions to enable users to manage structures of simulation and process data across the complete product lifecycle. SDM artifacts can be data, models, processes, documents, and metadata relevant to modeling, simulation, and analysis.”

Siemens Digital Industries Software is a leading software provider in the SPDM space with its very own solution, Teamcenter Simulation (TcSim). An add-on module to Siemens’ flagship PLM software Teamcenter, TcSim has been specifically designed to help companies avoid the above challenges. It allows them to gain complete control of their simulation process and data and help realize the digital twin.

Teamcenter Simulation offers several benefits, some of which include:
- Support of increasing volume and complexity of simulation work through data and processes management
- Increased confidence in simulations due to complete traceability from requirement gathering to design and validation.
- Speed up of simulations through better collaboration, improved time to find data and greater re-use of existing work.
- Quick delivery of results due to standardization and automation of simulation processes.
- Greater visibility into the simulation process and results for program managers and downstream operations.
- Improved flexibility through managed and standardized access to third party simulation tools.
- Lower implementation costs and risk by leveraging the proven Teamcenter platform as the common infrastructure solution.
To get a quick demo of TcSim, please contact your local Siemens sales representative.
About the author Rohan Wanchoo works as a Product Manager for Teamcenter Simulation at Siemens Digital Industries Software. This article is the first of a series of articles that will be posted on TcSim.